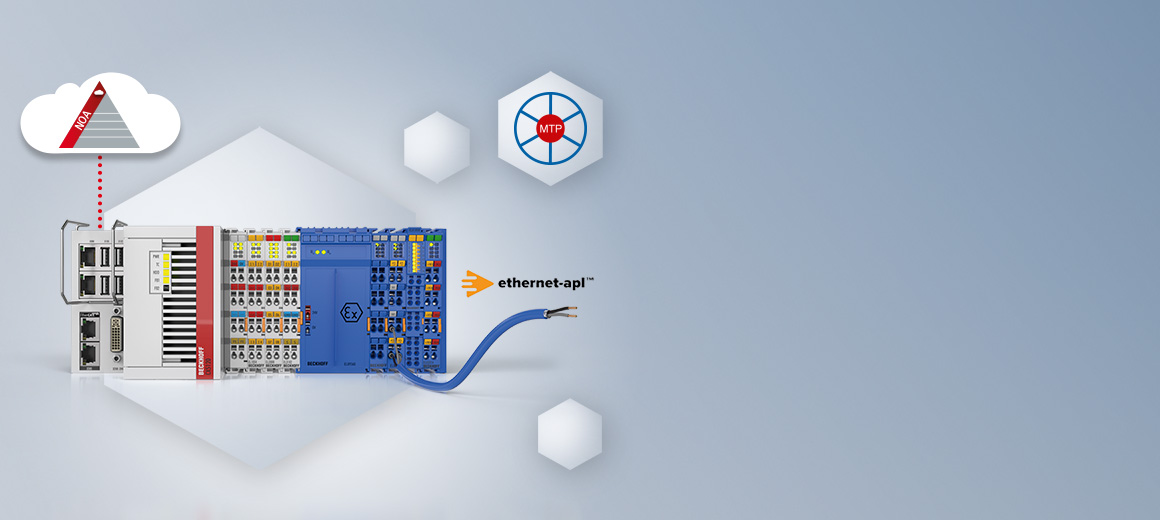
Future-proof
plant automation
Ethernet-APL, NAMUR Open Architecture, MTP
Biuras Kaune
Beckhoff Automation OÛ
Ethernet-APL, NAMUR Open Architecture, MTP
Future-proof digitalization concepts are becoming increasingly important in the process industry. The aim is to boost efficiency, output, and availability through predictive maintenance, data-based process optimizations, and targeted plant modularization. With automation technology from Beckhoff, you have the tools to seamlessly integrate digitalization into your process technology plant in a way that suits your needs, for both greenfield and brownfield projects.
What potential does digitalization offer for the process industry?
The Ethernet Advanced Physical Layer (Ethernet-APL) provides the process industry with a new communication standard that enables fast and consistent data transmission. The aim is to use an Ethernet base to implement the entire communication in process technology plants – from field level to higher-level control systems. This includes pure process data and, more specifically, status information from field devices for diagnostics and predictive maintenance. Beckhoff has developed the compact ELX6233 EtherCAT Terminal to integrate Ethernet APL-capable field devices on a modular basis.
The NAMUR Open Architecture (NOA) is a concept developed by NAMUR for implementing plant monitoring and optimization in the process industry. NOA makes previously unread data usable via an additional second channel without changing the existing automation structure. Brownfield systems can easily be retrofitted. To implement NOA, Beckhoff has developed an NOA edge device, which consists of an embedded PC, EtherCAT Terminals, and a TwinCAT software project.
The Module Type Package (MTP) is a manufacturer-independent standard for simplifying the modularization of process technology systems. The MTP contains all the necessary information and standardized interfaces to easily integrate individual process modules into the superordinate level process orchestration layer. Regardless of the control system manufacturer, modules developed once can be easily reused in other systems. With TwinCAT MTP, Beckhoff integrates the Module Type Package into the familiar TwinCAT Engineering environment.
A compact tabular overview of the technologies and concepts for digitalization in the process industry can be found in our onepager:
Process analytical technology (PAT) plays a crucial role in the chemical industry. Bayer AG, for example, is enhancing efficiency and transitioning from time-based to condition-based maintenance by embracing the cutting-edge NOA concept. This is implemented via the seamless integration of a compact edge device featuring a CX8110 Embedded PC, EL3182 EtherCAT HART Terminals, and TwinCAT OPC UA Server from Beckhoff, all without any alterations to the existing control technology.