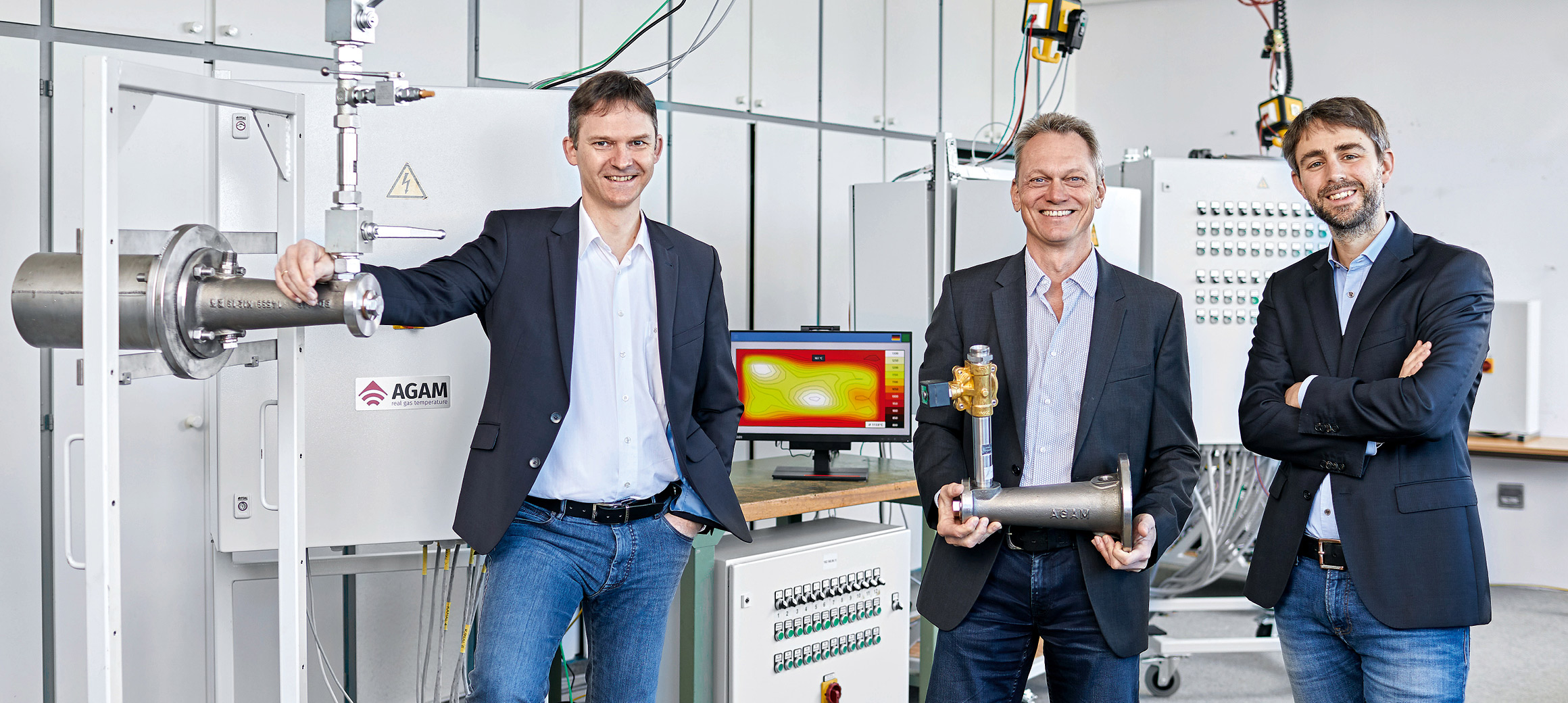
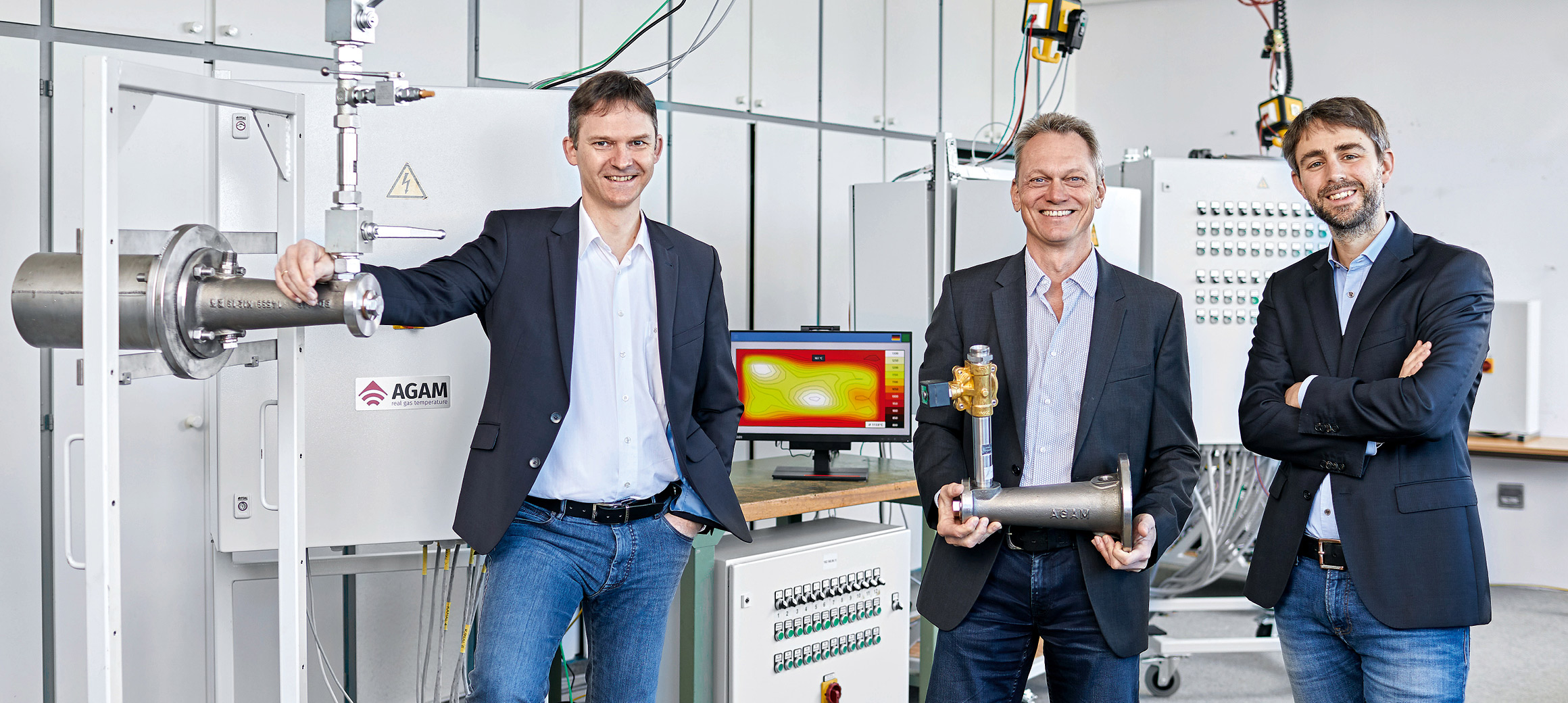
Control and measurement technology for acoustic gas temperature measurement in combustion plants
In highly complex plants such as those in the energy sector or steel industry, standards for the measurement and analysis technology in use are also correspondingly high. These include not only fast and precise data acquisition, but also a system design that is as flexible, expandable, cost-effective and space-saving as possible. This is precisely why Bonnenberg & Drescher relies on PC- and EtherCAT-based control and measurement technology from Beckhoff for its acoustic gas temperature measurement (AGAM).
Based in Aldenhoven, Germany, Bonnenberg & Drescher GmbH is a specialist in process analysis and optimization and works primarily in combustion applications. The company was founded in 1971 and initially dealt with nuclear engineering projects, from the design and lifetime analysis of cooling systems and critical components to nuclear safety considerations such as radiation protection, radioactive emissions and their behavior in the environment. In the 1980s, its range of services expanded to include conventional power plants, with a particular focus on the analysis and optimization of combustion processes. The company has been using the AGAM system for this purpose since the early 1990s, with the technology also used in waste incineration plants and blast furnaces.
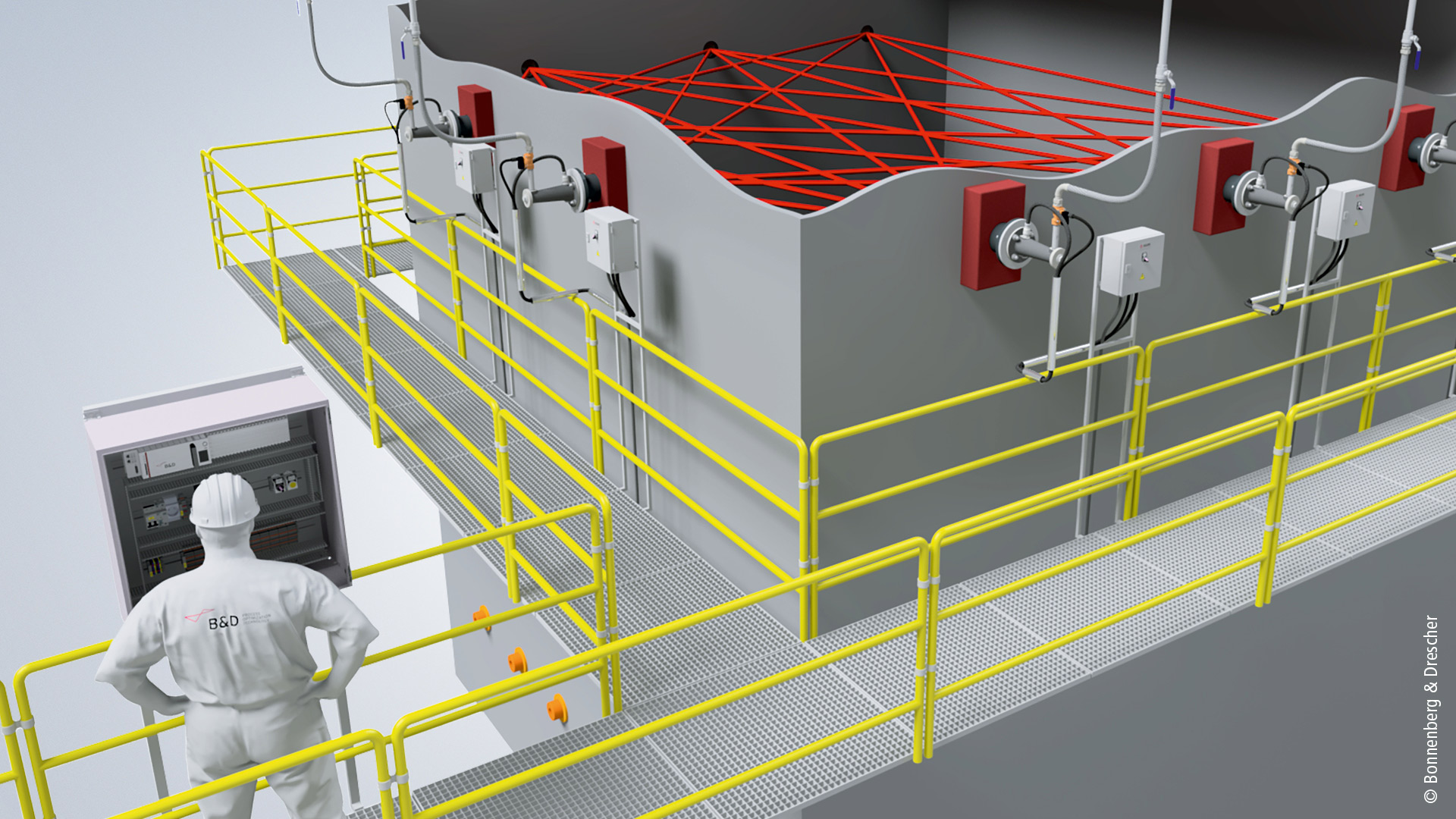
The physical principle behind the measurement setup is simple: the speed of sound in a gas depends on the gas temperature – the hotter the gas, the faster the propagation speed of the sound waves. For accurate measurement of gas temperatures, several microphones are distributed around the boiler, which in turn generate a signal that is received simultaneously by all units. This is then used to calculate a 2D temperature profile of the gas in the boiler. The special benefit of this method is the radiation-free measurement of the gas temperature, which is used to optimize processes within the plant for results including:
- optimized combustion to reduce fuel usage and lower CO2 emissions
- strong reduction of corrosion in the plant
- increased plant throughput and availability (waste incineration)
PC-based control replaces specialized products and additional components
In the past, the system setup for this measurement and analysis system was implemented rather ‘conventionally’: up to 16 channels with a 25 kHz clock frequency (i.e., 400,000 values/s) were acquired and processed using a powerful server system for measured value processing and archiving (through methods such as Fourier transformation and correlation). There was also a PLC for simple automation functions and various special products such as A/D converters for fast, deterministic and high-resolution acquisition of analog signals (sound waves).
The use of PC-based control technology from Beckhoff reduced the number of necessary components to a single CPU system. The CX2062 Embedded PC offers sufficient performance for the computationally intensive analyses with its Intel® Xeon® CPU (2.0 GHz clock frequency and 8-core processor), and even more powerful processors are available if necessary. According to Bonnenberg & Drescher, the fast and time-synchronous acquisition and digitization of the analog signals is particularly important for the quality of the analysis system. The higher the sampling rate, the more accurate the temporal resolution in particular, and the lower the jitter, the more accurate the temperature measurement via Fourier analysis and correlation of the measurement channels. This is where the EL3702 EtherCAT analog input terminals come into play, as these use the oversampling function, i.e. they run their own measurement cycle in addition to each fieldbus cycle, which they can use to ‘oversample’ the fieldbus. The distributed clocks of EtherCAT mean the time resolution is also very precise (+/-20 ns). What’s more, the entire data set is synchronized and time-stamped with the EtherCAT cycle and the TwinCAT software application with the same accuracy. With the EL3702 EtherCAT Terminal, signals can be acquired at up to 100 kHz, and the number of channels is no longer limited to 16 with the new system.
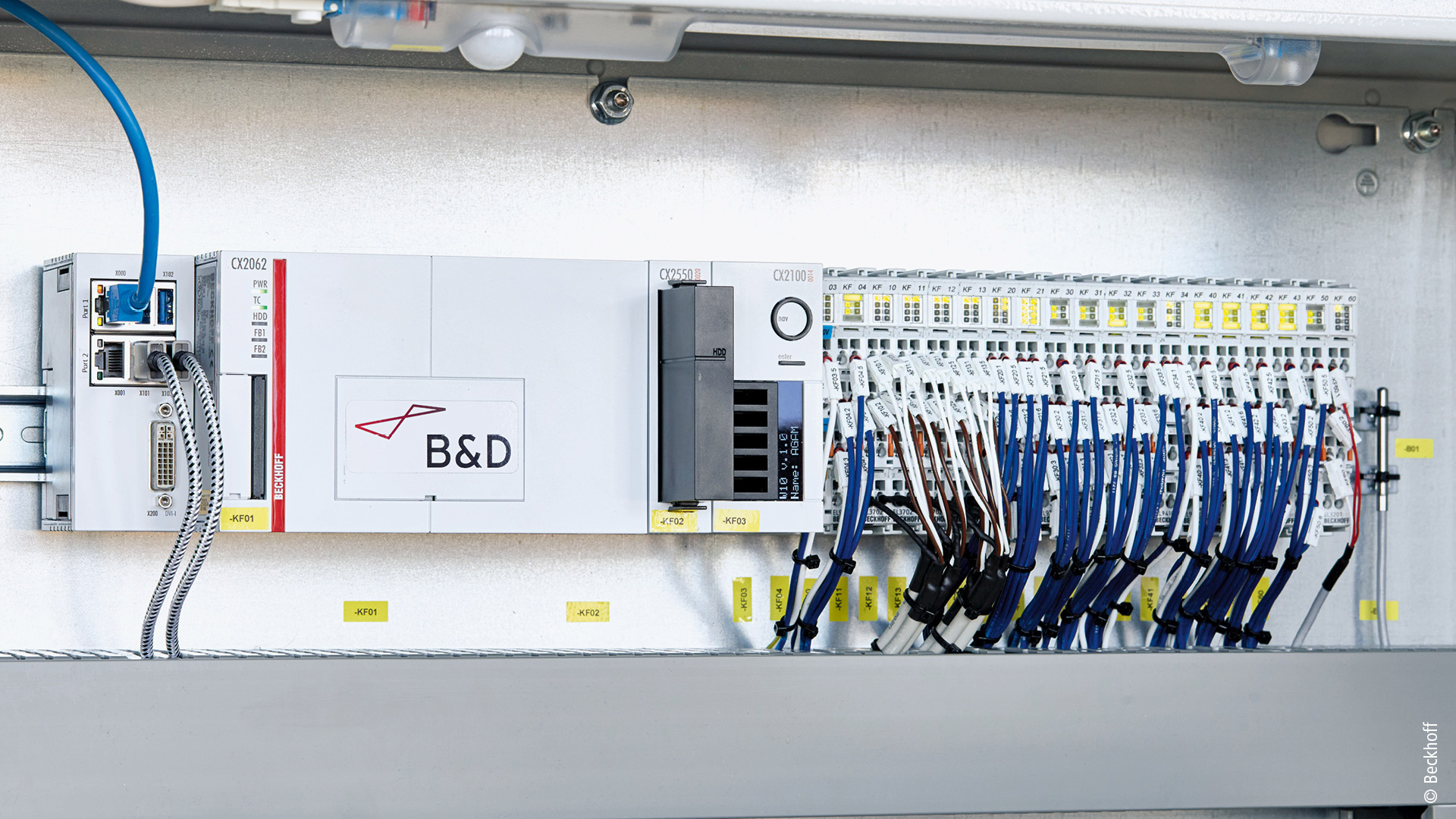
Modular system increases flexibility
The ADS router is the communication center of a TwinCAT system. From here, the pre-processed data is made available to other applications. The data are transferred to the C# environment of the AGAM system for further processing via ADS-DLL. The results are then also transferred back to the TwinCAT system via ADS and can be forwarded from there to customer systems via common fieldbus interfaces, such as EtherCAT, PROFINET and Modbus, or made available as a visualization web interface in the customer network.
On the I/O level, the system is also very easy to expand according to Bonnenberg & Drescher’s experience. Existing systems can be supplemented by simply plugging in additional terminals, and only further instances of existing software modules have to be formed within the software. The availability of EtherCAT Couplers with fiber-optic interfaces (plastic, multi-mode or single-mode fiber optic) makes the system even more flexible, as this makes it possible to reach distant measuring points and minimize analog wiring.
QM through reciprocal control system
The use of Beckhoff technology has also resulted in significant progress being made in terms of quality assurance. For the necessary simulations, essentially the same system is used as for the measurement technology, just on a reciprocal basis: the components on the boiler are simulated by generating the microphone data via the EL4732 oversampling analog output terminals, and the 24 V signals correspondingly in the reverse direction. Each measurement system undergoes several days of endurance testing before it is delivered to customers.
The modified AGAM-Q1 system has also been available since 2021. It has been approved by German inspection body TÜV and is suitable for use in official and certified temperature measurements in plants. The EL4723 output terminals are used for the legally required self-test of the measuring system.
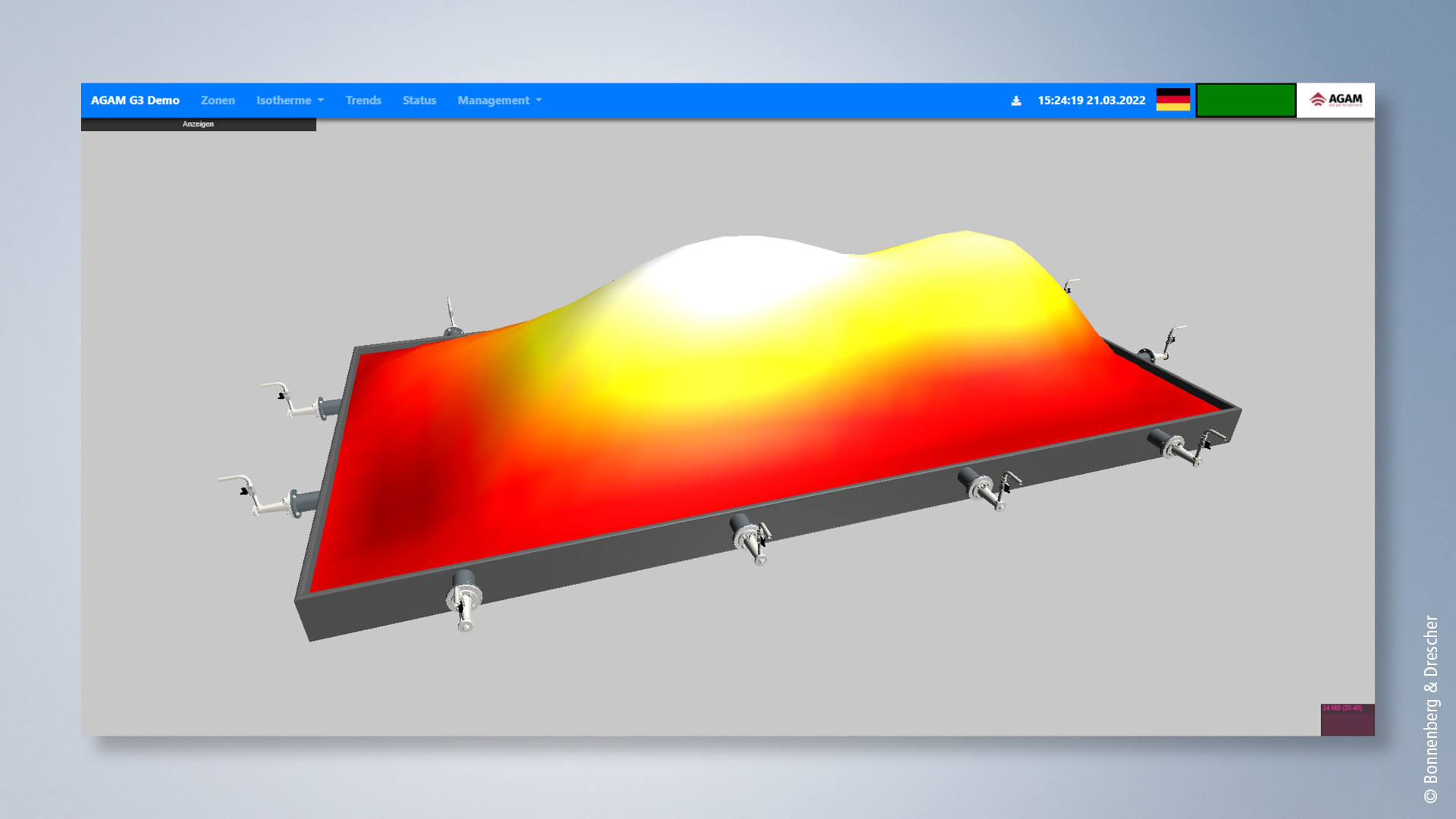
Overcurrent protection terminals save space and costs
In the case of the EL9227-5500 electronic overcurrent protection terminal, the initial focus was on its standard use: replacing conventional fuses with an electronic fuse with EtherCAT interface. The many benefits of this include:
- space and cost savings
- flexible configuration of tripping current, warning level for current and voltage, fuse characteristics, starting behavior, etc.
- complete measurement function of current and voltage as cyclic process data for the PLC (power supply and load diagnostics)
- extensive diagnostics – for example, with regard to trigger reason, setting changes by users and log files
In addition, Bonnenberg & Drescher also identified another very useful application scenario in that the electronic overcurrent protection terminal serves as a digital switching output with measurement and diagnostic functions, namely for solenoid valves. The measurement functions of this EtherCAT Terminal enable the current and voltage characteristics at the switching point to be displayed as trend lines, so that various valve faults – cable break, coil defect, or mechanical defects in the valve – can now be easily and reliably diagnosed.
Advantages of system integration
“The integration of measurement data acquisition, archiving, analysis and presentation offers tangible benefits for us,” sums up Dr. Martin Brodeck, Managing Director at Bonnenberg & Drescher. “At the start of the measurement chain, special electronics are replaced by standard fieldbus technology. This guarantees the supply of spare parts for decades and ensures that we are continuously involved in innovations without having to reserve resources ourselves.”
Another important aspect mentioned by Dr. Martin Brodeck is the long-term availability of the CX2062 Embedded PC, which is available for at least 10 years and subsequently covered by service for a further 10 years – and on a worldwide basis, no less: “Our customers can obtain these components almost anywhere in the world directly from one of the 40 Beckhoff international subsidiaries and via cooperation partners in more than 75 countries. The handling of the entire system has been significantly simplified compared to before, so it has become much more manageable for our customers. In many cases, they can now help themselves without us having to intervene. What’s more, having the embedded PC as the basis of our platform ensures a successful symbiosis of automation technology and the IT world, which is an invaluable advantage especially for our computationally intensive applications including database connections and web interfaces.”