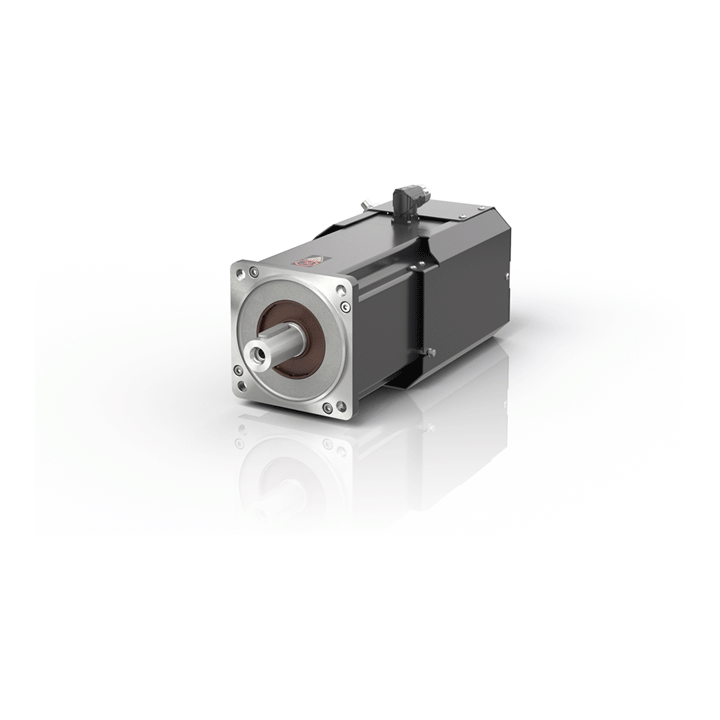
The AM8563 high-inertia servomotor is suitable for drive solutions with increased moment of inertia to ensure synchronism and optimal ratio of load/motor inertia in the 100…480 V AC voltage range. The standstill torque of the motor depends on the winding and is in the range of 29.0…41.4 Nm. It is available with the OCT feedback system (absolute encoder). The high-inertia servomotor with flange code F6 (142 mm) and motor length 3 has a shaft diameter b = 32 k6 and a free shaft end of d = 58 mm.
Product status:
regular delivery
Product information
Data for 400 V AC | AM8563-wLyz |
---|---|
Motor type | permanent magnet-excited three-phase synchronous motor |
Nominal voltage | 100…480 V AC |
Standstill torque | 41.4 Nm |
Rated torque | 33.9 Nm |
Peak torque | 111 Nm |
Rated speed | 1400 min-1 |
Rated power | 4.97 kW |
Standstill current | 11.6 A |
Peak current | 38.9 A |
Torque constant | 3.33 Nm/A |
Rotor moment of inertia | 66.1 kgcm² |
Motor feedback | resolver, single-turn absolute encoder
HIPERFACE®, multi-turn absolute encoder OCT, 18 bit, single-turn or multi-turn absolute encoder, electronic nameplate OCT, 24 bit, SIL 2-capable, single-turn or multi-turn absolute encoder, electronic nameplate OCT, EnDat® 3, 19 bit, SIL 3-capable, single-turn or multi-turn absolute encoder, electronic nameplate |
Cooling | external axial ventilation |
Connection technology | M23 speedtec® plug |
Ambient temperature (operation) | +5…+40°C |
Approvals/markings | CE, cURus, EAC |
All electric quantities are RMS values.
Housing data | AM80xx forced cooling |
---|---|
Protection rating | selectable IP20, IP65 |
Design form | flange-mounted according to IM B5, IM V1, IM V3 |
Material | aluminum |
Coating/surface | dark gray powder coating, similar to RAL7016 |
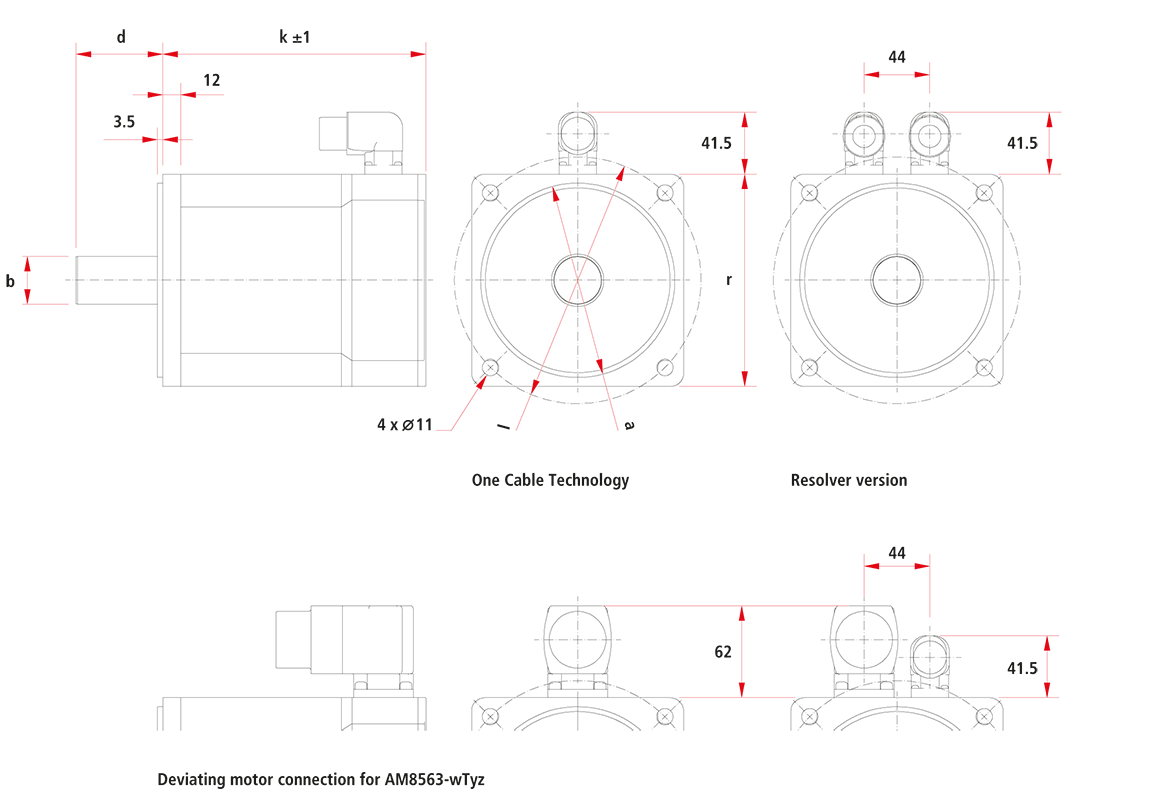
Dimensions | AM8563-wLyz |
---|---|
a | 130 j6 |
b | 32 k6 |
d | 58 mm |
l | 165 mm |
r | 142 mm |
k (without brake) | 398 mm |
k (with brake) | 438 mm |
Order reference
AM8563-wLyz | |
---|---|
w = 0 | smooth shaft |
w = 1 | shaft with groove and feather key according to DIN 6885 |
w = 2 | smooth shaft with IP65 sealing ring |
w = 3 | shaft with IP65 sealing ring and with groove and feather key |
w = 4 | shaft with IP65 sealing ring, smooth shaft and sealing air connection (not for AM801x) |
w = 5 | shaft with IP65 sealing ring, shaft with groove and feather key and sealing air connection (not for AM801x) |
y = 0 | 2-cable standard: feedback resolver |
y = 1 | One Cable Technology for power and feedback: feedback transmission via motor cable, no feedback cable necessary, electronic nameplate, single-turn, absolute position within one revolution, 18 bit resolution |
y = 2 | One Cable Technology for power and feedback: feedback transmission via motor cable, no feedback cable necessary, electronic nameplate, multi-turn, absolute position within 4096 revolutions, 18 bit resolution |
y = 4 | 2-cable standard: feedback multi-turn, absolute encoder SKM36, 128 SinCos periods (only for AM856x) |
y = G | One Cable Technology for power and feedback: feedback transmission via motor cable, no feedback cable necessary, electronic nameplate, single-turn, absolute position within one revolution, resolution 24 bit, SIL 2-capable (mandatory for TwinSAFE Safe Motion functions at AX8xxx-x2xx) |
y = H | One Cable Technology for power and feedback: feedback transmission via motor cable, no feedback cable necessary, electronic nameplate, multi-turn, absolute position within 4096 revolutions, resolution 24 bit, SIL 2-capable (mandatory for TwinSAFE Safe Motion functions at AX8xxx-x2xx) |
y = I | EnDat® 3; One Cable Technology for power and feedback: feedback transmission via motor cable, no feedback cable necessary, electronic nameplate, single-turn, absolute position within one revolution, resolution 19 bit, SIL 3-capable (mandatory for TwinSAFE Safe Motion functions at AX8xxx-x2xx), only for AM802x to AM807x |
y = J | EnDat® 3; One Cable Technology for power and feedback: feedback transmission via motor cable, no feedback cable necessary, electronic nameplate, multi-turn, absolute position within 4096 revolutions, resolution 19 bit, SIL 3-capable (mandatory for TwinSAFE Safe Motion functions at AX8xxx-x2xx), only for AM802x to AM807x |
z = A | forced cooling IP20, without holding brake, for AM855x, AM856x(1) |
z = B | forced cooling IP20, with backlash-free permanent magnet holding brake, for AM855x, AM856x (1) |
z = C | forced cooling IP65, without holding brake, for AM855x, AM856x(2) |
z = D | forced cooling IP65, with backlash-free permanent magnet holding brake, for AM855x, AM856x(2) |
The options cannot be installed in the field. |
(1) The EL2022 or KL2022 digital output terminal with matching ZK4054-6400-xxxx supply cable is recommended for controlling the 24 V DC IP20 ventilation.
(2) The PS1111-2402-0002 power supply with matching ZK4054-6400-0xxx supply cable is recommended for controlling the 24 V DC IP65 ventilation.
Loading content ...
Loading content ...
Loading content ...
Loading content ...
© Beckhoff Automation 2024 - Terms of Use