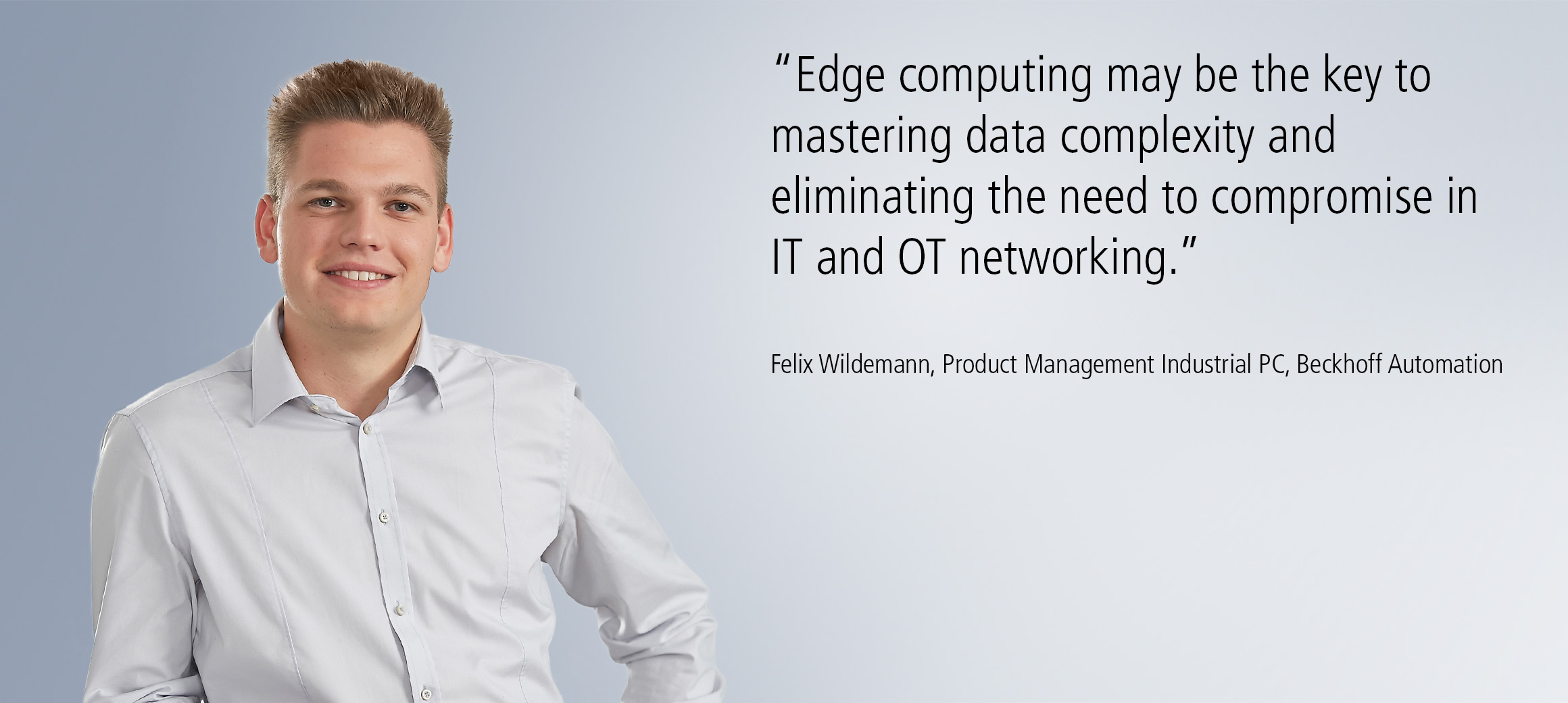
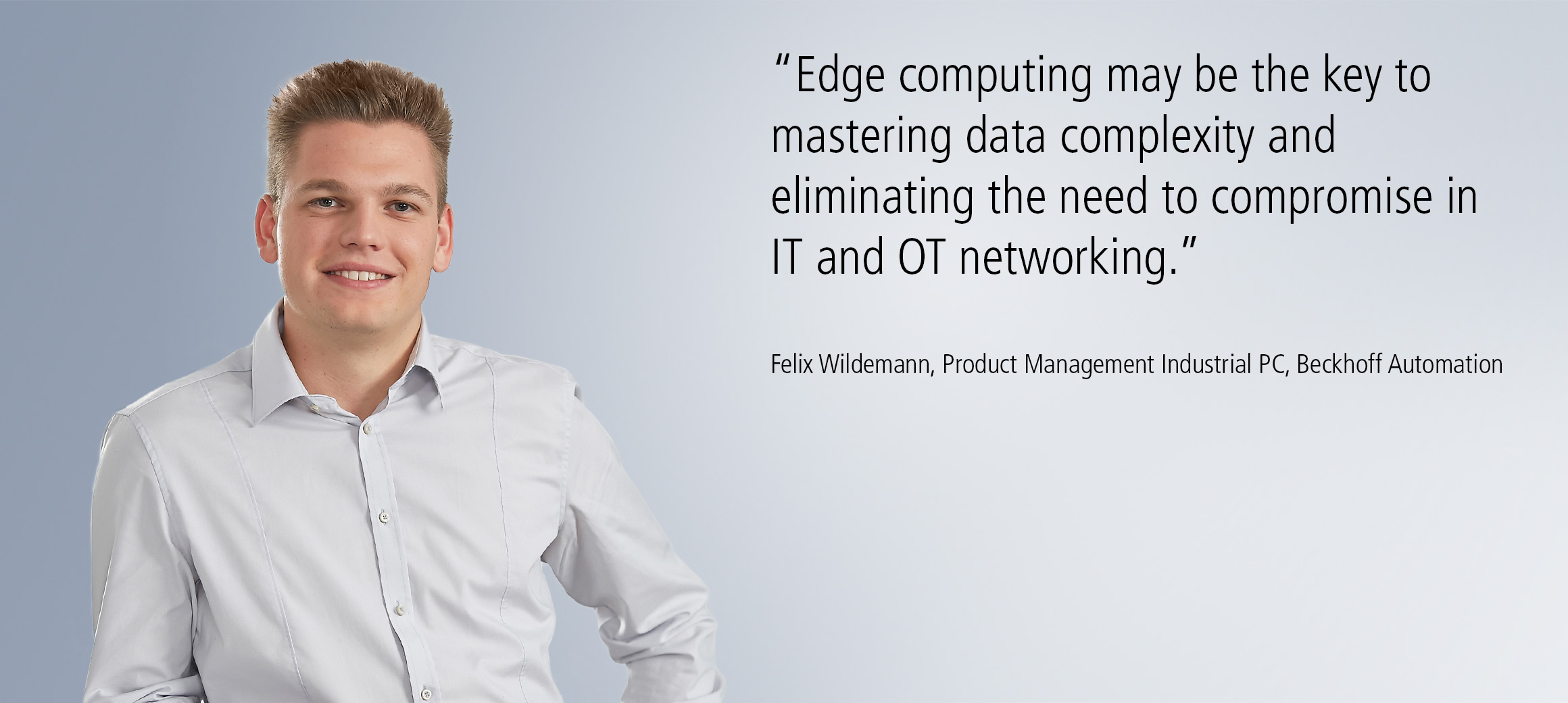
Statement by Felix Wildemann, Product Management Industrial PC, in Computer&Automation
Source: “Computer&Automation, 3 questions on...edge computing”
What role does software play in the successful networking of IT and OT? And how is it matched to the hardware that it works with? Felix Wildemann, Product Management Industrial PC, gives a glimpse into the world of edge computing.
The Industrial IoT landscape is generating more and more data, creating a complex collection that needs to be managed somehow. What role does edge computing play in this process?
Felix Wildemann: Classic automation takes a very cautious approach to opening up and networking with the outside world, because the safety and stability of the production plant could be called into question when it is networked with IT. The ability to directly network both worlds is often not without its compromises.
Edge computing may be the key to mastering data complexity and eliminating this need to compromise in IT and OT networking. This is thanks to the fact that it pre-selects, sorts, and processes data at the edge, allowing the process data that is truly relevant to filter through. Although all edge functions can also be executed directly on the Industrial PC that is responsible for control, there are also significant advantages in targeted decoupling and pre-processing of relevant process data at the edge. This is particularly true for brownfield scenarios, where an edge device is integrated into an existing plant concept. By retrofitting a dedicated edge device, IoT functions can be introduced into the existing application without the need for any subsequent changes to the controller’s software or hardware. But in many cases, it is also worth considering an additional, dedicated edge device for greenfield scenarios, where there is no pre-existing plant equipment.
Edge computing makes it possible to pre-select sensor data, process software applications, and even calculate AI formulas. What do users need to consider when it comes to edge software? Which technologies are must-haves?
Felix Wildemann: A modular software platform that effectively combines the IT and OT forms the basis for an integrated edge concept. The modular nature of this means we can liken it to an app concept – users can select and execute the functions they actually need from a wide range of options on the edge device. Not only that, but they don’t require any additional programming skills – they can simply access ready-to-use function blocks that are quick and easy to integrate.
What’s really important is that the edge device speaks the same “language” as the machine. It also has to provide secure, standardized IT protocols and mechanisms that enable the machine to be coupled indirectly and securely to the cloud or local servers via the edge device. This aspect also underlines how important international standards for interfaces and protocols are in this context, as they allow all the various plant components to fully combined in a way that creates a truly integrated edge solution.
With its TwinCAT control software, Beckhoff offers a wide variety of function blocks and protocols for this very purpose. This means that the TwinCAT ADS protocol or OPC UA at the edge can be used to acquire data on the machine side without the need for any changes in the control computer’s TwinCAT program code. In addition to standard IT protocols, the OT supports protocols of both commonly used cloud providers and private cloud scenarios.
Fully coupling the edge device and the controller is a fine art. It’s not just a question of collecting data from the controller and making it available – the edge software also has to be designed in a way that prevents it from impairing the availability and real-time capability of the controller. At the same time, the relevant process data has to be transmitted back to the controller to retroactively optimize plant production, achieve predictive maintenance, and minimize machine downtimes. Thanks to Beckhoff’s solutions, this works without any restrictions: TwinCAT uses one and the same software for the controller and all IoT tasks. And with its modular set-up, TwinCAT can be adapted to the application exactly as is needed.
Container technologies such as those from Docker are also suitable for accommodating all the desired functions on a single device. Docker systems not only channel and optimize the execution of edge software to save resources, but also help to integrate third-party apps and functions directly into the edge device. This means that customer-specific functions can also be mapped at the edge and operated in parallel to TwinCAT.
We are dealing with a growing number of tasks in this context, and this is also leading to more requirements for hardware to meet. What should users look for when choosing the right edge computing hardware?
Felix Wildemann: An edge solution only works if both the hardware and software are perfectly aligned with the IoT and controller approaches. This requires a scalable portfolio of extremely compact, modular, and versatile industrial PCs featuring different performance classes that can be perfectly adapted to the edge scenario in question – based on the required computing power and interfaces, and on the available installation space.
Beckhoff’s approach ensures that our Industrial PCs with TwinCAT software can be used as both control computers and edge devices, which means that the hardware offers the unbeatable advantages of a conventional Industrial PC, such as long-term availability, robustness, and longevity. At the same time, our approach is also capable of directly integrating industrial bus systems, enabling various sensor data from the field to be acquired directly at the edge in addition to the data made available in the controller. Two operating systems that support Beckhoff’s own TwinCAT control software, all IT protocols, and Docker functions are available in the form of Microsoft Windows and TwinCAT/BSD®.
This means that users can access Beckhoff’s entire Industrial PC portfolio without being restricted to specific hardware. Ultimately, our portfolio’s modular, scalable, and flexible features provide the perfect conditions for creating a perfectly integrated controller, IoT, and edge solution.