Products
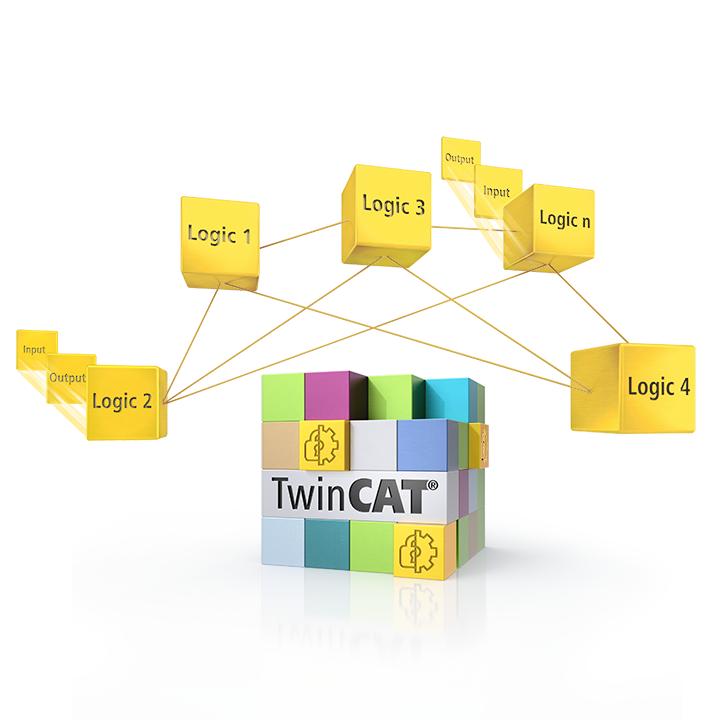
TwinSAFE project design
TwinSAFE gives machine builders the possibility to realize the most diverse safety architectures with components in different form factors according to individual requirements.
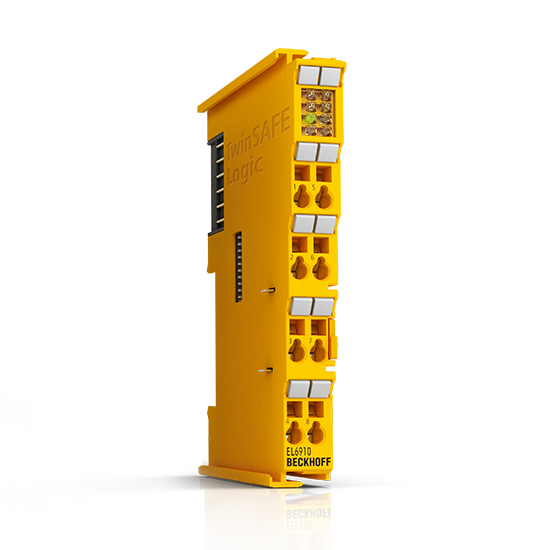
TwinSAFE hardware
A broad range of components equipped with TwinSAFE Logic means full freedom in terms of choosing an architecture for the safety application at hand.
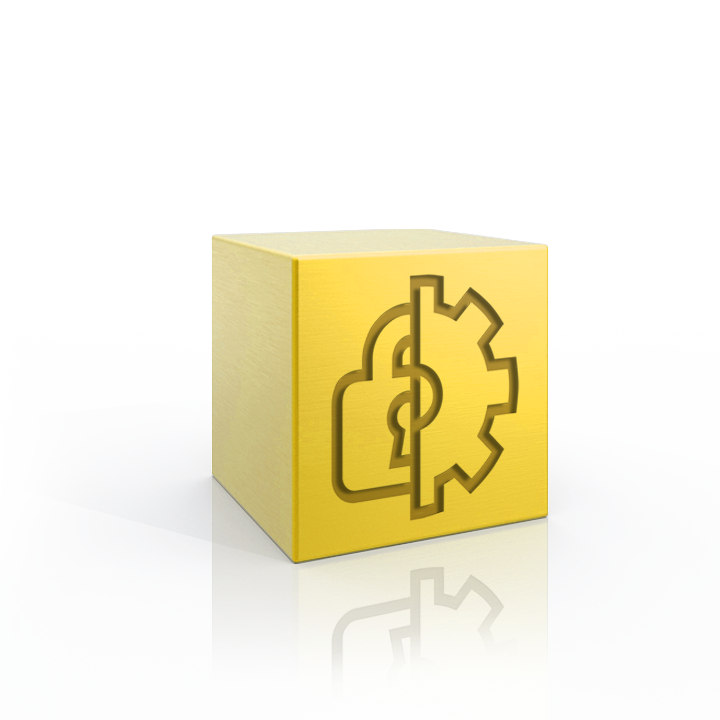
TwinSAFE software
TwinSAFE provides a range of essential software utilities to complement hardware components for safety-related applications.
TwinSAFE: the open and scalable safety technology

The TwinSAFE integrated safety solution represents the consistent continuation of the open and PC-based control philosophy from Beckhoff.
Due to their modularity and versatility, the TwinSAFE terminals fit seamlessly into the Beckhoff control system.
All essential areas of automation technology are covered. TwinSAFE offers solutions in the control, I/O, motion, automation, and MX segments. All components can be combined across areas to provide a fully comprehensive security architecture for almost any customer application.
Your winning edge through complete integration of safety functionalities
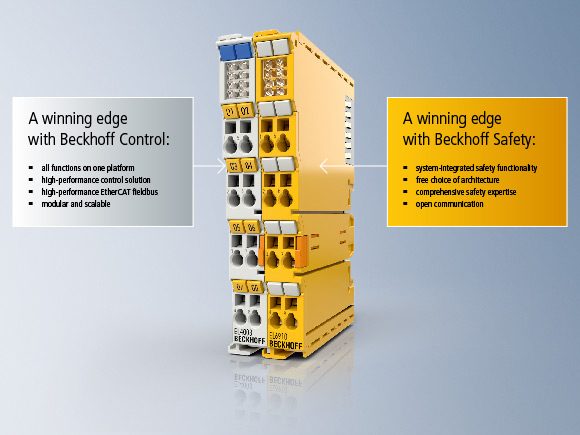
Safety and non-safety are converging
As a specialist for PC-based control, Beckhoff enables especially simple implementation of all required safety standards through direct integration into the Beckhoff control system. This is based on a comprehensive, highly scalable and modular automation portfolio, extending to all components from IPC to I/O, motion and software. All functionalities can be integrated into the overall control system with this portfolio – from HMI to measurement technology, IoT, vision, PLC and motion through to safety. Safety can therefore be integrated seamlessly with considerably reduced effort, because machine builders are gaining access to a uniform tool base and hardware platform.
System integration can be realized in all application areas with TwinSAFE, effectively ending the historically strict separation of “safety” and “non-safety”. At the same time, TwinSAFE impresses through ultimate flexibility and scalability. All safety features can be integrated in any conceivable machine architecture – from stand-alone control to compact control and the “traditional” solution through to distributed control and software-based control, which allows even the most complex requirements to be fulfilled. End users can therefore obtain a complete safety package tailored to their needs, while unnecessary costs for overdimensioned safety solutions are avoided.
Machine builders and users will benefit from the extensive and long-standing safety expertise provided by Beckhoff. The full wealth of safety know-how is available in-house with Beckhoff and is drawn on for customers in every individual TwinSAFE solution. The focus is on the principle of openness, as is typical of Beckhoff technology. On the one hand, the safe communication protocol Safety over EtherCAT (FSoE, Fail Safe over EtherCAT) is internationally certified and on the other hand there are no restrictions regarding transmission media.
Your winning edge through complete integration:
- consistency: everything from one source
- connectivity: all information available in one integrated system
- adaptability: modularity and scalability for simple adaptation to current and future requirements
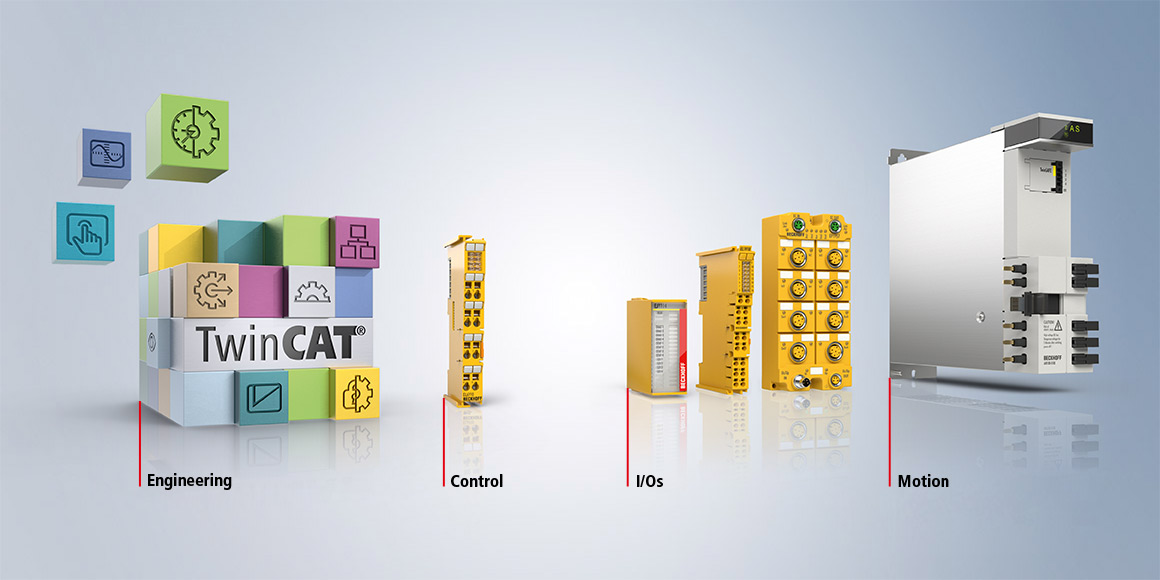
TwinSAFE – the cross-sectional solution
Non-safety related automation technology from Beckhoff can essentially be divided into four categories, that is, IPC (control), I/O (input and output), motion (drive technology) and automation (software). These components can be used to realize the most comprehensive range of automation tasks. As the complexity of non-safety related control functions continues to grow, the requirements with respect to safety technology are increasing in the same way. Modern safety technology therefore covers a very broad range of tasks, with appropriate safety solutions required in all areas of automation.
TwinSAFE offers the right solution in all application areas. A broad range of components equipped with TwinSAFE Logic means full freedom in terms of choosing an architecture for the safety application at hand. In terms of I/O components, the TwinSAFE system offers an appropriate choice of safe input, output and mixed components, allowing the solution to be easily adapted to the specific requirements. The broad range of TwinSAFE components for all requirements includes the EtherCAT Terminals for control cabinet installation, the EtherCAT Box modules for use directly in the field and the EtherCAT plug-in modules for use in series machines.
In the area of drive technology, too, solutions are scarcely conceivable any more without safety functionality. Beckhoff has therefore integrated safety functionalities in its drive solutions early on, both into standard and compact drive technology. In the area of engineering, the safety and non-safety tools from Beckhoff have already merged, enabling a universal configuration and programming of all applications. With a graphical editor, the TwinCAT Safety Editor simplifies the implementation of safety applications by means of certified function blocks. A certified application manual makes the engineering process even more straightforward from conceptual design through to realization.
Flexible implementation of safety solutions with TwinSAFE:
- comprehensive software support
- high-performance safety controllers in various form factors
- safety components for different environmental conditions
- safety components in the most diverse granularities for optimum adaptability
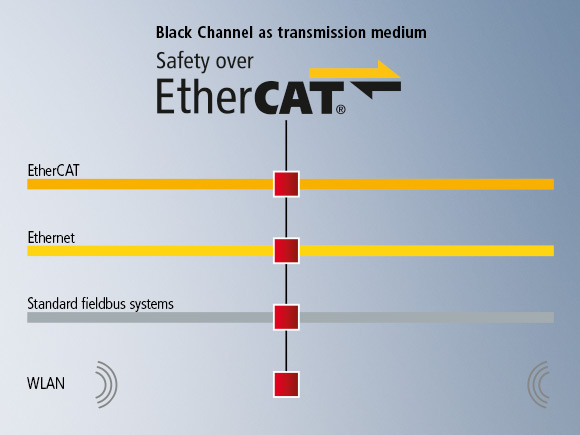
Safety over EtherCAT (FSoE, Fail Safe over EtherCAT)
The Safety over EtherCAT (FSoE, Fail Safe over EtherCAT) protocol defines open, safe data transmission. The technology certified by TÜV is internationally standardized according to IEC 61784-3 and fulfills the safety requirements specified by IEC 61508 up to the SIL 3 safety level. The transport medium is considered as a “black channel” in Safety over EtherCAT communication, meaning that the FSoE protocol can be transmitted using any communication technologies – over EtherCAT or Ethernet, but also via standard fieldbus systems such as CAN and also over wireless networks. FSoE is an ideal complementation of the open EtherCAT technology and guarantees high-performance transmission of control and safety information via the same communication system.
Benefits of the highly flexible communication system:
- flexibility through transmission via any media
- flexibility through the large numberof component vendors
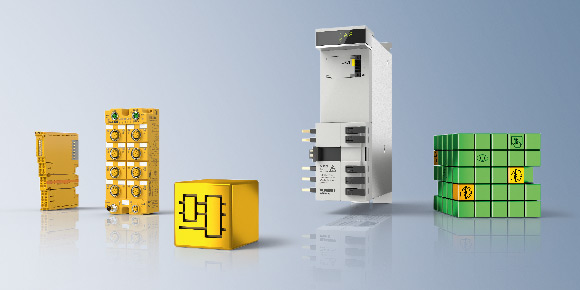
Integration of Logic functionality in all TwinSAFE components
With the introduction of the new Logic generation (from EL6910 on), Beckhoff has triggered a revolution in safety technology. The functionality of the TwinSAFE Logic is integrated in all new TwinSAFE components, thus considerably extending the range of potential deployment and application scenarios. TwinSAFE is becoming significantly more flexible in terms of adaption to individual safety requirements of a machine. For example, the integrated TwinSAFE Logic functionality in a digital input component (e.g. EL1918) can be used to selectively preprocess sensor data directly on the component. This preprocessing function can be developed separately and likewise verified and validated separately. If a central safety controller – central from a safety technology perspective – exists, it therefore only has to process the resulting sensor data. Special knowledge for ensuring proper preprocessing is then no longer needed, reducing the complexity of the centralized safety application and in turn simplifying validation and verification of the centralized safety application.
In addition to this “simple” application for preprocessing data, the safety option can also be used, for example, within a multi-axis AX8000 servo system to control a complete axis group from a safety technology perspective, while a central safety controller is used to control the overall axis group. By integrating the logic functionality in all TwinSAFE components, an even more flexible and complex modularization of a system can now be implemented very cost-effectively and efficiently.
Application scenarios of the integrated Logic:
- specific preprocessing of signals directly by input components
- fast local responses through localized safety applications
- efficient and flexible modularization without additional costs