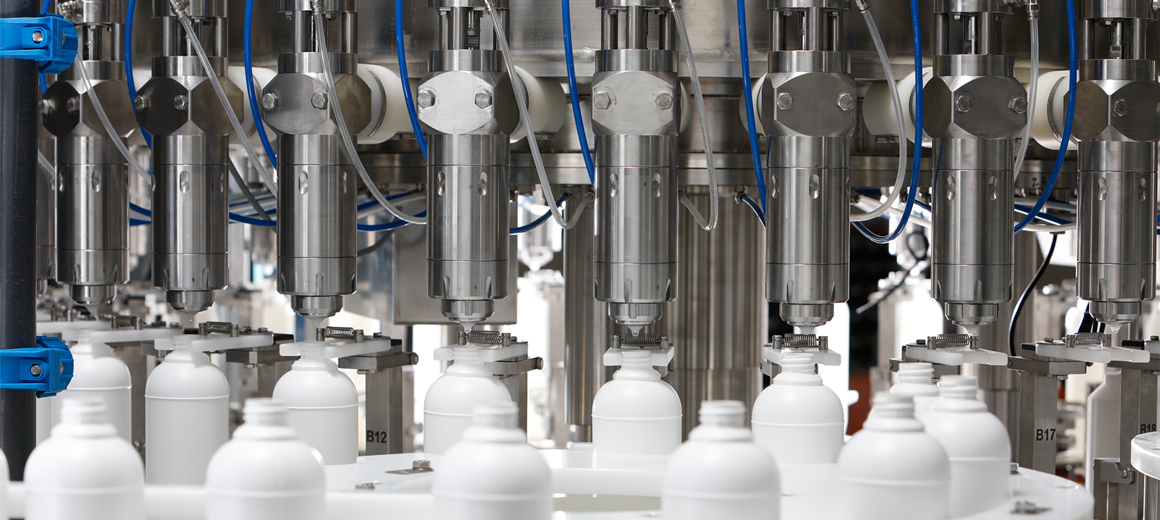
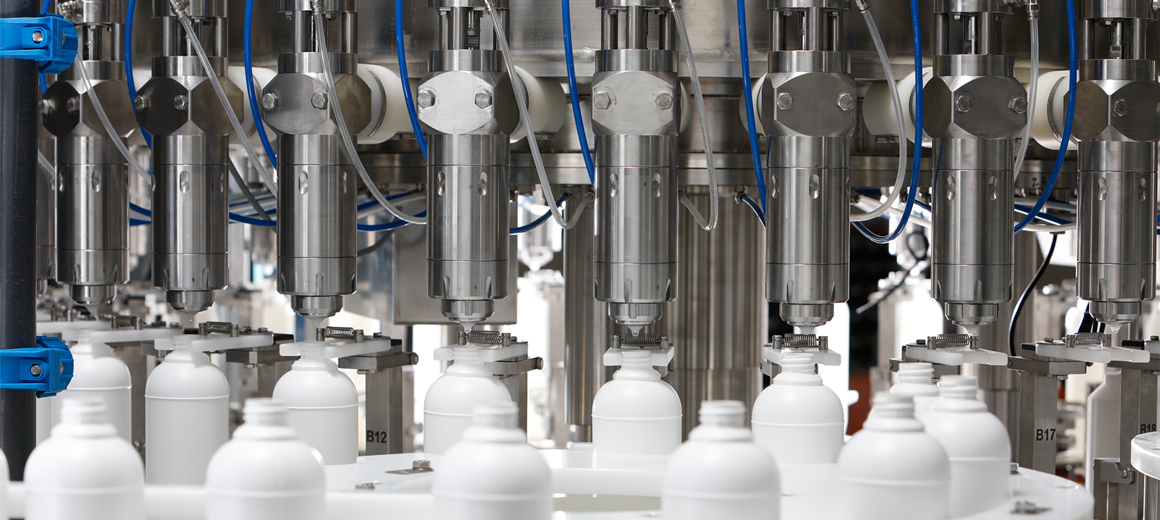
Indissolubilmente legata al nome del suo fondatore Carlo Corniani, che nel 1979 introduce la prima riempitrice rotativa a peso netto controllata elettronicamente, Weightpack ha scelto di affidare la gestione completa delle sue macchine alla tecnologia di Beckhoff. Ce ne spiega il perché il direttore tecnico Paolo Marogna.
È una storia di passione, ingegno e soprattutto di visione proiettata verso il futuro quella che caratterizza Weightpack azienda di Goito, in provincia di Mantova. È da sempre sinonimo di riempitrici ponderali di alta qualità, che l’azienda esporta in tutto il mondo in numerose versioni per il confezionamento di prodotti liquidi, densi e in polvere. Moltissimi sono i clienti che ad oggi si affidano con successo alle soluzioni di Weightpack. Come Chanteclair, leader in ambito di detersivi per lavatrice, ammorbidenti, saponi per bucato e sgrassatori, che nel suo sito produttivo di Sant’Agata Bolognese ha scelto di utilizzare per le operazioni di confezionamento dei suoi prodotti solo macchine Weightpack. Ad ogni modo, qualsiasi sia il settore e qualunque sia il prodotto o la confezione da riempire, le macchine Weightpack hanno tutte una caratteristica comune: si affidano alla tecnologia di controllo e automazione Beckhoff. Paolo Marogna, direttore tecnico dell’azienda, non ha dubbi sulle grandi potenzialità che l’architettura PC-based è oggi in grado di offrire ai costruttori di macchine innovative come Weightpack.
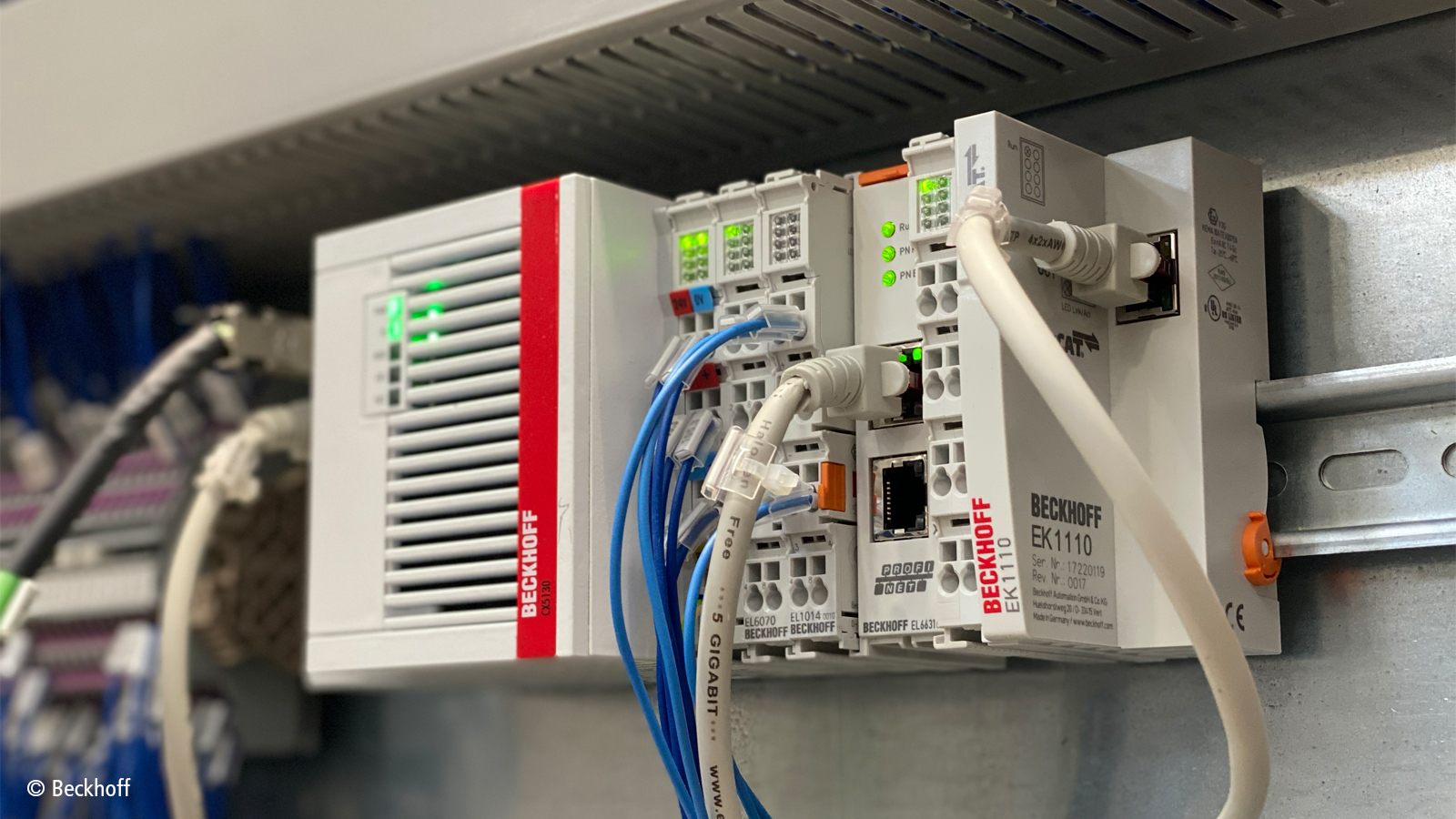
Una mission precisa: innovare
“La nostra missione è quella, in qualità di leader di settore, di perseguire tutto ciò che può apportare un miglioramento, un’innovazione e, quindi, un vantaggio ai clienti che utilizzano le nostre macchine”, esordisce Paolo Marogna. A differenza delle tradizionali soluzioni di packaging ponderale, che si avvalgono di un serbatoio a pressione costante, le macchine di confezionamento a peso netto di Weightpack si basano su un’architettura che sfrutta un diverso approccio tecnico. Brevettato dal fondatore Carlo Corniani, il sistema prevede la sostituzione del serbatoio contenente il prodotto da dosare con un collettore dotato di valvole di riempimento, alimentato da una pompa a spostamento positivo azionata da un motore brushless. Un sistema di controllo fa sì che alle valvole di riempimento giunga un flusso di prodotto esattamente pari alla quantità del prodotto che viene riempito, così da mantenere la pressione all’interno del manifold costante e, di conseguenza, garantire riempimenti precisi e ripetibili nel tempo.
Ma come fare a garantire il controllo dell’intero processo, ovvero controllare in tempo reale la pressione, gestire l’azionamento della pompa e sincronizzare gli oltre 50 assi di cui le macchine possono disporre con una precisione centesimale e in tempo reale? Ebbene, Beckhoff riveste un ruolo di fondamentale importanza. “Riconosciamo in Beckhoff, nella sua tecnologia, nei prodotti e nel supporto tecnico che offre degli elementi chiave che ci mettono in condizione di perseguire il nostro obiettivo: disporre di un’architettura performante, flessibile e scalabile con cui poter affrontare e vincere le sfide che i nostri clienti ci pongono in termini di innovazione ed efficienza”.
Il passaggio dall’era del PLC a quella della new automation
Originariamente, le riempitrici ponderali di Weightpack utilizzavano la classica architettura a logica programmabile, con PLC e pannello operatore. Nel 2012 si passa a sostituire il pannello operatore con un PC industriale, al quale vengono demandate alcune funzioni secondarie. Di fatto la strada è aperta.
Alcuni anni dopo maturano le prime esperienze con i controllori Beckhoff, che l’ufficio tecnico inizia a sperimentare per gestire la parte più delicata delle sue macchine: il controllo della pressione all’interno del collettore di riempimento e la relativa gestione della pompa di spinta del prodotto. “Oggi tutte quelle che sono le funzionalità core delle nostre macchine sono gestite da controllori Beckhoff: il sistema di pesatura, le sequenze, il motion, la gestione di tutti gli assi, non solo della stazione di riempimento, ma anche di tutte le altre parti macchina, come la tappatrice e il sistema di espulsione delle confezioni non conformi”, afferma Paolo Marogna, che si dichiara molto soddisfatto della scelta.
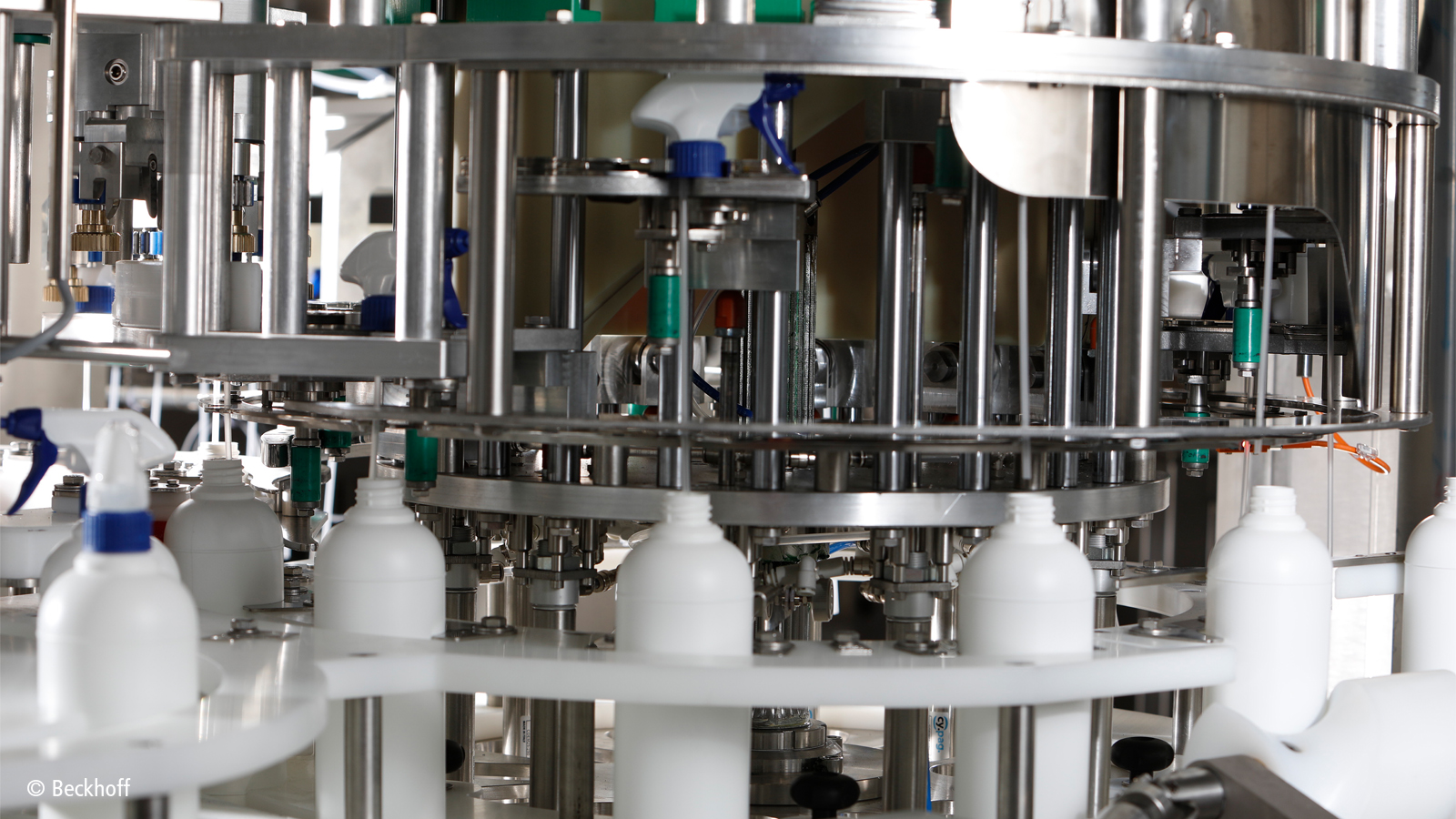
I benefici di un’architettura completa, scalabile, integrata
I prodotti Beckhoff offrono un’elevata scalabilità in relazione alle prestazioni computazionali che sono richieste dalla specifica applicazione e consentono di riunire in un’unica architettura standard, in modo semplice ed integrato, il mondo dell’automazione con quello del processo e delle infrastrutture IT, tipiche dell’ambiente di produzione in cui l’applicazione normalmente si inserisce.
La possibilità di governare con un unico controllore tutte le funzionalità della macchina costituisce un plus enorme, che semplifica notevolmente l’effort di progettazione, riuscendo allo stesso tempo a garantire prestazioni ottimizzate a livello di sistema. “Vediamo in TwinCAT una soluzione tecnologicamente completa, che se da un lato permette di sviluppare applicazioni di automazione e controllo in tempo reale, dall’altro le integra con la tecnologia tipica del mondo IT, un dominio certamente affine a quello dell’automazione digitale, ma che rimane ancora di natura prettamente informatica”, sottolinea Marogna. Il sistema di controllo è in grado di monitorare in tempo reale i manifold di riempimento, ovvero lo stato di ogni singola valvola di cui essi sono dotati, comandando la pompa prodotto in base alle richieste per modulare l’apporto di prodotto in relazione al feedback della pressione misurata all’interno del collettore.
Questa soluzione offre notevoli vantaggi, poiché consente di minimizzare il volume del circuito in cui transita il prodotto. Ciò rende la produzione non solo più efficiente, ma anche eco-friendly, in quanto le operazioni di lavaggio sono ottimizzate in termini di risparmio di detergenti, energia elettrica e di riduzione dei tempi e dei relativi costi – sia diretti che indiretti – legati ai fermi macchina.
Fondamentali le prestazioni di EtherCAT
Nelle applicazioni di automazione implementate da Weightpack, EtherCAT svolge un ruolo importante. “EtherCAT non è solo veloce, ma ha una topologia flessibile, è robusto e ha una banda tale da consentire anche la sicurezza integrata e il traffico TCP/IP, tutte caratteristiche che lo rendono una piattaforma di comunicazione versatile e universale”, dichiara Paolo Marogna.
L’utilizzo del protocollo EtherCAT, la più veloce tecnologia Ethernet industriale attualmente disponibile, porta con sé il notevole vantaggio di riuscire a controllare le applicazioni in tempo reale senza sovraccaricare il processore. Questo ha permesso a Weightpack di realizzare applicazioni con oltre cinquanta assi sincroni mantenendo errori di posizione inferiori allo 0,05%, un requisito necessario per gestire la movimentazione ad alta velocità di bottiglie, flaconi e tappi, evitando incastri o inceppamenti, nonché effettuando le operazioni di tappatura con estrema precisione.
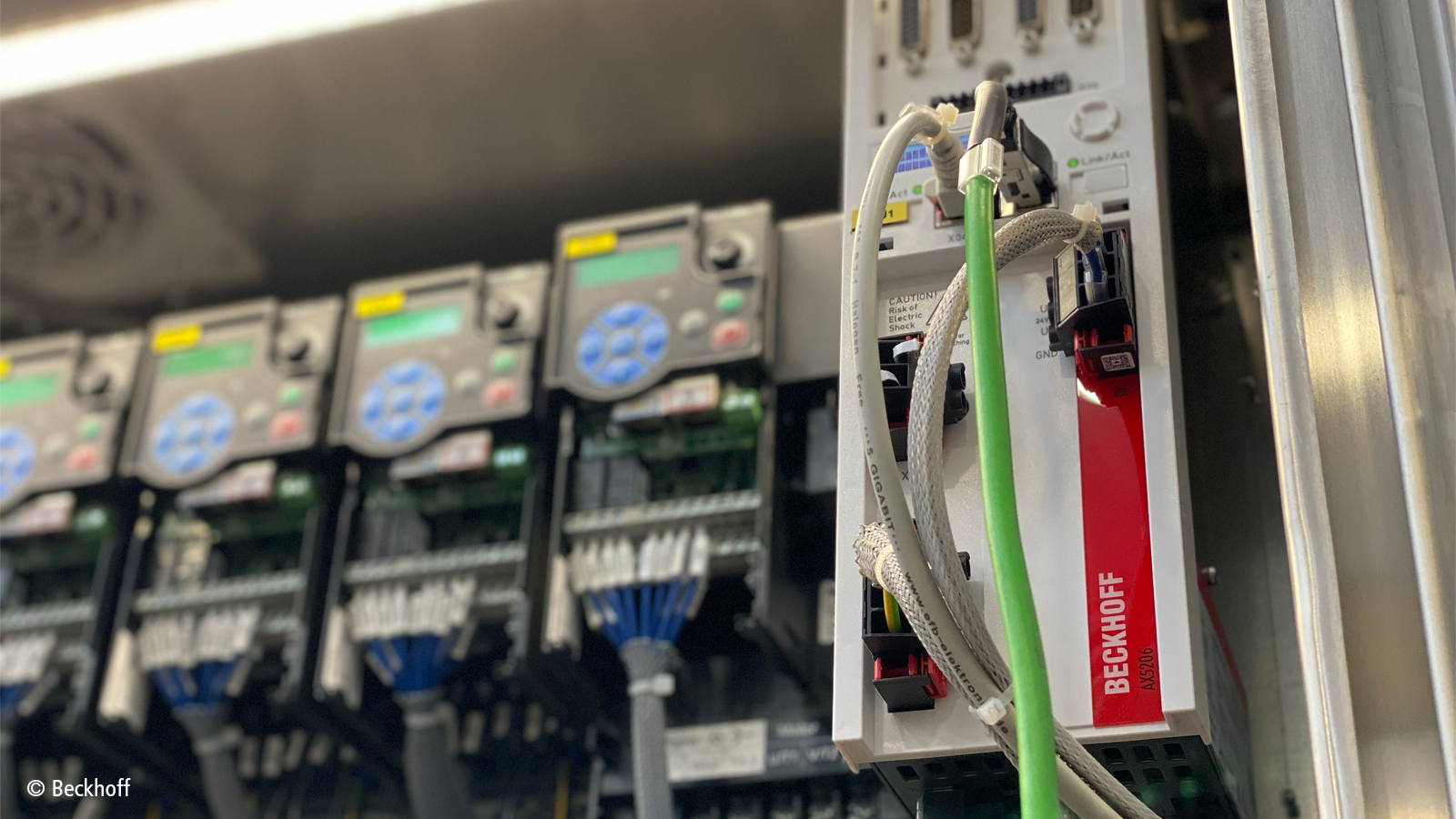
Con Beckhoff un canale sempre aperto, anche nei momenti più critici
La recente pandemia di Covid-19 e la crisi hanno impattato sulla supply-chain della componentistica, ma hanno anche suggellato una stretta partnership tra Weightpack e Beckhoff.
“Per Weightpack il periodo della pandemia di Covid-19 ha rappresentato una circostanza molto sfidante”, ricorda Paolo Marogna. “La richiesta di macchine explosion proof, cioè adatte al riempimento di prodotti a base alcolica, o capaci di gestire agenti aggressivi, quindi resistenti alla corrosione, è stata elevata e Beckhoff ci ha fornito un supporto fondamentale”. L’ampio catalogo di componenti di cui Beckhoff dispone, nonché la scalabilità delle sue soluzioni, ha permesso di sopperire in modo puntuale alla mancanza di specifici prodotti con una serie di altre soluzioni. Beckhoff, infatti, in quel periodo aveva espressamente dato priorità a tutte le richieste provenienti da quelle aziende che, proprio come Weightpack, avevano in essere progetti e attività destinati a far fronte alle emergenze in atto. Il confronto con la parte commerciale e con il supporto tecnico messo a disposizione dai tecnici Beckhoff non è mai venuto meno, nemmeno nei periodi più critici. È stato anche grazie a questa continuità che Weightpack è stata in grado di adeguare di volta in volta le architetture che prendevano forma in relazione ai componenti che in quel momento erano disponibili.
Già al lavoro per il futuro
Weightpack ha recentemente avviato un importante progetto che mira a utilizzare l’intelligenza artificiale per trarre informazioni strutturate dalla mole dei dati che possono essere fruiti da tutto l’equipaggiamento elettrico delle sue macchine. Ciò, ad esempio, per ottimizzare le performance dal punto di vista energetico, per ridurre al minimo i fermi macchina grazie a un supporto informativo mirato in ottica di manutenzione predittiva; o ancora per suggerire i settaggi migliori per raggiungere le performance ottimali. “In Weightpack siamo certi che puntare su una soluzione strutturata, ma al tempo stesso completamente standard, come quella basata su un’architettura di automazione PC-based, sia la scelta migliore. Ed è per questo che siamo convinti che Beckhoff sia il partner giusto per raggiungere gli obiettivi che ci siamo posti, ovvero offrire ai nostri clienti macchine performanti e in linea con le loro esigenze”, conclude Paolo Marogna. È questo il motivo per cui Weightpack punta all’obiettivo di un’architettura full Beckhoff per tutte le sue macchine. Già quest’anno l’azienda ha in essere due progetti pilota volti a integrare la safety e la visione.