Ability to implement Ethernet-APL on a modular basis with Beckhoff
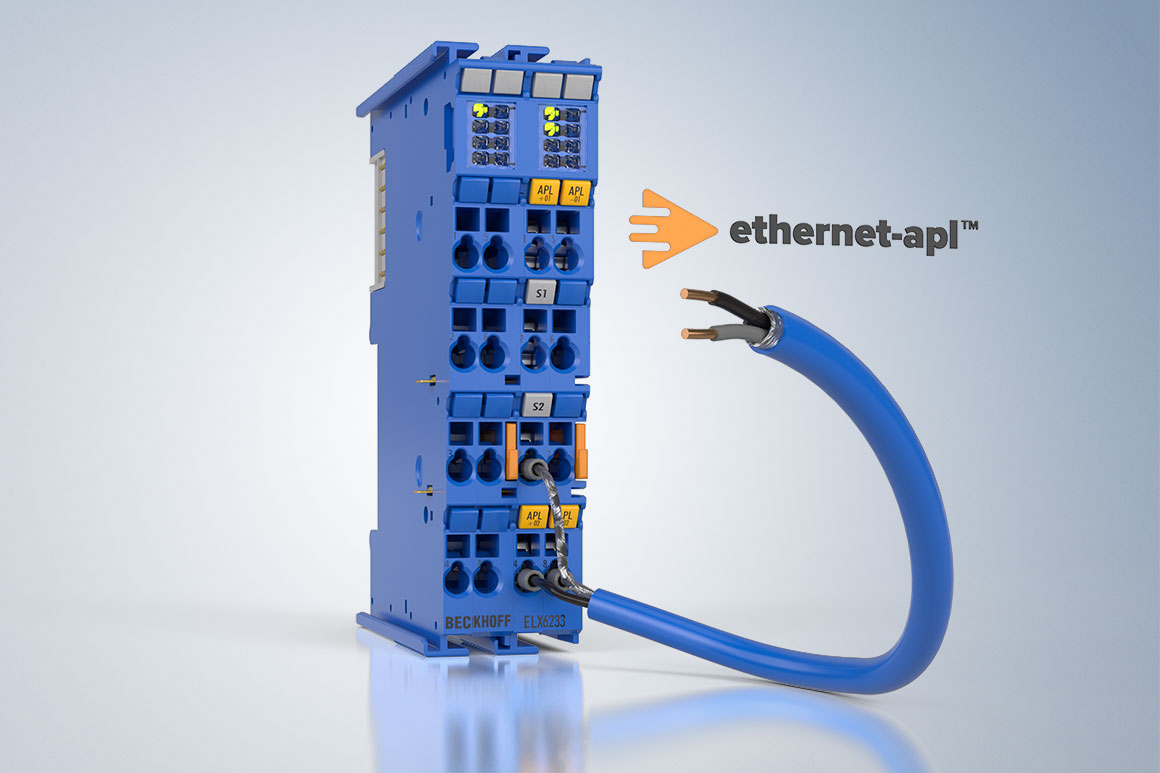
The vision of the Ethernet-APL concept is to implement the entire communication in process technology plants – from the field level to higher-level control systems – on an Ethernet basis. New APL-capable field devices are also required to convert entire plants. Since the technology is still relatively new and involves a high level of development work, the market does not yet offer a broad range of devices. The added value of a transmission rate of 10 MBit/s is also limited for simple digital sensors.
This is why Beckhoff integrates the Ethernet-APL technology into its modular terminal portfolio. The compact ELX6233 can be mounted in the control cabinet in combination with other EtherCAT Terminals. Two Ethernet-APL field devices can be connected via each ELX6233 terminal. As with all EtherCAT Terminals in the ELX series, the ELX6233 enables the direct connection of intrinsically safe field devices from zone 0 and zone 1. The EL6233 EtherCAT Terminal is available for applications with less stringent explosion protection requirements. It makes it possible to connect field devices from zone 2 hazardous areas and can also be integrated into the terminal segment on a modular basis.
Advantages of Ethernet-APL integration with Beckhoff
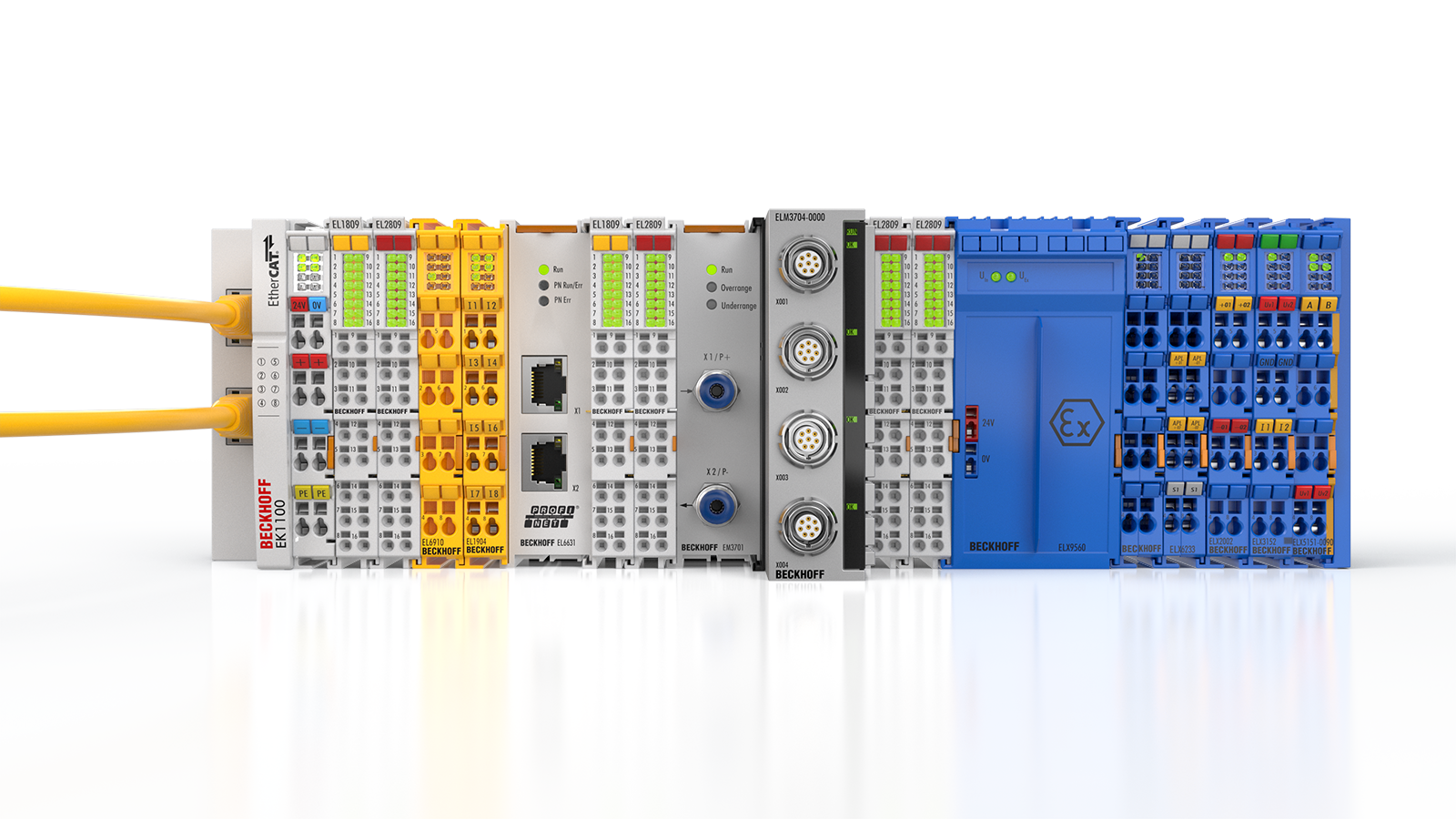
Modular and flexible combination options
The Beckhoff system solution allows all EtherCAT Terminals to be interconnected without requiring special tools. Both the ELX6233 and the EL6233 feature a standard housing and can therefore be easily integrated into existing terminal segments. When it comes to digitalization, direct connection to CX Embedded PCs in particular offers a whole host of advantages, including enablinggateway applications to process data from the field and filter it before sharing it further.
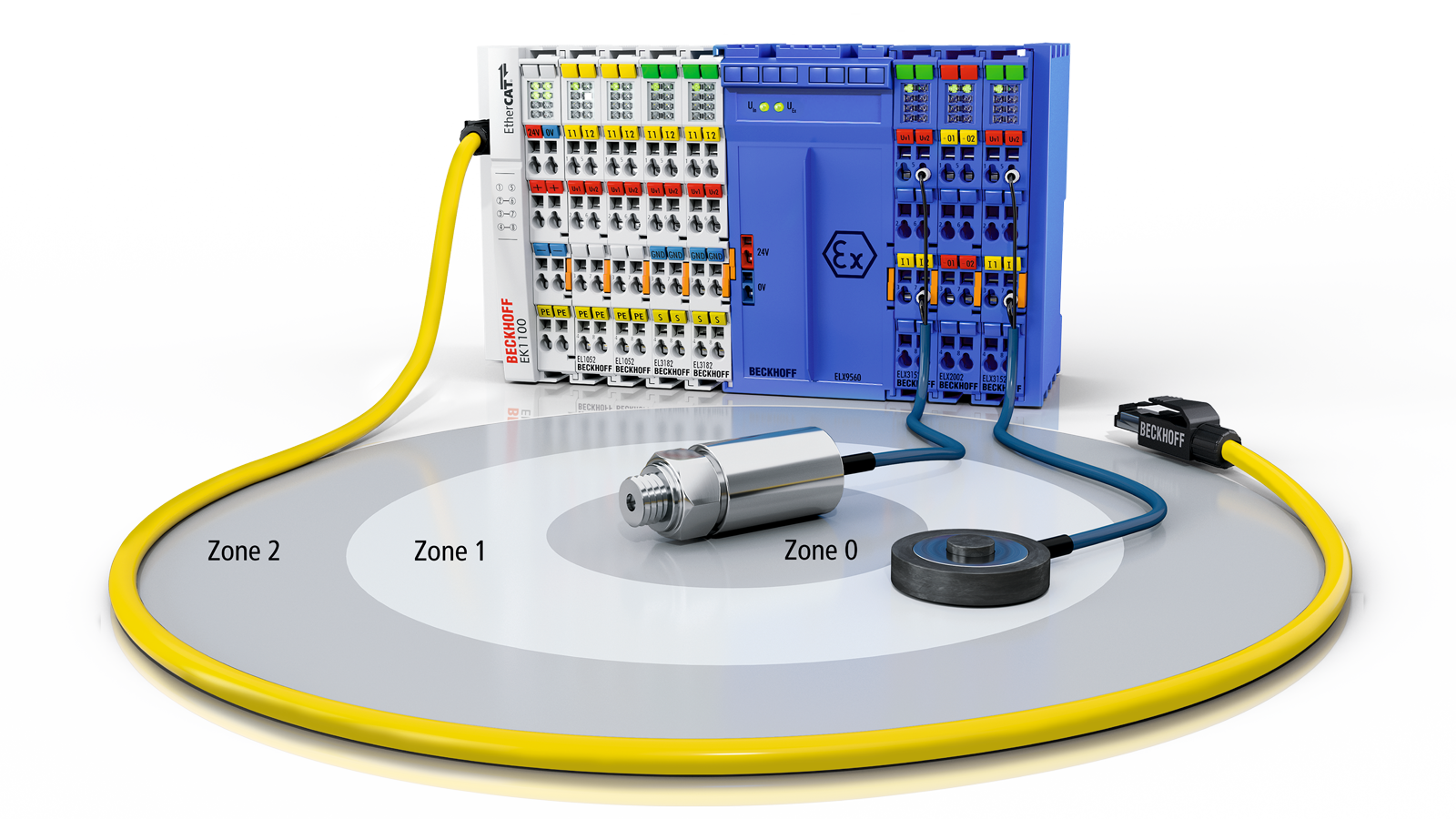
Connection of intrinsically safe field devices
Like many of our EtherCAT Terminals, the EL6233 and ELX6233 are suitable for mounting in zone 2 hazardous areas. What’s more, the special circuitry means the ports of the ELX terminal offer the highest explosion protection class and allow the connection of intrinsically safe field devices from zone 0. The parameters are adapted to suit the specifications of IEC 60079-47 and follow the SPAA port profile.
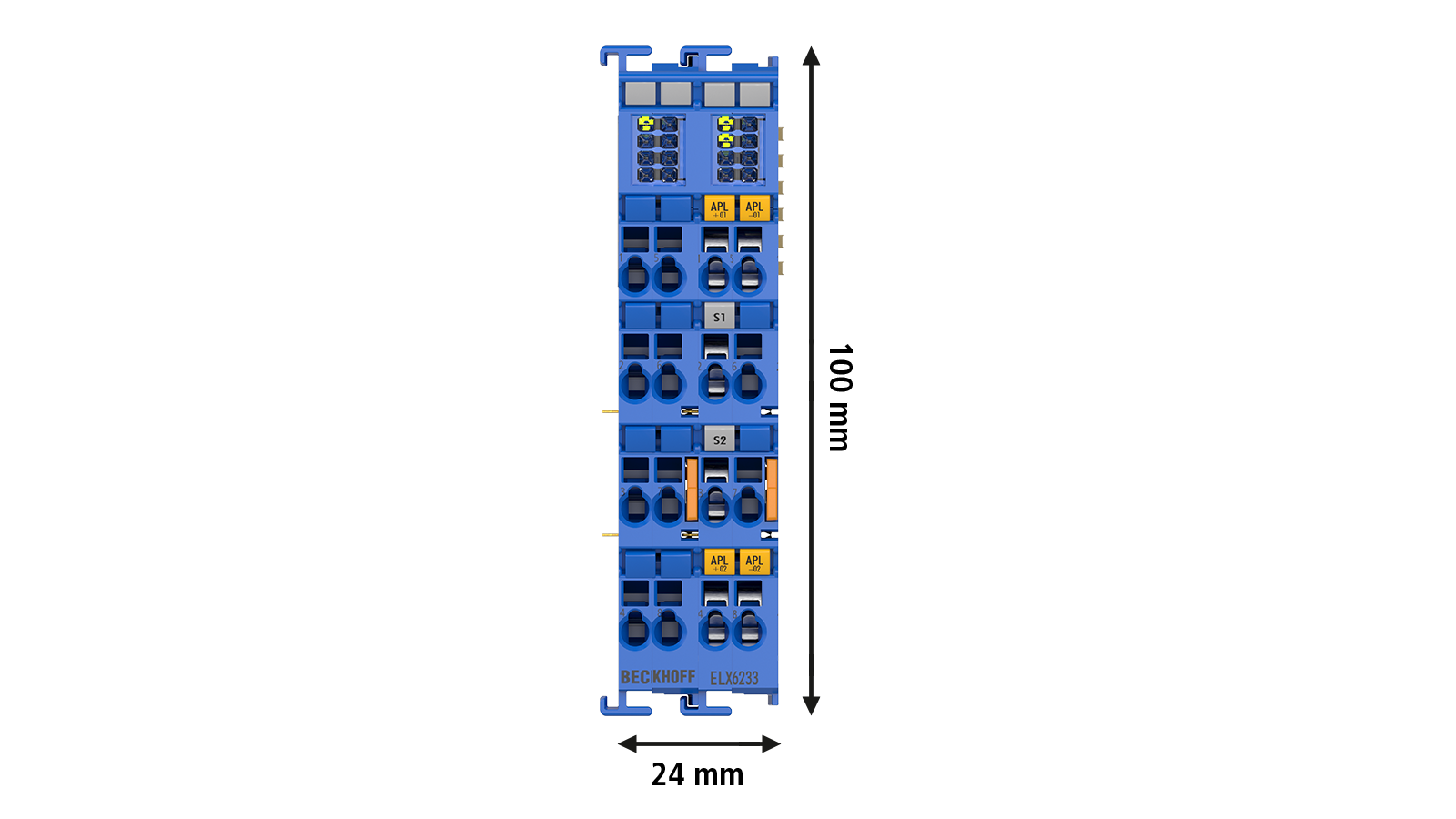
Space-saving solution
The ELX6233 or EL6233 allows you to create exactly the number of Ethernet-APL channels you need in your control cabinet. Its compact design not only saves you space, but also costs. And with a width of just 12 or 24 mm, the EtherCAT Terminals fit into any application, whether it’s a large process technology plant or a compact test setup.
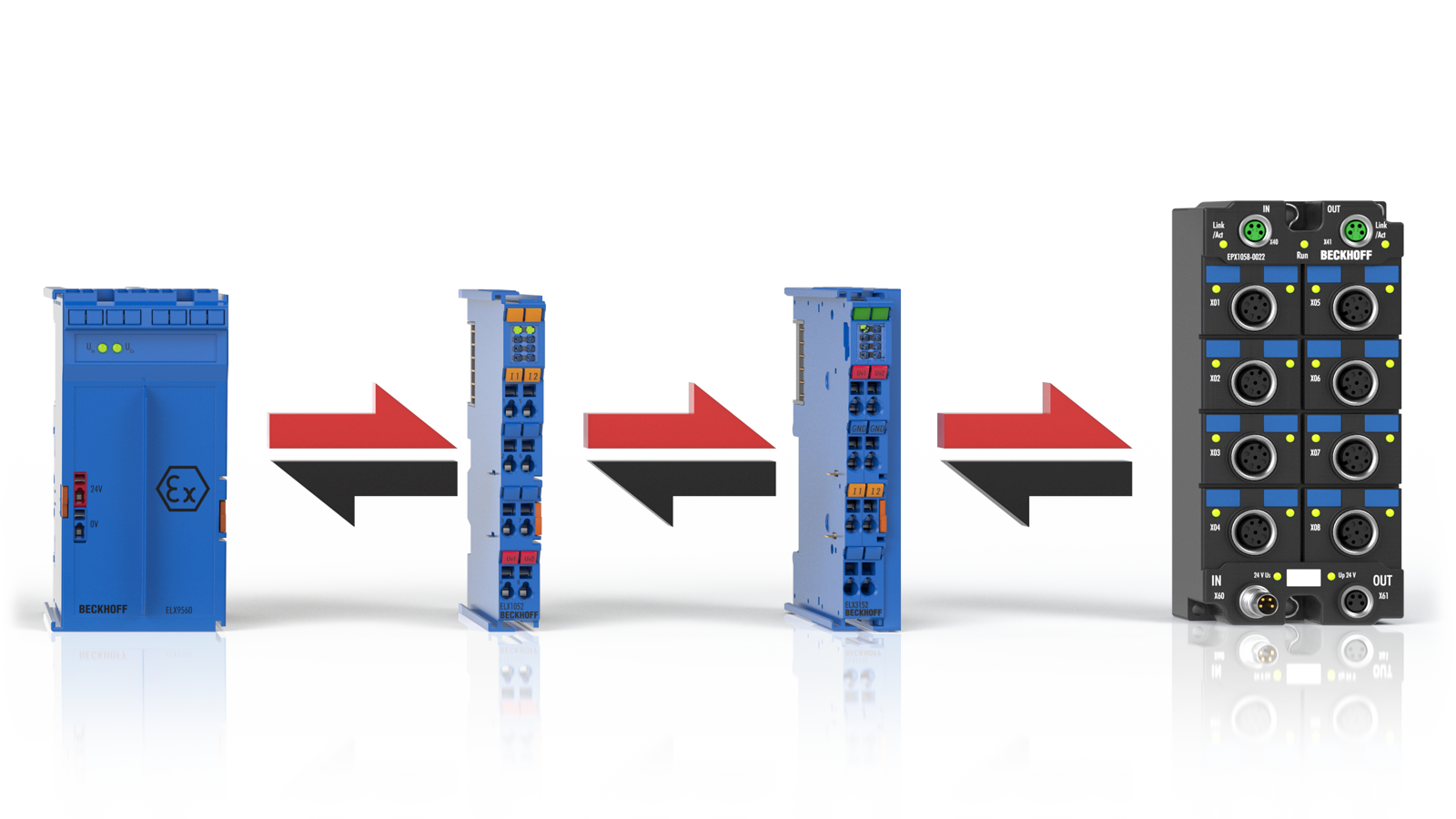
Fast communication with EtherCAT
Unlike in many PROFINET architectures, the controller is located directly in the EtherCAT Terminal and not in the higher-level controller. Since EtherCAT enables a more compact data size of the process image compared to PROFINET, the performance can be significantly increased in terms of cycle times. Data security is also higher than with classic switched networks due to the separation of individual ports and protocols.

Functional safety with PROFIsafe
Many of the field devices that will be connected via Ethernet-APL in the future will fulfill safety-related functions. Communication via PROFIsafe is therefore an important component of the Ethernet-APL technology package. PROFIsafe devices are still integrated via the EL6233 or the ELX6233. The only thing that needs to be added to the application is an EL6930.

Easy changeover from HART to Ethernet-APL
The modular design of the EtherCAT Terminals enables the EL6233 or ELX6233 to be combined with other EtherCAT Terminals, such as the EL3184 or ELX3184. In brownfield plants in particular, it may make sense to gradually switch from the familiar HART protocol to Ethernet-APL for warehousing reasons and due to the installed base. For these applications, the stations (small controller + terminals) can be preconfigured so that the technology can be changed by maintenance personnel as part of a simple device replacement.
Tutorial: Getting started with the ELX6233 (video in English)
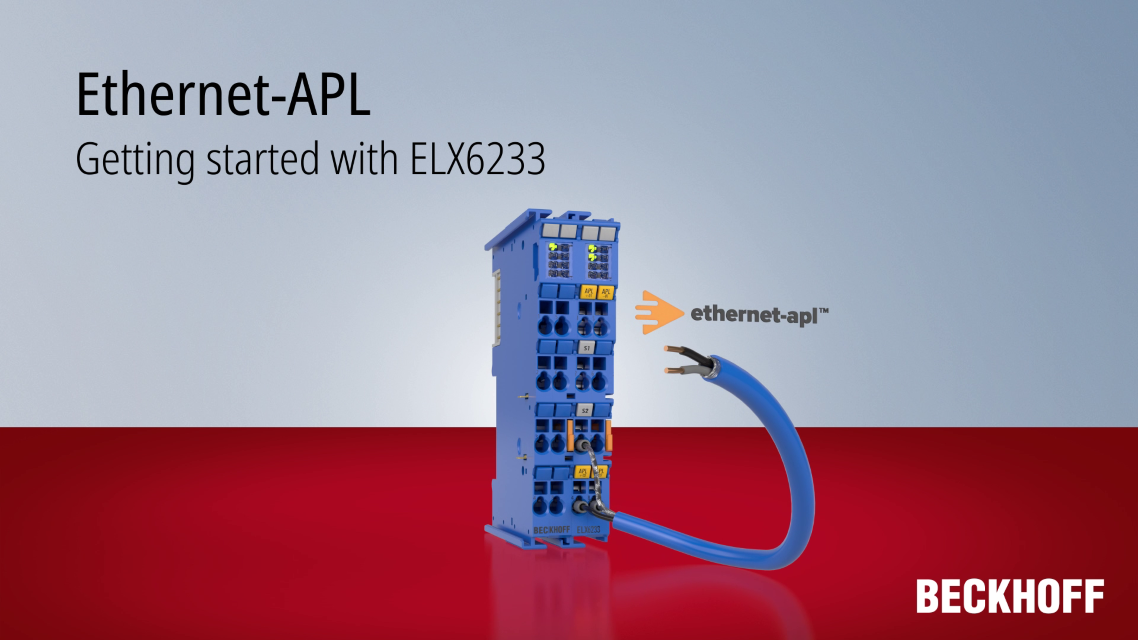
Learn how to commission the ELX6233 in TwinCAT and integrate field devices via Ethernet-APL. In this video tutorial, we guide you through the installation process step by step and provide useful tips on configuration and troubleshooting. We will show you how to effectively set up and optimize communication between the ELX6233 and connected devices.
The ELX6233 allows direct connection of Ethernet-APL-capable field devices from zone 0/20 and 1/21 hazardous areas. The sensors are supplied in accordance with the SPAA (TS10186) port profile and integrated via PROFINET. The flexible EtherCAT system architecture and ELX portfolio allow Ethernet-APL, HART, and simple digital signals to be integrated into the same terminal segment.
Further products and solutions for your systems
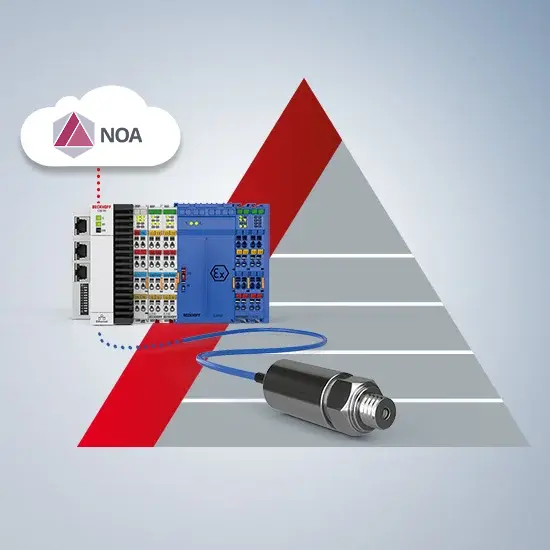
NAMUR Open Architecture (NOA)
Implementation of NOA concepts for seamless plant monitoring and data acquisition in brownfield and greenfield applications.
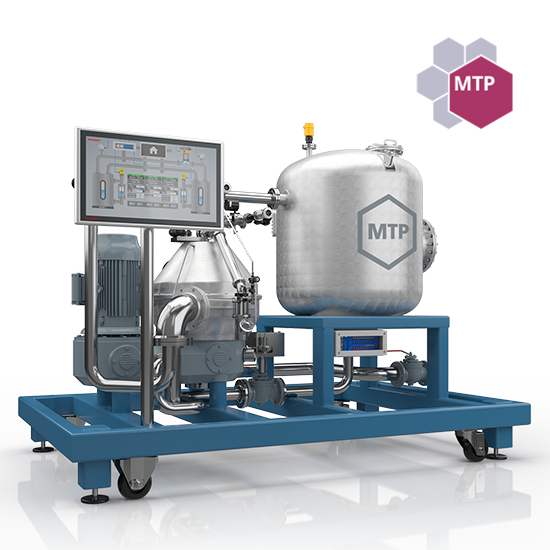
Module Type Package (MTP)
TwinCAT MTP integrates the Module Type Package concept into the engineering environment and enables efficient development of modular plants.
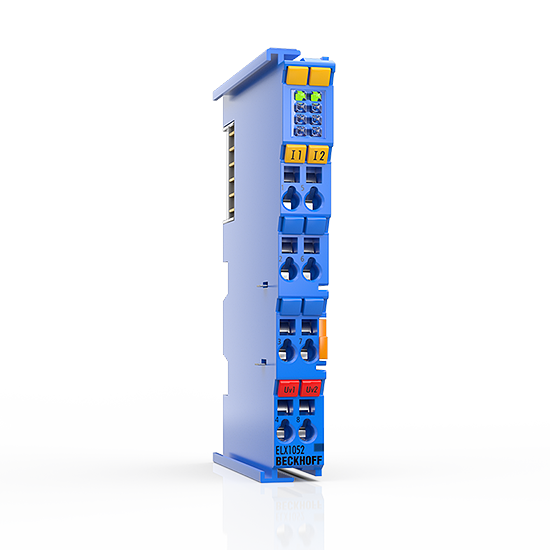
ELXxxxx | Explosion protection (Ex i)
The EtherCAT Terminals from the ELX series with intrinsically safe inputs/outputs enable the connection of field devices up to zone 0/20.
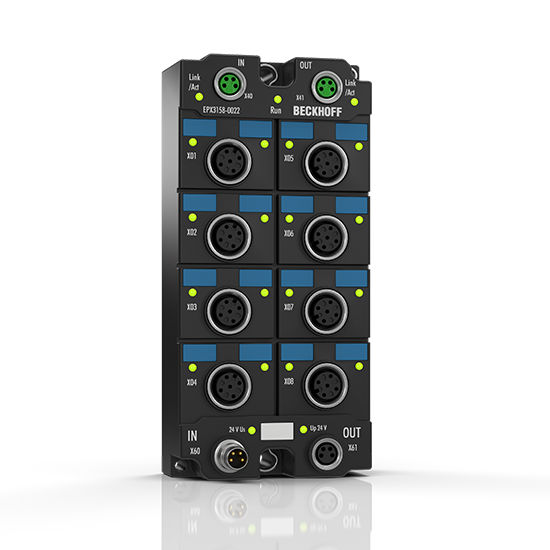
EPXxxxx | Explosion protection (Ex i)
The EtherCAT Box modules from the EPX series with intrinsically safe inputs/outputs enable the connection of field devices up to zone 0/20.