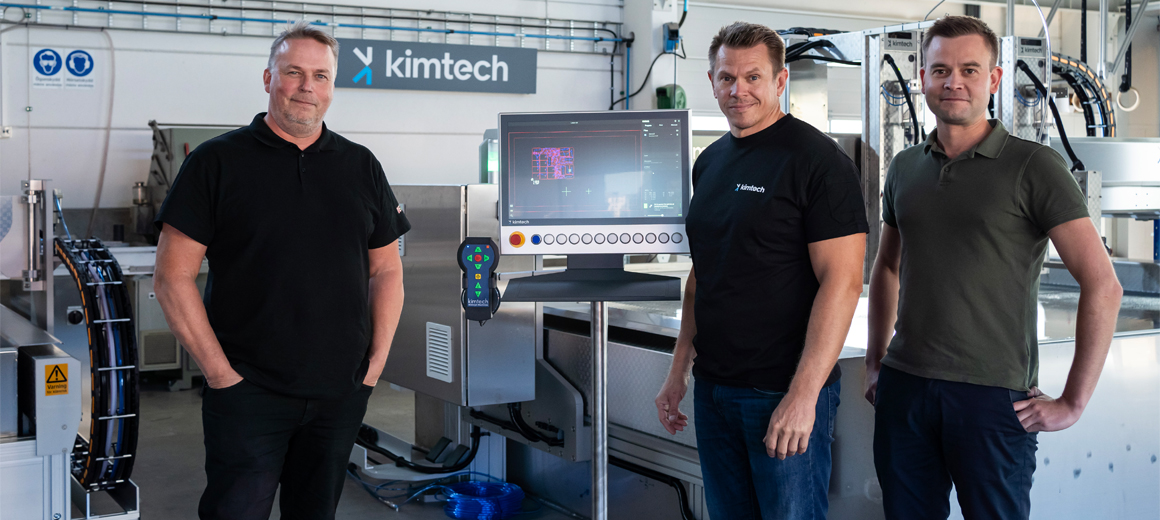
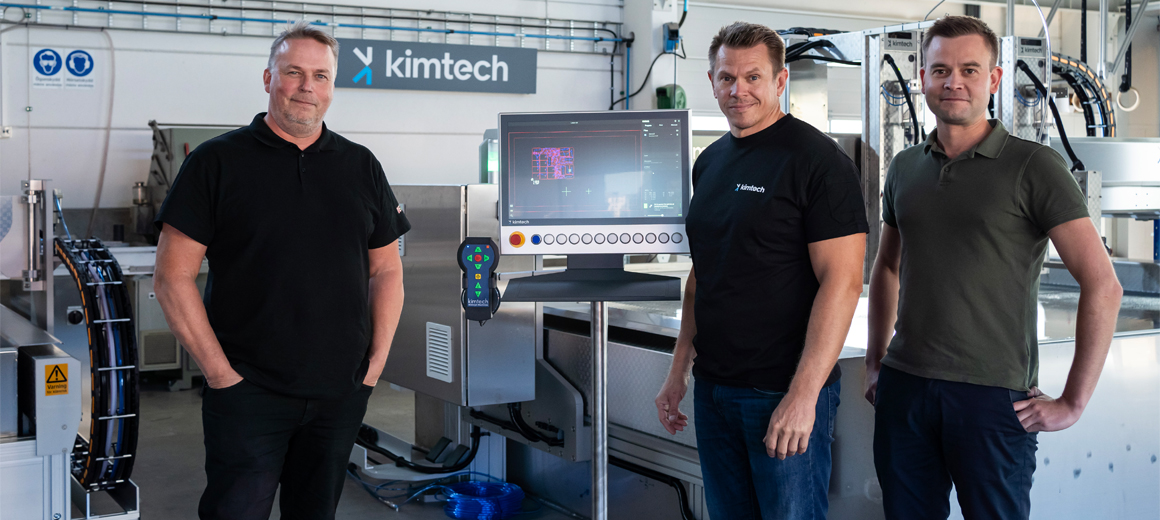
A precise and fast way to the perfect contour
Control systems are subject to very specific demands from every form of production technology – including waterjet cutting. IGEMS from Sweden set itself the goal of taking this process to a new level in terms of precision and speed, and achieved it with the help of PC-based control. Users such as the machine builder Kimtech are now benefiting from the results.
Waterjet cutting is an effective and versatile process for cutting a wide range of materials, including metals, plastics, glass, ceramics, stone, and composites, and can even handle unusual applications such as portioning fish fillets and dessert cakes. “We love waterjet cutting because of its versatility, precision, cleanliness, eco-friendliness, and cost efficiency,” says Jesper Kimblad, Technical Manager at IGEMS, a company based in Borås, Sweden, specializing in CAD/CAM software for waterjet cutting systems. However, it takes more than these credentials to achieve the perfect cut: “We have studied the physics of the waterjet in depth and developed CNC-software that takes its constantly changing nature into account,” says Jesper Kimblad. “In the same way as water cutting requires specific CAD and pre-production software, it also needs an optimized control system.” TwinCAT 3, equipped with a range of functions and other Beckhoff components, forms the basis for the IGEMS control platform.
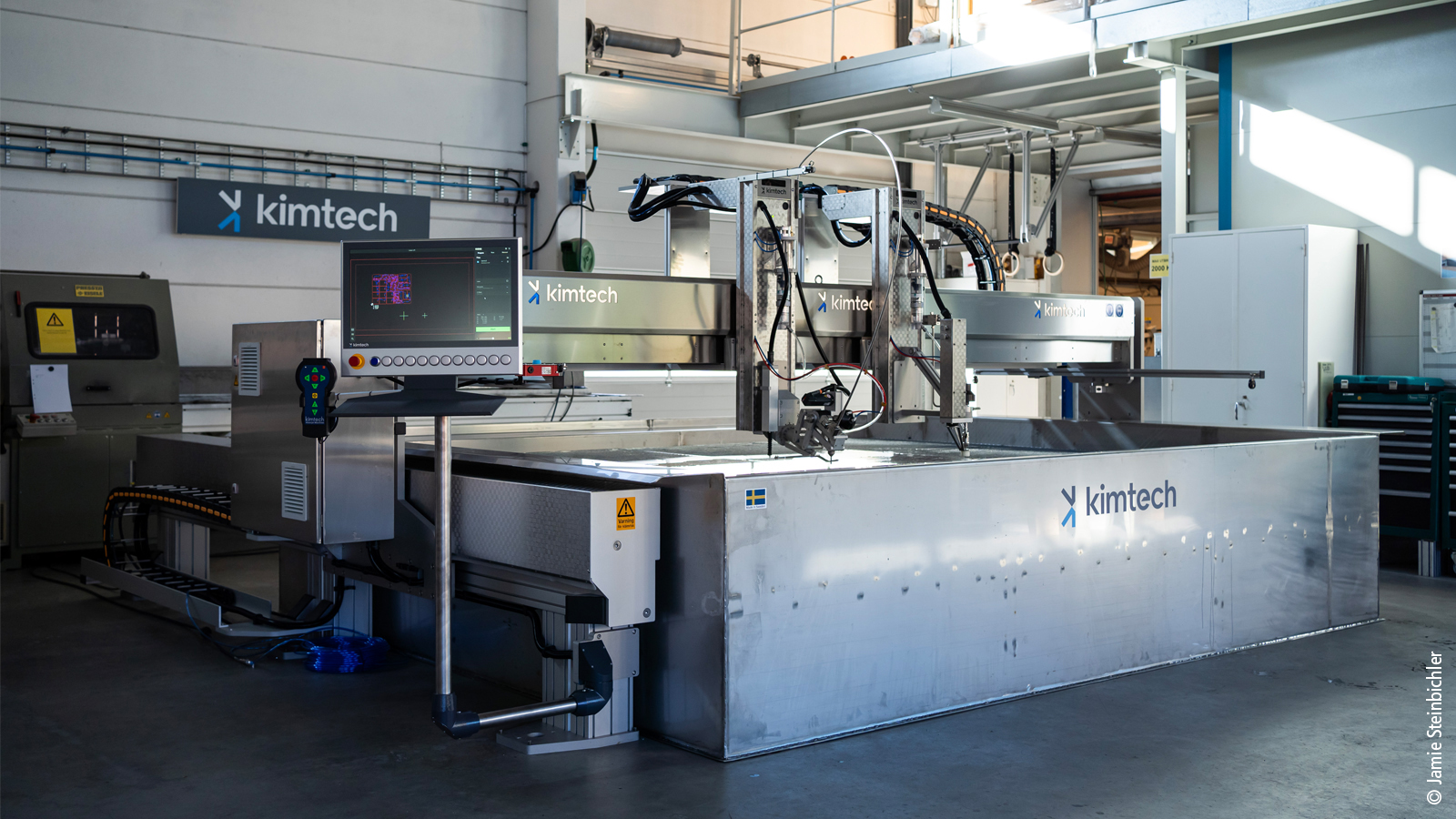
Flexibility and openness deliver benefits
According to Jesper Kimblad, no other system offered the necessary flexibility and functionality: “One problem with conventional control systems is that the digital outputs cannot be controlled quickly and synchronously enough during the path movements of the nozzle.” It is exactly this level of control that waterjet cutting requires, however: The water and abrasive materials must be precisely metered because even the briefest of stops or delays will leave marks on the cutting edges. Citing a further advantage of PC-based control technology from Beckhoff, Jesper Kimblad adds that no other controller would be able to switch the feed rate from mm/minute to inverse time during operation. This function is particularly useful when cutting pipes and in 5-axis operation.
IGEMS went through a total of four iterations with other control providers before Jesper Kimblad finally found the right platform with the open approach of PC-based control and TwinCAT 3: “We simply couldn’t implement the necessary adaptations in the other systems. In addition, the other providers had a limited range of hardware, so IGEMS control system users would always have had to purchase the additional control components they needed from different suppliers and integrate these themselves.”
Single sourcing in hardware and software
As Jesper Kimblad explains, however, Beckhoff’s wide range of technologies allows it to provide all the electrical components required for waterjet cutting machines – anywhere in the world. This is vital for IGEMS’ customers, who sell their water cutting systems worldwide. “Most importantly, however, TwinCAT 3 ensures that a machine does not have to stop while the program is running, which means it can perform multiple cutting tasks in one operation and ensure a straight cut,” says Jesper Kimblad.
IGEMS uses Beckhoff’s TwinCAT software, in particular the TC1200 (PLC), TF5000 (NC PTP), and TF5060 (NC FIFO Axes) functions to calculate the trajectories of the motors, control the drives and movements, perform axis interpolation, track I/O changes and transfer all this data to the FIFO (First In, First Out) buffer integrated in TwinCAT. All data is communicated in real time via the EtherCAT network protocol from Beckhoff. Jesper Kimblad comments: “I really appreciate the open nature of TwinCAT. The software handles difficult tasks involving flowing positions very quickly and ensures a precise and perfect cut. It’s ideal for monitoring values and runs on an industrial PC, which means we can carry out the entire development process on laptops. Setting up and programming the water cutting system is also very quick – between just 5 and 30 minutes.”.
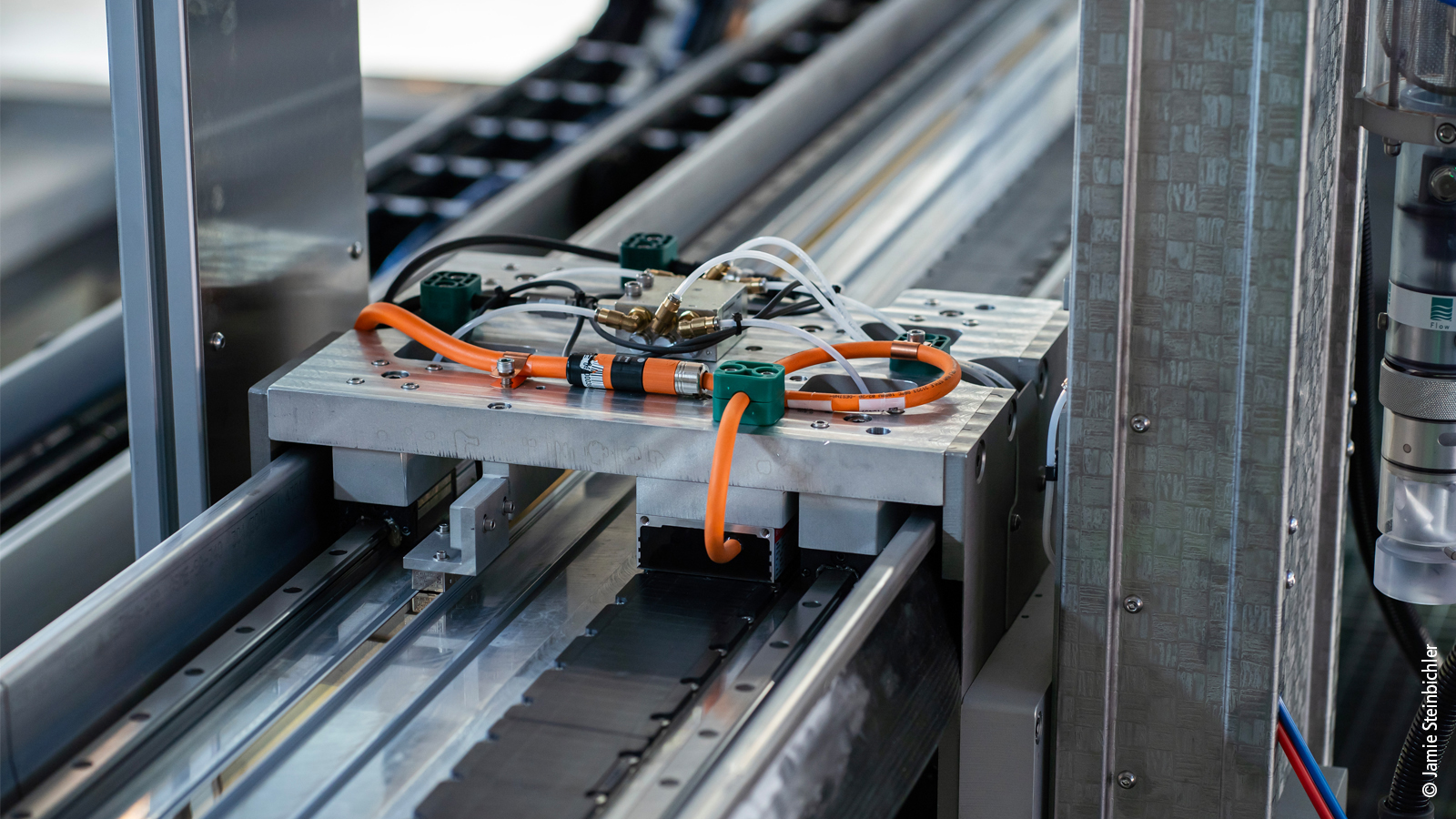
And thanks to the openness of PC-based control, machine builders can easily integrate additional functions into the control system and automate them with Beckhoff hardware.
IGEMS itself uses this flexibility for optional functions – when preparing work and performing calibration, for example. In most cases, leftover pieces of sheet metal are stored for subsequent orders and clamped several times on the cutting systems. An optional camera above the cutting systems scans these pieces and transmits the images to the control system. The contour is scaled there and displayed in the “cutting pattern” of the upcoming processing program. The machine operator can then set the zero point of the NC program directly on the image and adjust the position of the parts if necessary. IGEMS has also integrated a system calibration function into the control system; together with the optional IGEMS Rounder, this measures and compensates for deviations in the X, Y, and Z directions. “Machine builders used to need half a day to a whole day for this calibration; with our software and the measuring head, it only takes 9 minutes,” says Jesper Kimblad, highlighting the benefits of an open control architecture.
Machine builders benefit from sector segmentation
The company Kimtech in Stockholm has now installed 15 machines with control systems from IGEMS and ordered a further 30 complete systems from Beckhoff. CEO Gustaf Kimblad comments: “We are delighted with the control system, which is specially tailored to waterjet cutting. The control system optimizes operation, monitoring, and remote maintenance. It also enables precise calibration and reduces the amount of work involved in programming. The HMI is user-friendly and the integrated tools are intuitive. Overall, the control system simplifies the structure of the waterjet cutting machines and reduces their complexity.” Gustaf Kimblad cites Beckhoff’s One Cable Technology (OCT) as an example: “OCT allows us to connect the drives with just one cable and requires fewer components, which makes us much more competitive. As a machine builder, we can now concentrate more on what we do best.” And Kimtech is not the only company to benefit from having just one contact partner in IGEMS, which provides the complete control system together with Beckhoff. Jesper Kimblad refers here to other projects in the USA and China.