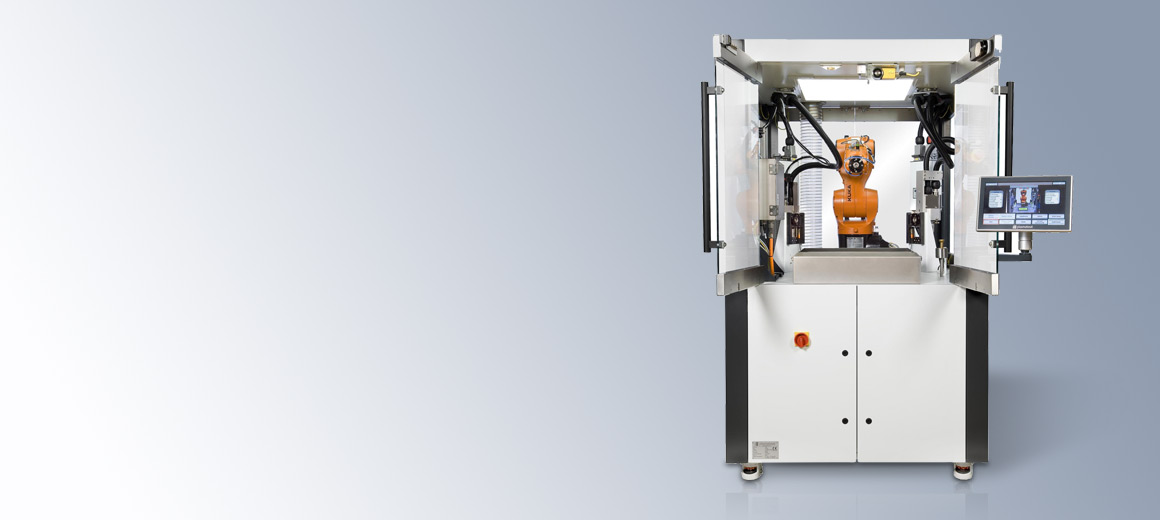
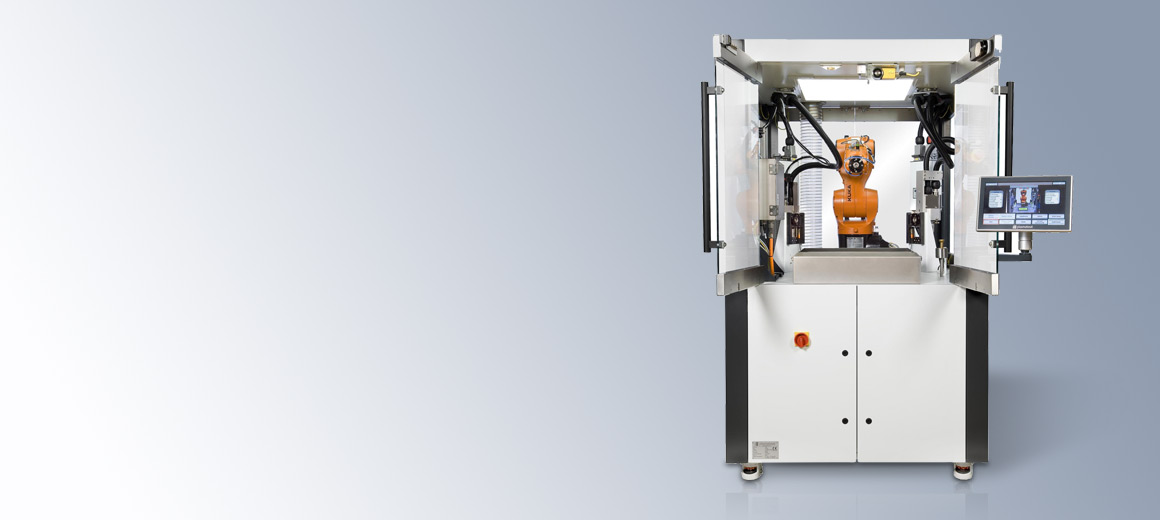
As the efficiency of plastics machines increases, the integration of production cells and the independent communication between individual machines and plant components are becoming increasingly important. In order to ensure a secure and reliable data exchange between heterogeneous production installations, the components must communicate via an interoperability standard based on OPC UA, in accordance with the Euromap Companion Specifications. In TwinCAT, Beckhoff integrates a powerful OPC UA engineering tool for the implementation of Euromap-compatible interfaces of all types.
Automation devices and sensors from different manufacturers are linked in production cells. The particular strength of Beckhoff's open automation technology is shown in this environment. Different fieldbus systems can be integrated into a hardware and software family with the help of the large interface portfolio and the elegant integration into TwinCAT. The efficient design of production cells follows a basic concept with which a large variance can be realized. This requires flexible, easily adaptable technology for safety devices. Beckhoff's modular safety hardware and software offers distributed I/O components close to the safety devices as well as application-specific software adaptation within the framework of the safety regulations.
PC-based control is ideal for use in production cells
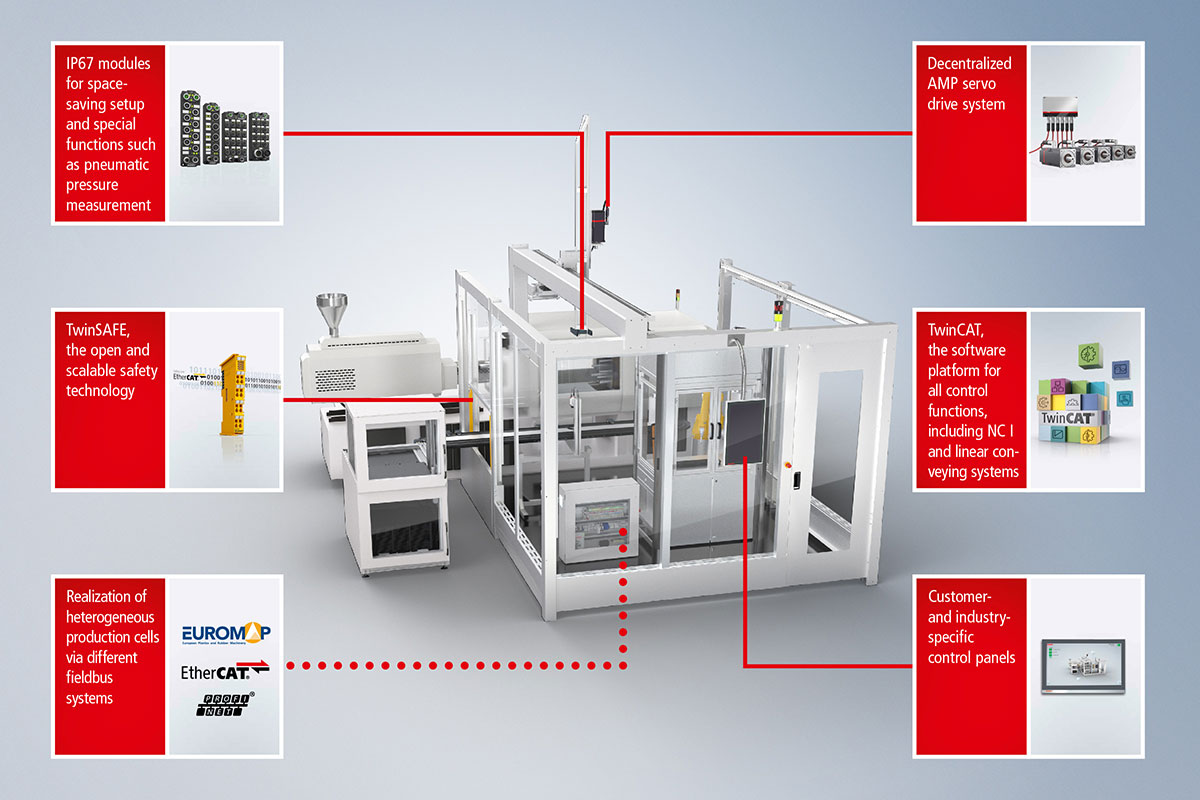
Injection molding machines and production cells with universal engineering platform
In the manufacture of injection-molded parts, plastics processors are increasingly relying on production cells to produce complex parts with high output in perfect quality and with minimal personnel costs. In cleanroom applications, production cells are often mandatory for meeting hygiene standards. Thanks to their modular design, the engineering effort and the variety of parts of production cells are reduced. The extensive Beckhoff portfolio includes a wide range of software and hardware solutions to meet the typical requirements of production cells:
- Special devices can be omitted due to the consistent implementation of all functionalities as software modules. This reduces hardware costs, engineering effort and lifecycle costs.
- Display devices with different screen sizes and orientations offer ergonomic operation in an appealing design.
- EtherCAT as a fast fieldbus forms the backbone for production cells with Beckhoff technology. Subsystems can easily be integrated by interfaces to all common fieldbuses.
- The EtherCAT Box modules in IP67 or the AMP8000 distributed servo drive system reduce the mounting space required in control cabinets and support the modular design of production cells.
- The Beckhoff safety architecture supports the design of a modular safety concept from a single source with additional customization.
- The design of a wide range of heterogeneous production cells is enabled through support for the vendor-neutral Euromap standards based on OPC UA, EtherCAT as a fast fieldbus and TwinCAT as a universal engineering platform.
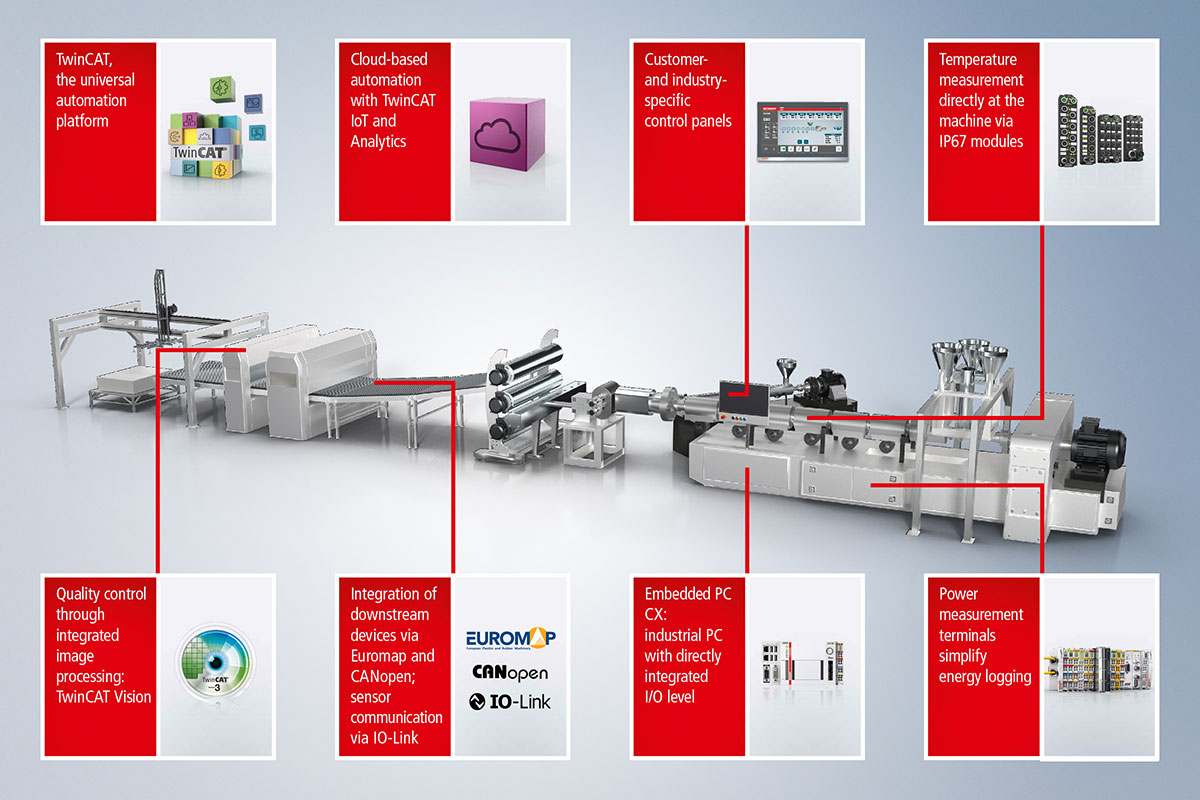
PC-based control for extruders with integrated downstream automation
The Beckhoff control portfolio provides the basis for innovative automation concepts in extrusion. In addition to the control technology for extruders, there are numerous fields of application for the downstream devices for tube and profile extruders as well as for film extrusion. As a specialist for various fieldbus variants based on EtherCAT, Beckhoff provides extensive options for the integration of subsystems.
- EtherCAT as a communication base allows the secure and high-performance networking of a complete extrusion line with the help of different fieldbuses or via the serial interfaces that are still used.
- EtherCAT-based fieldbus interfaces allow the integration of measuring systems or trimming devices with third-party controllers.
- Euromap-compatible Ethernet interfaces support sustainable solutions for the integration of line components.
- PC-based control supports cloud communication, including for the retrofitting of existing machines, enabling the aggregation of data in global production networks.
- TwinCAT provides special function blocks for automatic size adjustment for hose extrusion lines, for smoothing units in flat film extrusion and for roller winders for blown film plants.
- Through the perfect integration of image analysis algorithms into TwinCAT, the machine programmer can improve the monitoring of plant functions and the quality of the end products.
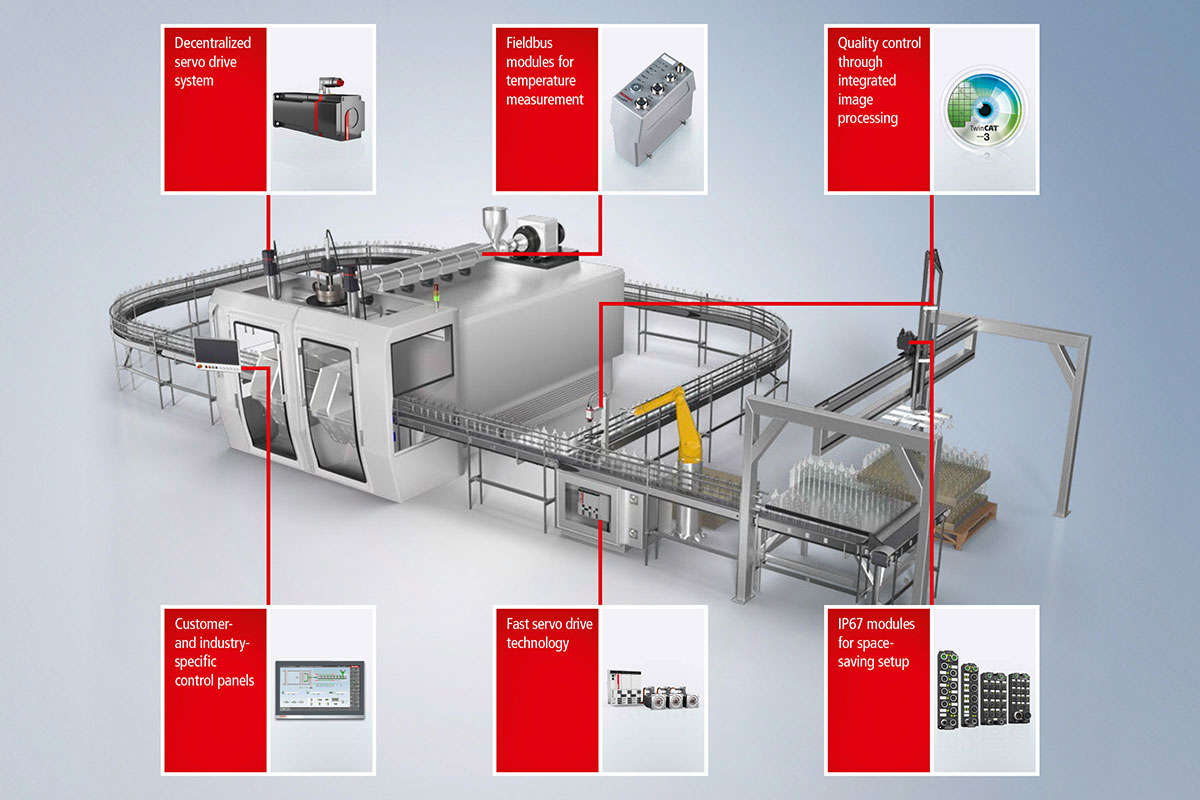
Production cells for complex plastic articles
In the manufacture of blow-molded articles, plastics processors are increasingly relying on production cells to produce complex articles with high output in perfect quality and with minimal personnel costs. The modular design of the production cell reduces the engineering effort and limits the variety of parts. The extensive Beckhoff component portfolio includes a wide range of solutions to meet the typical requirements of production cells:
- Display devices with different screen sizes and orientations offer ergonomic operation in an appealing design.
- EtherCAT as a fast fieldbus forms the backbone for production cells with Beckhoff technology. Subsystems, e.g., for labeling or marking, can easily be integrated by interfaces to all common fieldbuses.
- The EtherCAT Box modules in IP67 or the AMP8000 distributed servo drive system reduces the mounting space required in control cabinets and support the modular design of production cells.
- Special IP67 modules with integrated sensors for pressure measurement are available for leak testing.
- In addition to the classic servomotors with gear units, the highly flexible linear XTS and XPlanar linear drive systems are available for parts transport, stacking devices or film insertion (IML). They are suitable for the realization of innovative solutions, for example for product transport to the filling machine for linked plants.