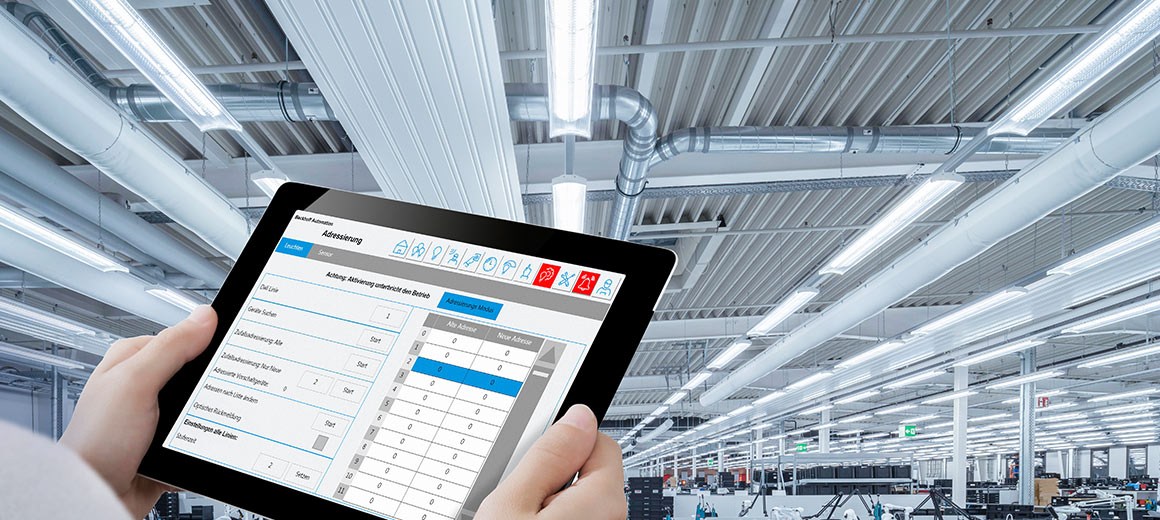
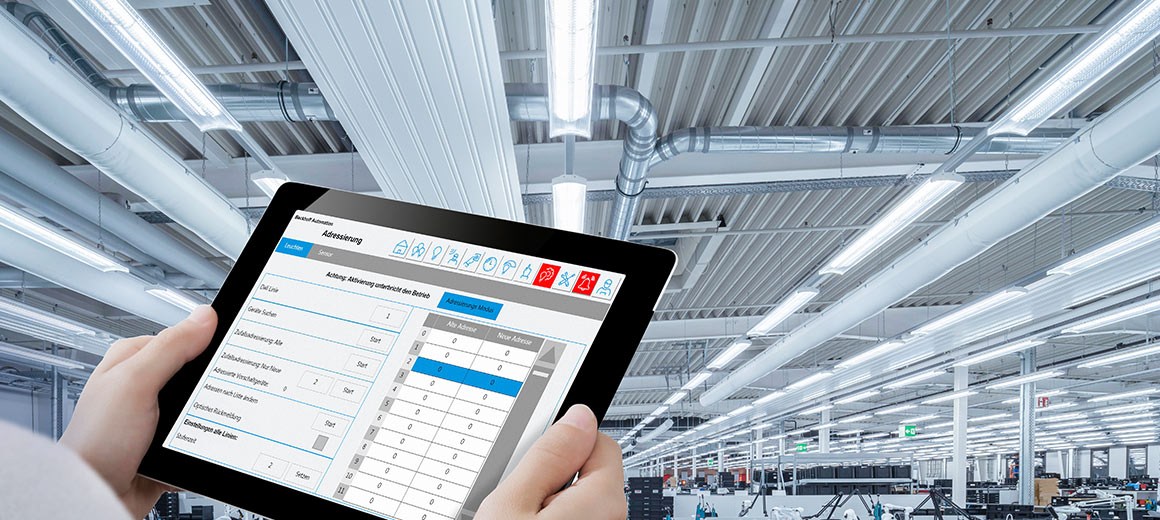
With the TwinCAT 3 Lighting Solution, Beckhoff presents an advanced, intelligent lighting solution for building automation that simplifies all work steps from commissioning to maintenance. It integrates all common lighting controllers and enables an unlimited number of DALI lines. The TF8050 TwinCAT 3 Lighting Solution is fully web/HTML5-capable, decentrally scalable, and can be operated directly via a panel. Quick function changes, addressing, and extensions can be performed immediately during operation, along with DALI line-independent groupings of DALI devices. Even daylight-dependent human-centric lighting concepts can be implemented with the TF8050. The TwinCAT 3 Lighting Solution automatically saves energy by cutting switch-on time for the lighting in presence-dependent environments to a minimum by automatically optimizing the switch-off delay.
New features and extensions from version 2.0.2:
- simplified commissioning mode
- automatic optimization of switch-off delay per group
- lighting controller with intelligent starting value
- Optimized trends and evaluation:
- determination of energy consumption per light
- graph of total energy consumption (day, month, week, year)
- effectiveness report: display of energy, cost, and CO2 savings
- display of the operating hours for all lights in relation to the service life
- daily progression of current presence and group switch-off delays
- EL6821 EtherCAT Terminal integration
- KNX/EIB and EnOcean® integration
- DALI emergency lighting for self-contained lights
Rapid configuration with comprehensive functions: Lighting management with the TwinCAT 3 Lighting Solution
The TF8050 TwinCAT 3 Lighting Solution is a purely configurable software solution. The required hardware is linked to the TF8050 by parameterization. After activating the controller, all necessary settings for lighting control and DALI addressing are executed via the integrated and intuitive visualization interface.
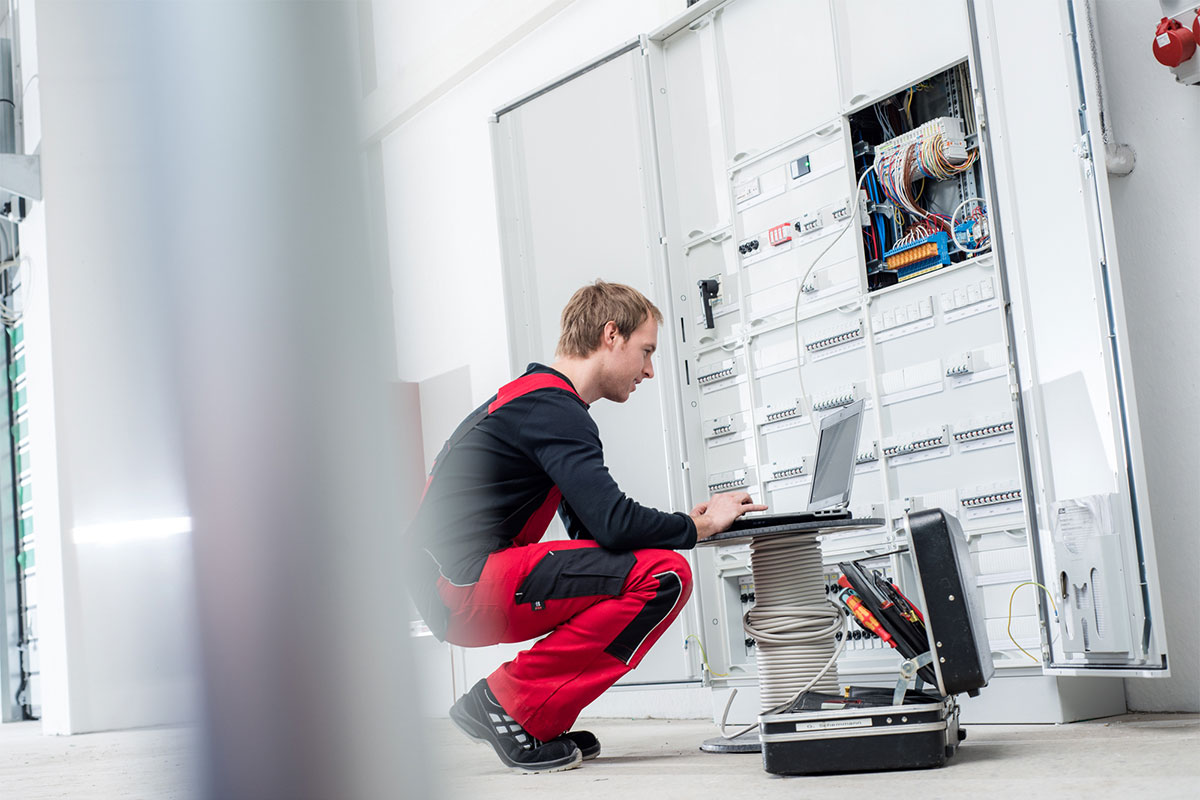
Simple installation
The TwinCAT 3 Lighting Solution can be installed on all Beckhoff Embedded, Panel, or Industrial PCs. The software solution uses the EL6821 or KL6821 DALI-2-certified DALI master terminals as core hardware components. However, other bus terminals can also be used to connect lights and sensors. The number of DALI-2 lines per controller is essentially unlimited. To facilitate the wiring process, decentralized I/O stations can be set up using the BK1150 EtherCAT Bus Coupler or the BK9050 Ethernet Bus Coupler, for example. The TF8050 is also able to meet all project specifications.

Simple commissioning
The TF8050 is a TwinCAT 3 software library that can be operated on all Beckhoff controls. In terms of commissioning, only the project-specific I/Os have to be connected to the TF8050 project, and all necessary light settings and DALI device addressing processes are subsequently performed via the integrated visualization interface. No additional DALI tools or expertise in how to handle these tools is required. What’s more, it's also easy to readdress and extend DALI lines at any time during runtime. Automatic detection of DALI-2 sensor types and automatic addressing of new lights and sensors make commissioning significantly easier. The search function can be used to quickly determine quantities for lights and sensors of all DALI lines. In addition to an overview of all addresses, duplicate addresses are also displayed.
The integrated visualization interface is an excellent tool for quickly configuring the lighting settings and thus for commissioning. All main lighting control functions can be selected individually for each lighting group. The TF8050 supports functions such as human-centric lighting (HCL), daylight control, and constant light regulation, as well as timetables and timers for implementing individual controls. Another major advantage of the TF8050 is that it allows devices from one lighting group to be assigned to different DALI-2 lines, meaning that groupings can span DALI-2 lines and controls can be flexibly implemented.
The configuration option is even faster and more convenient thanks to the use of Excel sheets. The preconfigured light settings can be saved in Excel files and transferred to the controller via FTP or USB. The configuration is activated by loading the Excel files. Subsequent changes can be saved on the controller and copied to a USB stick as a backup, whereby all system settings can also be saved.

Simple adaptation
All lighting control settings can be changed and adjusted during runtime via the integrated visualization interface. What’s more, DALI-2 input devices can be freely configured to control any of the 200 available groups. The DALI-2 control gears can also be assigned to several of these groups, making the TF8050 one of the most flexible lighting solutions on the market. The intuitive visualization interface allows lighting controllers and groups to be adjusted with ease.
On request, some adjustments can also be made with software support. With daylight control, for example, the switch-on value can be optimized automatically and specifically based on the setpoint. You can also use templates to create groups and then make changes to all similar groups with a single click.
Simple operation
When it comes to controlling and monitoring the lighting, the visualization interface integrated into the TF8050 offers a clear and fully comprehensive solution. Buttons for easy access are available on the home page for the main lighting groups, and there are also visualization pages for calling up and configuring scenes for different lighting environments. This allows users to modify and change scene settings with ease. All 50 timetables and calendar functions used to control lighting can be configured as required.
The functionality of DALI devices is constantly monitored, so if there are problems in the DALI line or in the DALI devices, an alarm is displayed with a clear description of the cause of the problem. External alarms can also be configured and visualized with individual texts. The TwinCAT 3 Lighting Solution also supports energy data monitoring with the Beckhoff EL3403 and KL3403 power measurement terminals. All relevant data can be recorded – including current and power for all three phases as well as the sum of these measurements. Energy data is recorded every 15 minutes and stored in a separate CSV file on the controller. The CSV file can be opened in Excel, for example, for further analysis of the energy data.
Even more convenient: with the help of trends and recordings, energy consumption data and savings can be displayed in various evaluations directly on the panels. This ranges from the energy consumption of the individual light to an overview of the entire lighting system. This data can also be evaluated to draw further conclusions about maintenance, energy costs, and CO2 savings, and indicates the operating hours of all lights in relation to their service life.
The TwinCAT 3 Lighting Solution in action
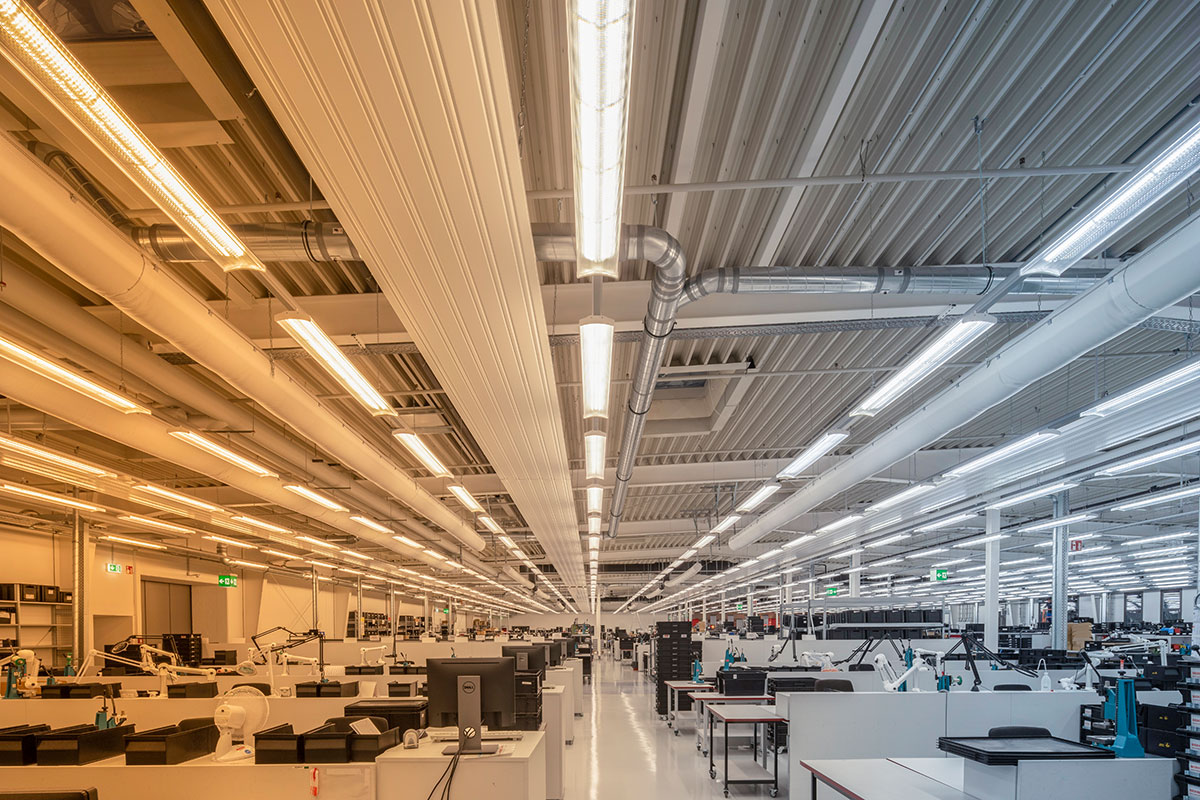
Beckhoff production hall for I/O components
In our production hall for I/O components, all lighting control is performed by the TF8050 Lighting Solution. The TF8050 runs on a CX5020 and controls 874 lights and 88 DALI motion sensors, which are connected via corresponding DALI-2 bus terminals. Installation and commissioning can be implemented quickly and easily thanks to the high compatibility of software and hardware.
The TF8050 provides optimal lighting conditions in the production hall, and different lighting environments can be set at the touch of a button. The TF8050 Lighting Solution also adjusts the color temperature (HCL) in production. The integrated daylight control system enables high energy savings during operation, with the lighting being automatically adjusted for optimum efficiency depending on the position of the sun and the natural incidence of light. In addition to lighting control, a whole host of further functions are also integrated into the control via TwinCAT, such as the control of ventilation, air-conditioning equipment, roof domes, and radiator valves. This enables maximum exploitation of all energy-saving opportunities.
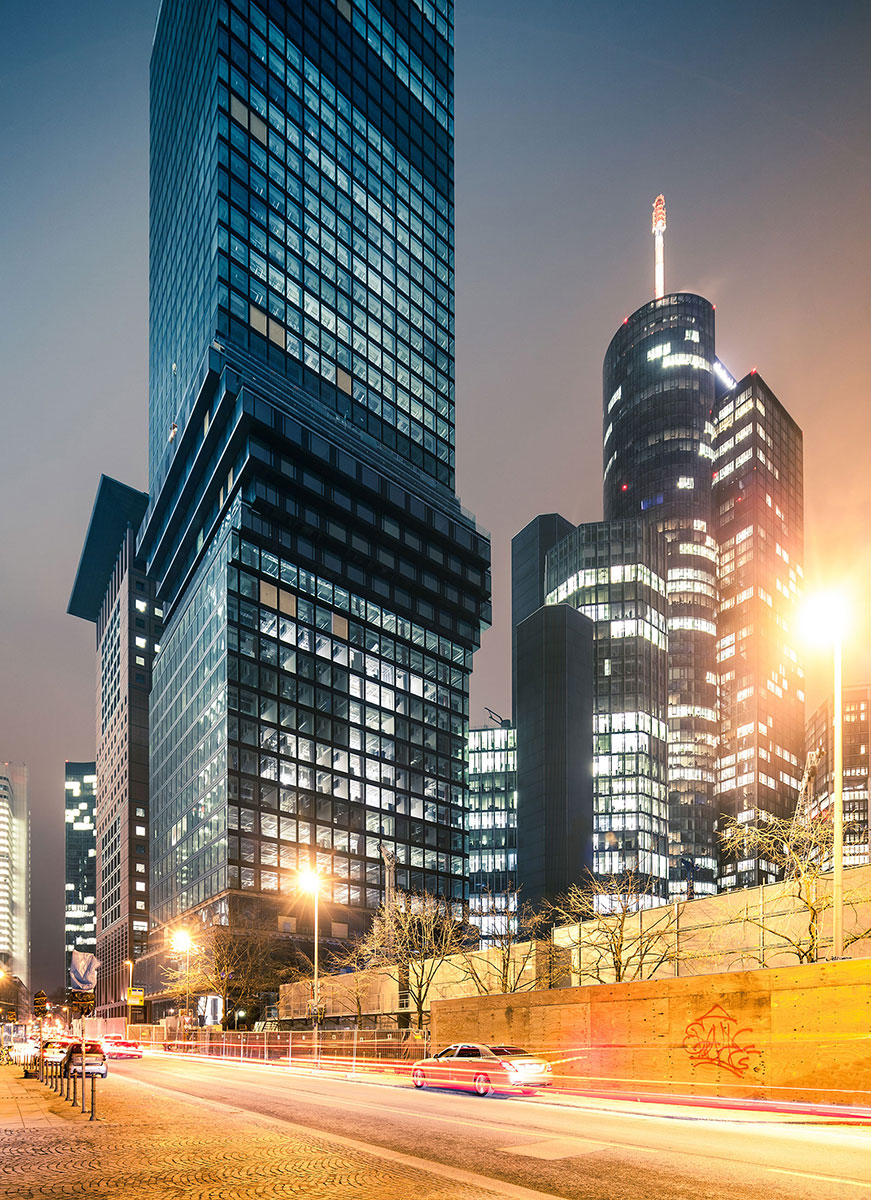
The Omniturm in Frankfurt am Main
The Omniturm in Frankfurt is a literally outstanding project in which the TF8050 TwinCAT 3 Lighting Solution from Beckhoff forms the lighting control system.
Across more than 40 floors, the lighting solution controls some 10,000 LEDs with HCL and collects data from 2,500 sensors with maximum flexibility, since the lighting behavior on each floor can be individually adjusted via the building management system.
However, the automation possibilities go far beyond simply switching the lights on and off: Further options include dimming, presence-dependent switching on and off, daylight-dependent control, and the additional activation of human-centric lighting (HCL). While presence-dependent switching and daylight-dependent control, for example, have great energy-saving potential, human-centric lighting focuses on people. As such, the effect of light – and therefore the lighting settings – are geared to people’s emotional, visual, and biological requirements with the aim of improving the quality of their work and lives.
The sheer size of the building and the various setting options for each floor meant the implementation of this technically demanding lighting control system was no mean feat, but the TF8050 TwinCAT 3 Lighting Solution was able to bring this project to fruition reliably and comprehensively with outstanding results.
Products
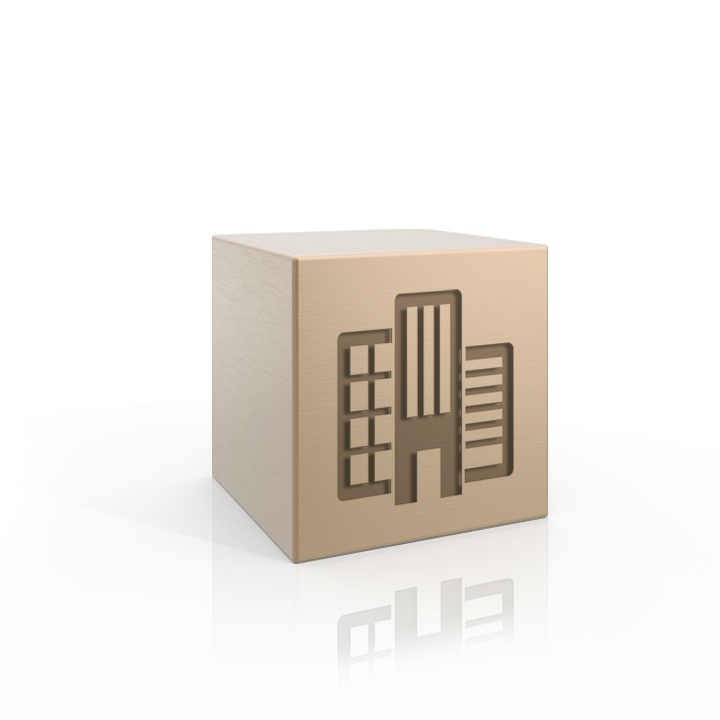
TF8050 | TwinCAT 3 Lighting Solution
The Beckhoff lighting solution offers many benefits that make commissioning simple for DALI light controllers, among other things. Beckhoff bus couplers installed decentrally in the network can be used in extensive lighting systems, which significantly reduces cabling work. The TwinCAT 3 Lighting Solution supports functions such as automatic optimization of switch-off delays, remote control via the web, and importing and exporting Excel data, along with energy measurement and the provision of consumption data. Functions for human-centric lighting (HCL) are included, as well as integration of DALI-2 sensors. All these functions are easy to configure, even without programming expertise.
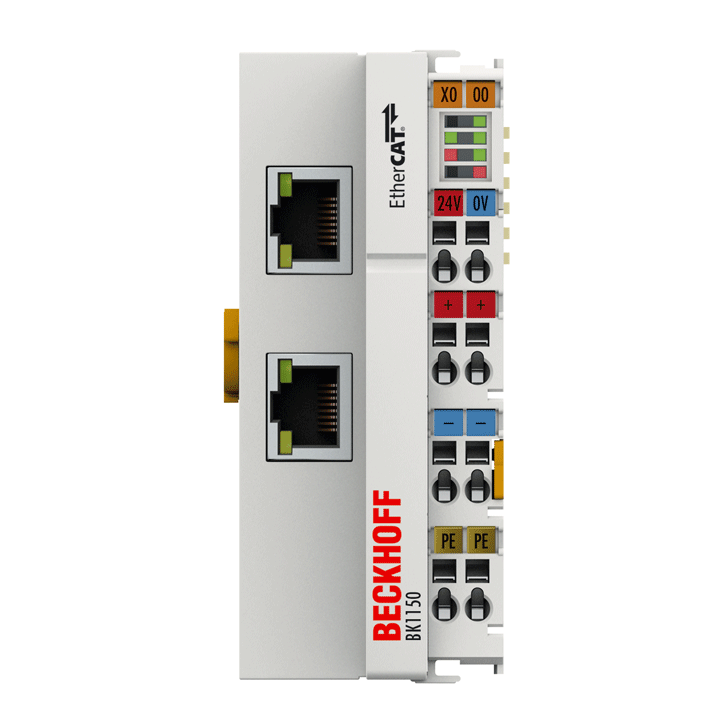
BK1150 | EtherCAT Compact Bus Coupler
The BK1150 EtherCAT Coupler is the link between the EtherCAT protocol at fieldbus level and the Bus Terminals. The coupler converts the passing telegrams from Ethernet 100BASE-TX to the internal, fieldbus-independent terminal bus. A station consists of a coupler and up to 64 Bus Terminals plus a bus end terminal. The process image of the EtherCAT system is assigned automatically. Up to 255 Bus Terminals can be connected via the K-Bus extension.
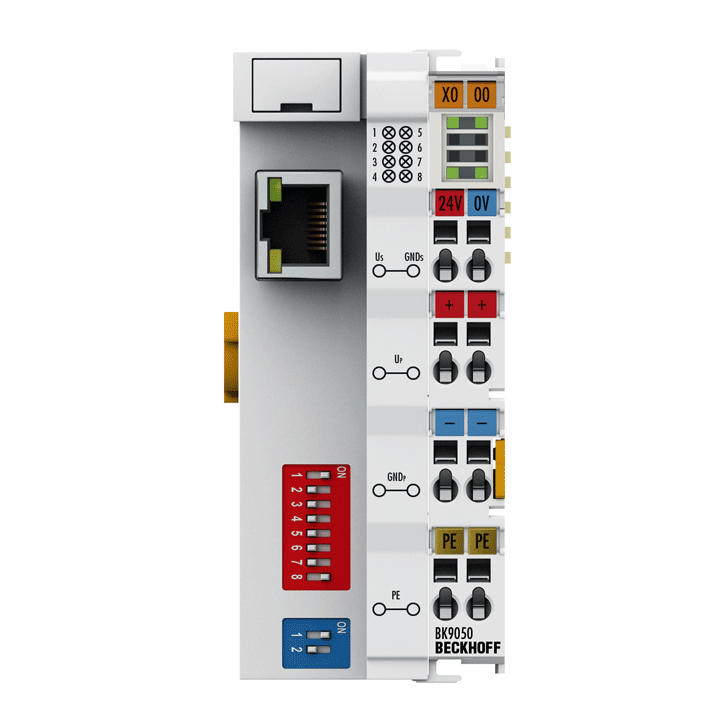
BK9050 | Ethernet TCP/IP Bus Coupler
The BK9050 Compact Bus Coupler with compact housing connects Ethernet with the modular, extendable electronic terminal blocks. One unit consists of one Bus Coupler, any number from 1 to 64 terminals and one end terminal. With the K-bus extension, up to 255 Bus Terminals can be connected.

EL3403 | EtherCAT Terminal, 3-channel analog input, power measurement, 500 V AC, 1 A, 16 bit
The EL3403 EtherCAT Terminal enables the measurement of all relevant electrical data of the supply network. The voltage is measured via the direct connection of L1, L2, L3 and N. The current of the three phases L1, L2 and L3 is fed via simple current transformers. All measured currents and voltages are available as root-mean-square values. In the EL3403 version, the effective power and the energy consumption for each phase are calculated. The root-mean-square value of voltage U, current I and the effective power P, apparent power S, reactive power Q, frequency F and phase shift angle cos φ can be derived. The EL3403 provides a comprehensive network analysis and an energy management option.
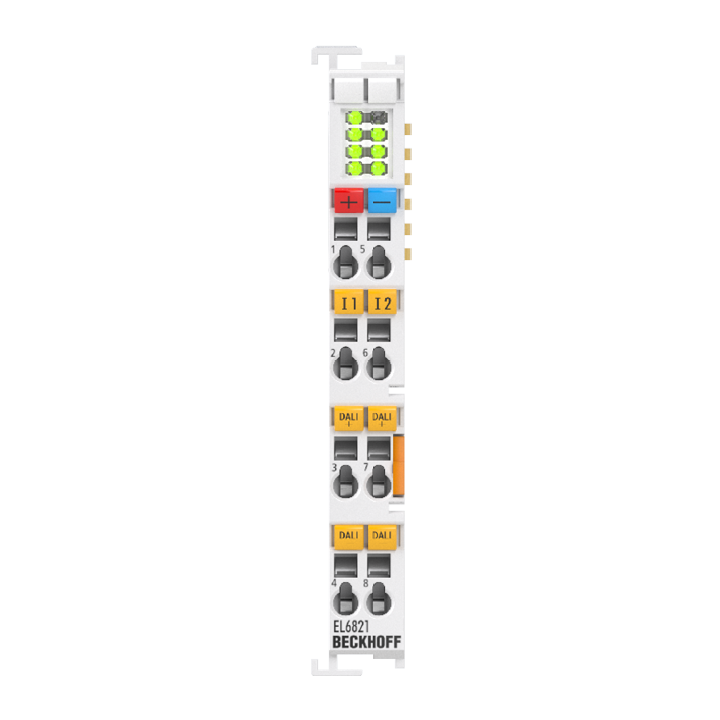
EL6821 | EtherCAT Terminal, 1-channel communication interface, DALI-2, master/power supply
The EL6821 allows up to 64 DALI-/DALI-2 slaves and 64 DALI-2 input devices to be connected. The TwinCAT 3 System Manager makes it easy to configure and parameterize DALI devices. Programming is performed exclusively via TwinCAT 3 function blocks. The EL6821 contains an integrated DALI bus power supply that can be switched off. The galvanically isolated input voltage of 24 V DC must be supplied via the EL9562 power supply terminal or via the PS1111-2402-0002, PS1111-2403-0000, or PS1111-2403-0002 power supplies in order to comply with the certification requirements.
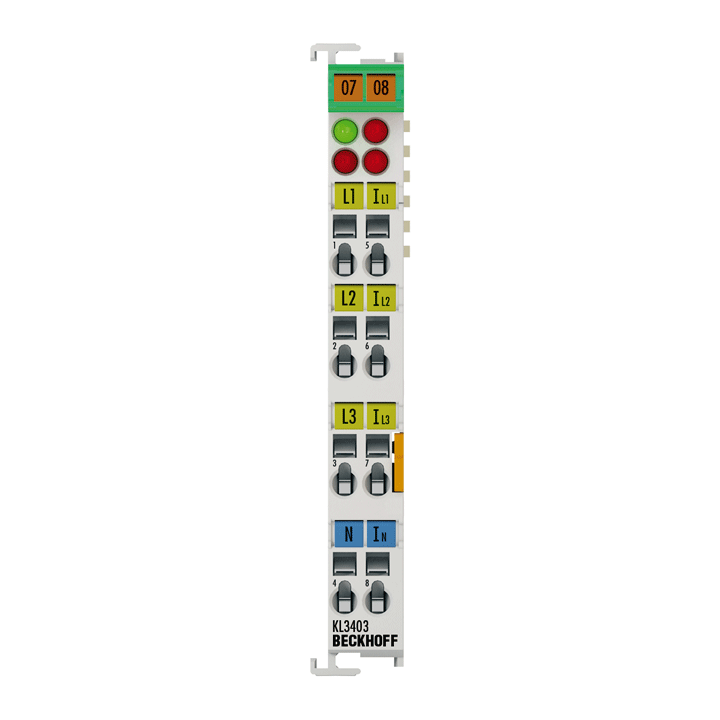
KL3403 | Bus Terminal, 3-channel analog input, power measurement, 500 V AC, 1 A, 16 bit
The KL3403 Bus Terminal enables the measurement of all relevant electrical data of the supply network. The voltage is measured via the direct connection of L1, L2, L3 and N. The current of the three phases L1, L2 and L3 is fed via simple current transformers. All measured currents and voltages are available as root-mean-square values. In the KL3403 version, the effective power and the energy consumption for each phase are calculated. Through the relationship of the root-mean-square values of voltage U * current I and the effective power P, all other information such as the apparent power S or the phase shift angle cos φ can be derived. For each fieldbus, KL3403 provides a comprehensive network analysis and an energy management option.
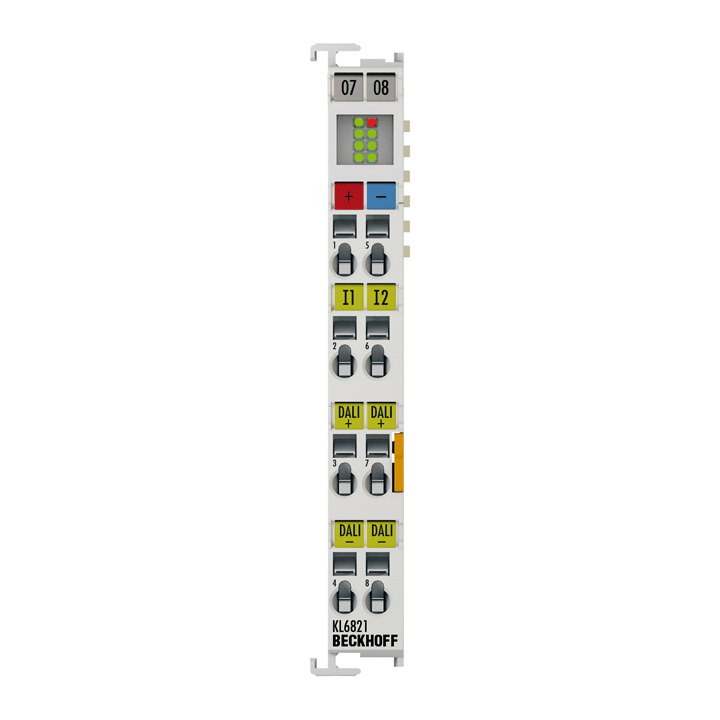
KL6821 | Bus Terminal, 1-channel communication interface, DALI/DALI-2, master/power supply
The KL6821 enables the connection of up to 64 DALI/DALI-2 slaves and 64 DALI-2 input devices. The KS2000 software enables simple configuration via a PC that is directly coupled with the bus coupler via an RS232 interface or via the fieldbus. Operation is done exclusively via TwinCAT function blocks. The KL6821 contains an integrated, switchable DALI bus power supply with galvanically isolated output voltage. No further components are required for the operation of the DALI/DALI-2 devices.
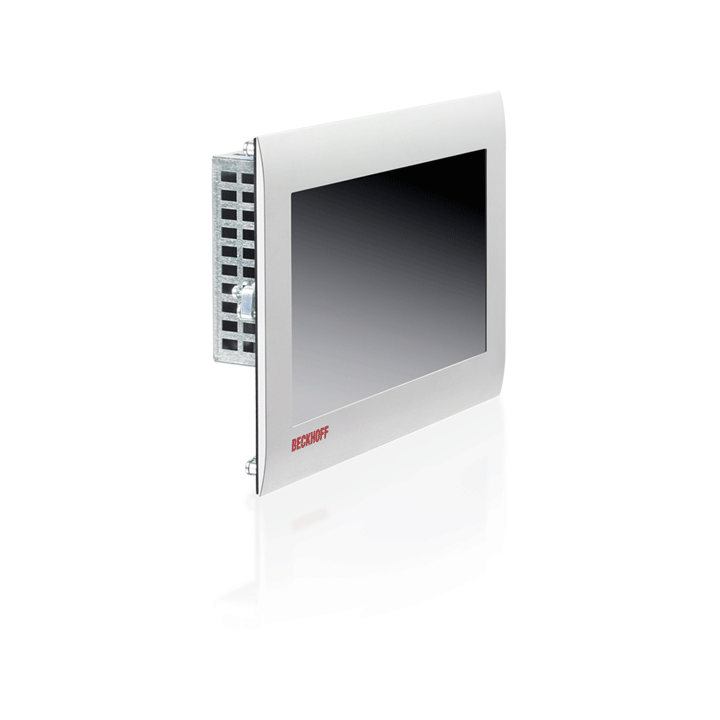
CP6600, CP6606 | Economy built-in Panel PC
The CP6600 and CP6606 built-in Panel PCs are designed for installation in the front of a control cabinet or control housing and can be used for a variety of applications in machine construction and plant engineering – for example, as a stand-alone controller with the TwinCAT automation software running on Windows Embedded Compact 7 or as a remote desktop display. They are available with two different touch screen displays with a 7 or 10.1-inch screen size.
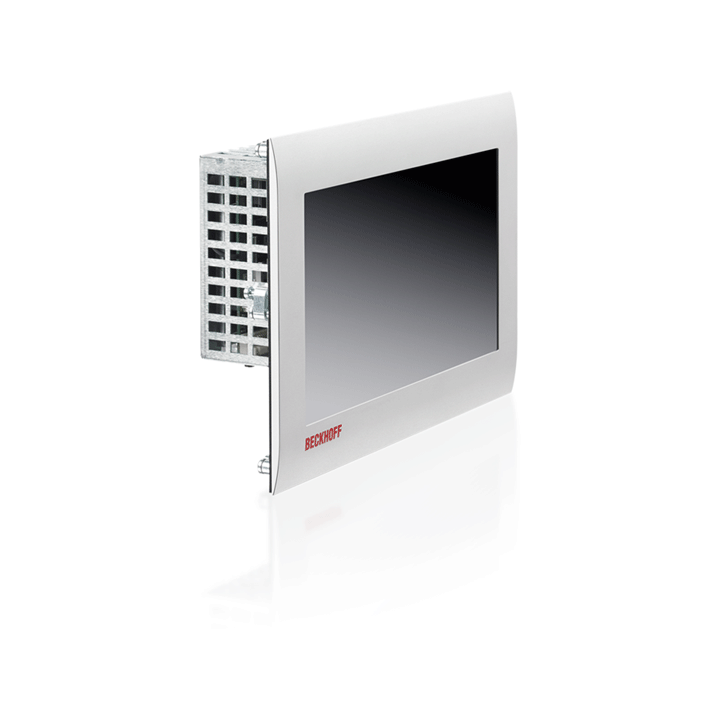
CP6700, CP6706 | Economy built-in Panel PC
The CP6700 and CP6706 built-in Panel PCs are designed for installation in the front of a control cabinet or control housing and, with their highly integrated 3½-inch motherboard, they represent a powerful platform for use in machine construction and plant engineering, for example with the TwinCAT automation software running on Windows 10 IoT Enterprise. They are available with two different touch screen displays with a 7 or 10.1-inch screen size.
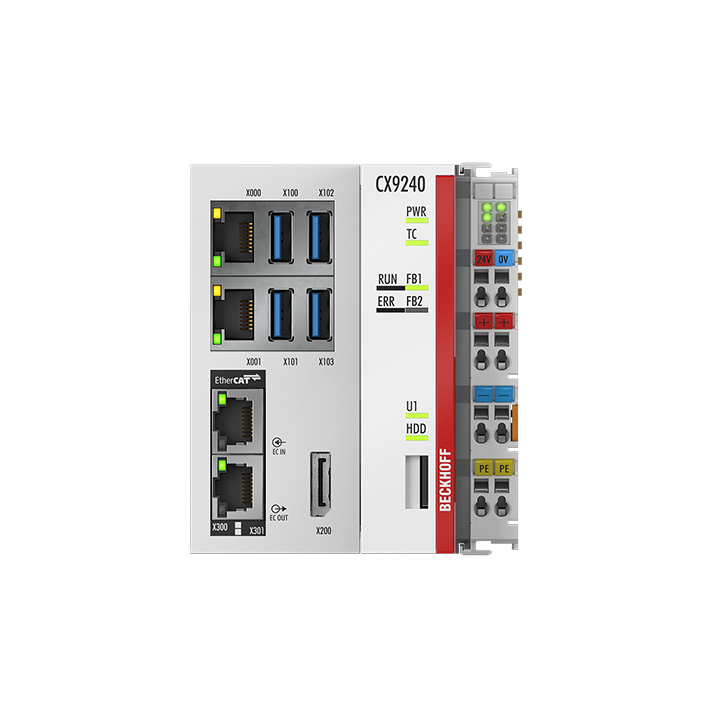
CX9240 | Embedded PC with Arm® Cortex®-A53
The CX9240 Embedded PC is a compact, DIN rail-mountable Ethernet control system with a 1.2 GHz Arm® Cortex®-A53 CPU. It represents a further development of the existing CX9020 and relies on a faster CPU with four cores and a modern 64 bit architecture. The multi-core CPU allows PLC projects to be distributed to several cores for significantly enhanced performance.

CX9020 | Embedded PC with Arm® Cortex®-A8
The CX9020 is a compact, DIN rail-mountable Ethernet control system with 1 GHz Arm® Cortex®-A8 CPU. The connection for the Beckhoff I/O systems is directly integrated into the CPU module. The unit offers automatic bus system identification (E-bus or K-bus) and independently switches in the corresponding mode. The CX9020 comprises the CPU with two microSD card slots, the internal RAM and 128 kB NOVRAM as non-volatile memory. The basic configuration also includes two switched Ethernet RJ45 interfaces, four USB 2.0 interfaces and a DVI-D interface. The RJ45 interfaces are connected to an internal switch and offer a simple option for creating a line topology without the need for additional Ethernet switches. The operating system is Windows Embedded Compact 7. TwinCAT automation software transforms a CX9020 system into a powerful PLC and motion control system that can be operated with or without visualization. Optionally, the unit can be ordered with a fieldbus, serial or audio interface.
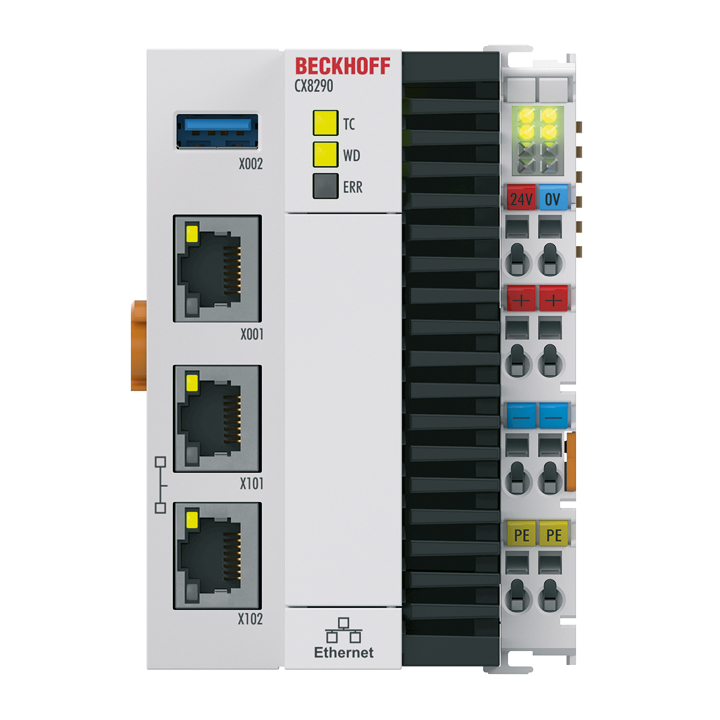
CX8290 | Embedded PC with Arm® Cortex®-A53 and 2-port Ethernet switch
The CX8290 Embedded PC is a controller with a second, switched Ethernet port. Protocols such as real-time Ethernet, ADS UDP/TCP, and EAP (EtherCAT Automation Protocol) are supported, and additional real-time protocols such as PROFINET, EtherNet/IP™, and BACnet/IP can be retrofitted via TwinCAT Functions.
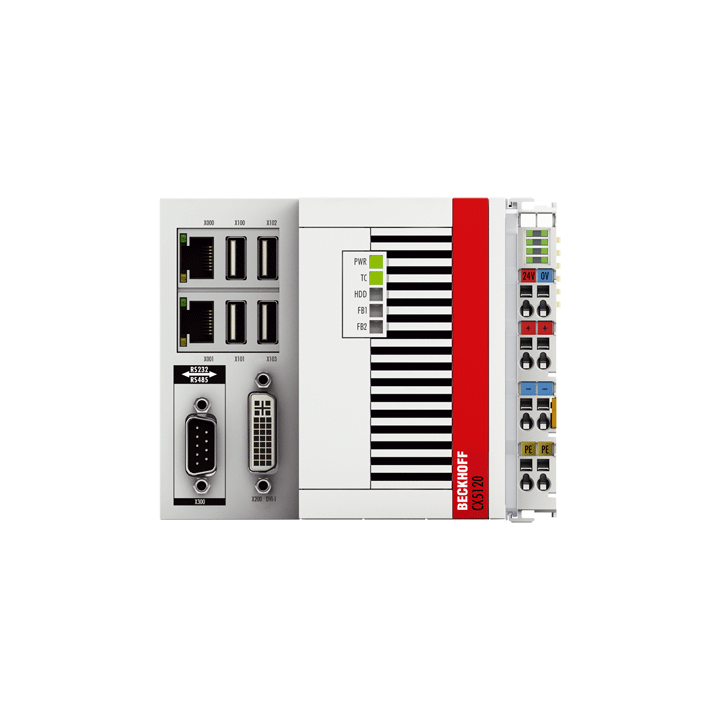
CX5120 | Embedded PC with Intel Atom® E3815
The CX5120 has an Intel Atom® single-core processor with a clock rate of 1.46 GHz. The hardware interfaces in this series are oriented and implemented identically to those of the existing CX5000 series. Two independent, Gigabit-capable Ethernet interfaces as well as four USB 2.0 and a DVI-I interface are available. A multitude of further connection options or gateway functions are created by an optional interface, which can be pre-fitted in the factory, as well as the I/O level, which can selectively consist either of E-bus or K-bus terminals.
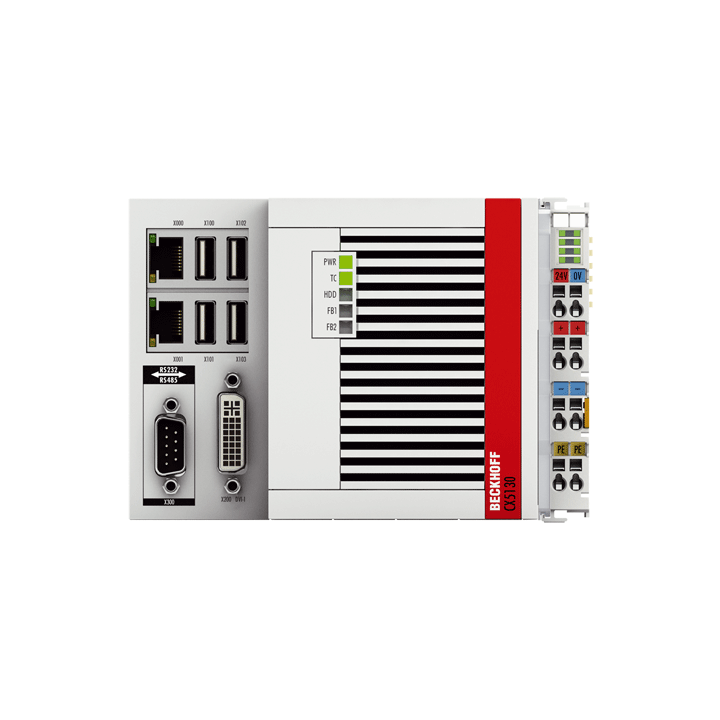
CX5130 | Embedded PC with Intel Atom® E3827
The CX5130 has an Intel Atom® dual-core processor with a clock rate of 1.75 GHz. This makes genuine multi-core technology possible in the Embedded PC segment. The hardware interfaces in this series are oriented and implemented identically to those of the existing CX5000 series. Two independent, Gigabit-capable Ethernet interfaces as well as four USB 2.0 and a DVI-I interface are available. A multitude of further connection options and gateway functions is created by an optional interface, which can be pre-equipped ex factory, as well as the I/O level, which can optionally consist of either E-bus or K-bus terminals.
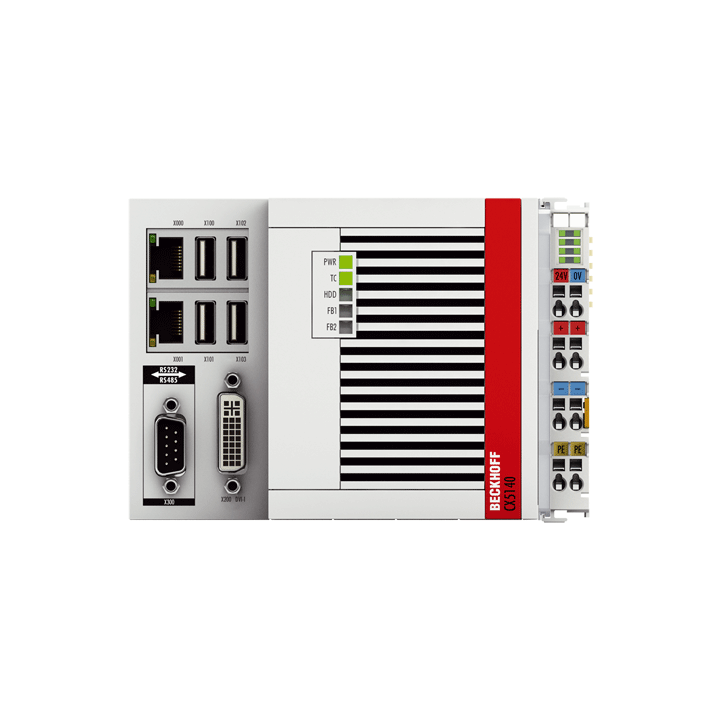
CX5140 | Embedded PC with Intel Atom® E3845
The CX5140 has an Intel Atom® quad-core processor with a clock rate of 1.91 GHz. This makes genuine multi-core technology possible in the Embedded PC segment. The hardware interfaces in this series are oriented and implemented identically to those of the existing CX5000 series. Two independent, Gigabit-capable Ethernet interfaces as well as four USB 2.0 and a DVI-I interface are available. A multitude of further connection options and gateway functions is created by an optional interface, which can be pre-equipped ex factory, as well as the I/O level, which can optionally consist of either E-bus or K-bus terminals.