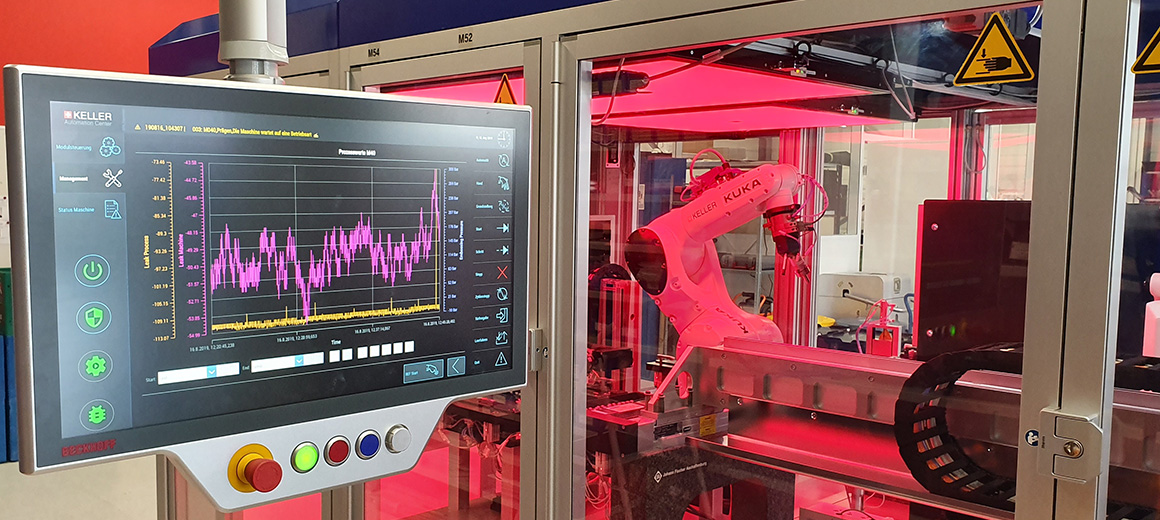
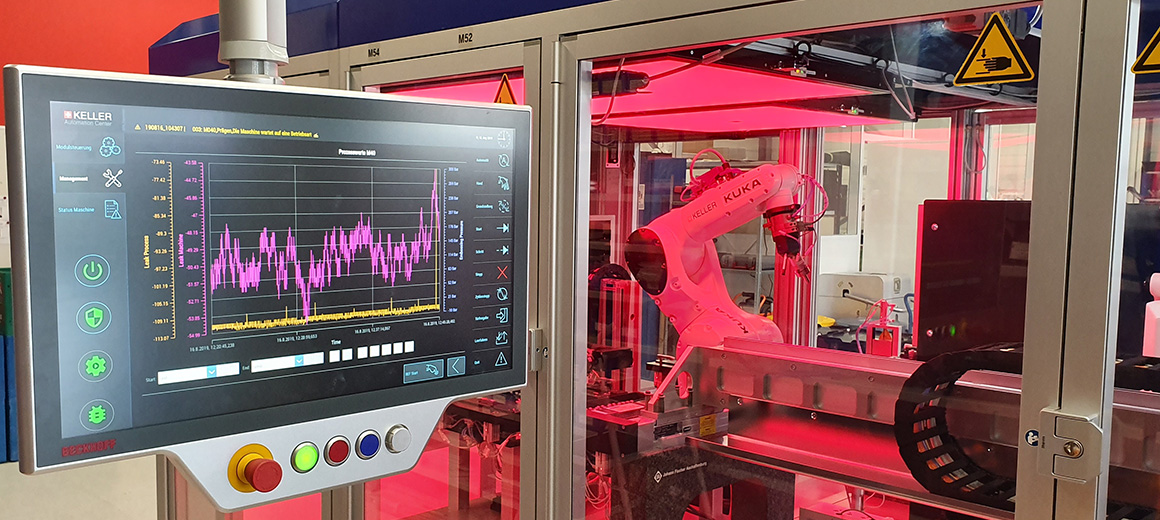
Diaphragm embossing machine for pressure sensor technology
The Swiss company KELLER AG für Druckmesstechnik is a specialist in pressure sensor technology and offers an extremely wide range of products for a host of applications that require correspondingly complex production processes. A diaphragm embossing machine used in prefabrication illustrates how the demanding process sequences can be automated with the aid of open control technology from Beckhoff, which is optimally scalable from a simple tabletop device to a large production plant.
Winterthur-based Keller AG für Druckmesstechnik was founded in 1974 by the inventor of the integrated silicon measuring cell, Hannes W. Keller, and proudly asserts itself as the market leader in the manufacturing of isolated pressure transducers and pressure transmitters. The piezoresistive pressure sensors offer very high accuracy as well as pressure ranges from 5 mbar to 2,000 bar. In addition to more than 500 standard products, Keller AG also develops and produces customer-specific solutions. In more than 35 highly specialized production islands, they manufacture large series of industrial OEM transducers, as well as special designs in very small quantities using the latest automated manufacturing processes. Applications for the pressure transducers include monitoring groundwater levels, controlling aircraft cabin pressure, switching from natural gas to gasoline in bivalent vehicles and serving as reference sensors in laboratory technology.
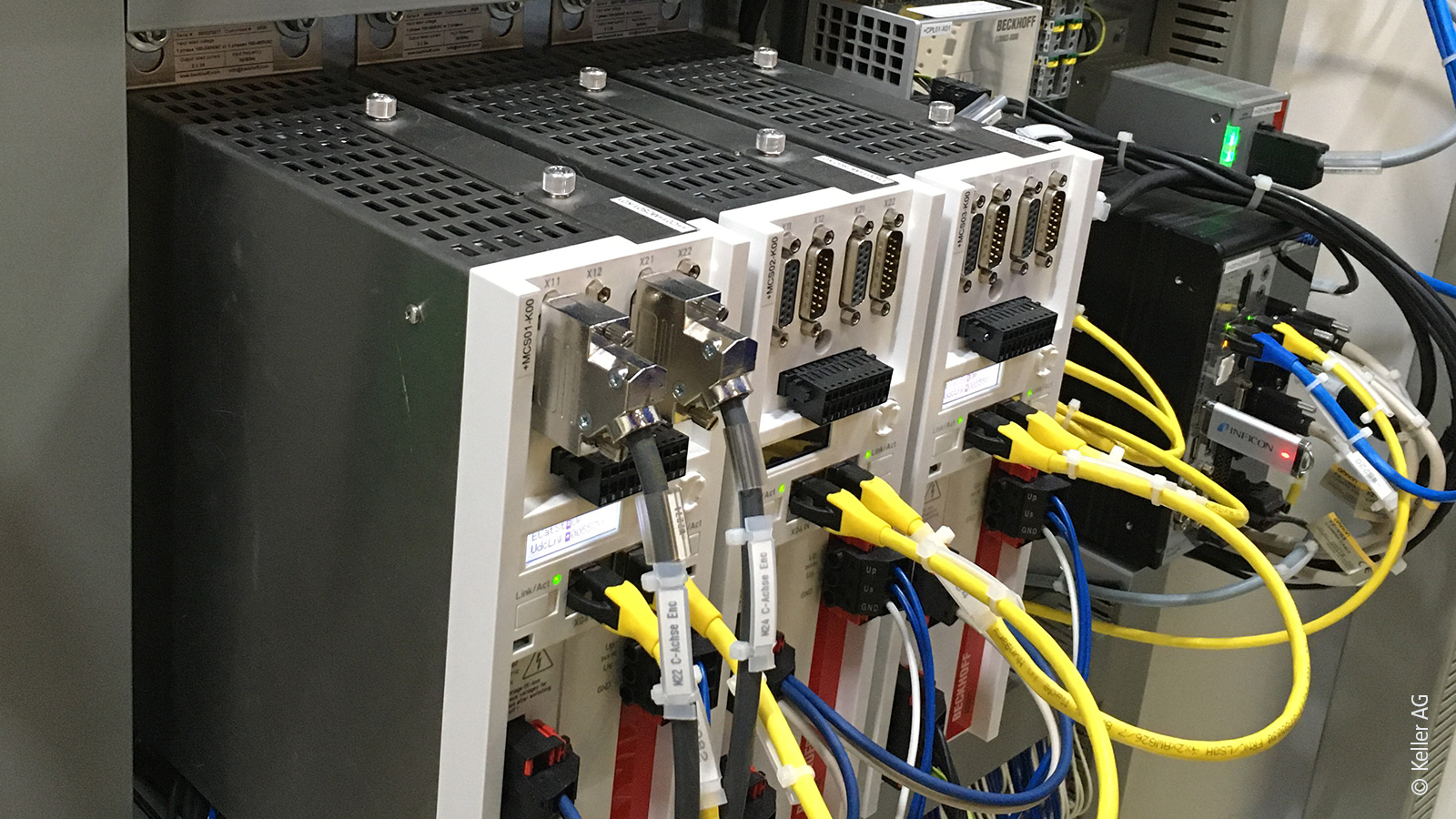
Embossing the sensor diaphragm is an essential process step
Embossing the sensor diaphragm is an essential intermediate process during prefabrication, as Florian Wernli, Project Manager at Keller AG, explains: “Most of our pressure sensors feature a steel housing filled with oil. The diaphragm is crucial for transmitting the pressure of the surrounding medium to be detected via the oil to the measuring chip inside the sensor.” This requires the diaphragm to have a special shape, which is achieved with a powerful automatic embossing machine. Bruno Thalmann, Development & Production Equipment at Keller AG, adds: “After a leakage pre-test, cleaning with compressed air and a thermal equalization process, we carry out high-pressure embossing and a definitive leakage test in the same process step using a hydrogen sensor. This is followed by an error check based on image processing and artificial intelligence.” The central handling element within the embossing machine is a KUKA robot, which acts as a pick-and-place unit to feed the blanks into the process and separate the finished workpieces into OK and NOK parts.
Bruno Thalmann explains the advantage of this fully automatic embossing and inspection system: “Our goal was to automate a process that previously required three manual stations in production. In this way, we were able to increase both manufacturing quality and production quantity.” Florian Wernli confirms: “The higher productivity is due on the one hand to the fast, fully automatic process with a throughput time of only 15 s per workpiece, and on the other hand to the fact that production can continue at night despite staff working in a single shift.”
Advantages of open and modular control technology
Keller AG has relied on PC-based control technology from Beckhoff since 2018. Bruno Thalmann sees advantages in the level of openness in terms of both programmability and the wide variety of supported interfaces. The optimal scalability of PC-based control also manages easily the system complexity or the desired degree of modularization from centralized to decentralized. All in all, TwinCAT 3 benefits from a modern, object-oriented software platform that is integrated into Visual Studio® and, together with TwinCAT HMI, offers powerful visualization capabilities that are consistent right through to tablet operation. In addition to the high computing power of the C6920 control cabinet Industrial PC, further important solutions from Beckhoff include compact drive technology with One Cable Technology (OCT), the EtherCAT P and CP-Link 4 one-cable solutions, safety technology integrated into the system with TwinSAFE, and the simple integration of EtherCAT-capable third-party components such as vision systems, flow controllers, valve terminals and electric grippers.
Florian Wernli cites the simple robot integration as a particular example of the advantages of system openness: “By integrating the robot via the EL6695 EtherCAT bridge terminal and TwinCAT Robotics mxAutomation, it was possible to implement the pick-and-place functionality via simple configuration without the need for special robotics expertise. The fact that we have full control of the robot via PC-based control makes this the perfect solution for us.”
In addition to the C6920, the hardware core of the automation solution is the CP3921 multi-touch Control Panel connected via CP-Link 4, which has a 21.5-inch display and push-button extensions. According to Florian Wernli, this provides the machine end user with a control unit that is as convenient as it is striking: “For us, design is an extremely important factor within the overall machine concept. Added to this is the high display resolution, which is necessary for convenient access to our inspection system. Featuring a remote control panel mounted on a support arm, the design means that the machine, which offers 360-degree accessibility, really can be operated quite flexibly from all sides.”
Compact and flexible drive technology and I/O level
Since the automatic embossing machine handles only small workpieces, compact drive technology from Beckhoff is practically made for this application. A total of 11 EL7211 and two EL7221 servomotor terminals, 11 EL9576 brake chopper terminals with ZB8110 external brake resistors, and 15 AM8100-series servomotors are used. Complementary motion axes from the portal system are implemented via three AX5203 Servo Drives and AM803x servomotors.
According to Florian Wernli, EtherCAT also offers great advantages in terms of data communication: “We consistently rely on the EtherCAT standard because, for one, we can count on a very wide range of components from both Beckhoff and third-party suppliers. Another bonus is that we benefit from the extensive diagnostic functions and level of openness when integrating other bus systems, for example.” He sees another important aspect in the various options for reduced cabling effort: “Essentially, every cable we don’t have to lay is a real bonus for us. PC-based control opens up additional optimization potential here with EtherCAT P – in addition to CP-Link 4 and OCT. In the I/O area, we consistently rely on EtherCAT P – that is, in the case of the automatic embossing machine, on I/O Box modules from the EPP series.” Specifically, these are an EPP1004 4-channel digital input, five EPP1018 8-channel digital inputs, nine EPP1809 and two EPP1816 16-channel digital inputs, as well as two EPP3184 4-channel analog inputs.
Bruno Thalmann also confirms the practical advantages: “EtherCAT P simplifies not only installation, but also maintenance. If, for example, a sensor fails, all you have to do is simply unplug the cable at the socket rather than having to pull the whole thing through all the drag chains. And, after replacing the device, you simply plug it in and the system is ready to go again.”