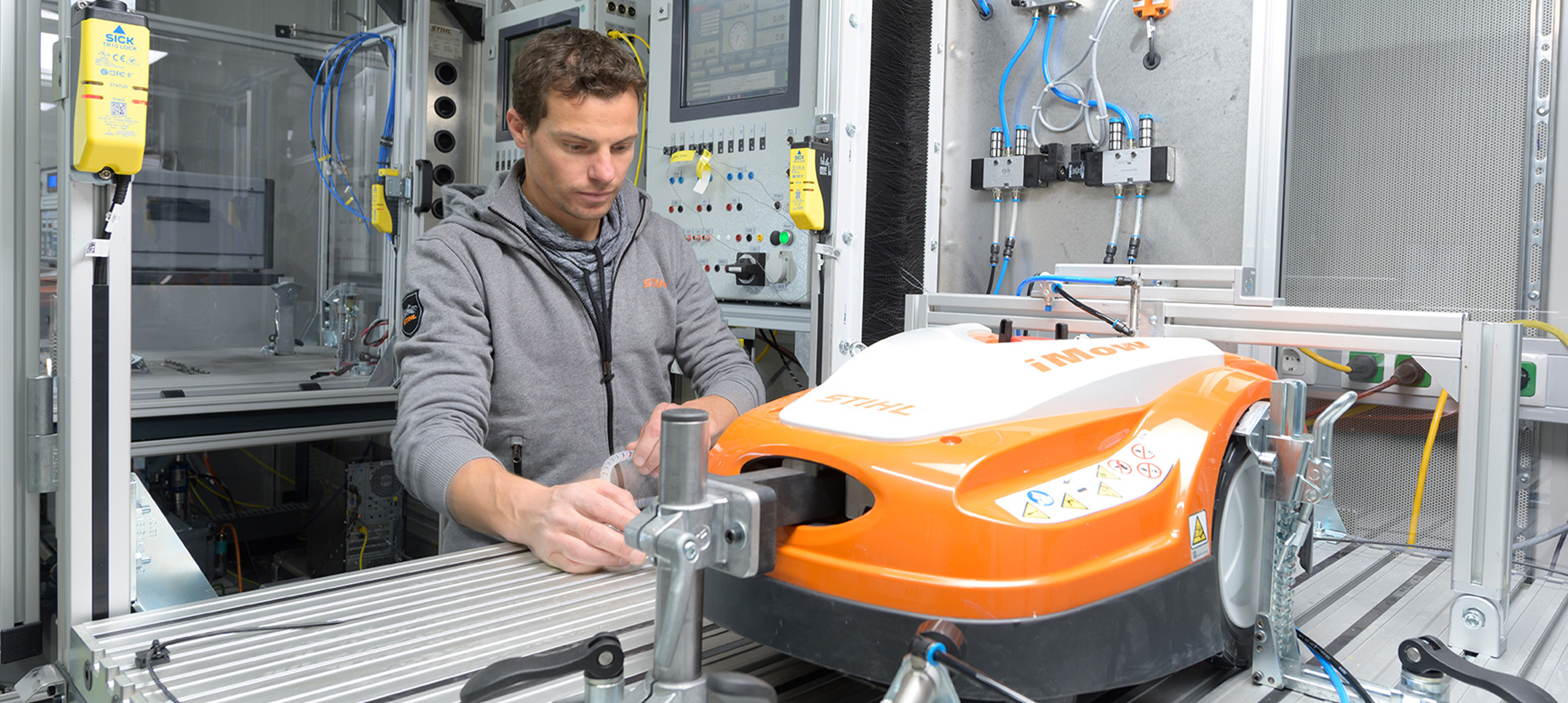
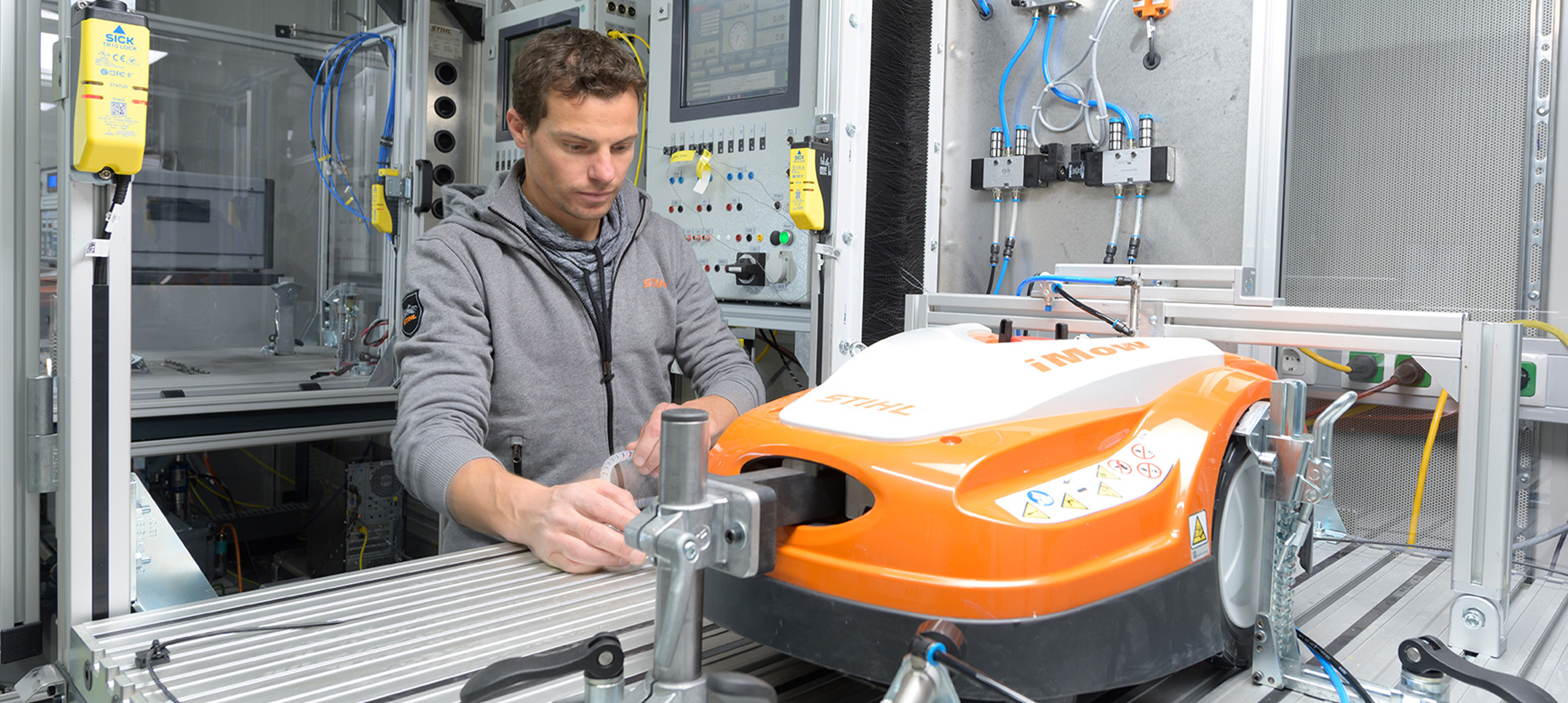
TwinCAT seamlessly integrated with LabVIEW™ for test rig automation at STIHL
Measurement technology specialist measX has developed a flexible, universal automation solution for the heterogeneous endurance testing environment of world-leading power tool manufacturer STIHL. The solution enables the fast implementation of variable, high-quality test plans. Efficient interaction between the Beckhoff TwinCAT automation software and LabVIEW™ plays a crucial role in the success of the solution.
measX GmbH & Co. KG, based in Mönchengladbach, Germany, has been designing and implementing customer-specific measurement, test and evaluation systems for applications in a wide range of industries since 1981. In the field of test rig technology, one of the company’s main focal points is automated development test rigs. ANDREAS STIHL AG & Co. KG (STIHL) commissioned the measurement technology specialist to create a highly efficient automation solution for a large endurance testing facility featuring the EtherCAT and Bus Terminal I/O systems as well as TwinCAT PLC from Beckhoff. The endurance testing automation solution (“Dauerlaufautomatisierung” or DLA in German) was implemented using a combination of LabVIEW™ and TwinCAT software. STIHL is now using the system for endurance testing throughout the company; it was originally developed for the test rigs at the state-of-the-art development center at the company headquarters in Waiblingen near Stuttgart.
At the STIHL development center, prototypes and series products – ranging from power saws and hedge trimmers to cut-off machines and robotic mowers – undergo a great variety of load tests, functional tests and lifetime tests in parallel around the clock in hundreds of test cabins. A detailed test plan is produced for each device type. “The DLA application is designed to ensure reliable, high-performance testing of all types of different equipment with varying configurations. A standardized, intuitive operating concept makes it easy to define, perform and monitor each test session. It is also very simple to switch between different test sequences,” explains Marco Tiskens, the measX engineer responsible for the STIHL project.
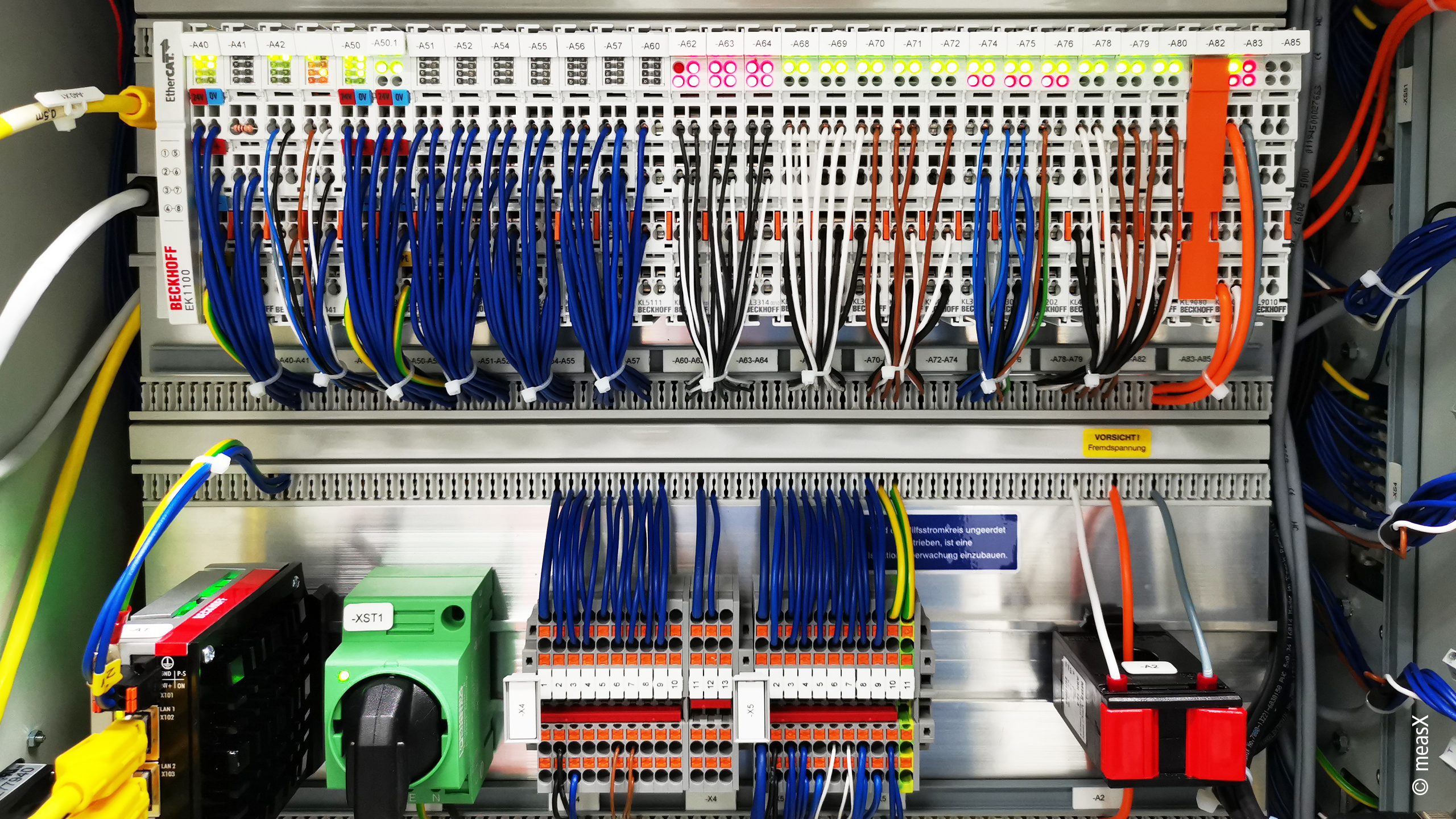
Wide-ranging tests require high flexibility
The test systems are controlled by a C6015 ultra-compact Industrial PC with TwinCAT, which uses an EK1100 EtherCAT Coupler to collect the measurement data acquired by numerous EtherCAT and Bus Terminals in real time. As a universal I/O system, those two terminal systems provide the flexibility required for development test rigs, as Marco Tiskens explains: “There is no need for a separate measurement system and the data can be acquired synchronously with the control outputs without any additional effort. Furthermore, measurement channels can easily be used to alter the test sequence. Additional or alternative terminals can simply be integrated as required. The stability and robustness of the I/O terminals are a particular advantage for endurance testing. And they also offer attractive cost benefits.”
Due to the wide range of test specimens and test types, the test rigs have to meet a great variety of requirements. For example, one piece of equipment might require fuel supply while the next needs water supply and the one after that power supply. The EL3314-0002 EtherCAT Terminal, which features electrically isolated channels, demonstrates its advantages when it comes to precise, fault-free temperature measurement with thermocouples. For most test runs, speed is another important measurement variable – with EtherCAT Terminals from the EL5xxx series, it can be captured within the same system and, therefore, synchronously with all other variables. In addition, energy measurement terminals provide important data about the power consumption of the test specimen.
Different parameters need to be measured and controlled or regulated on all test specimens. However, as one of the objectives it should also be possible to carry out the same test on a different test rig or even in a different location, despite the different hardware used in each case. This is achieved by defining the measurement technology and channels as well as the test sequence separately and only bringing them together to form a test program at the start of each measurement run as required for the task in question.
Seamless integration of measurement and control technology
For every endurance test, the channels to be measured and all necessary test parameters are defined precisely in the STIHL test database. The relevant measurement and sequential program is generated automatically and in a generic form suitable for the TwinCAT environment in the DLA via a LabVIEW™ framework. It is then compiled, and only when the process is complete is it transferred to the PLC. No in-depth knowledge of TwinCAT is required to implement test sequences. The actual sequence is created once for every test type in Sequential Function Chart (SFC) programming and then reused with new parameters each time. This results in an entire library of templates for test sequences.
The DLA application “translates” the test specification from the test database via multiple abstraction levels for TwinCAT, ensuring that the correct I/O configurations and variables are automatically defined. The test rig-specific assignment of variables to I/O terminals is also carried out automatically. The DLA software activates the control program, monitors execution during the test sequence and records all parameters and measured values. “We control Microsoft Visual Studio® remotely with the TwinCAT environment from within LabVIEW™ in order to generate PLC source code and then compile and execute this source code. We use programs to do everything that the users would otherwise have to do by themselves,” says Marco Tiskens, describing the special software concept.
Automation Interface as the linchpin
Configuring and creating the measurement and control programs from within the DLA is only possible with the TwinCAT Automation Interface. This open interface for automatic code generation supports complex applications such as the DLA, which uses predefined templates for configuration. “The reuse of tested program sections and the automated compilation of the different sections to form test-specific sequential software applications save time and minimize errors. This method also helps to standardize the tests, making it easier to compare them,” says Marco Tiskens.
All test rigs can be operated and monitored via the same graphical user interface. The necessary values are read out from TwinCAT or set via ADS. The spectrum ranges from setting an individual variable – for example, in order to switch on the media supply or start the test sequence – to reading out well over 100 measurement channels. The latter is carried out via multiple ring buffers that are generated dynamically when the program starts and temporarily store the data for up to 12 s.
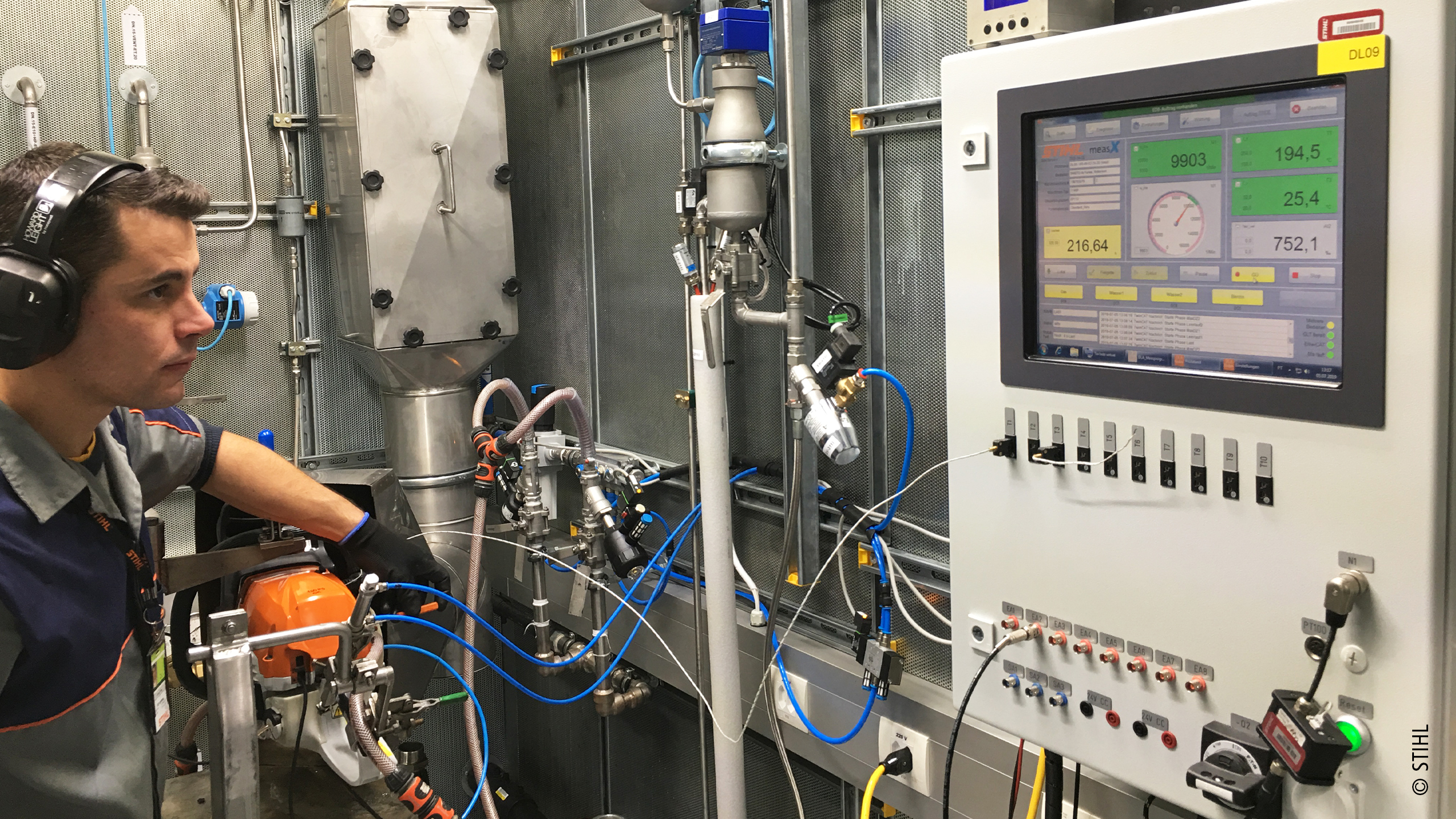
The DLA application offers a wide range of visualization and monitoring functions. PCs integrated into the network can be used to monitor entire test rig groups via the DLA Viewer or to operate individual systems. The dashboard provides an overview of all configured test rigs and their operating states. In the detailed view, display elements and color codes provide information about the current channels and characteristic values of individual test rigs during the measurement process. In addition, a graph visualizes the measured data since the start of the test, which can provide an early indication of the results to be expected.
The DLA saves the data files provided by TwinCAT during testing to the test rig computer and transfers them to a central file server at configurable intervals or when the files reach a certain size. The data packets are automatically consolidated and are immediately available for further offline evaluation. Important formulas and parameters are calculated while the data is still being prepared, and PDF reports with basic evaluations are generated.
Ready for new requirements
The DLA is currently being used successfully for endurance testing in STIHL test centers in Germany, Austria, China, the USA and Brazil. The same software runs on all test rigs regardless of the hardware employed. Marco Tiskens continues: “The high-performance Beckhoff components and friendly collaboration with STIHL and Beckhoff have resulted in this highly efficient test rig automation solution with virtually unlimited scalability. For us, the solution offers exemplary reliability, performance, flexibility and standardization. It enables rapid adaptation to future test specimens and tests and it speeds up the process from the formulation of a test to evaluation of the results. Measurement data and basic evaluations are made available to test departments quickly.” This is confirmed by Alexander Klein, Team Leader Endurance Testing at STIHL: “With the DLA tool from measX, we here at STIHL are able to develop and ensure the safety of equipment quickly, efficiently and reliably within our global network in order to make sure our customers are satisfied.”
Future-proof: Precise EtherCAT measurement technology and LabVIEW™
Flexible test rig automation is essential for accommodating the wide range of different test requirements. In cases like this, it is worth establishing partnerships with experienced system integrators such as measX, who have a wealth of expertise to draw on. The results of this close collaboration are high-performance, future-proof test rigs that can be quickly adapted to new products and technologies. With the new TwinCAT 3 Interface for LabVIEW™ (TF3710), Beckhoff has simplified the connection of the control level to the LabVIEW™ application. The Interface provides VIs that have been developed for high-performance reading and writing of ADS symbols and for configuring I/O terminals. Together with the ultra-precise EtherCAT measurement terminals from the ELM series, Beckhoff provides all of the tools needed to implement high-performance test rig applications. “Our customers working in the field of test rig construction particularly appreciate the wide selection of I/O terminals: From the simple 12-bit voltage measurement terminal to the highly precise, calibrated 24-bit multi-functional terminal with LEMO connector, our range provides the right terminal to ensure projects can be implemented cost-effectively. Beckhoff offers suitable EtherCAT Terminals for all key measurement variables, from standard signals to temperatures, speeds, vibrations, torques and shifts. Furthermore, all measurement data is perfectly synchronized via EtherCAT and provides comprehensive diagnostic information – something that is vital for ensuring reliable test rig operation,” adds Christian Lindemann, sales specialist for measurement, analytics and control from the I/O product management team at Beckhoff.