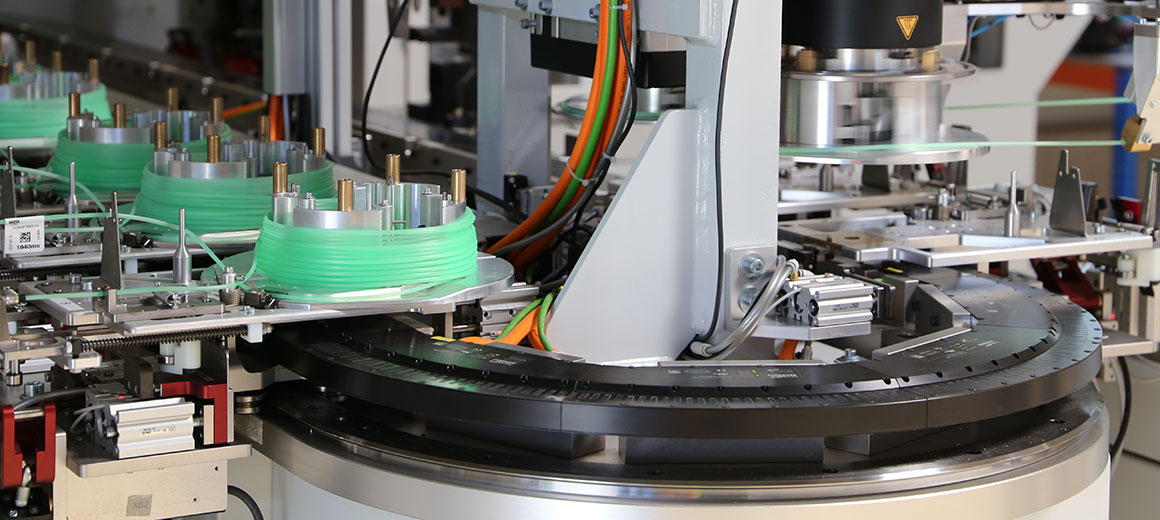
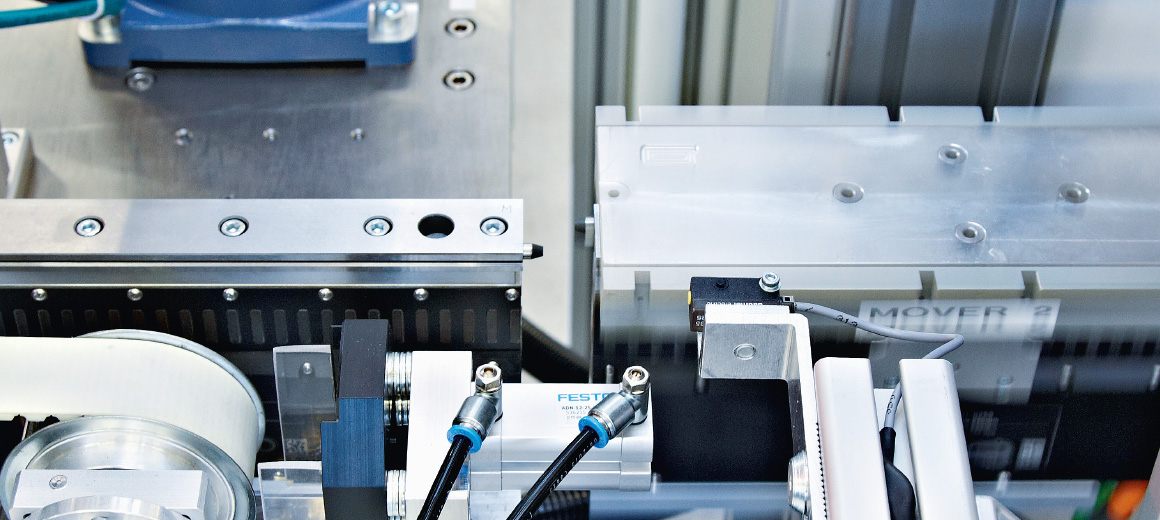
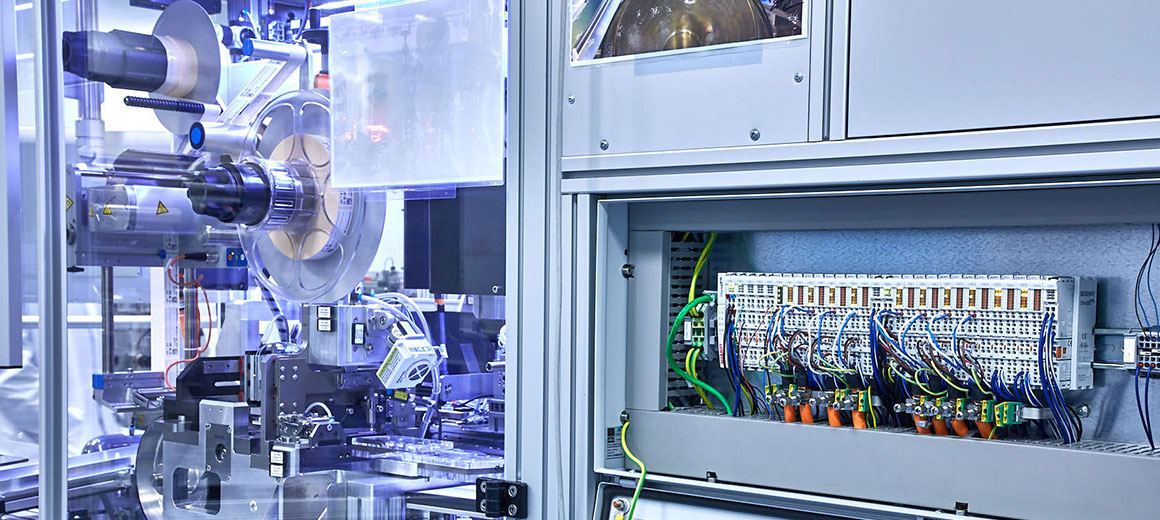
Flexible and cost-effective production of Plasma Separation Cards
Roche-Gruppe, Switzerland
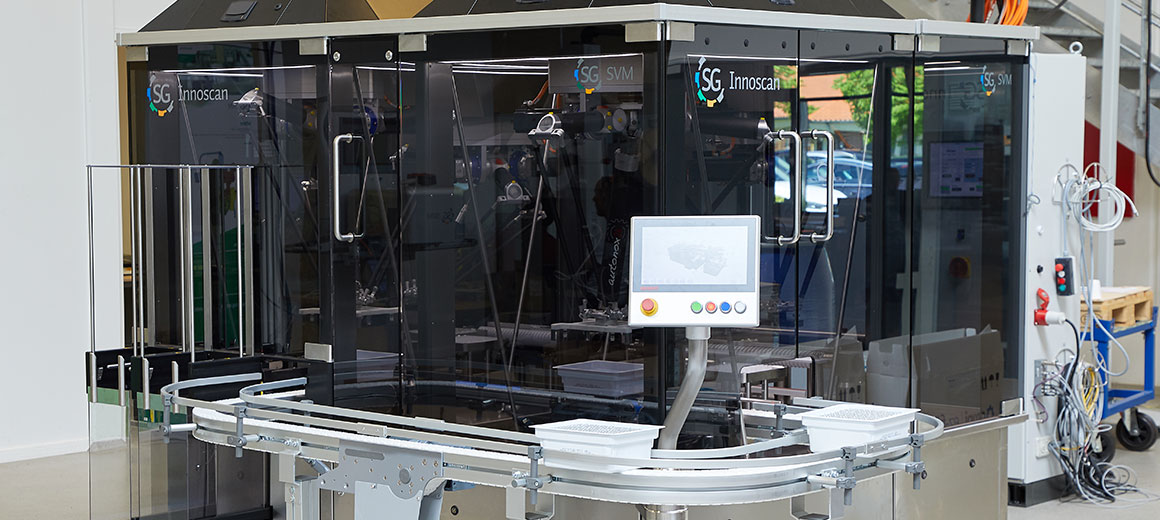
Headquarters South Africa
Beckhoff Automation (Pty) Ltd
Roche-Gruppe, Switzerland
With PC-based control, EtherCAT, and our intelligent transport systems such as the XPlanar planar motor system, XTS linear transport system, and ATRO modular industrial robot construction kit, we offer our customers a flexible and high-performance automation platform. Our powerful control technology is ideally suited to your assembly and handling processes where speed and precision are essential, but even ‘slow’ processes can benefit from Beckhoff automation solutions when it comes to productivity. This applies to all areas, too – from transport, joining, welding, and bonding through to assembly and testing, from a lot size of one to mass production, and from simple to sophisticated applications.
Do you have any questions?