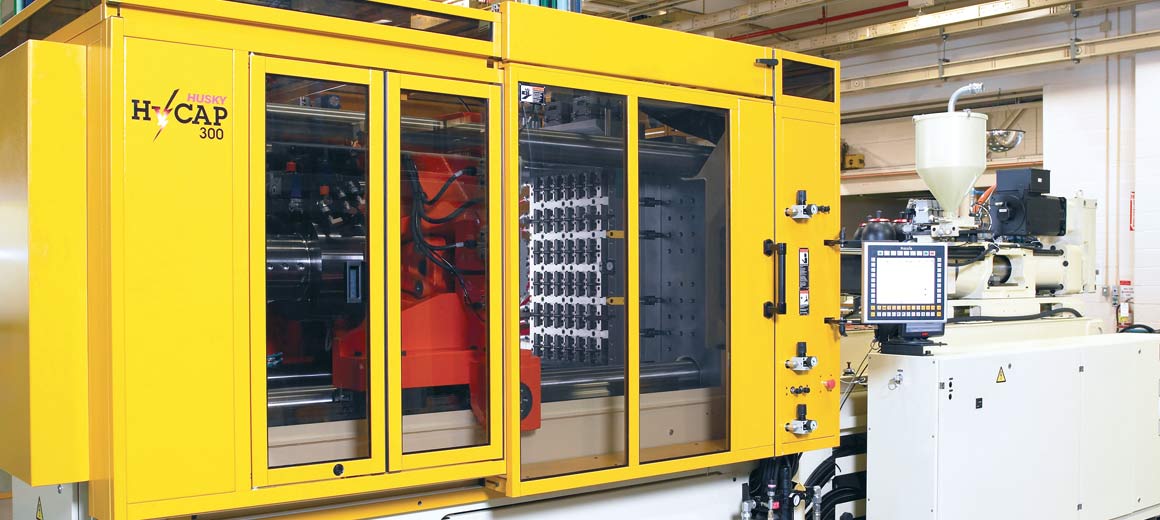
PC-based control lowers consumption of raw materials
Husky Injection Molding Systems, Canada
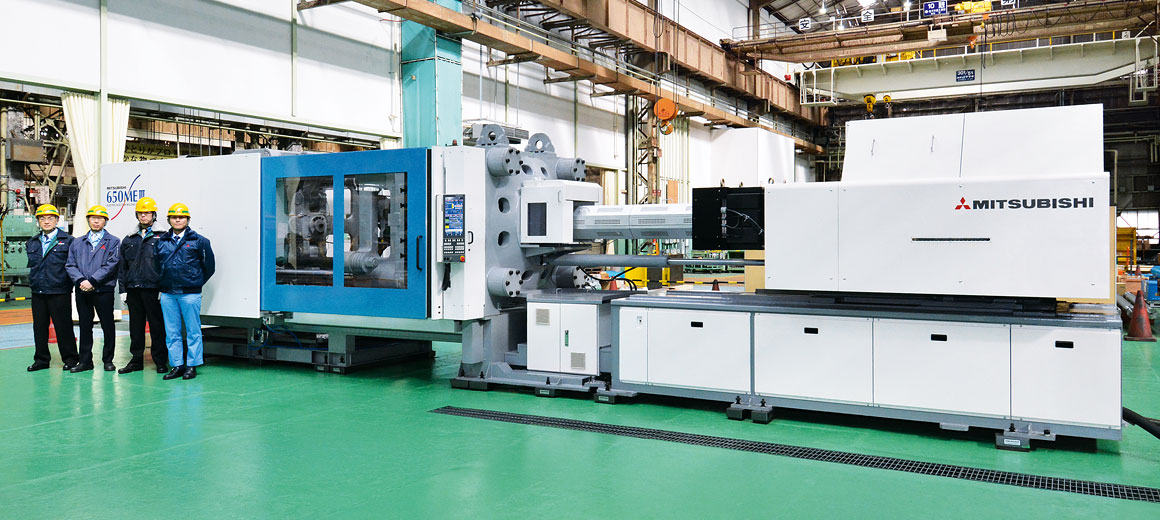
PC Control optimizes injection molding machines
Mitsubishi Heavy Industries Plastic Technology, Japan
Headquarters United States
Beckhoff Automation LLC
+1 952 890-0000
beckhoff.usa@beckhoff.com
www.beckhoff.com/en-us/
Husky Injection Molding Systems, Canada
Mitsubishi Heavy Industries Plastic Technology, Japan
Beckhoff has been a development partner for the "first choice" companies in injection molding for many years. From individual components to the complete solution, the user benefits from Beckhoff's broad process and application know-how in plastics processing. The high demands of high-performance injection molding machines were a major motivation for Beckhoff to develop the extremely fast communication technology XFC (eXtreme Fast Control). XFC increases the accuracy of < 100 ns when switching from injection to holding pressure, thus improving part quality and reducing material consumption.
The development of EtherCAT plug-in modules for use on customer-specific backplanes for large-volume applications was driven by the desire to minimize wiring errors and achieve cost savings in switching production for small and medium-sized machines.
The FM3312 and FM3332 Fieldbus Modules in a sturdy metal housing are suitable for temperature measurement on injection molds or on injection barrels. Up to 32 temperature channels can be contained in one industrial connector. Operational reliability is additionally ensured by reverse polarity protection against phase voltage.
Beckhoff's many years of experience in hydraulic and electric drive technology or temperature control led to the development of injection molding-specific engineering platforms. Machine manufacturers can use Beckhoff's industry know-how or incorporate their own process knowledge – also in combination with the tested application modules, for example for temperature control.
Through support for the vendor-neutral Euromap standards based on OPC UA, EtherCAT as a fast fieldbus and TwinCAT as a universal engineering platform, the Beckhoff controller enables the realization of a wide range of heterogeneous production cells.
The Beckhoff solution for injection molding machines is based on a universal hardware and software platform. It comprises an extensive portfolio of Industrial PCs, EtherCAT as a fast communication system, the decentralized I/O modules, drive technology components and TwinCAT automation software. The latter serves as a software platform for engineering, runtime and the diagnosis of all control functions: from PLC, motion control and robotics to HMI and vision, and from safety and measurement technology to cloud communication and analysis functions. On the one hand, this ensures the efficient interaction of all system components and thus maximum productivity. On the other, special devices can be omitted due to the consistent implementation of all functionalities as software modules. This reduces not only hardware costs, but also engineering effort and lifecycle costs.
In order to meet the high market requirements for product quality, functionality and efficiency, machine manufacturers have extensive software and hardware components from the Beckhoff product and technology portfolio at their disposal:
With the TwinCAT 3 Plastic Framework, we offer a modular software solution for the control of plastics machines that minimizes development effort and maintains the open nature of Beckhoff architecture. The TwinCAT 3 Plastic Framework brings together our many years of expertise in plastics, seamlessly integrating important industry-specific functions into the established TwinCAT environment. As a result, plastics machines can be programmed, visualized, and controlled on a single platform.
The TwinCAT 3 Plastic Framework contains three software libraries: TF8540 enables comprehensive software-based temperature control in plastics processing. TF8560 is a technology package that provides all the components for controlling motion functions in plastics machines. TF8550 is an HMI package specially developed for the plastics industry that enables the visualization of typical processes with minimal engineering effort and integrates seamlessly into the other technology packages.
Integrated, application-specific templates and sample code for various plastics applications facilitate project planning and programming, and are made available free of charge via the TwinCAT 3 Plastic Application. Of course, existing templates can also be used and your own process expertise can be integrated.
TF8540: Plastic Processing Framework
TF8560: Plastic Technology Functions
TF8550: Plastic HMI Framework