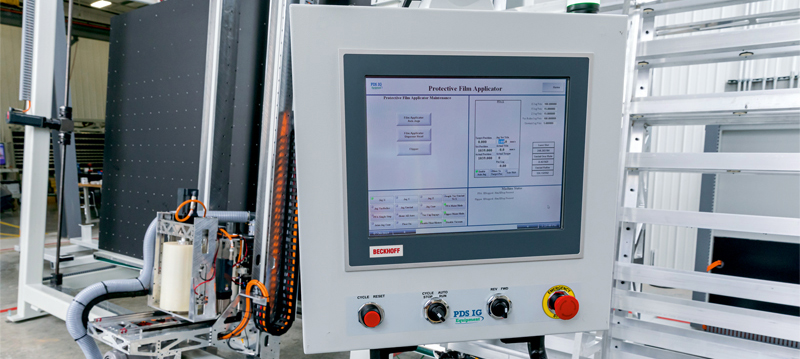
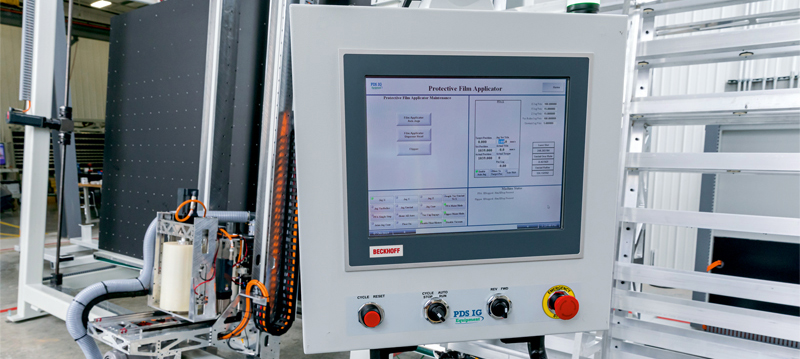
EtherCAT and PC-based control increase precision and flexibility in window film application system
In order to protect glass windows from damage during shipping and installation in buildings, they are covered with protective PET film during the manufacturing process. For this purpose, PDS IG Equipment developed a modular window film application system, which facilitates adaptation to customer facilities through open control technology from Beckhoff. The system delivers a throughput considerably higher than the industry standard, and it provides increased data transparency, which adds value for system operators.
PDS IG Equipment, based in Prairie du Sac, Wisconsin, was formed in 2011 and offers a broad range of window production machinery. PDS IG created a modular automated solution to ensure that protective PET film is applied to window glass units of all sizes during manufacturing with high repeatability, short cycle times and robust data acquisition capabilities, according to Michael Rapp, vice president of sales and part-owner of PDS IG Equipment. For this purpose, PDS IG selected EtherCAT and PC-based control technology from Beckhoff, which the company has been using successfully in other areas for some time.
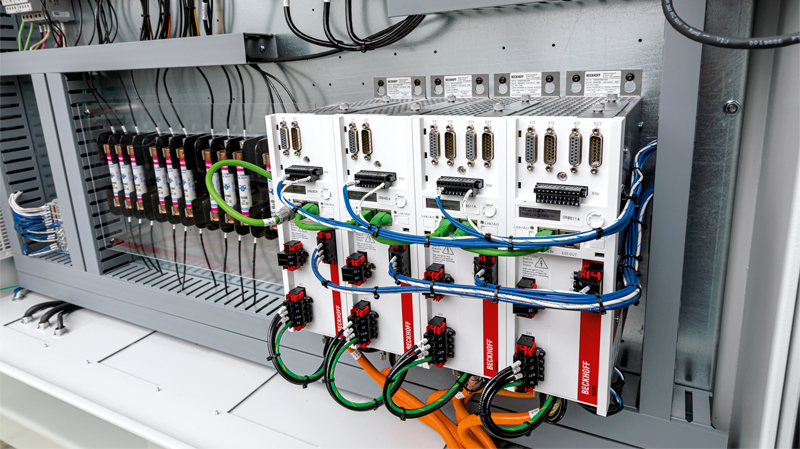
High demands on precision
The window film application system created by PDS IG uses multiple modules, beginning with an intake conveyor module, which transports each insulating glass (IG) unit into the film applicator module. The machine precisely measures each glass unit. The application head covers the surface with as many passes as necessary using 12- to 16-inch rolls of PET film. Once film is applied on one side, the IG unit moves into a glass-flipping station that turns the workpiece 180 degrees horizontally and conveys it into the second film applicator to cover the other side. Finally, an operator or robot offloads the fully protected glass.
When PDS IG engineers began to design the system in early 2018, they knew that real-time communication was key to ensuring high precision. The film applicator needed to leave a consistent “cutback.” This is a thin strip around the edges that remains uncovered, allowing the film to be removed after installation in the sash without any problems, and with it any dirt that may have collected on it. “These windows range from 12 inches by 12 inches (30 x 30 cm) up to 96 inches by 140 inches (245 x 355 cm)”, says Steve Polkinghorne, automation controls engineer at PDS IG. “Our equipment needs to keep that cutback the same across that area.” In addition to accurate measurement, this level of precision requires reliable motion control. In fact, it takes 28 axes of motion to properly control the conveyors and the X- and Y-axis movements of the film application head.
Flexible and open automation technology
The PDS IG window film application system relies on numerous Beckhoff technologies. For its operator interface, the system uses CP6202 “economy” built-in Panel PCs from Beckhoff. These panels are mounted to small electrical cabinets hung from the machine modules. “The CP6200 series allows us to run not only the HMI but also a thin client to increase modularity,” Polkinghorne says. “Depending on how many modules are used, a machine line that makes IG and applies protective film could span 100 feet. The thin clients allow users to navigate HMI screens for every machine module from any control panel.”
The machine control itself relies on a C6930 control cabinet Industrial PC (IPC) and TwinCAT 3 automation software from Beckhoff. The CPU core-isolation capabilities of TwinCAT 3 allow PDS IG to designate control functions such as PLC, motion control or safety to run on a specific core of the C6930 IPC’s quad-core Intel® Core™ i7 processor. Polkinghorne says the TwinCAT Database Server also allows flexibility to collect production information in SQL databases that customers can turn into actionable information to enhance production.
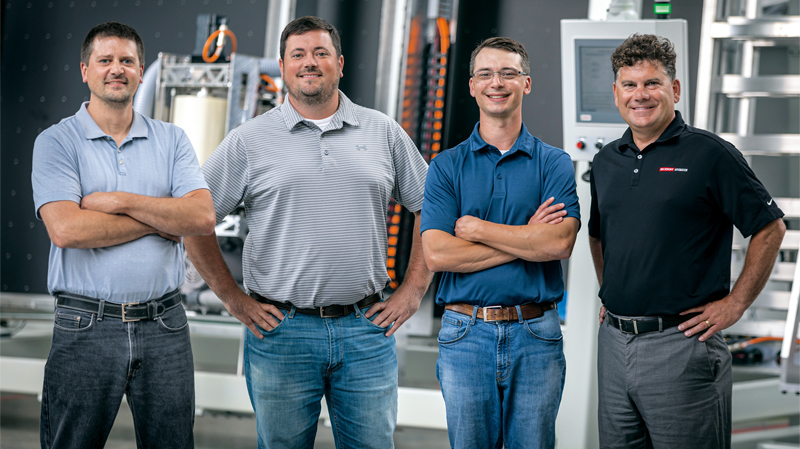
EtherCAT provides the fast, highly deterministic communication necessary for precise measurement and film application. In particular, the EL1252 digital input terminal with eXtreme Fast Control (XFC) technology from Beckhoff offers timestamping with a resolution of 1 ns. EtherCAT also enables the use of TwinSAFE integrated safety technology to implement custom safety logic programmed in TwinCAT 3, which can load directly onto TwinSAFE components, including the EL6900 TwinSAFE Logic Terminal, and other devices.
For control of the 28 axes of motion across the standard machine setup, the system uses the powerful AM8000 series Servomotors and AX5000 series Servo Drives with cost-saving One Cable Technology (OCT) providing control and power. Through the addition of AX5805 TwinSAFE drive option cards, AX5000 drives also implement drive-integrated safety functions such as safe operating stop (SOS), safe stop (SSI, SS2), safe speed (SSR, SLS, SSM), safely limited position (SLP), safe acceleration (SMA, SAR) and rotating direction functions (SDIp, SDIn).
High performance capacity includes options for the future
The PDS IG Equipment window film application system achieves impressive repeatability, flexibility and cycle times. Using the high-speed measurement of EtherCAT XFC terminals, the applicator boasts a cutback precision of +/- 1/8 inch, even across the largest glass units it handles. “When applying this film on a 7- or 8-foot-long window, that consistency is pretty remarkable, especially considering how the film can stretch,” adds Michael Rapp.
While glass dimensions vary from piece to piece, the PDS IG solution roughly doubles what is possible from other systems on the market, according to Rapp. “Our cycle times average 25 to 30 seconds per window, so the throughput for an eight-hour shift is about 1,000 to 1,200 IG units, compared to others in the industry that produce 500 to 600 in that same timeframe,” he says. “However, with flexible and scalable technology, our expandable system could add further modules to increase per-shift throughput to 2,000 IG units — even if each one has a different SKU.”