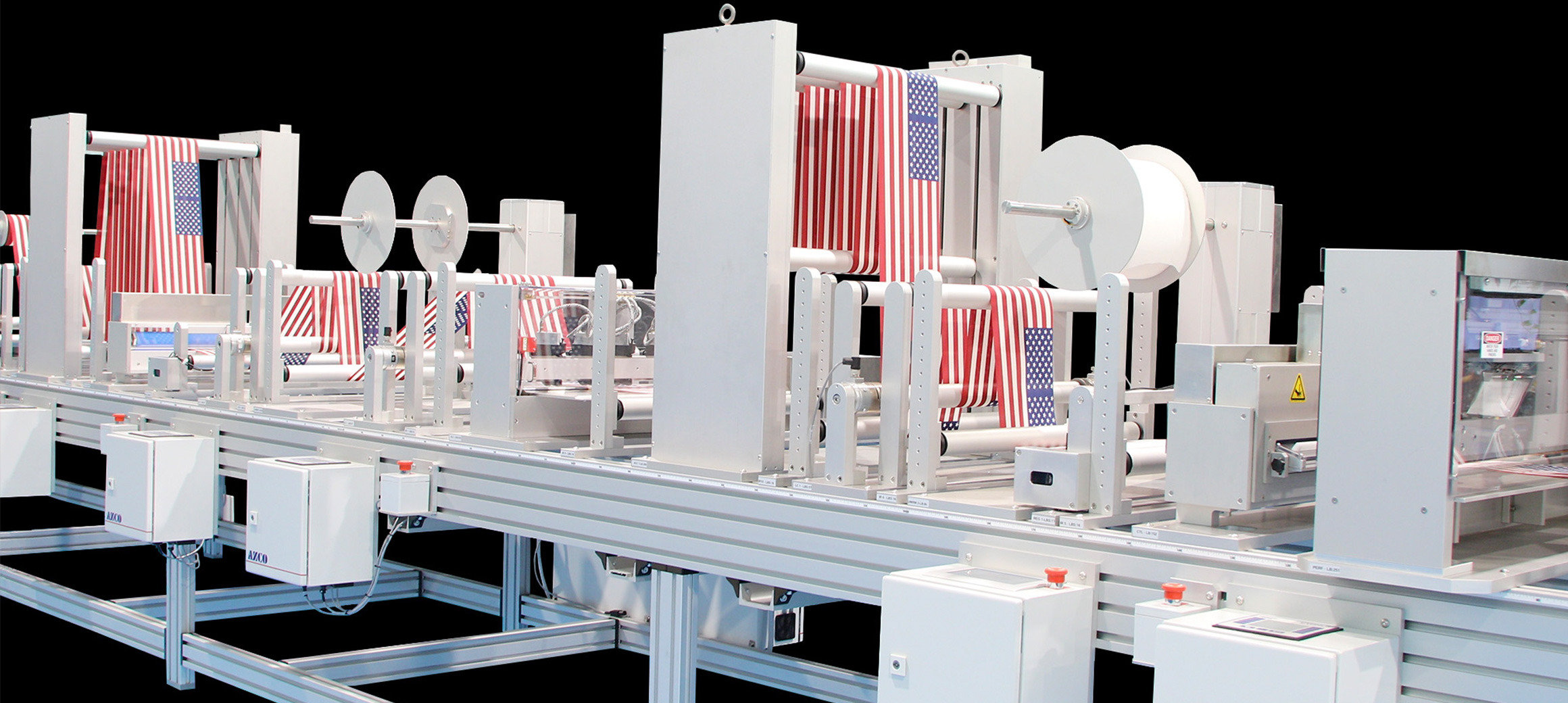
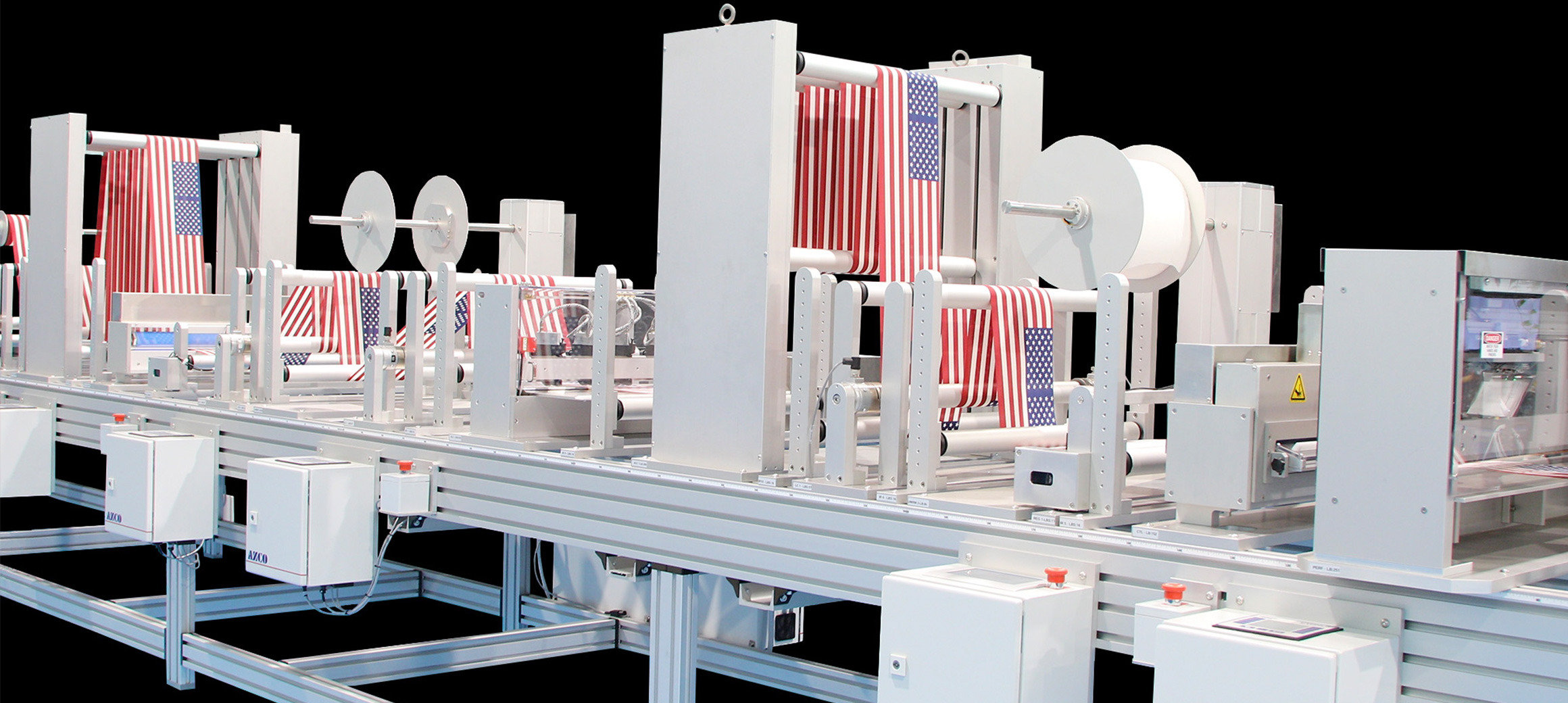
PC-based control optimizes building block system for film and paper converting machines
Implementing a machine and using it to manufacture product samples within hours – machine builder AZCO from Fairfield, New Jersey, shows how this is possible. The combination of machine modules for feeding, cutting and placing flexible materials minimizes engineering effort. An update with the modular and finely scalable control technology from Beckhoff brought AZCO’s Building Blocks of Automation approach to a new level.
Flexibility has been central to AZCO Corporation since its inception. The specialized machine builder serves a range of customers primarily in the U.S. in medical device manufacturing, converting and packaging, as well as machine builders that serve these markets. AZCO carved out a niche in feeding, cutting and placing flexible web materials, offering numerous modules that can be integrated easily into the process. “Our goal is to create standardized products that meet customers’ unique needs, which is a strength of AZCO. Our more recent Building Blocks of Automation machines took this to a new level with an update in control technologies,” Andy Zucaro, founder and president of the company, says.
The Building Blocks of Automation system for film and paper converting machines allows customers to select specific modules that mount on a standardized frame called a Smartframe. Customers only need to connect power, Ethernet and air supply to the modules to begin production. Modules can be removed, added or rearranged to adapt to new products, materials or processes. A recent machine for a large end user included 17 modules: several unwinds for the material, transducers for tension control as roll diameters change, a product accumulator to switch from intermittent to continuous motion for feeding material before cutting it, a slitter and traversing knife, as well as a lamination station. “To provide this much functionality, most companies would have to design a machine from scratch. We simply selected from our standard components and installed them on a Smartframe,” Andy Zucaro explains.
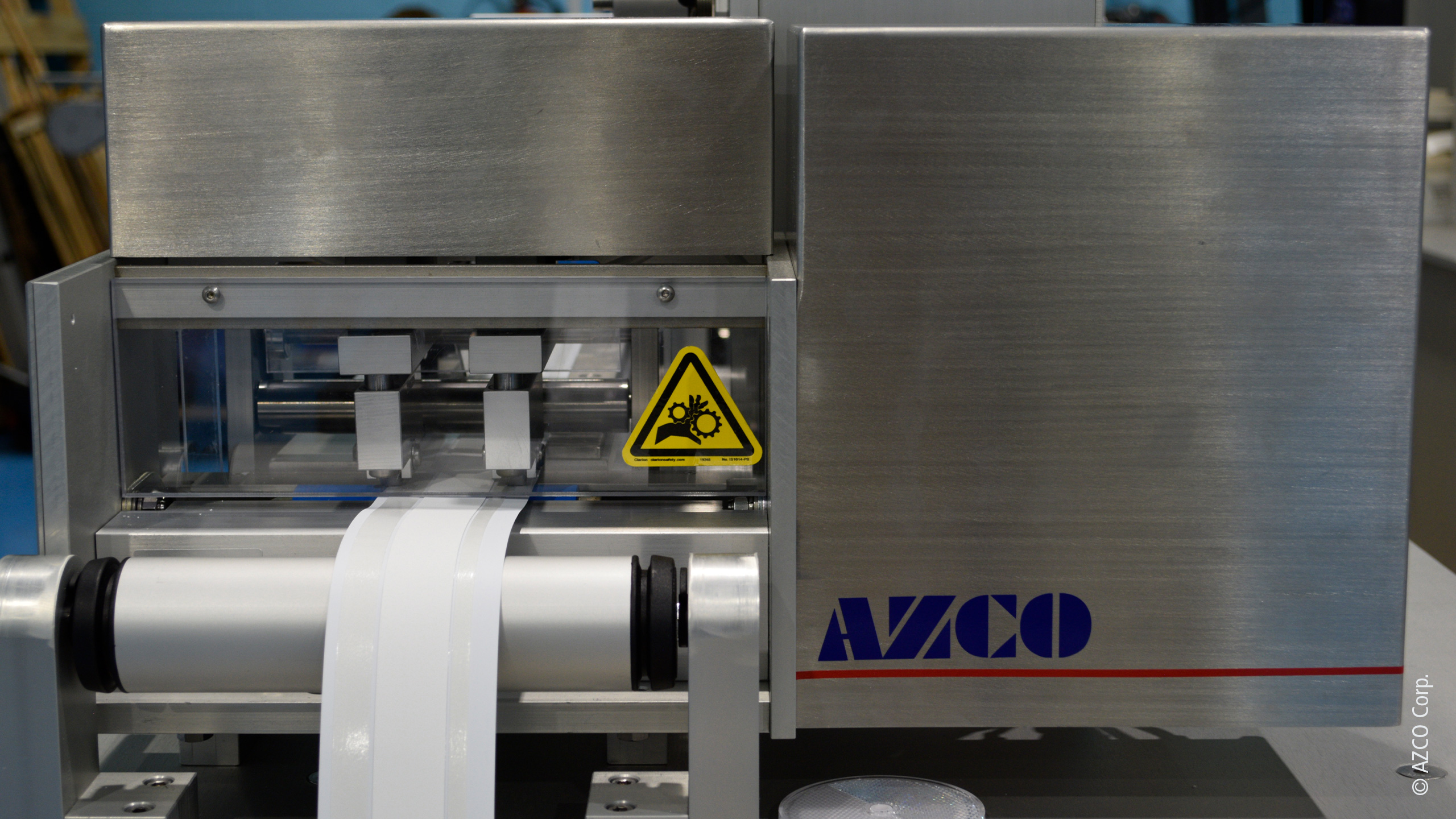
To illustrate the benefits of this outstanding flexibility, Zucaro uses another example: “In fact, one customer visited our office for a meeting and noticed the demo machine that we assembled for trade shows. Using these standard modules on our Smartframe, they were able to produce product samples within just two hours, without even planning to make anything before arriving.”
Flexible and scalable control technology
However, a prerequisite for the Building Blocks of Automation’s inherent flexibility is flexible control technologies. The machines need to be able to connect to existing production lines or other equipment, which means communicating with a wide variety of fieldbuses. In addition, the control components must sit inside a compact enclosure along the Smartframe. “With the Building Blocks of Automation, we preprogram and preconfigure as many pieces as possible, so we don’t have to redesign and retest later,” AZCO Controls Engineer Krunal Padmani says. “We want to develop our programs using function blocks and subroutines assigned to different subassemblies, and operators can easily turn them on or off from the HMI.” However, the company’s legacy PLC and networking technologies struggled to provide adequate capabilities to switch out modules. During this time, Andy Zucaro recalled a PC-based controller from Beckhoff, which he had seen when attending Hannover Messe 2018. “The integrated control philosophy offered a perfect fit for the Building Blocks of Automation with a similarly flexible and modular design,” says Matt Kleven, Applications Engineer for Beckhoff.
The broad I/O portfolio from Beckhoff for the powerful and flexible EtherCAT fieldbus system provides a wide range of networking options. The Hot Connect feature of EtherCAT also helped to make the Building Blocks of Automation concept work; engineers simply plug in any module to a CU1128 EtherCAT hub via standard RJ45 sockets. Hot Connect also allows the remaining modules to continue working when one piece is removed.
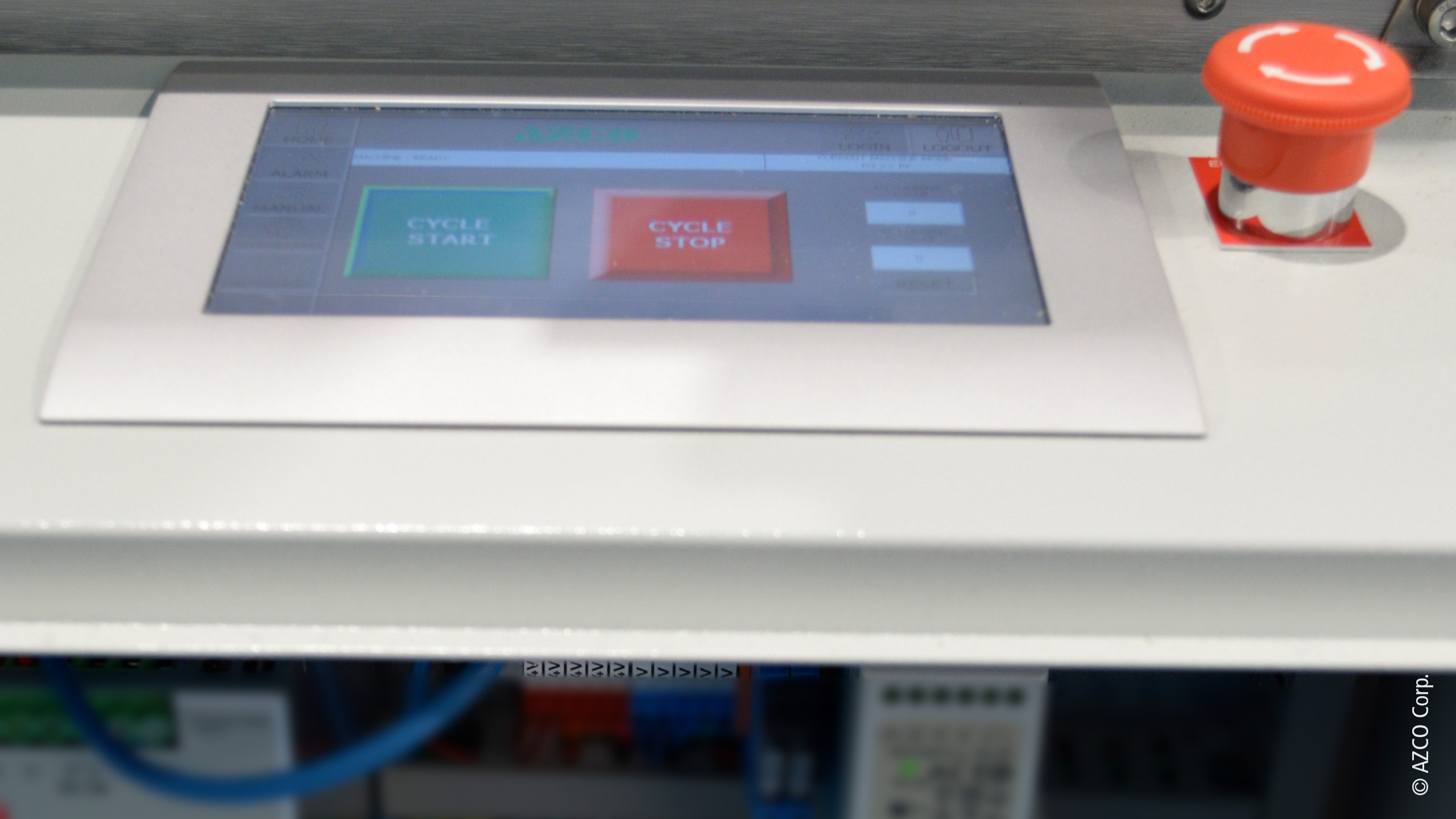
The electrical cabinets feature several EtherCAT components, including EL1859 8-channel digital input terminals and EL2521 1-channel output terminals. “The output terminal supports pulse train functionality up to 24 V DC, which was ideal to operate several third-party DC servomotors,” Krunal Padmani explains. Along with a new implementation of integrated functional safety via TwinSAFE Terminals, AZCO uses the EK1100 EtherCAT Coupler to connect the I/O segments to the machine controller.
For module control, CP6606 Economy Panel PCs are used. These space-saving devices combine a 7-inch touchscreen and ARM Cortex™-A8 processor, a 1 GHz clock speed and 1 GB DDR3 RAM. Each CP6606 is face-mounted to the top of the 18-by-18-inch electrical cabinets, which supports the distributed, modular concept of the Building Blocks of Automation. TwinCAT 3 automation software allows engineers to easily reuse code for each new machine, further modularizing the design.
A clear migration path for the future
“We use the PLC, HMI and motion control functionality in TwinCAT, but we plan to offer customers additional communication options, like OPC UA, MQTT and AMQP, in the future,” Krunal Padmani says. The collaboration between Beckhoff and AZCO has only just begun, according to Matt Kleven: “As customer specifications develop, the flexibility of the Beckhoff system will allow AZCO to expand into areas such as IoT, remote I/O or plug-and-play solutions to add new building blocks.”