In addition to the core processes in plastics processing, there are important technologies for the further processing of plastic preliminary products. A distinction is generally made between thermal and non-thermal processes in post-processing.
The advantages of the innovative Beckhoff technology for the post-processing of plastic parts:
- Open, platform-independent control technology makes development expenditure sustainable.
- High-performance, scalable control technology improves productivity and offers an optimal price-to-performance ratio.
- I/Os for all common signal types and different environmental conditions support a modular machine design.
- A wide range of drive components in different performance classes, including the innovative XTS and XPlanar transport systems, make completely new machine concepts possible.
- EtherCAT, as a fast fieldbus, brings the high system performance to the sensors/actuators and also allows the use of third-party components, e.g., in drive technology.
- The large Beckhoff component portfolio and EtherCAT as a fieldbus that is perfectly integrated in TwinCAT allow the construction of complete production lines, including filling stations and packaging.
Beckhof technology optimizes the post-processing of plastic parts
Post-processing of semi-finished plastic products without repeated thermal treatment
Extrusion lines or foil machines integrate the post-processing processes such as trimming, cutting to length or winding; these machine modules are often equipped with their own Beckhoff control system. For joining processes and ultrasonic welding, Beckhoff offers among other things compact drive technology with integrated motion control as well as the appropriate temperature control algorithms. For the assembly of plastic components, for example in the production of medical products, Beckhoff customers have a broad portfolio of drive components at their disposal, including the XTS linear transport system. Vision products are also increasingly being used in this area. XPlanar has also been used for the first time as a flexible, fast workpiece carrier for coating. An important technology in the field of packaging foils is printing. More detailed information on Beckhoff solutions for printing applications can be found here.
The following processing steps for plastic pre-products are widely used:
- trimming, cutting to length, winding
- joining, gluing, ultrasonic welding
- coating
- printing
- assembly
For these processes, Beckhoff offers solutions from its rich product portfolio:
- TwinCAT as engineering software with integrated Motion Control functions
- drive components, including the innovative XTS and XPlanar transport systems
- I/Os for all common signal types and different environmental conditions
- high-performance Industrial PCs and a wide variety of operating devices
- various fieldbus interfaces for connecting post-processing machines with their own controller
PC-based control optimizes the further thermal processing of plastic products
Thermal post-processing determines the geometry and mechanical properties of the preform. Widely used methods are stretch blow molding and the thermoforming process. Beckhoff's PC-based control technology is used for these production processes, with TwinCAT as the engineering platform. Of particular interest here are the motion control solutions from Beckhoff for hydraulic and electric axes, the extensive drive technology portfolio and the high system performance of the PC-based control technology in conjunction with EtherCAT. Beckhoff operating devices with HTML5-based visualization open up web-based operating concepts.
Thermoforming/deep drawing
The input materials for the thermoforming process are plastic flat foils, which are produced in an extrusion process. In the thermoformers, the plastic film is heated and brought into the desired shape by thermoforming tools/stamps.
Beckhoff optimizes the thermoforming process through:
- open, PC-based control technology with advanced path control, e.g., for non-linear gear unit functions (cam plates)
- temperature controllers for foil heating by means of infrared radiators
- hydraulic software library for hydraulically driven deep-drawing tools
- compact drive technology and motor-integrated drives for the realization of a compact, modular machine design
- HTML5-based process visualization with prefabricated framework controls for visualizing the temperature controllers
Stretch blow-molding process
Two-stage production processes are also common in the production of plastics, such as in the production of PET bottles. First, a so-called preform is produced in an injection molding process. In the second stage of production, the heated preforms are stretched with the help of the stretch blow molding process and inflated to the desired shape in a mold by pressing in air. Beckhoff supplies automation technology for both production steps. Husky Injection Molding Systems, the market leader in the production of preforms, has been using Beckhoff technology for more than 20 years.
The Beckhoff development criteria for the production of preforms:
- Open, platform-independent control technology makes development expenditure sustainable.
- High-performance, scalable controllers contribute to material savings.
- EtherCAT as a fast fieldbus allows the use of third-party components, e.g., drive technology.
- Flexible automation technologies enable easy integration into production cells.
Beckhoff technology highlights for post-processing
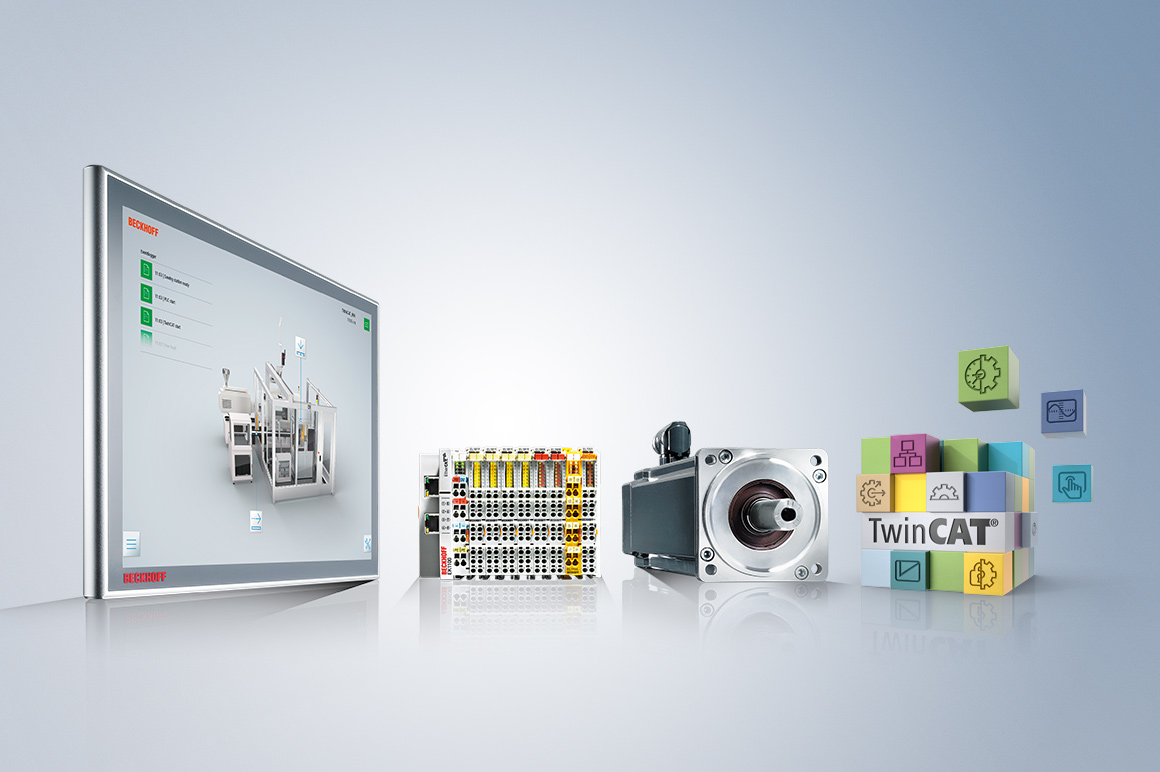
The PC-based control principle
With PC-based control technology, we offer comprehensive system solutions in various performance classes for the automation of all types of plastics machines. The basic principle is based on a powerful industrial PC, a high-performance fieldbus connection with the connected peripheral devices for sensors and actuators, and the software for engineering and real-time control. The control platform is supplemented by an extensive portfolio of drive components. TwinCAT automation software bundles all necessary functionalities such as PLC, motion control, robotics, measurement technology, image processing, and HMI. Our technology is based on IT standards and has the necessary openness to implement intelligent production concepts according to Industrie 4.0.
Due to the high performance of modern processors, which we install in all of our PC series, computationally intensive applications can easily be integrated into the control platform. Plastics machine manufacturers benefit from the continuous increase in the performance of PC processors: Shorter sampling times are already increasing the quality of the end product today and will be the requirement for the realization of self-learning machines in the future. The possibility, for example, to completely simulate an injection molding machine in the virtual design process saves time during development and commissioning.
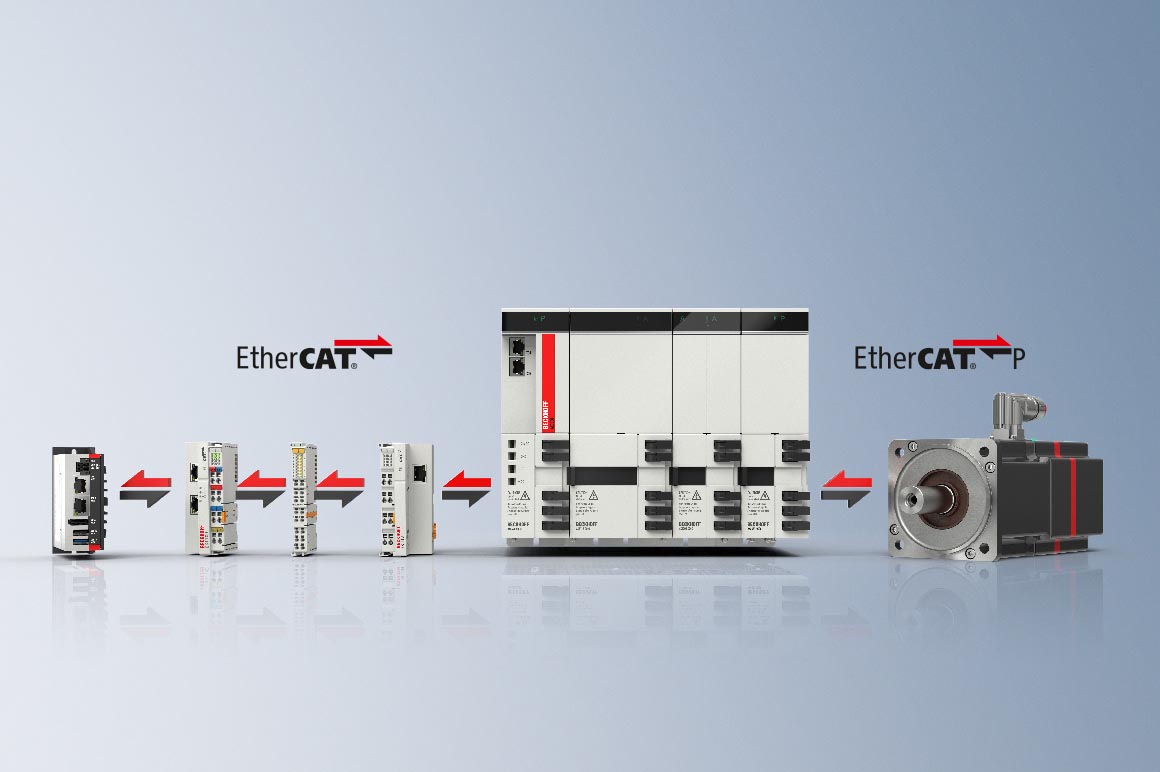
EtherCAT: World standard for plastics machines
The EtherCAT technology was launched on the market by us in 2003 and made available as an open standard for automation technology. With outstanding performance, flexible choice of topology, comprehensive diagnostics and simple configuration, EtherCAT is ideally suited for use in plastics machines. We offer the largest number of EtherCAT-compatible automation modules for I/Os and for drive technology.
EtherCAT is one of the most widely used standards in plastics technology. A large number of EtherCAT-compatible sensors and actuators are available on the market, which guarantees a high level of investment security. Particularly interesting for electrically driven injection molding machines is the problem-free connection of drives from third-party suppliers. Other fieldbus systems can also be integrated as communication layers via EtherCAT.
The fast and high-precision Beckhoff control solution eXtreme Fast Control (XFC) is based on EtherCAT and special I/O modules optimized for XFC that record signals or trigger actions with high accuracy. With I/O response times under 100 μs, XFC enables very fast and extremely deterministic reactions and thus contributes to process optimization.
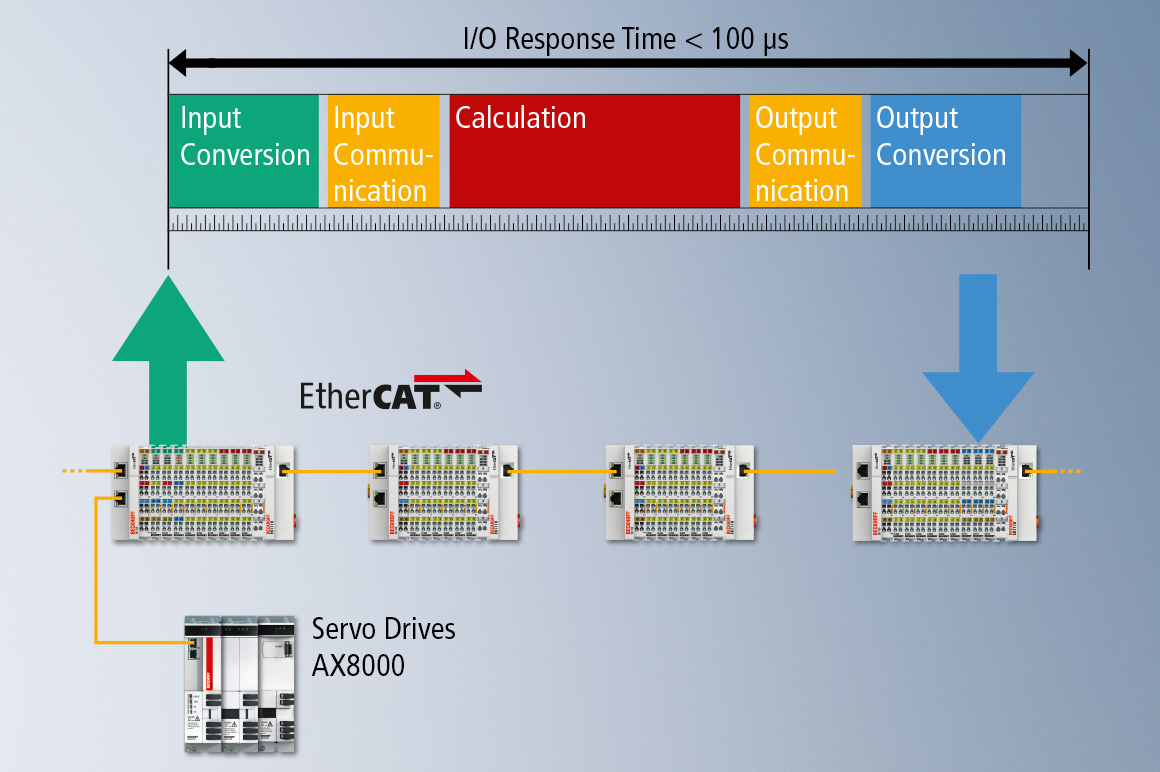
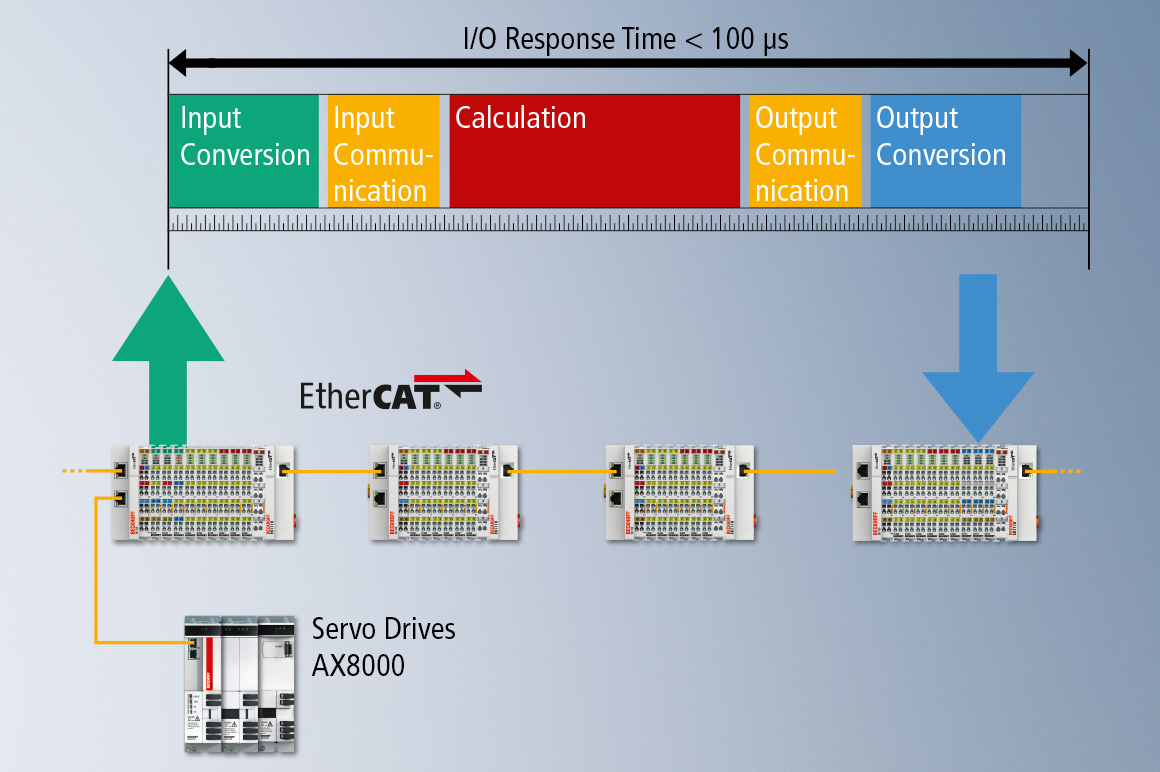
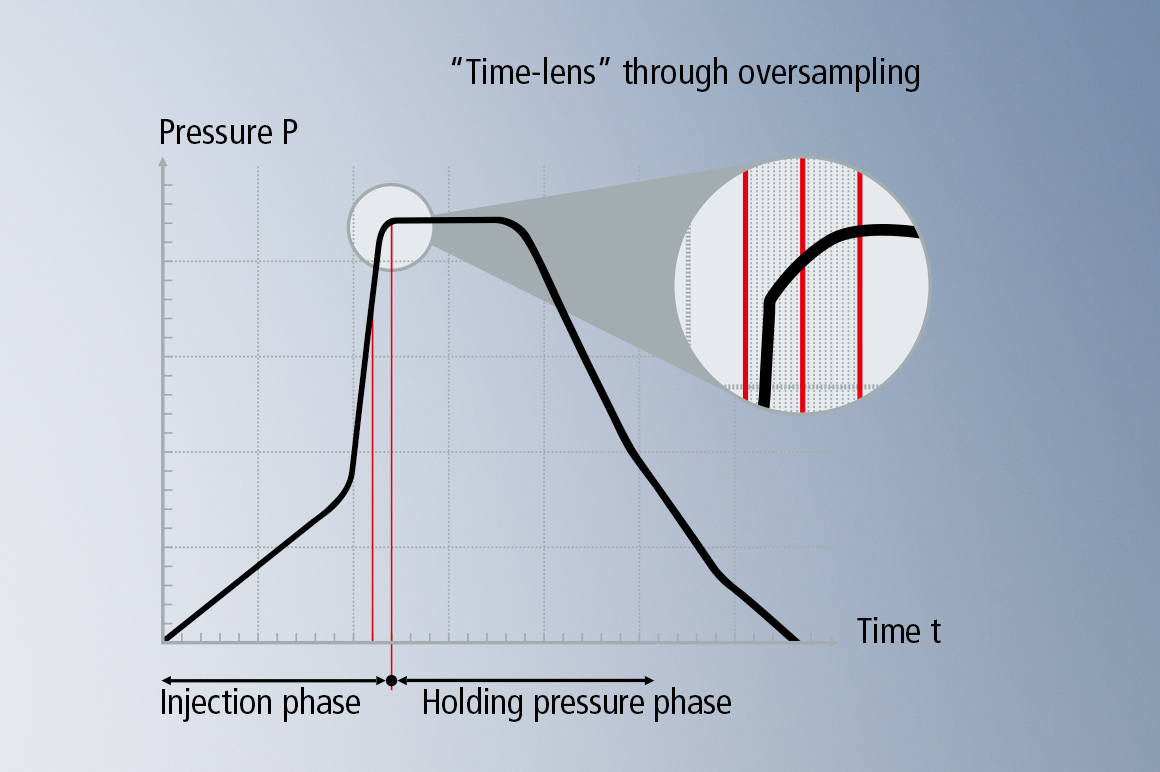
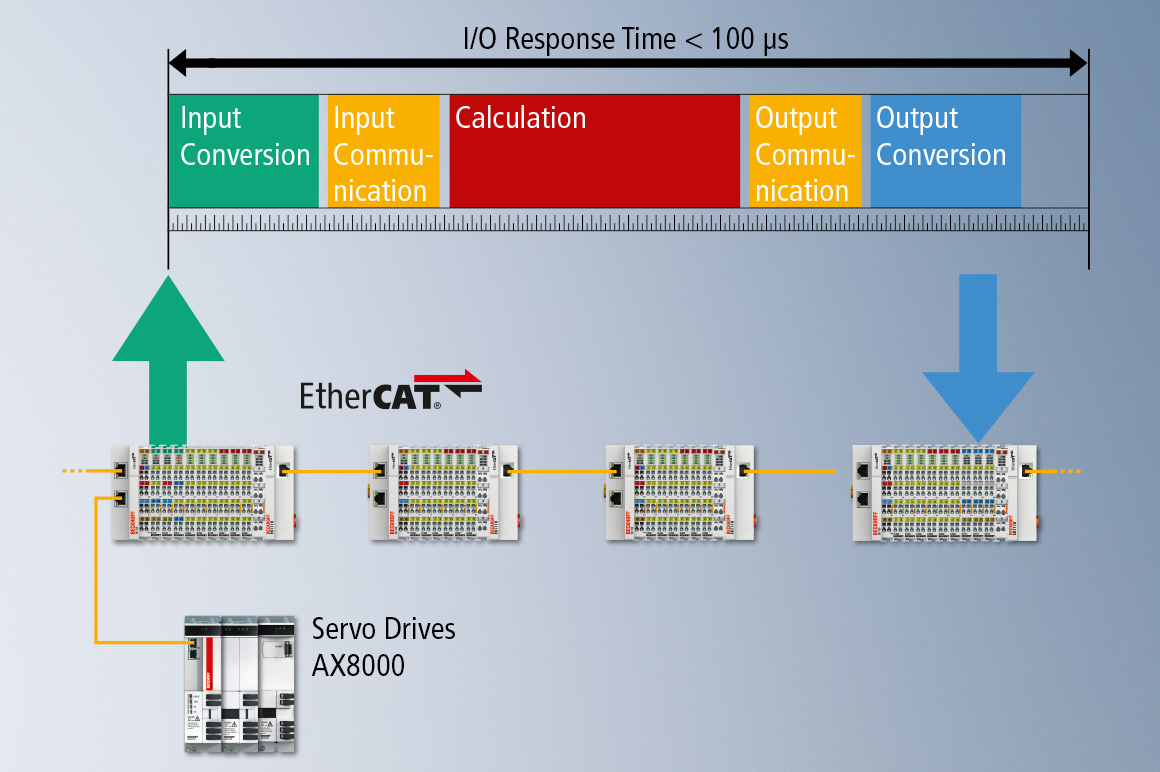
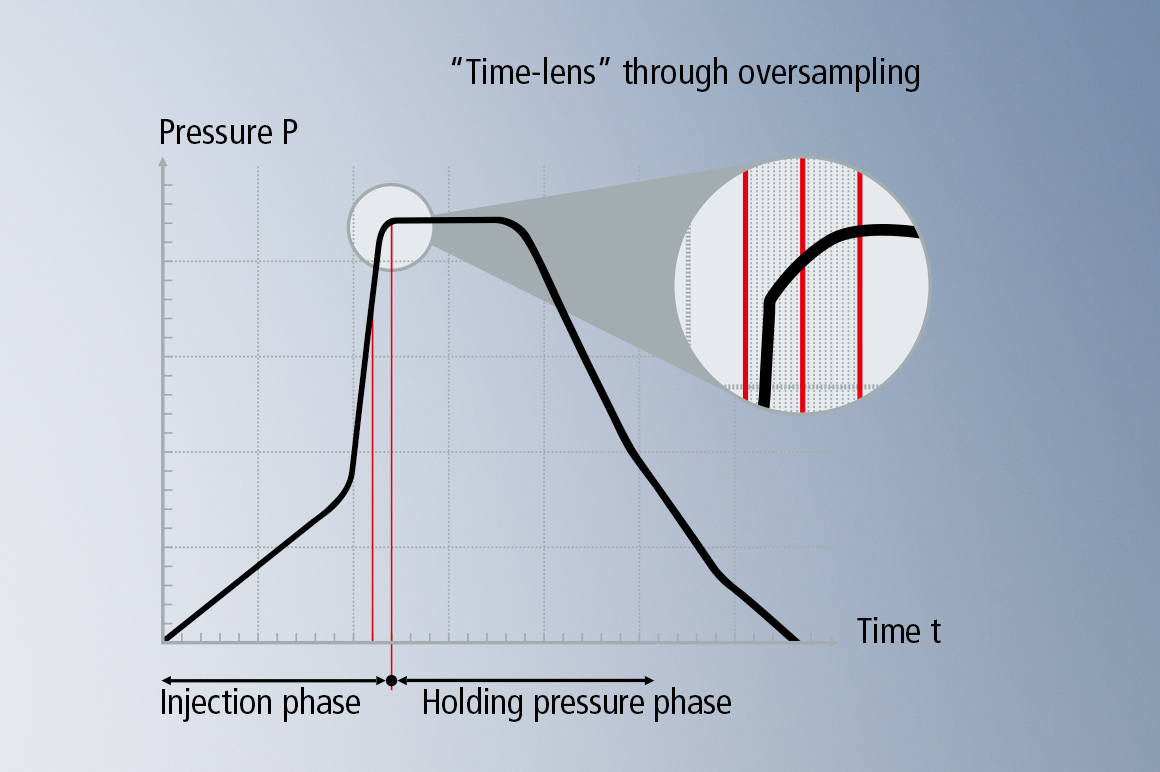
Maximum production efficiency with XFC
The fast, high-precision eXtreme Fast Control Technology (XFC) developed by us reduces the raw material consumption and increases parts quality. I/O response times of less than 100 µs can be achieved with a powerful industrial PC, the ultra-fast EtherCAT I/O terminals, EtherCAT as the communication system and the TwinCAT automation software. Logging of highly variable input signals with high temporal resolution enables precise control of the injection molding process. Fast algorithms enable the magnitude and trend of the control value to be precisely calculated as a function of the switching event time. The working window becomes narrower, while part weight fluctuations and raw material consumption are reduced. High-precision servo drive technology, in conjunction with XFC, increases the reproducibility of the injection molding process even further. XFC also enables the integration of measurement technology into the machine control system, eliminating the need for special hardware. This way, it is possible to implement a cost-effective solution for condition monitoring, for example, which can extend the service life of machines and minimise downtime through preventive maintenance.
The acquisition of rapidly changing input signals with high temporal resolution makes it possible, for example, to precisely control the injection process in injection molding machines, especially with servo-electric drive technology. Fast algorithms enable the magnitude and trend of the control value to be calculated precisely as a function of the switching event time. This reduces part weight fluctuations and material consumption.
The oversampling technology based on XFC makes the signal curve exactly determinable. In combination with the timestamp function of EtherCAT, which links each event with a precise point in time, the reproducibility of procedures is increased significantly compared with conventional solutions.
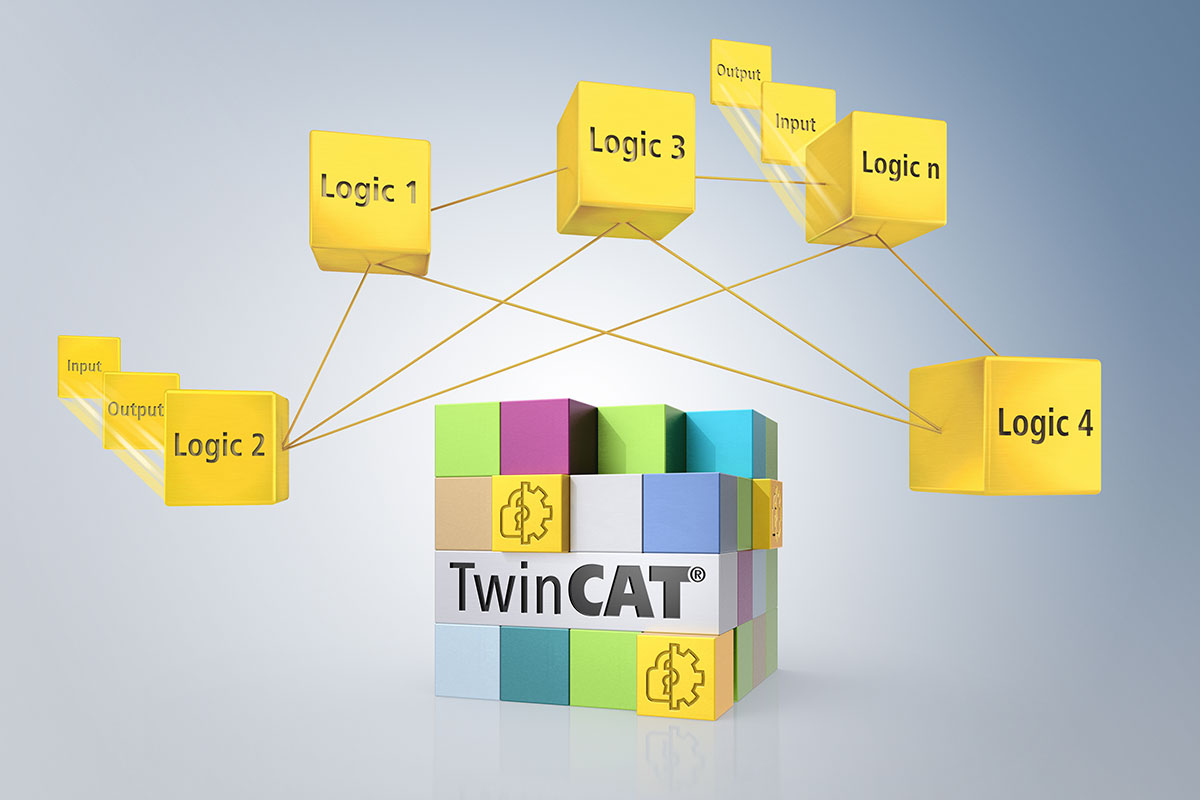
TwinSAFE: The open and scalable safety technology
With TwinSAFE, we have implemented a consistent safety concept that integrates safe functionalities into the non-safety-related control architecture. Separate safety controllers are thus superfluous. The typical safety functions can be programmed and configured on the EL6910 TwinSAFE Logic or the compact EK1960 safety controller, based on standard safety function blocks according to the safety requirements. The Beckhoff safety solution accelerates the engineering process, as the safety-related requirements of different machine configurations can be realized by software. All our safety controllers are suitable for applications up to SIL 3 according to IEC 61508 or PLe of ISO 13849-1 and meet the EN 201 standard for injection molding machines.
Safety technology seamlessly integrates into the terminal segment via the TwinSAFE I/O modules, whereby safe signals can be mixed with standard signals as required. This benefits, for example, blow molding machines or production cells with control cabinets in different installation locations. Due to its scalability, the Beckhoff safety solution is suitable for expansive, complex systems with distributed I/Os as well as for small injection molding and blow molding machines. One safety logic is sufficient here to realize the complete safety technology. The compact EK1960 safety controller is particularly suitable for injection molding machines with hydraulic and/or electric drives. It allows the direct control of digital switching valves with a load of 2 A, such as those used in core pullers. With the help of the TwinSAFE SC technology, signals with a low safety level can be used redundantly for safety tasks.
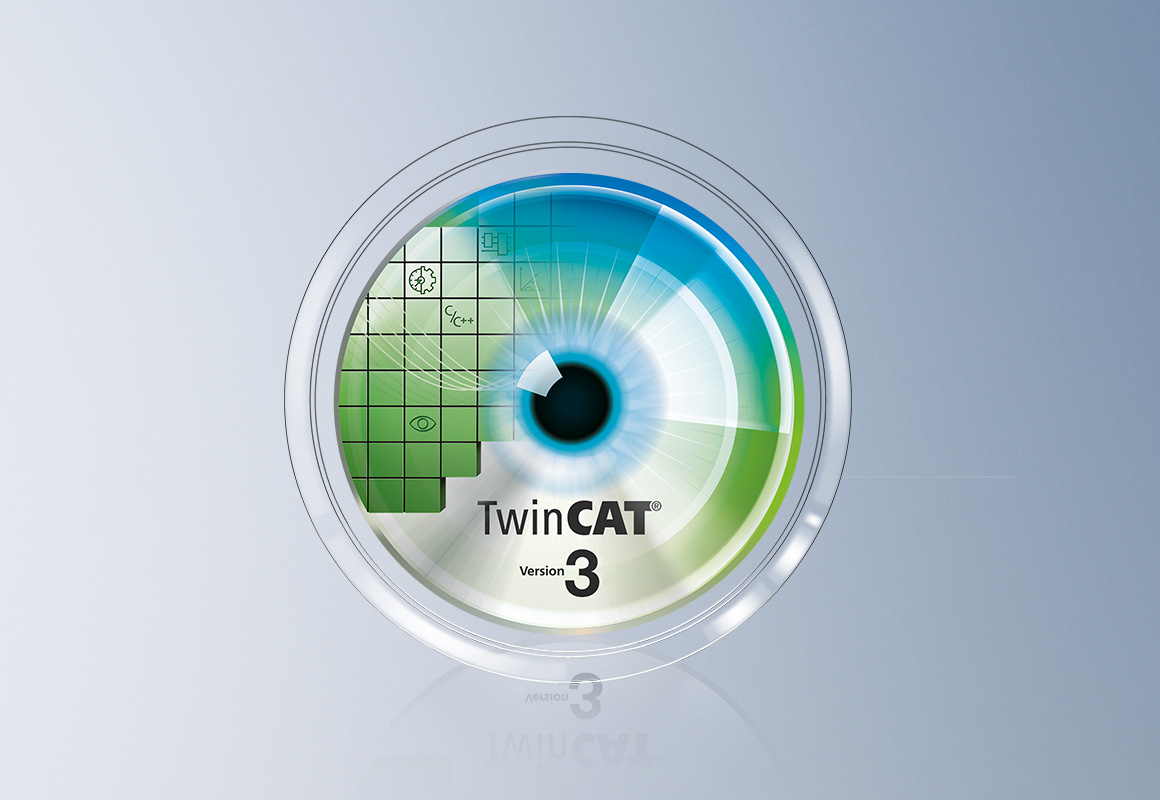
Image processing integrated into the controller ensures the quality of the parts in plastics processing
Optical quality monitoring has long been known in plastics technology. However, due to integration costs and the lack of complete solutions, it has not yet established itself as a standard. The approach of PC-based control technology offers the ideal solution here: with TwinCAT Vision, Beckhoff integrates the image processing functionalities completely into the familiar engineering environment of the machine programmer, which makes programming and testing much simpler. All control functions derived from image processing, such as the exact determination of the position of the workpiece as well as the triggering of the camera and the light source, are synchronized in real time. This is a key advantage of the integrated image processing solution over separate systems.
The vision solution from Beckhoff is ideally suited in the plastics industry for process monitoring, e.g., for the ejector, for determining the part geometry and for position orientation.
Advantage through TwinCAT Vision
- Improvement in quality: Precise measurement and exact optical inspection ensure compliance with the process parameters.
- Increase in efficiency: The synchronous inline measurement of parts without a separate measuring station improves efficiency.
- Quality assurance: Applications such as Track & Trace enable the traceability of product quality for each individual part, such as is required for safety-critical applications in the medical technology sector or for special automotive parts.
- Temperature measurement: The surface temperature of plastic parts can be determined with the help of thermal imaging cameras.
- Machine Learning: Inferences between machine settings and part geometries are a prerequisite for the development of learning algorithms as a milestone towards intelligent, self-learning machines.
Beckhoff product highlights for post-processing
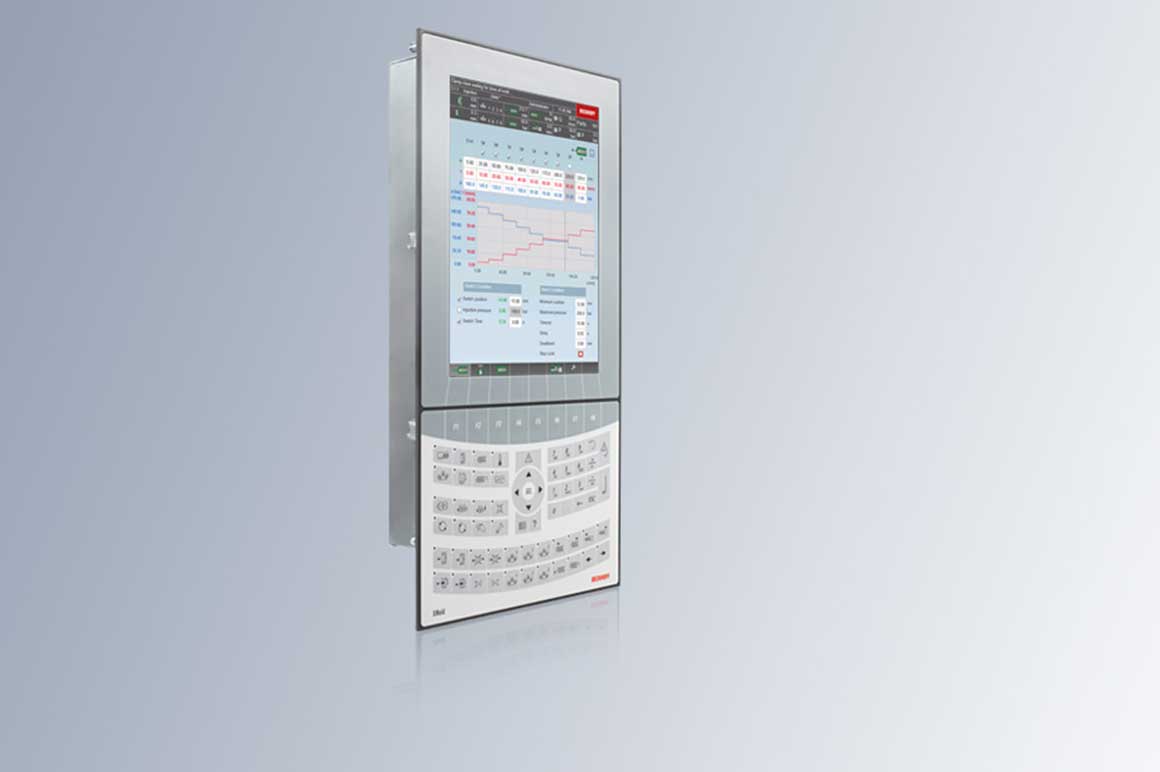
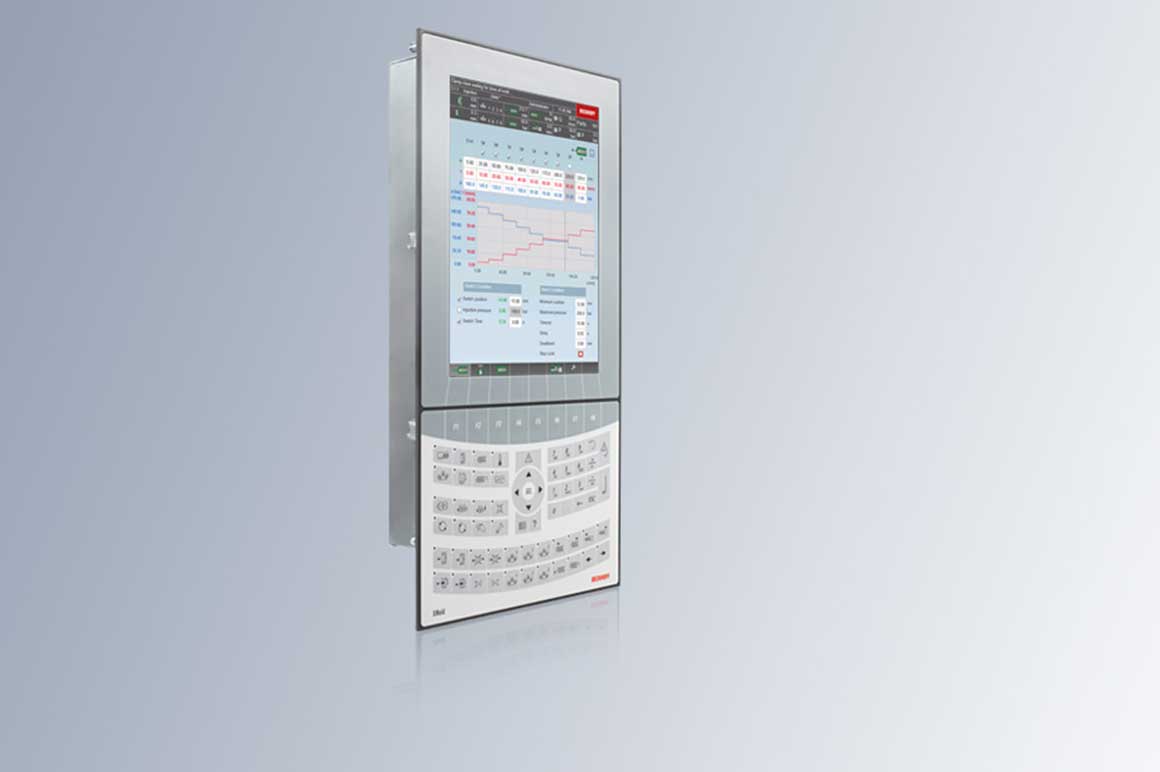
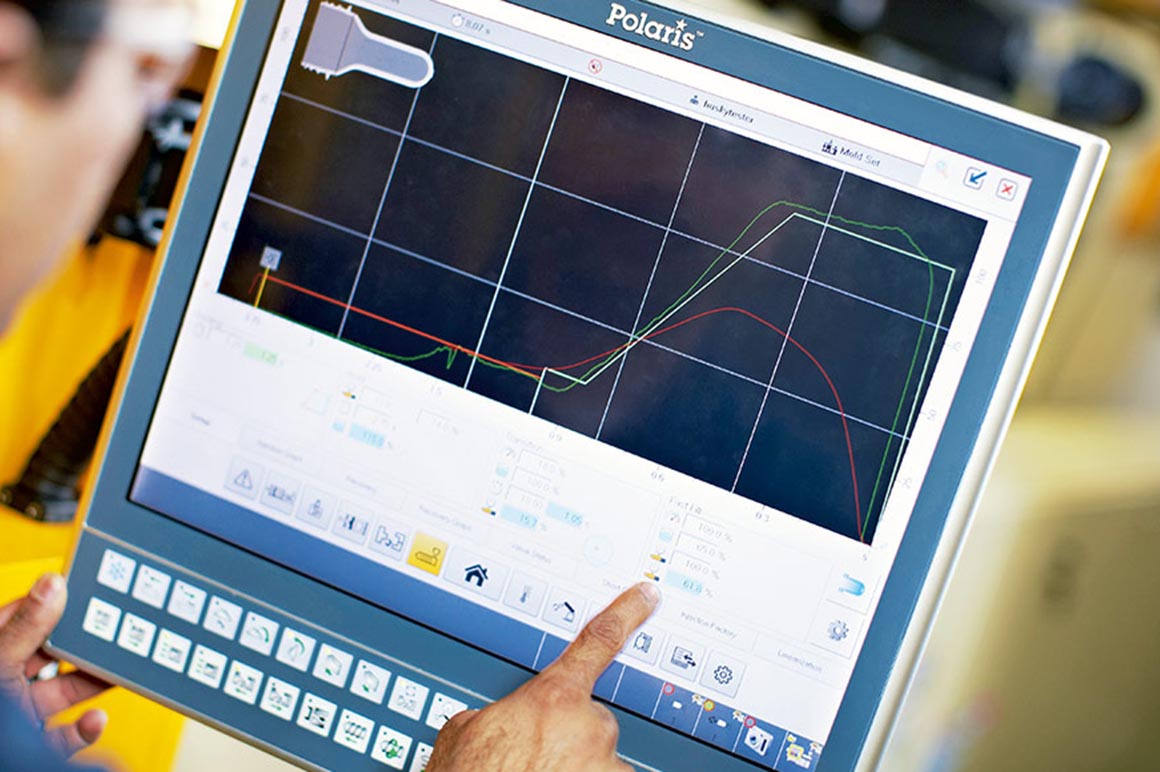
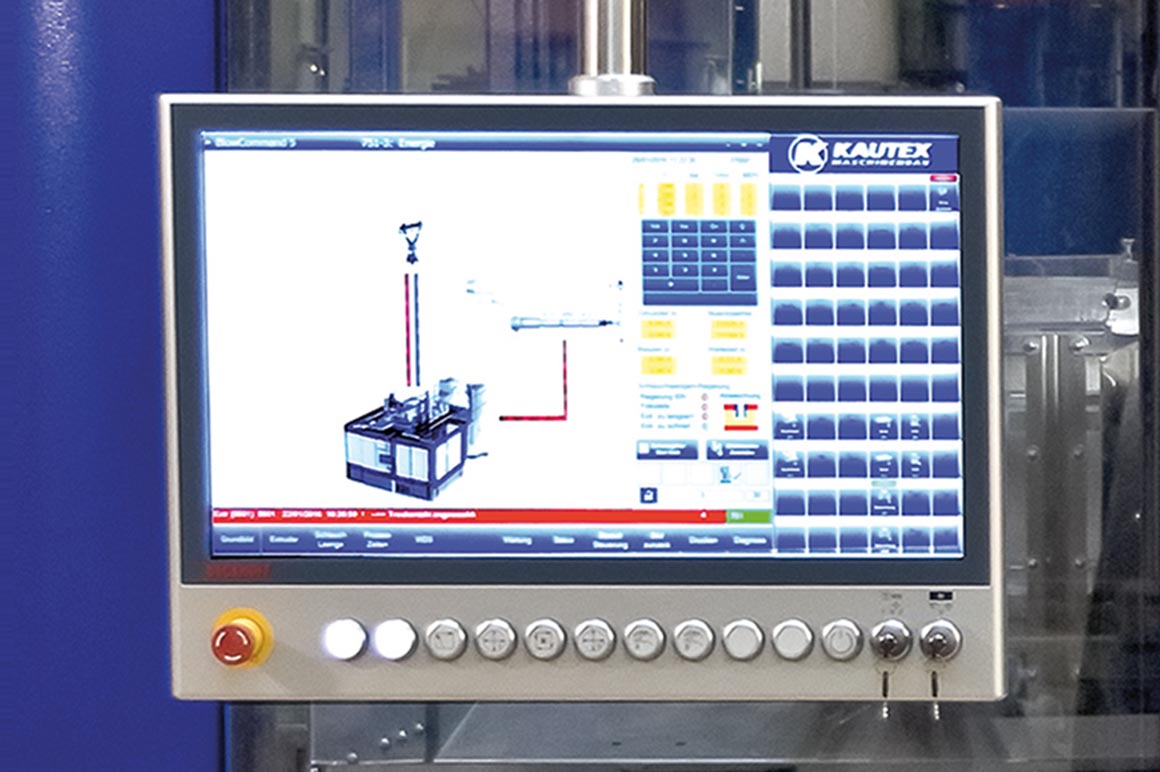
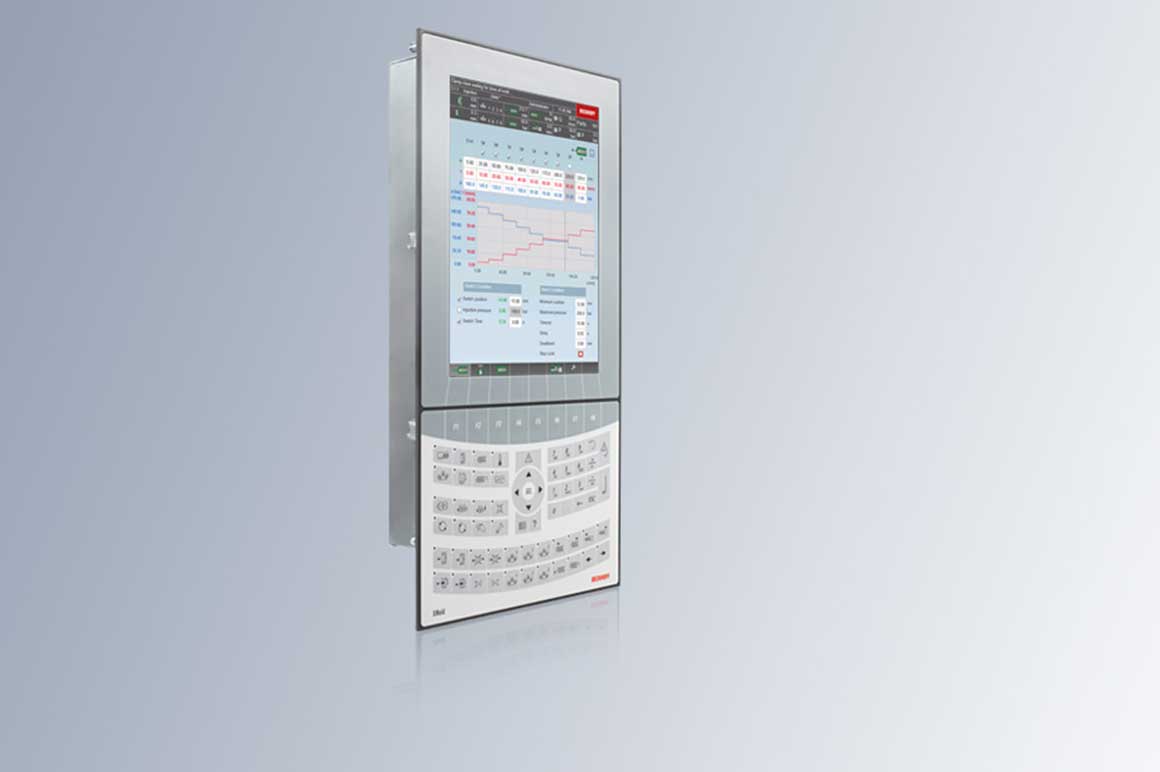
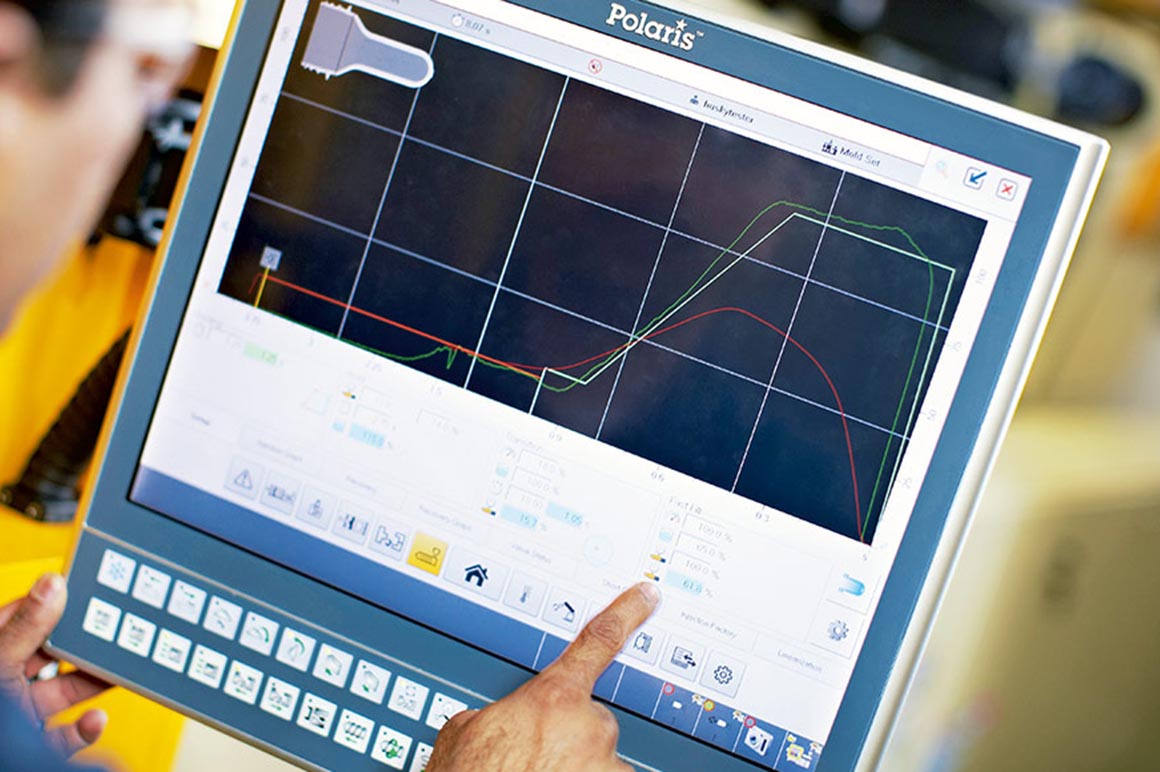
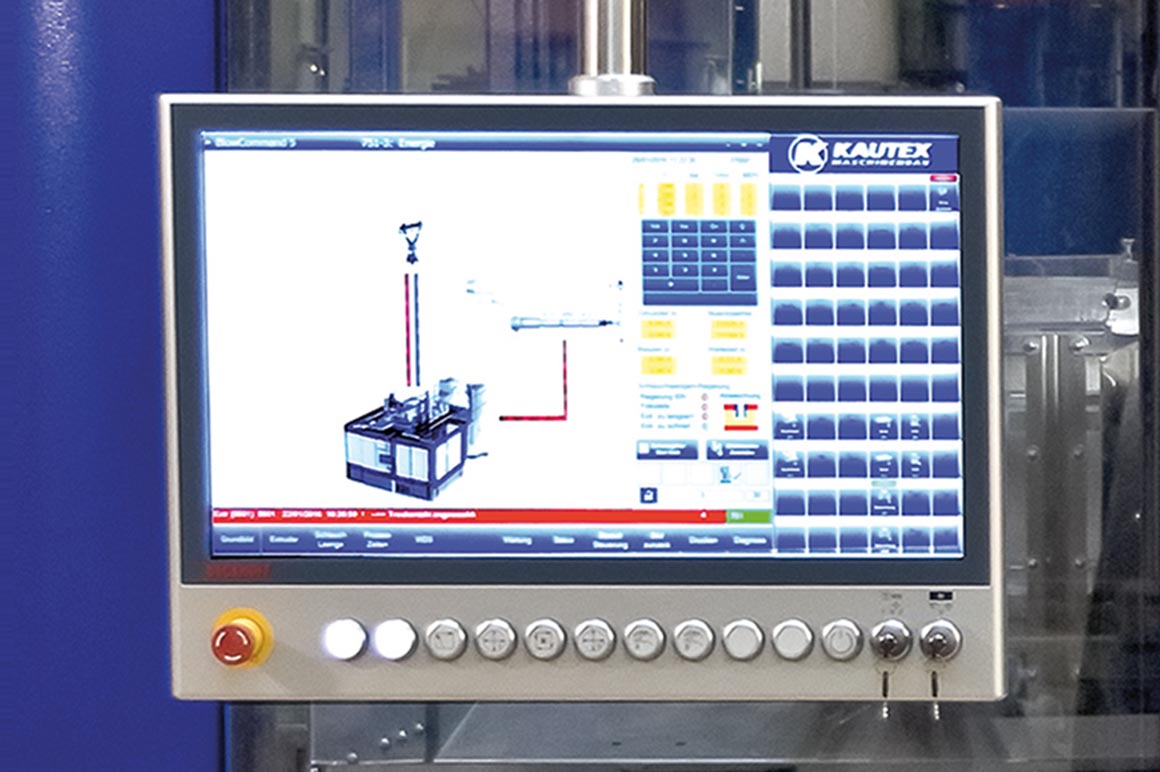
Industry and customer-specific Control Panels and Panel PCs as a unique selling point for your machine
The ergonomic operation and the unmistakable appearance of a machine play a significant role in its success on the market. In addition to design and color, the Control Panel is of great importance as the front end of a machine. More and more mechanical engineering customers therefore want an industry or customer-specific user interface as a unique selling point. Based on an extensive portfolio of standard Control Panels and Panel PCs, Beckhoff offers a wide range of solutions with regard to technical form and design. A panel design that matches the appearance of the machine in color and dimensions underlines its innovative character. There are no limits to the implementation of the customer's wishes: from the customer-specific company logo inserted in the factory and the color scheme matching the machine design, to the completely individually designed panel on the basis of an individual device construction.
In order to meet the needs of the plastics industry for ergonomic operation, Beckhoff offers Control Panels and Panel PCs that are optimally suited to the various processes. The needs-based design of the standard panels through the integration of manually operated push buttons and switches makes machine operation more comfortable. Based on in-depth knowledge of the individual process steps in plastics processing, Beckhoff offers an industry-specific panel based on standard hardware without a great deal of development work and expenditure.
With the XMold Panel PC, Beckhoff has developed a turnkey system solution that covers the wide range of injection molding applications, from standard to special requirements. It includes a CP6212-1001 Panel PC with a 12-inch display in portrait mode, the Beckhoff I/O modules, the technology software for injection molding machines and (optional) drive components. The XMold Panel features a key arrangement that is optimized for injection molding process and is designed to suit most applications. The technology software includes standard functionalities, such as extensive core puller functions, so that there is no great programming effort on the part of the customer.
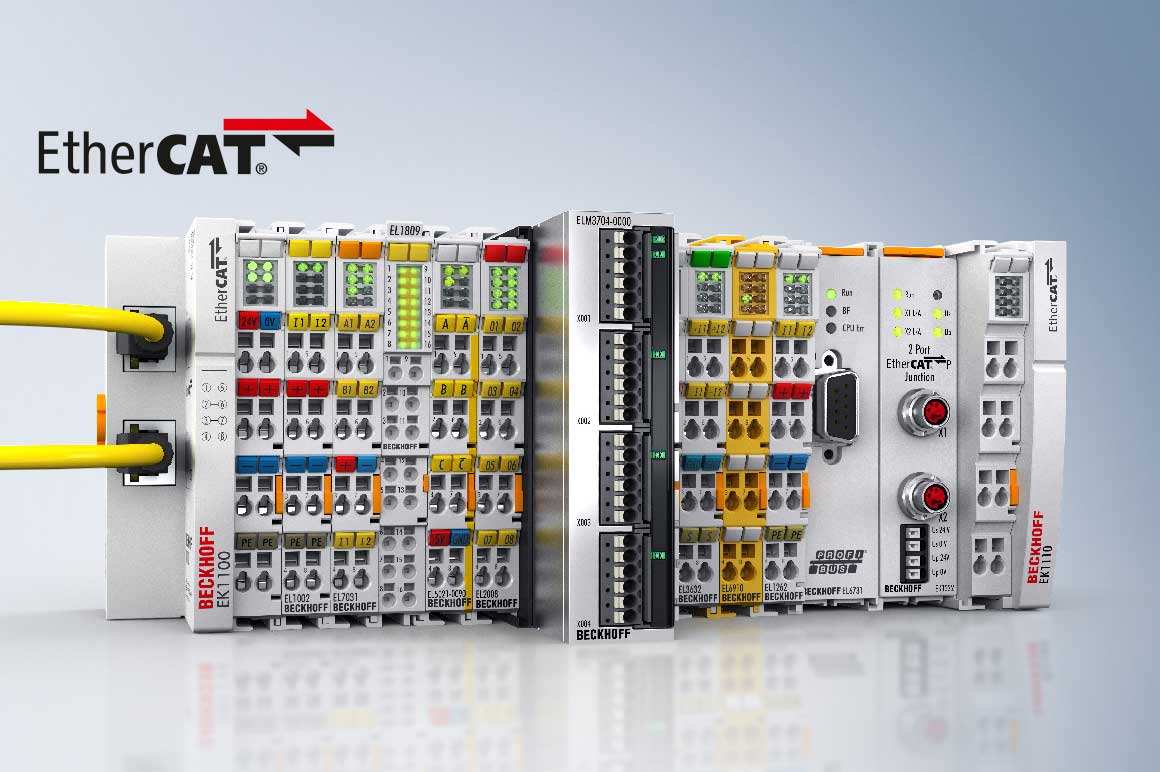
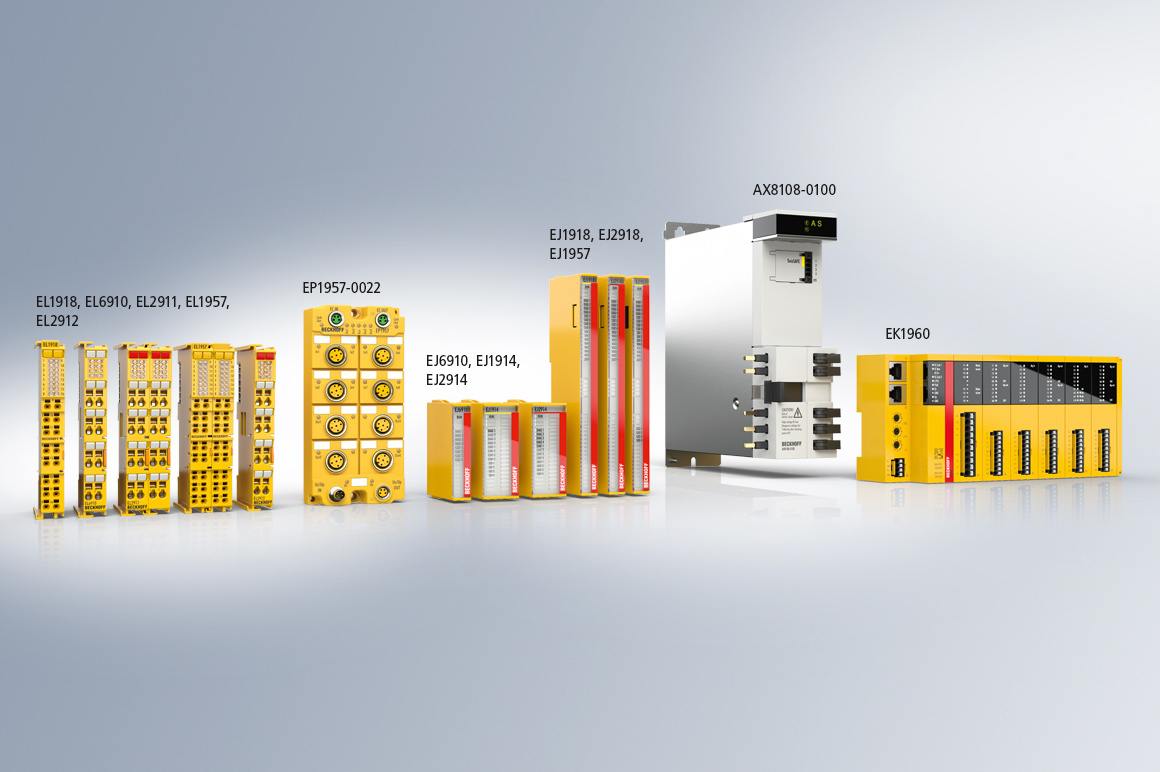
EtherCAT I/O modules integrate temperature control, energy measurement and safety technology into the control platform
In 1995, Beckhoff launched the Bus Terminal, which has since become one of the most important technology standards in automation technology. This was followed in 2003 by the development of the EtherCAT fast communication system. Launched by Beckhoff as an open system, it became a global standard in automation within a few years. An extensive EtherCAT I/O Terminal portfolio is available to users that is extremely well suited for automating every functionality in plastics machines and their peripherals in terms of both its performance and variance.
- EL3318 for temperature measurement
The EL3318 EtherCAT Terminal is ideal for temperature measurement via thermocouples. The 8-channel input terminal with integrated cold junction compensation is very compact in its design and measures temperatures with high accuracy and high signal-to-noise ratio. - EL3403 and EL3446 for power measurement
The EL3403 three-phase power measurement terminal can be used to measure and optimize the power consumption of a plastics machine. In conjunction with the TwinCAT Plastic Processing Framework, the EL3403 is used for the cost-effective Condition Monitoring of the heating tapes through sequentially alternating testing in operation. In traditional control structures, the power measurement terminal can also be used for current measurement. The EL3446 is available for simple monitoring of the heating tape function. In combination with the voltage measurement in just one power measurement terminal, the power consumption of individual machine components can be recorded cost-effectively by means of current measurement. The Beckhoff SCT current transformers (SCT2xxx, SCT1xxxx) enable assembly of the appropriate combination of sensor and power measuring terminal without requiring detailed knowledge. - EL3255 for position detection
The EL3255 EtherCAT Terminal allows potentiometric position detection. Due to its integrated power supply, the terminal delivers precise results (voltage values) even in environments with high interference fields. The EL3255 is particularly suitable for injection molding and blow molding machines with hydraulic drive technology. - EL6224 IO-Link terminal
IO-Link is an inexpensive fieldbus for the reading of sensors with low real-time requirements. A preferred application, for example in extrusion, is the reading of melt pressure and melt temperature via the EL6224. - Thermocouple Fieldbus modules FM33xx
The fieldbus modules with EtherCAT fieldbus connection allow the safe and accurate reading of thermocouples on injection molds, for example in injection mold making. The fieldbus modules have back-voltage protection circuitry to protect against external voltages applied to the thermocouple inputs. The cabling costs are reduced by eliminating compensation cables. - TwinSAFE terminals for integrating safety technology into the controller
Due to its scalability, the Beckhoff safety solution is suitable for expansive, complex systems with distributed I/Os as well as for small injection molding and blow molding machines. One safety logic is sufficient here to realize the complete safety technology. The compact EK1960 safety controller is particularly suitable for injection molding machines with hydraulic and/or electric drives. It allows the direct control of digital switching valves with a load of 2 A, such as those used in core pullers.
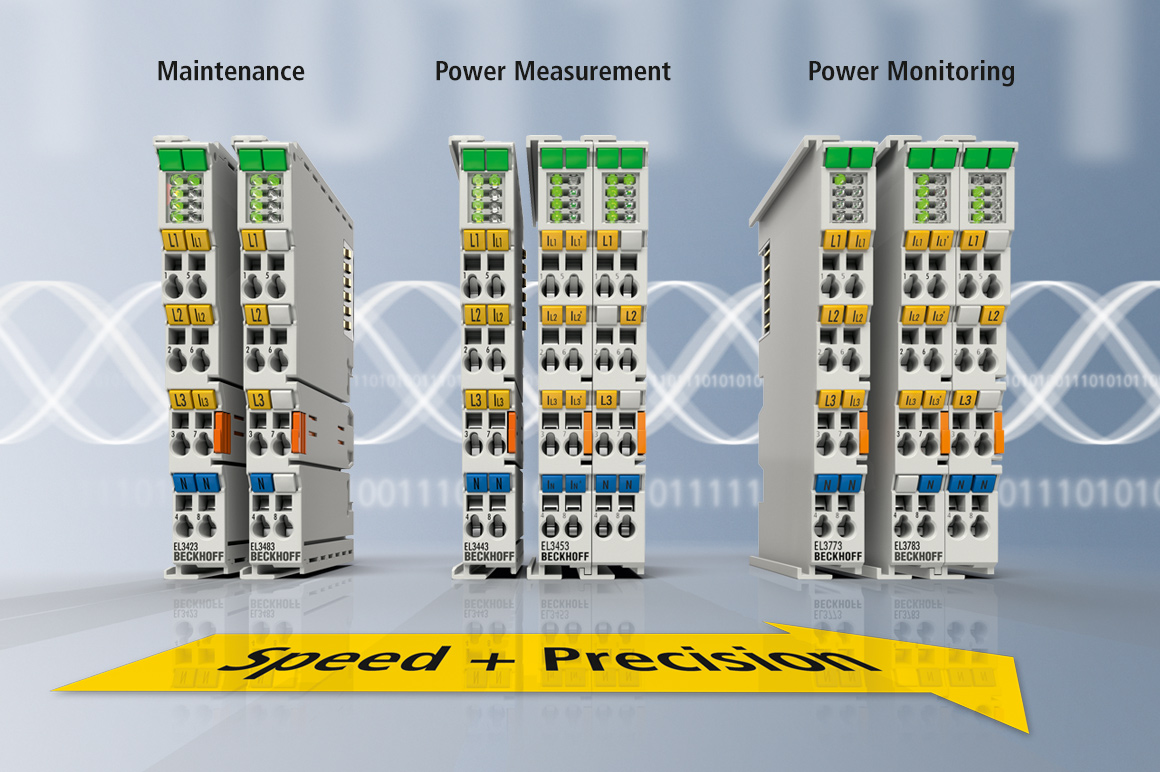
Efficient energy management
The energy consumption in plastics processing varies depending on the process, but it is generally very high and represents a considerable cost factor. Energy efficiency is therefore an essential building block for sustainable production. Beckhoff provides suitable technology for the continuous monitoring of energy consumption as well as for the detailed consumption analysis of new developments.
Beckhoff offers performance and cost-optimized software and hardware components for this purpose:
- The TF3650 TwinCAT 3 Power Monitoring software library is a PLC library for the evaluation of raw current and voltage data provided by the EtherCAT Terminals. Appropriate function blocks are available for calculating RMS values for current, voltage and power.
The following EtherCAT Terminals are particularly suitable for the plastics industry:
- The EL3443 and EL3453 EtherCAT Terminals enable the direct measurement of all relevant electrical data of the mains supply in the EtherCAT I/O system. The integrated monitoring of the energy efficiency of a plant is thus simple to implement.
- The EL3773 and EL3783 power monitoring terminals are designed for the detailed acquisition of the condition of a 3-phase AC or DC grid.
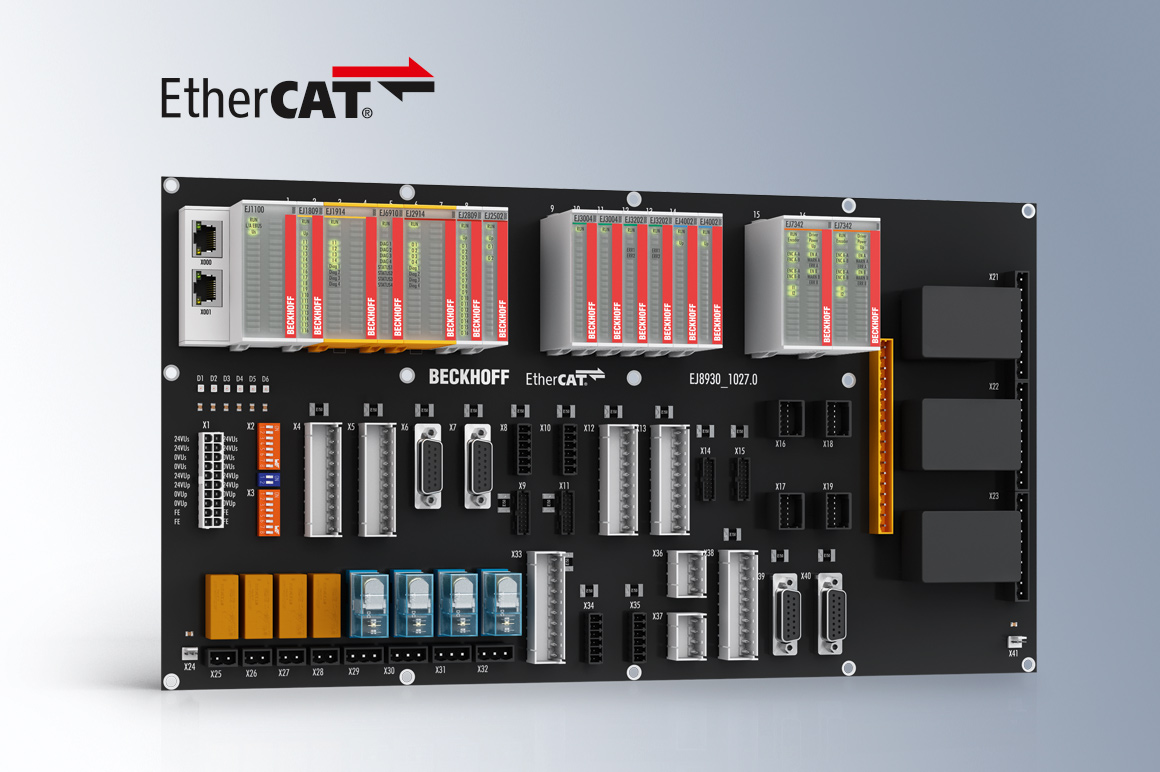
EtherCAT plug-in modules: the perfect I/O solution for series production
The EtherCAT I/O plug-in modules are based electronically on the well-known EtherCAT Terminals, and they provide the same broad variety of signals, including functional safety (TwinSAFE). Their electromechanical design enables them to be plugged directly into an application-specific signal distribution board. This routing board distributes the signals and power supply to machine modules via pre-assembled cables with application-specific plug connectors. One of the main advantages of using the signal distribution board is that all steps take place with a high degree of automation, from the manufacture of the circuit board and its population through to the inspection. All connection boards can be placed on the circuit board according to the customer’s specification. The connection level, which is matched to the application, considerably optimizes the wiring work, for example with pre-assembled cables and coded plug connectors.
The manufacturing process is accelerated as far as possible and the risk of wiring errors is reduced. This saves working time and thus costs. It allows production at different worldwide locations with a minimum of risk, since errors are avoided by concept through automation and coding. The plug-in modules are particularly suitable for injection molding machines because the I/O level in the core is always identically structured; an optional extension by IP20 terminals is also easily feasible. The integration of safety technology and additional relays minimizes the mounting space requirement, which is particularly interesting for small and medium-size machines.
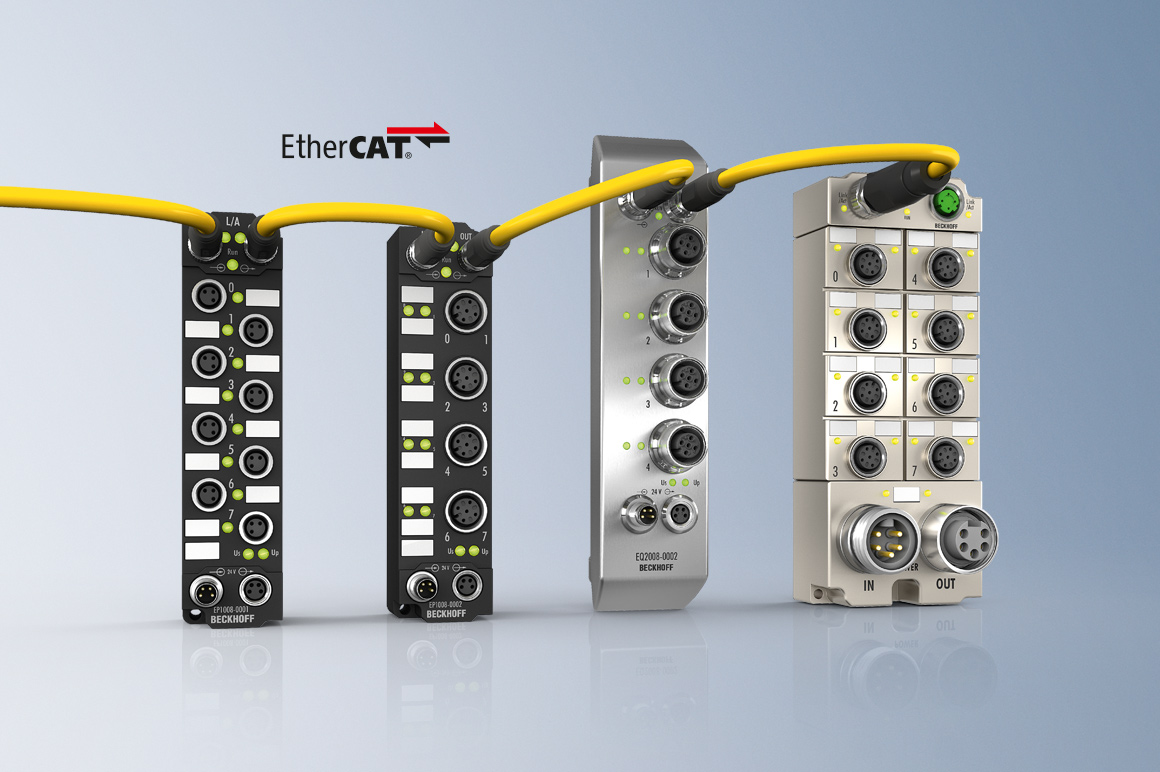
Universal EtherCAT for the IP67 world
With the EtherCAT Box, EtherCAT technology is used without a control cabinet. The modules from the IP67 series have an integrated direct EtherCAT interface, so that the high performance is retained right down to each module. In the IP67 world, this enables fast process data communication with XFC, high-precision measurement technology and integrated drive technology functions directly in the field. The robust design of the EtherCAT Box modules enables them to be used directly at the machine. Control cabinets and terminal boxes are now no longer required. In addition to the sturdy M12 screw connectors, D-Sub connectors, which are perfectly suited for handling applications, are also available for cost-sensitive applications.
- With the EP3744 EtherCAT Box, pneumatic pressure monitoring for the gripper elements can be implemented in handling applications; at the same time, six digital inputs can be read in.
- In the EP1816, the acquisition of 16 digital inputs is combined with the measurement of acceleration forces in three axes.
- The EP3752 enables the measurement of acceleration forces without additional inputs. The measured values of the accelerometers can be used for the acquisition of the mass forces, e.g., on machine bodies or for innovative control concepts with jerk compensation on handling devices.
- The EP3314 EtherCAT Box is suitable for the acquisition of process temperatures directly at the point where they arise. It increases measuring accuracy and saves having to use compensating cables for the thermocouples.
- The FM3312 or FM3332 Fieldbus Modules in a sturdy metal housing are particularly suitable for temperature measurement on injection molds or nozzles in extrusion lines. Up to 32 temperature channels can be contained in one industrial connector. Operational reliability is additionally ensured by reverse polarity protection against phase voltage.
- With the EP3356, the high-precision evaluation of load cells is possible, which is required in extruder applications for dosing and melt throughput measurement.
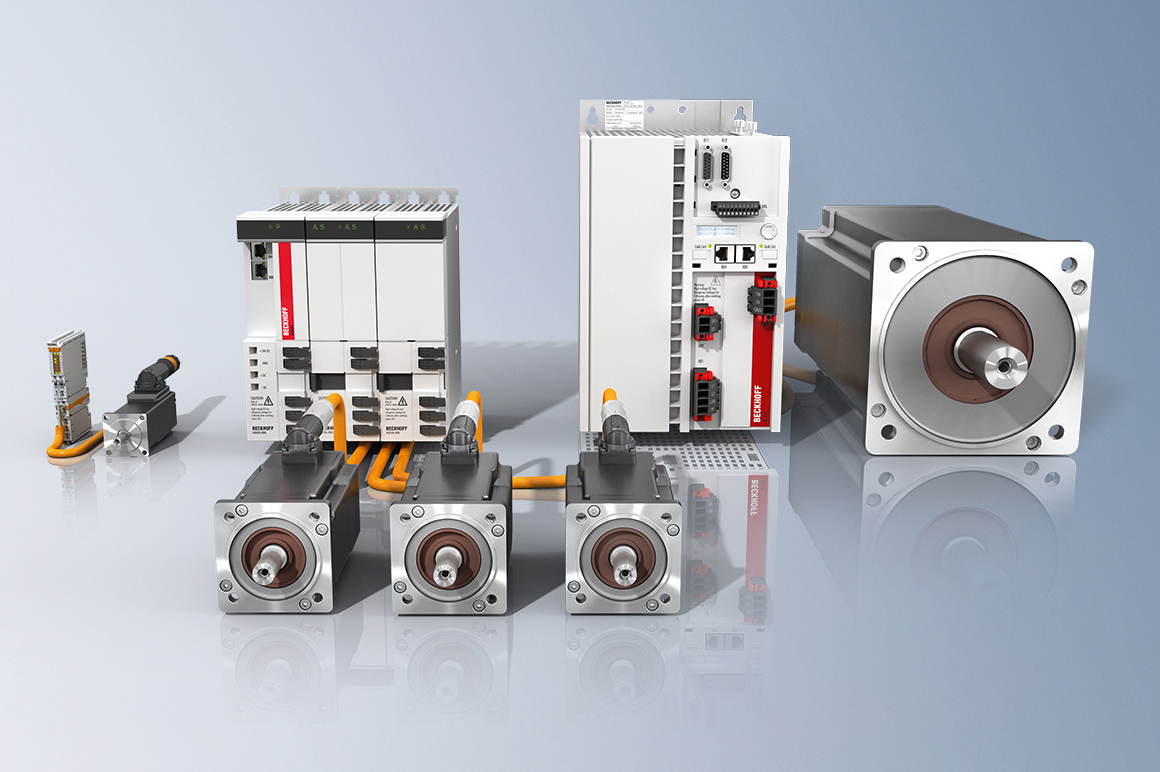
Drive systems for highly dynamic positioning tasks
In combination with the motion control solutions in the TwinCAT automation software, Beckhoff drive technology represents a complete drive system for all applications in plastics technology. With EtherCAT as a fast communication system, it is suitable for single and multi-axis positioning tasks with highly dynamic requirements. Due to its scalability, the Beckhoff drive technology enables machine manufacturers to design their drive solution to suit the required performance.
The AX5000 and AX8000 servo drive series offer maximum performance and dynamics with powerful EtherCAT system communication. The integrated, fast control technology of the AX series supports the execution of high-precision positioning tasks, such as those required in the field of film production: The smoothing rollers, which smooth the extruded film before winding, must be adjustable in the submillimeter range. The AX5000 offers the optimal solution for ultra-fast removal processes. The flexible concept of the AX5000 with 1- and 2-channel units as well as the variable motor power ensure a cost-optimized design. The drives from the AX8000 series are predestined for compact, modular drive units and for Cartesian handling devices.
In the lower performance range, the EtherCAT servo terminals, which offer a complete servo drive in the standard terminal housing, represent a drive solution that is both compact and inexpensive for low part weights or for additional units with low power consumption.
Beckhoff drive technology is characterized by its enormous in-house production depth: the servo drives and motors come virtually from a single source. The drives are produced at the production site in Verl, while the motors are developed and produced at a company belonging to the Beckhoff group. Thus, all drive technology components follow a consistent engineering concept. The extensive range of linear and rotary motors is optimally tailored to the Beckhoff servo drives. One result of this successful development collaboration is, for example, the One Cable Technology of the AM8000 motor series, which combines power and feedback systems in one standard cable. This reduces the mounting space on the machine and lowers the commissioning costs. Another technical innovation as a result of this close cooperation is the AMP8000 distributed servo drive system. It integrates the servo drive into the servomotor in a compact design.
The Beckhoff drive components are seamlessly integrated into the TwinCAT engineering tool. The motion control software packages TwinCAT NC-PTP, NC I and TwinCAT Rotobotics are perfectly matched to the servo drives and motors. Thanks to the integrated safety technology the servo drives meet the stringent safety requirements for plastics machines and simplify the configuration of production cells. For the new development of machines, Beckhoff has integrated tools into TwinCAT for the design of motors and gear units. For complex applications or the design of new systems, Beckhoff also offers support in the design of motors and gear units. The customer thus benefits from the many years of expertise of the Beckhoff engineers in various drive applications.
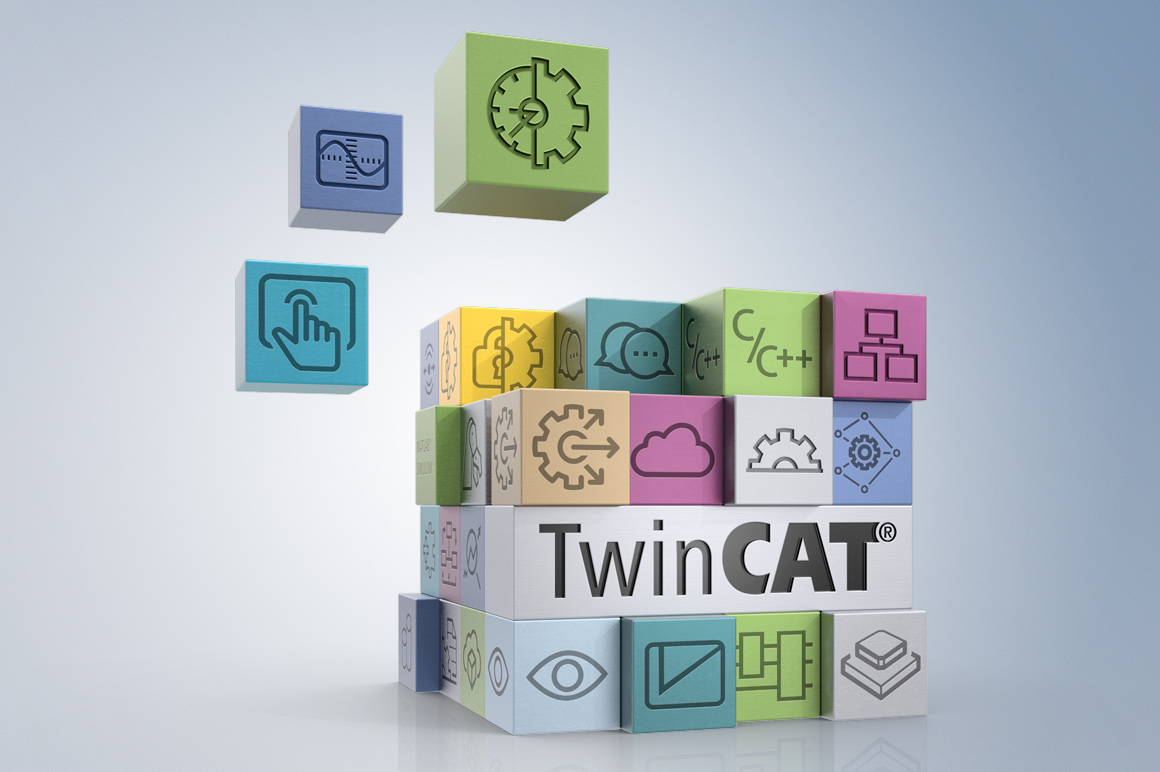
TwinCAT: the integrated engineering and control platform
TwinCAT integrates all engineering and runtime processes on a central software platform. This applies to programming, configuration, real-time environment and all runtime modules. By programming in the common IEC PLC dialects and integrating C/C++ algorithms, machine manufacturers can freely choose the most suitable programming method depending on the qualifications of the programmers, the service strategy and the need to protect expertise. With the integration of MATLAB® and Simulink®, controller concepts are developed based on models, thus contributing to virtual machine design. By using Microsoft Visual Studio as integrated programmer workbench, different version control systems are supported and teamwork is simplified. For series production, TwinCAT offers open interfaces for the integration of commercial IT systems for machine program generation.
- Extensive TwinCAT libraries for motion control save development time thanks to tested and optimized algorithms. The TwinCAT PTP and TwinCAT NC I supplements are ideally suited for handling applications with Cartesian robots. Ready-to-run solutions are available with TwinCAT Kinematic Transformation for other robot kinematics, such as SCARA, Delta and articulated arm.
- Commissioning and service processes are accelerated and improved with TwinCAT Scope, a software oscilloscope fully integrated into the TwinCAT system architecture, and thus contribute to increasing machine quality.
- TwinSAFE software-based safety technology simplifies the wiring of complex systems; variants can be mapped in software. This allows, for example, the modular development and commissioning of production cells. Documentation is also simplified and adaptations to additional customer requirements can be implemented quickly.
- The integrated, browser-based TwinCAT HMI visualization solution enables convenient development and maintenance of visualization objects. The information is presented either on the machines and systems or via the internet using a web browser.
- TwinCAT IoT provides the prerequisite for data aggregation in the cloud or locally in the production plant. TwinCAT also includes standardized communication protocols for cloud applications.
- The collected data can be specifically evaluated using TwinCAT Analytics.
- The TwinCAT interfaces to machine learning algorithms allow the use of AI methods in the traditional control environment.

TwinCAT Motion Control: perfectly suited for all drive tasks in plastics technology
Motion Control has been an important part of Beckhoff's software engineering tools for many years. With TwinCAT PTP and TwinCAT NC I, the requirements of electric drive technology in plastics machines and their peripherals are perfectly covered. A wide range of software modules for different tasks such as cam plates, synchronization and interpolating movements of several axes are available. NC PTP is perfectly suited for the widely used Cartesian removal systems; integration into the machine controller of the processing machine is easily feasible. The TwinCAT Plastic Application Components are available for stand-alone handling applications. As an industry-specific extension of the TwinCAT, they support the widely used Euromap interfaces between injection molding machine and robot, either as Euromap 67 or in the future as Euromap 79 (OPC 40079). Fast removal processes, such as in-mold labeling with the help of side removal handling, are optimized with PC- and EtherCAT-based control technology: EtherCAT as a fieldbus with virtually delay-free synchronization leads to extremely short cycle times.
Following the philosophy of open automation technology, TwinCAT Motion Control is a tool for the design of production cells that allows the integration of Beckhoff drive components as well as third-party components. TwinCAT NC-PTP is a suitable engineering tool for a variety of drive concepts: from simple switched axes and stepper motors or frequency converters to servo drives. Different encoder technologies with fieldbus interfaces or direct connection via I/Os are supported. This makes it possible to design production cells modularly, flexibly and at an optimal cost according to market requirements.
In particular, the linking possibilities of master and slave axes in almost any structure as well as the powerful and diverse motion functions of TwinCAT cover wide-ranging applications in outstanding fashion. With the Flying Saw software library, for example, trimming units in extrusion lines can be perfectly synchronized. Powerful tools such as the TwinCAT CAM Design Tool and the TwinCAT Scope support machine design and commissioning. PLC libraries with function blocks according to the PLCopen Motion Control standard facilitate programming and save engineering effort through the reusability of the modules.