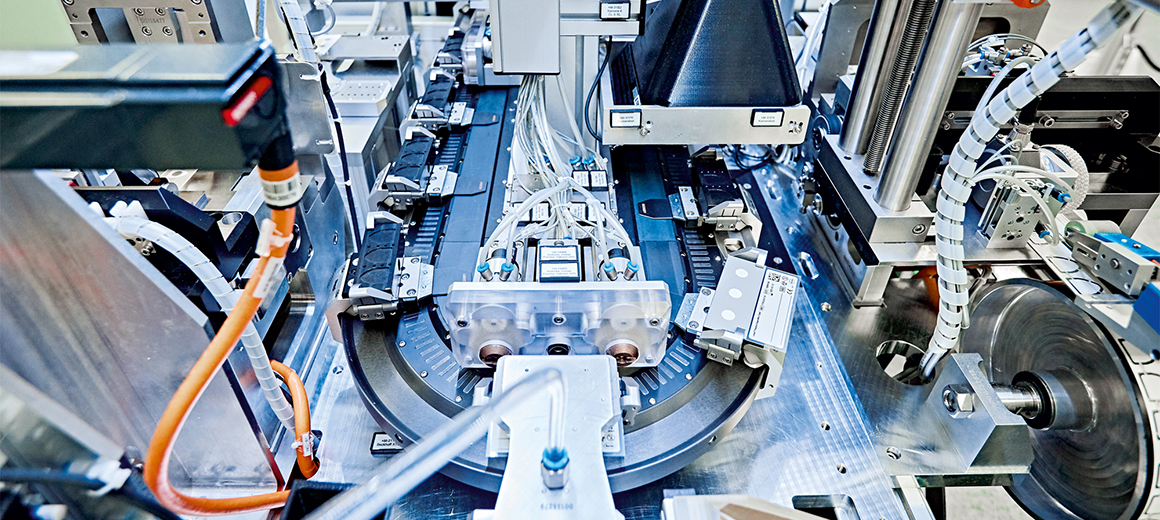
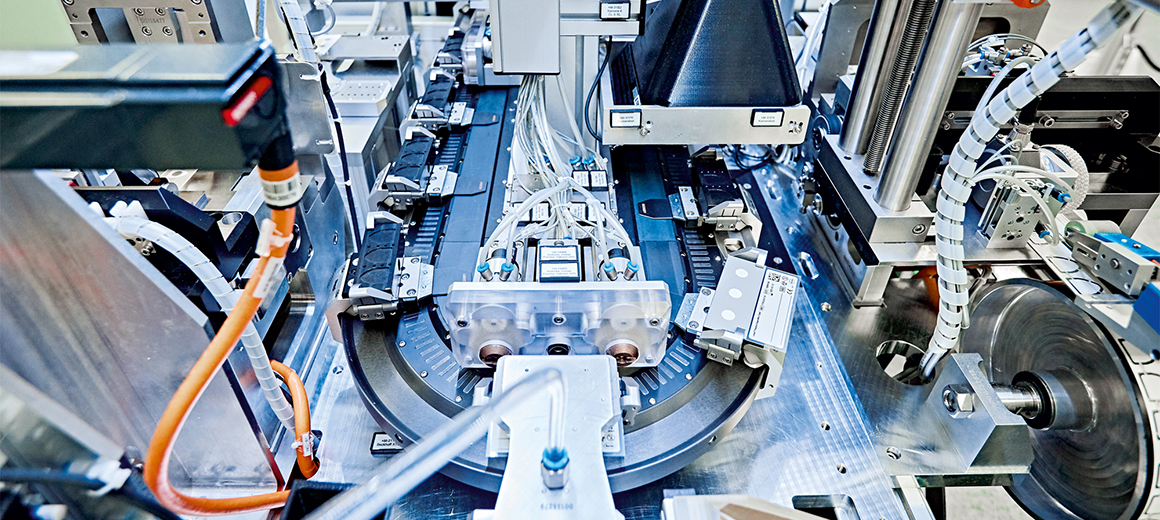
Roche: flexible and cost-effective production of Plasma Separation Cards
Roche has developed the Cobas Plasma Separation Card (PSC), a new technology that simplifies and improves the examination and monitoring of HIV patients, particularly in remote areas. For the first time, blood plasma samples no longer need to be cooled during transport to the laboratory. The prerequisite for this breakthrough was a flexible, compact and dynamic production technology that allows the PSC to be produced cost-effective. This was realized with the eXtended Transport System (XTS) from Beckhoff, which increases efficiency with its high flexibility.
Headquartered in Basel, Switzerland, the Roche Group operates in more than 100 countries and employs around 94,000 people worldwide. The company maintains a position as one of the leaders in personalized medicine, primarily through the combination of pharmaceuticals and diagnostics under one roof. The entire value creation chain, from diagnostics to the pharmaceutical endproduct, offers great potential for innovation. The Roche site in Mannheim, Germany, with around 8,300 staff is a case in point. A new Plasma Separation Card, part of the Cobas product range, meets the sensitivity requirements of the World Health Organization for determining an appropriate HIV therapy. The new product is a stable and easy-to-use blood plasma sampling card for subsequent HIV viral load testing.

The roughly credit-card-sized Cobas PSC requires only a small amount of blood from a patient's fingertip and also greatly simplifies sample transport. For example, for people in rural areas of sub-Saharan Africa, HIV testing is now more accessible as it eliminates the need to cool blood samples during transport to the lab. In this way, the Plasma Separation Card significantly changes the way plasma samples are taken and prepared, and it facilitates reliable quantitative testing even in environments with extreme heat and humidity.
Short time to market for complex card
The PSC is manufactured in a compact machine measuring around 3.5 x 3 m, in which the eXtended Transport System (XTS) from Beckhoff plays a central role. It was developed at Roche's Mannheim site by the company’s in-house mechanical engineering specialists in the Manufacturing Service & Technology department. Lukas Nagel, Specialist Engineer at Roche, explains that experts from development and production worked hand in hand, so that the project could be completed in just two years until it was ready for production. XTS played an important role as a highly flexible transport system, as it allowed the production unit to be adapted to changing requirements during the development process. Process optimizations can be implemented rapidly using the software-based functionality, which is easy to modify.
This was important not least in view of the complex structure of the Plasma Separation Card, which consists of several layers. Lukas Nagel explains: "A carrier layer is used for mechanical fixation. Next, a thin adhesive layer attaches to the plasma-separating membrane. Underneath is a non woven material separated with a chemical stabilizer, to preserve the human plasma for up to six weeks during transport. A label is provided on which the patient information can be recorded by hand. Finally, there is a protective layer. The special feature of the innovative product is that the human plasma only needs to dry up a little for safe transport and can then be easily liquefied again in the laboratory to be analyzed in the same way as normal blood plasma.”
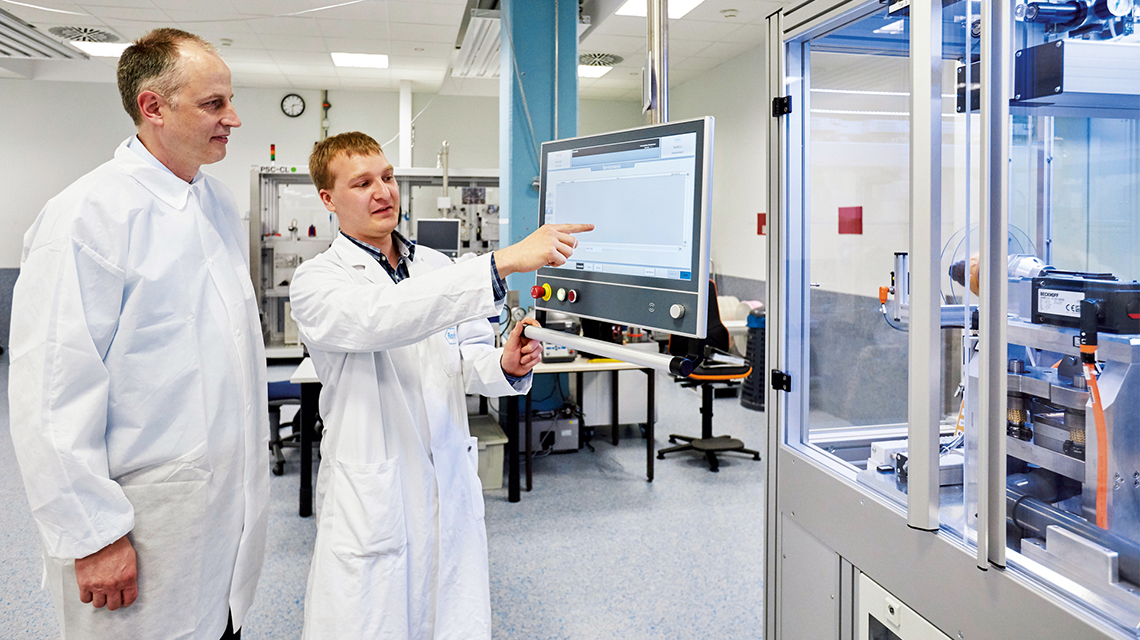
The complex structure of the PSC is illustrated by the sophisticated production process: The carrier layer is mainly used for sample transport. Two adhesive strips are applied to it, followed by the nonwoven fabric for plasma absorption.The desired geometry is punched into a carrier tape. Small adhesive dots are then applied to seal the plasma so that it cannot escape. Finally, a card is laminated with an adhesive tape to form the underside and bonded to the carrier layer. The two layers together then form the first intermediate product. These cond intermediate product, the PSC top side, is produced in a similar way. For this purpose, the desired geometries are also punched and the card corners are rounded off for easier removal in a subsequent step. After several optical test steps, both intermediate products are bonded and then the assembly and label placement are subjected to a final check.
Precise handling of sensitive nonwoven material
According to Lukas Nagel, the fact that special fabric for the plasma-separating membrane is very sensitive and expensive had to be taken into account during the development of the production unit: “This has resulted in stringent demands when cutting the nonwoven fabric and requires exact adherence to the desired geometry in order to minimize costs resulting from waste. Furthermore, the forces acting on the nonwoven fabric must not exceed 7 N in order avoid altering its structures and to ensure that the permeability of the structure is maintained.”
To guarantee this, a laser cuts out the membrane very gently, and a special measuring procedure occurs in the production unit, as Lukas Nagel explains: “When the unit starts up, the processing table from which the membrane is collected is measured. The system then checks the workpiece carriers on all 10 XTS movers. In this way, all component tolerances are compensated. In order to exert as little process force as possible, the membrane is applied to the adhesive layer with vacuum grippers. In this demanding product handling environment, XTS offers the great advantage that the component tolerances that were determined can easily be stored in the software and can therefore be assigned to each mover individually for the entire production process. In a conventional transport system, this would have to be implemented mechanically at each workstation and would therefore be much more complex. In addition, XTS automatically provides traceability, which would otherwise have to be implemented using QR codes, for example.” Furthermore, this kind of product handling facilitates efficient production. This is because any deformation of the nonwoven fabric cannot be detected optically early in the process, but only in the end product, resulting in rejects.
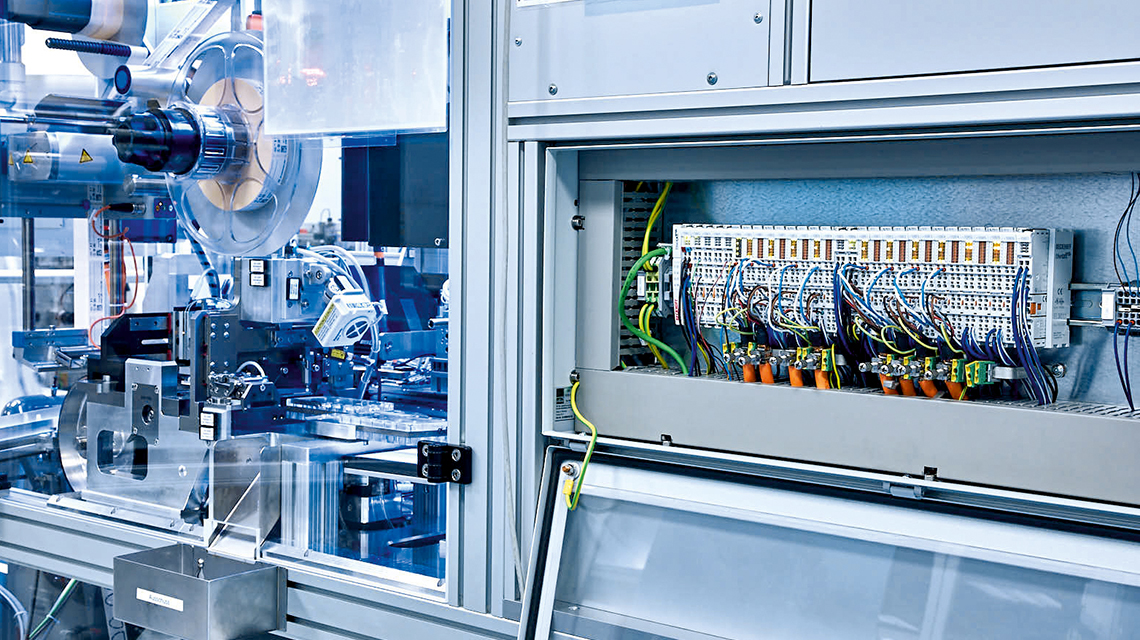
Lukas Nagel also appreciates the benefits of precision and software functionality in the motion axes of the workstations implemented using EL7211 servomotor terminals and AX5000 servo drives, such as cutting units, rotary tables and transfer arms. A good example is the measuring probe function of the AX5000 servo drive, which can be used to store the actual position of the controller without time offset, depending on an event: “This function comes into play when punching the geometry into the carrier tape and has been a great advantage during the development process. Initially, neither the exact card size nor the number of openings to be punched for subsequent application of the plasma were known. The lifting and punching sequences could be quite easily determined by software and adapted as required. For example, the card size could be optimized very efficiently, the number of application fields defined and the card corners rounded off.”
XTS for compact machine design
XTS enables highly flexible product transport with minimum space requirements, as Lukas Nagel explains: “With XTS, we were able to design an extremely compact system and accommodate it in the limited space available in the production environment. An XTS with 10 movers and a 3 m track length is used, around which the individual workstations are set up. This results in a symmetrical machine layout in which the first preliminary product – the carrier layer – is processed on one side and the second preliminary product – the upper layer – is processed and optically inspected on the other side. The membrane is cut out in the center of the unit, so that the complete card can be produced in a single XTS cycle. A system based on a rotary indexing table, which had been consideredinitially, would have been much larger.”
XTS offers additional benefits through its dynamic cycle and easy synchronization of fast workstations with slow process sequences. Workstations can be better utilized by duplicating time-consuming work processes. Lukas Nagel says:“The slowest processes in the line are laser cutting of the nonwoven fabric and the associated pick-and-place. With XTS, it is now very easy to prepare six cards at a time, transfer them to the laser cutting unit and then glue them individually to the corresponding card tops. Without this high flexibility offered by XTS, we would have had to process much larger membrane pieces or make provisions for multiple transfer stations. XTS, on the other hand, automatically adjusts itself to the slowest process step and remembers the current processing status and the missing input materials for each mover. The mover then moves to the corresponding stations.” In addition, the highly flexible product transport with XTS simplifies early ejection of defective sub-components. If a part is recognized as are ject, the mover ignores all other workstations and follows the other movers as a ‘pusher’ until the part can be ejected. Compared to a rotary indexing table, XTS thus avoids an unproductive cycle and unnecessary further processing of rejects.
In addition to the collision avoidance and synchronization functions provided by the TwinCAT 3 XTS Extension software, Roche also benefits from the option of limiting the controller current, as Lukas Nagel explains: “We use this function when the workpiece carriers for opening the holding clamps are mechanically fixed. Limiting the controller current simplifies this mechanical referencing without losing the position control via the XTS encoder system that is advantageous elsewhere in the system.” The EtherCAT communication system on which the concept is based offers further advantages, through its high performance, simple commissioning and widespread use as a global standard. According to Lukas Nagel, the IP 67-rated EtherCAT P I/O modules, which combine power and communication in a field-mountable form factor, also contribute to simplifying the production unit by reducing the wiring effort.