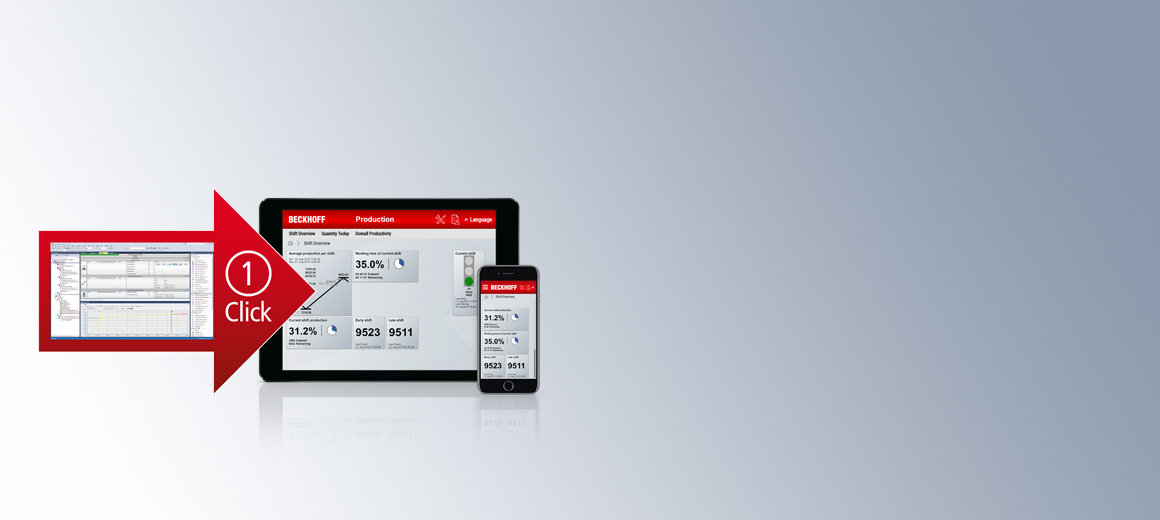
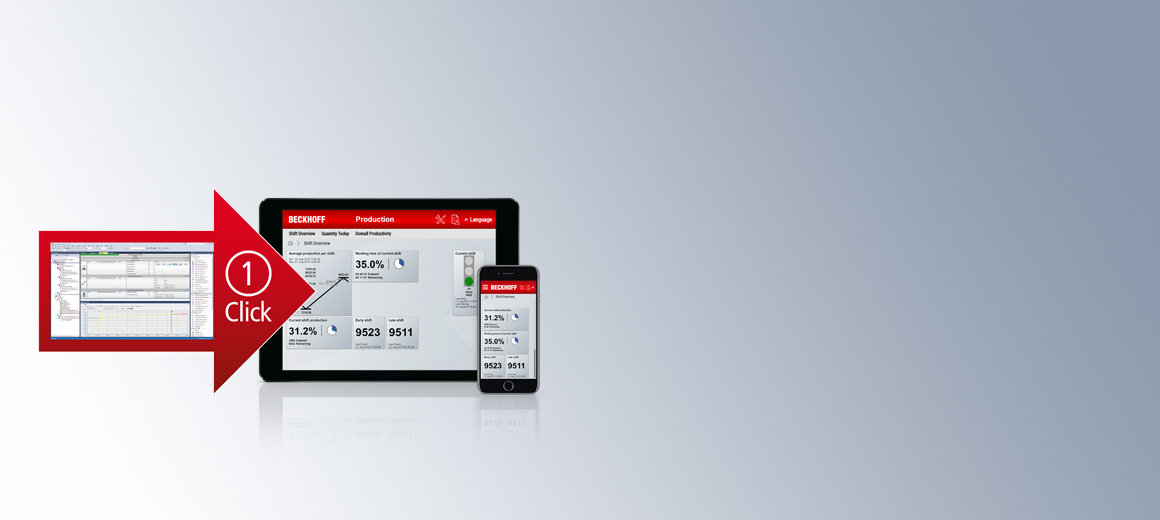
Since on-premises applications are increasingly being moved to cloud systems, the need for machines and systems to feed their production and status information into these systems is also increasing. In this way they become part of an Industrial IoT system, independent of a platform or an end device. Conventional proprietary communication protocols are being replaced by OPC UA, MQTT or REST and therefore become independent of manufacturers and tools.
Digital business models are increasingly designed 'as a service' and grow with the user's demands on the service. Streaming analytics and added value generation are shifting to cloud applications and are decoupled from the data source and the end device. For machines and systems acting as data sources, this means they must be made fit for IoT-capable communication. This can be achieved by retrofitting with IoT couplers, I/O components and sensors, which enables the machines to supply production and status information to higher-level systems. Due to limited resources and bandwidth in data communication, they often take on specific analysis tasks as decentralized edge devices, for example for the evaluation of fast measured data.
User behavior has also changed: increasingly, mobile phones and tablets are being used as working tools to access a wide range of data sources. With modern HTML5-based visualizations and responsive web design, users are free to use end devices of their choice. This also leads to a change in engineering: away from static programming, which remains unchanged over extended periods, to dynamically changing analyses and visualizations. User groups are also becoming more heterogeneous. For example, a service technician needs a more detailed view of individual process data than a production manager or business intelligence analysts who evaluate machine cycles and optimize a production process, for example.
The key issues:
- Use of modern cloud infrastructure and data communication
- Digitization of existing systems and integration into the cloud infrastructure
- Provision of visualizations and reports for the end user
- Simplified and accelerated engineering and deployment on the target system
- Easy expandability of the IoT system and the interfaces to higher-level systems
Beckhoff provides a wide range of hardware and software products for modern and scalable IoT systems:
- From simple IoT couplers (EK9160) with integrated IoT protocols (OPC UA and MQTT) to highly scalable, PC-based control technology and IoT PLC libraries.
- PLC libraries for OPC UA, MQTT, REST and IoT Data Agent as gateways between machine and cloud.
- Connection to cloud services like Amazon Web Services, Microsoft Azure™ or private clouds.
- The TwinCAT Analytics Logger records process and application data from the real-time environment synchronously with the cycle, sends them to a message broker via IoT protocol or saves the data locally on the controller.
- In the TwinCAT Analytics Workbench, analysis workflows are defined in graphical programming that can be extended with custom PLC programs. The dashboard for the analysis can be generated with one click and loaded onto the runtime.
- Fast EtherCAT fieldbus on the machine side: the entire I/O range of terminals and box modules is available for the acquisition of machine data.
Further information about our technologies and products for scalable IIot systems can be found here: