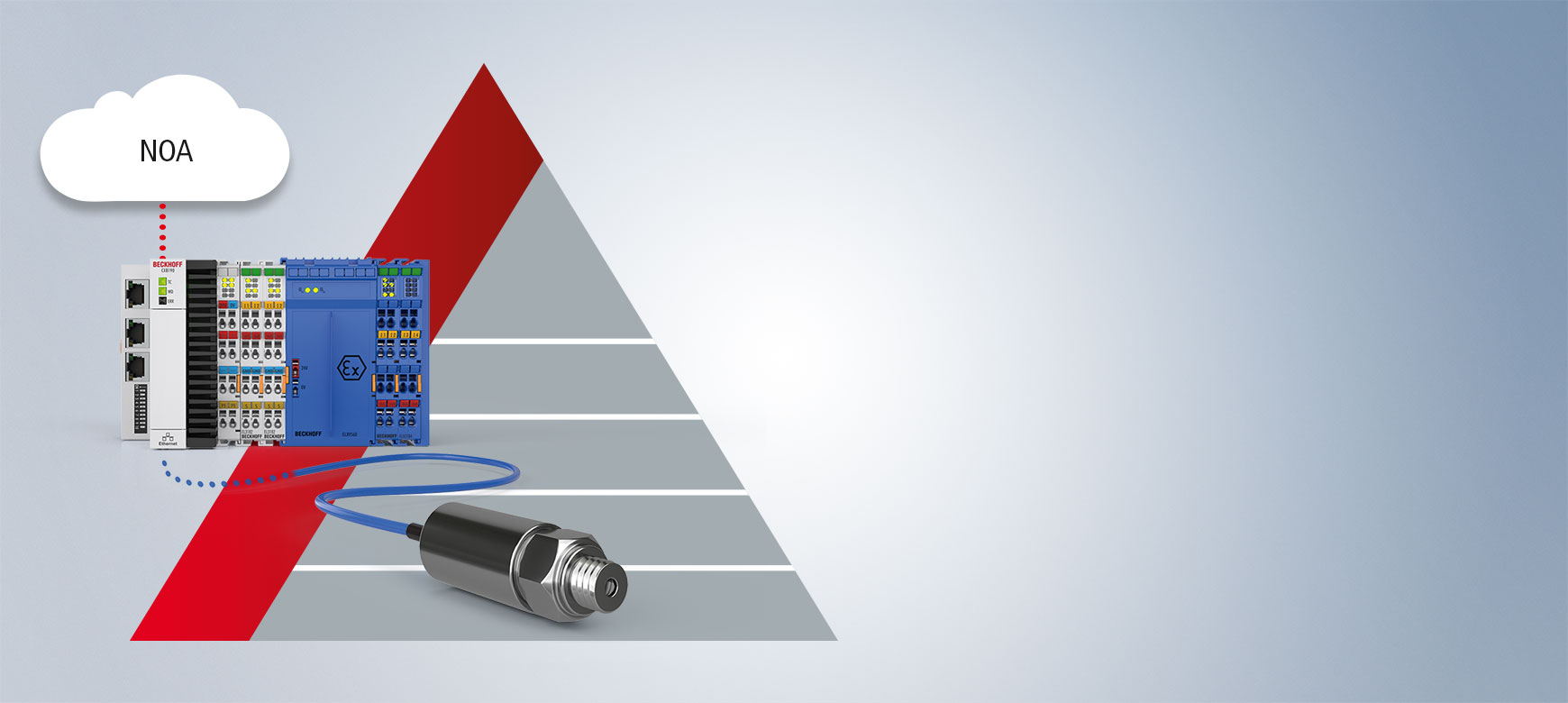
Plant monitoring and
optimization with NOA
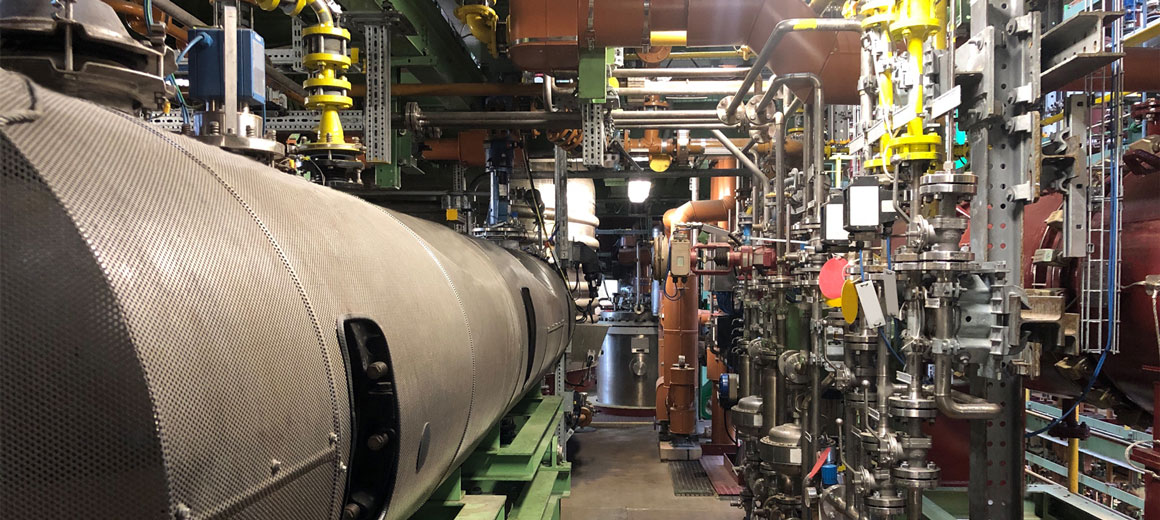
PC-based control for the implementation of
NAMUR Open Architecture (NOA)
Bayer, Deutschland
Headquarters Australia
Beckhoff Automation Pty. Ltd.
+61 3 9912 5430
info@beckhoff.com.au
www.beckhoff.com/en-au/
Bayer, Deutschland
Beckhoff has developed an NOA edge device specifically for reading out the additional operating data for the higher-level M+O. The edge device, which consists of a compact embedded PC, EtherCAT Terminals with HART functionality, and the relevant TwinCAT project, can be placed directly in the plant.
Functions of the NOA Edge Device from Beckhoff:
The NOA concept has a lot of potential, particularly for brownfield applications. Existing plants need to be future-proofed by converting or upgrading them: costs can be reduced and output increased by simply monitoring and optimizing plants without changing the current process control methods. Therefore, additional components are added so that the previously unused data from the field level can be collected.
The Beckhoff NOA edge device was developed for this application. Due to its compact design, it can be integrated into the established structures of the plant and saves on space. The edge device is joined to the 2-wire connection to the field device using a signal isolator, without influencing the process control.
If, in addition to data from established field devices, diagnostic data is also acquired by additional sensors, for example for vibration or temperature measurement, IP67-protected I/O modules installed directly in the field can prove incredibly useful. This version cuts down on cable routing work while also reducing the space required in the control cabinet.
The NOA concept also offers advantages for greenfield plants. For example, vital data can be transmitted directly from individual plant modules to the respective manufacturer, and the manufacturer can then provide appropriate spare parts or initiate maintenance work. This approach is particularly successful in conjunction with the Module Type Package (MTP).
Additional monitoring sensors can be installed in the plant planning stage, thus providing more data for monitoring and optimization. New technology such as Ethernet-APL makes implementation simpler, as process data and vital data can be transmitted simultaneously via the Ethernet connection. The processing and translation of the data can be implemented in the TwinCAT automation software, regardless of the protocol used.
We also offer ideal solutions for your edge device applications outside the process industry.
The ELX6233 EtherCAT Terminal enables full data collection for the processing industry with the Ethernet-APL communication standard.
TwinCAT MTP integrates the MTP concept into the engineering and enables the efficient development of modular plants.
The EtherCAT Terminals from the ELX series with intrinsically safe inputs/outputs enable the connection of field devices up to zone 0/20.
The EtherCAT Box modules from the EPX series with intrinsically safe inputs/outputs enable the connection of field devices up to zone 0/20.