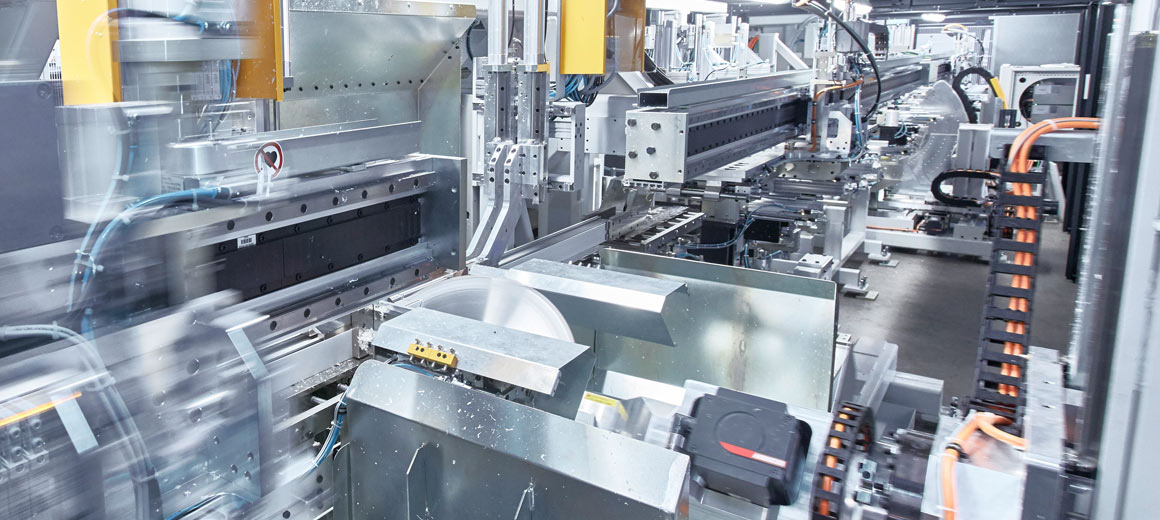
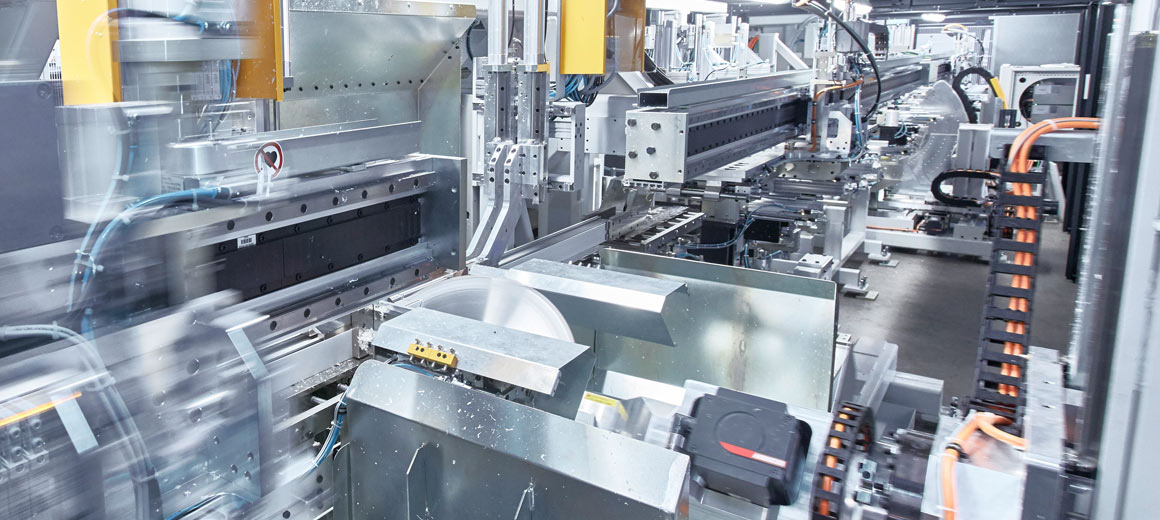
Today, a globalized market and the ever-increasing demands of end customers for product quality, individualization and cost reduction are having more of an impact on mechanical engineering than ever before. Development times from an idea to the finished machine are getting shorter, while modularity and connectivity are increasing at the same time. Innovative digitized service and maintenance concepts are therefore becoming more of a focus for end customers.
Far beyond the basic functionality, machines must provide optimal production capability in the long term, continuously supply information on energy and resource consumption, and be easy to integrate into existing information structures. Modular machine concepts require a flexible construction kit system from which designers and engineers can select the components for control, drive technology, I/Os and safety technology. New business models, e.g., for predictive maintenance or usage-based billing, require detailed information from the machine and the provision of data to the machine manufacturer or maintenance provider.
A faster machine will only be successful on the market through combination with optimal use of resources and sustainable communication technology. The technical information necessary for this can be recorded very precisely, continuously and with extensive diagnostics by machine-integrated measurement technology from the Beckhoff I/O system. Machine manufacturers can meet these high requirements with deep integration and interaction with PLC libraries for signal analysis.
The important parameters can be optimized with controller-integrated measurement technology and software from Beckhoff:
Optimal production:
- Integrated: high-quality, fast measurement modules within the controller for synchronous signal acquisition and full data access
- Flexible: signal conditioning and filtering in the module or PLC and flexible processing of the measured signals in the PLC
- Precise: high measuring accuracies allow smaller tolerances, more accurate process control and better resource efficiency
- Cost-effective: direct integration saves external computers, data loggers, synchronization mechanisms or connectivity
- Scalable: from standard terminals to calibrated 24-bit measurement modules − the right product for every measurement task
- Traceable: assurance of high measurement quality with ISO17025/DAkkS calibration certificates, also as recalibration
Transparent energy and condition information:
- All process information and measuring signals are available in the control system at any time and in full.
- Energy measurement with different complexities: from power quality factor (PQF) to harmonic and differential current measurement..
- Product-related energy data can easily be calculated in the controller and stored in production databases.
- Integration of condition monitoring through system-integrated measurement technology and condition monitoring PLC library.
- In-depth diagnostics: from the EtherCAT fieldbus and measurement technology to the PLC for maximum reliability in production use.
Integration into the existing infrastructure:
- Support for all fieldbuses and communication via OPC UA facilitates the integration
- Control of communication paths through central controller, no subsystems with additional connectivity required
- Support for SQL/NoSQL databases
Further information about our technologies and products for system-integrated measurement technology for machine building can be found here: