Introduction to TwinCAT 3 Scope
TwinCAT 3 Scope is a high-performance software oscilloscope and fundamental component of TwinCAT. Like TwinCAT itself, Scope is integrated into Microsoft Visual Studio®. A basic version is installed with the TwinCAT 3 Engineering Setup and is perfectly suitable for system and machine commissioning. TwinCAT 3 Scope View Professional is an extension of the basic version and is aimed at users wishing to track and monitor processes over a prolonged period.
In this 30-minute webinar Pascal Dresselhaus, TwinCAT Product Manager, introduces the application of TwinCAT 3 Scope and offers useful tips and tricks. The webinar is intended for technically orientated users who already have basic experience in using TwinCAT automation software.
More about this video
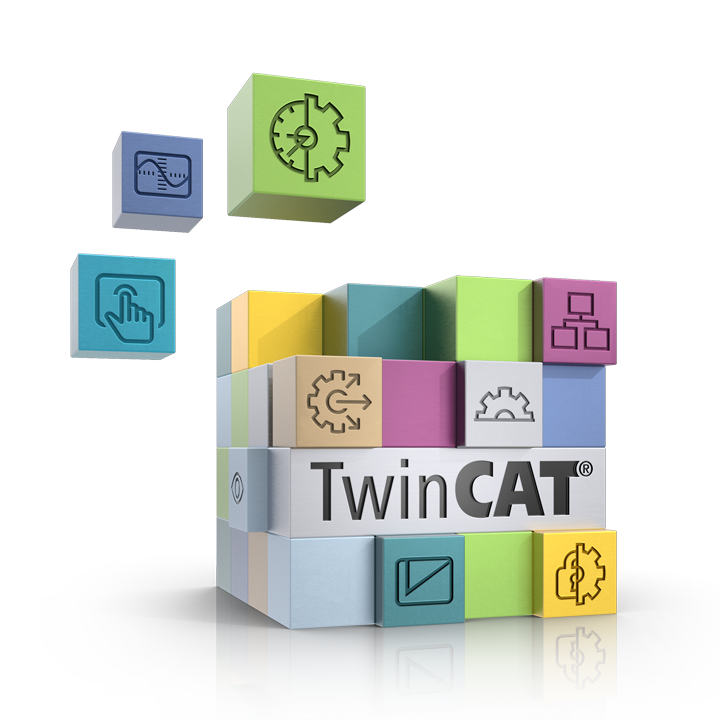
TwinCAT
The TwinCAT software system turns almost any PC-based system into a real-time control with multiple PLC, NC, CNC and/or robotics runtime systems.

TE1300 | TwinCAT 3 Scope View Professional
The TwinCAT 3 Scope View is a software oscilloscope for the graphic representation of signal curves in different chart types. These could be, for example, YT, XY, bar or digital charts. The Scope View Professional extends the Scope View Base version supplied with TwinCAT 3 XAE by additional functionalities. The field of application refers to processes that are to be tracked and monitored over a longer period of time.
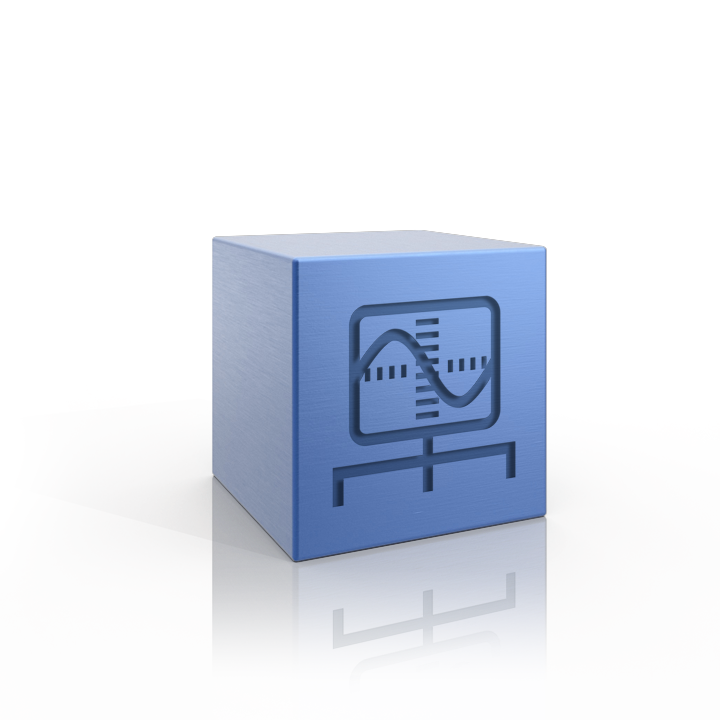
TF3300 | TwinCAT 3 Scope Server
The TwinCAT 3 Scope Server prepares data for the graphical display in the TwinCAT 3 Scope View. It can be used with the Scope View Base or the TE1300 Scope View Professional version. The Scope Server is particularly suitable for autonomous data recording in distributed systems in the production, plant or machine network. It not only has TwinCAT-specific communication interfaces, but also a standardized communication connection via OPC UA.