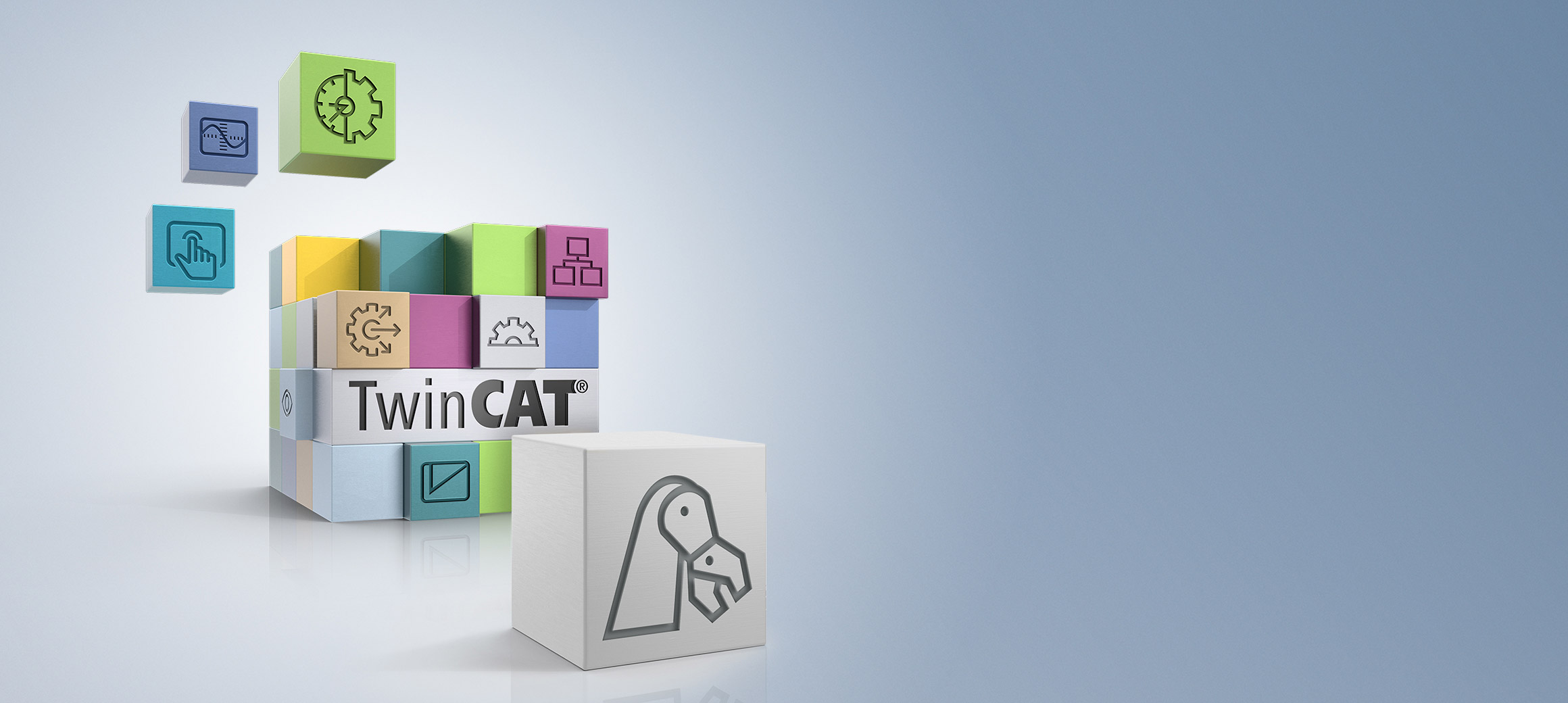
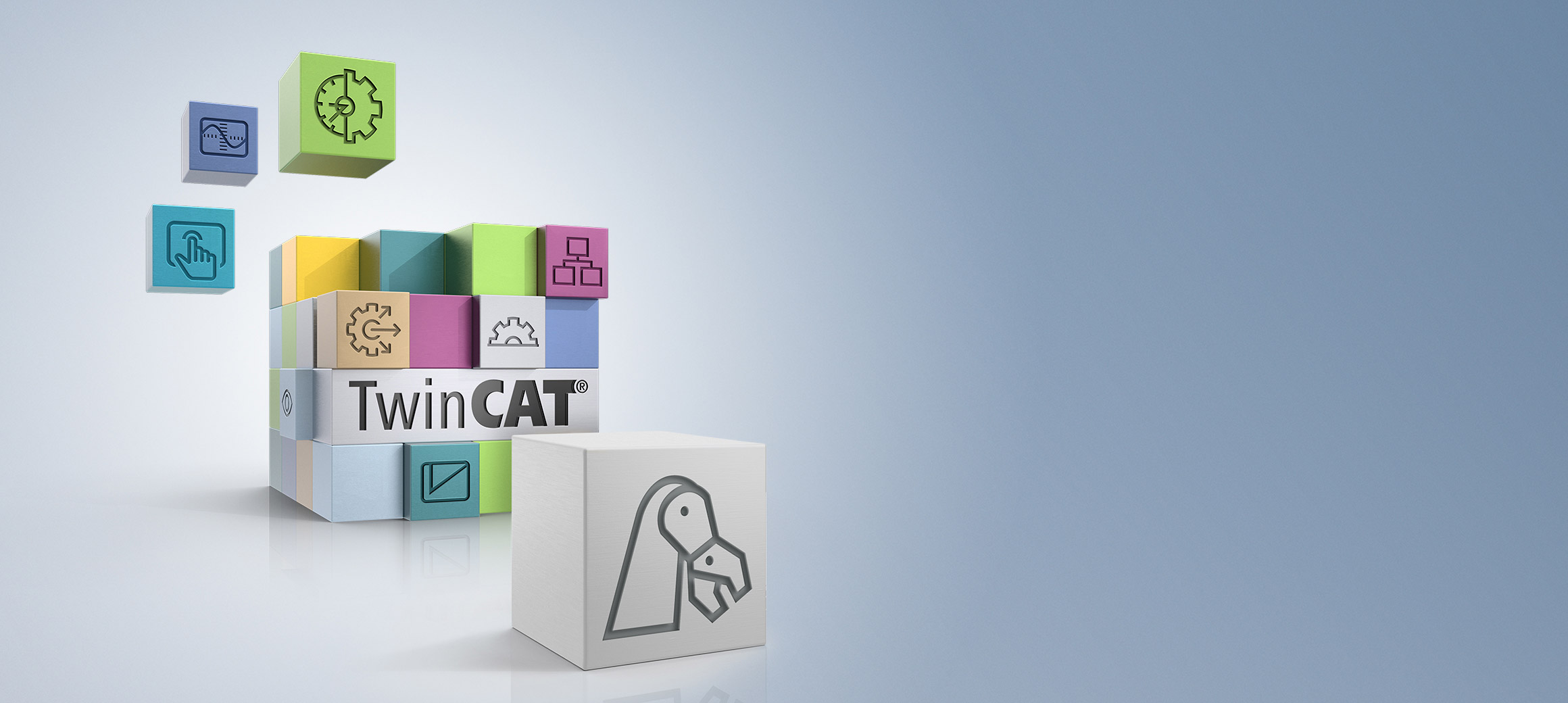
TwinCAT 3 Kinematic Transformation
TwinCAT maximizes performance and system accuracy
TwinCAT Kinematic Transformation integrates robot control into standard automation software, so that PLC, motion control and robotics functions can be executed on a single Industrial PC. 6-axis kinematics are also available in addition to Cartesian gantry, various 2D parallel kinematics and 3D Delta kinematics. The desired kinematics can be conveniently selected and parameterized in the TwinCAT System Manager. The kinematic channel is used to parameterize the robot type (e.g. delta or SCARA) as well as the bar lengths and offsets. Values for mass and mass inertia can be specified for dynamic pre-control. In addition, this TwinCAT software library includes tracking functionalities for synchronizing a robot with a moving object, so it can pick up workpieces from conveyor belts or inclined turntables, for example.
Using TwinCAT Kinematic Transformation, various parallel and serial kinematics such as those used for pick-and-place tasks can be realized simply and cost-effectively. The robot acts as an EtherCAT Slave and the communication with the Beckhoff controller is based on EtherCAT, a global standard in the robotics industry. The seamless integration of robot kinematics into the control system not only avoids the need for an additional robot CPU, it also ensures optimized interaction and synchronization with the PLC and existing motion control functions: direct interfaces replace the complexities and inefficiencies of communicating between different controllers and systems. This results in much higher performance and improved system accuracy.
Products
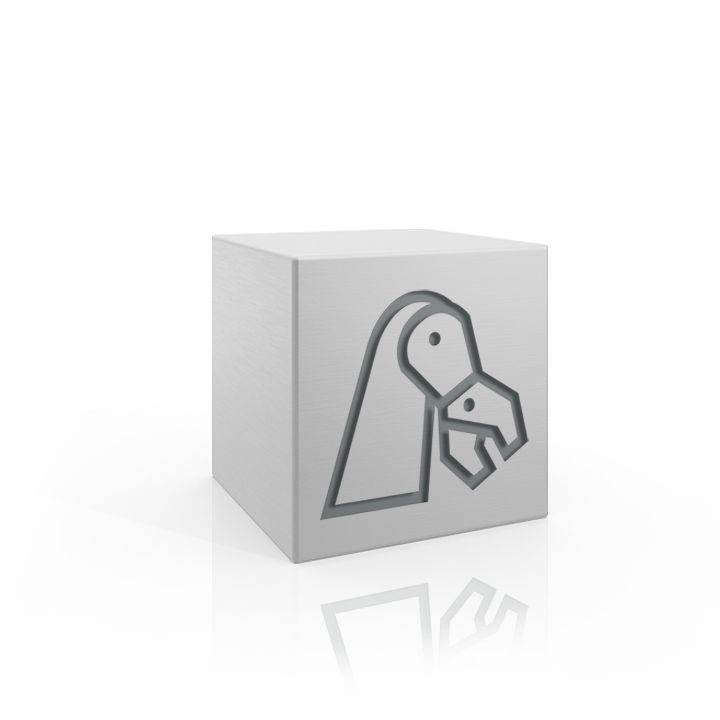
TF5110 | TwinCAT 3 Kinematic Transformation L1
Various robot types kinematics can be realized using TwinCAT Kinematic Transformation. The programming of the robot movements takes place in Cartesian coordinates using either DIN 66025 instructions or the PLCopen-compliant blocks from the PLC. An integrated dynamic pre-control ensures high precision of the movement even at high accelerations and speeds. Configuration takes place in TwinCAT 3 Engineering.
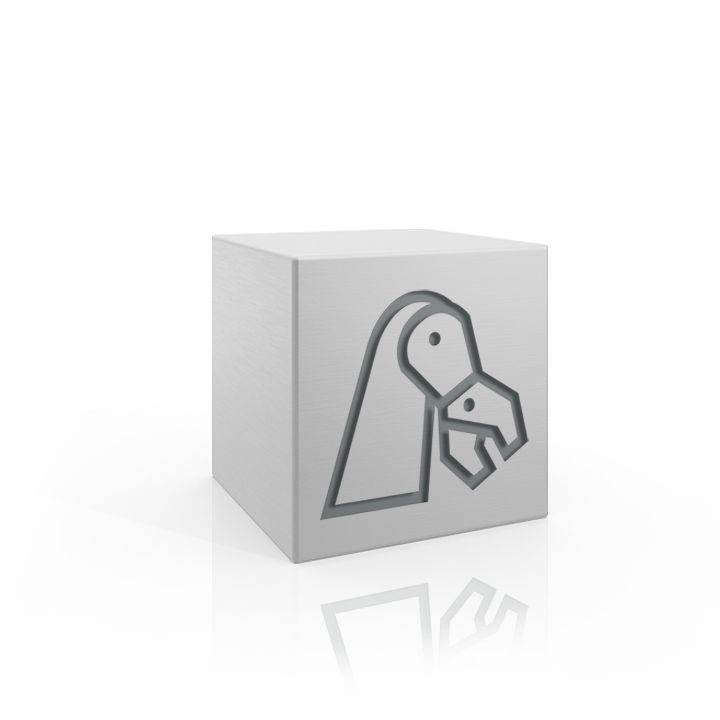
TF5111 | TwinCAT 3 Kinematic Transformation L2
Extension of the TwinCAT Kinematic Transformation L1 with additional kinematics:
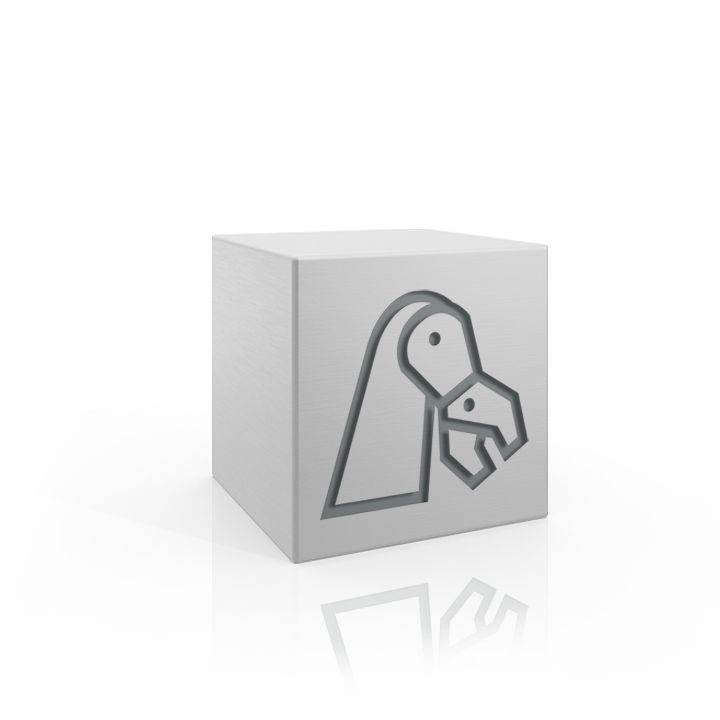
TF5112 | TwinCAT 3 Kinematic Transformation L3
Extension of the TwinCAT Kinematic Transformation L1/L2 with additional kinematics:
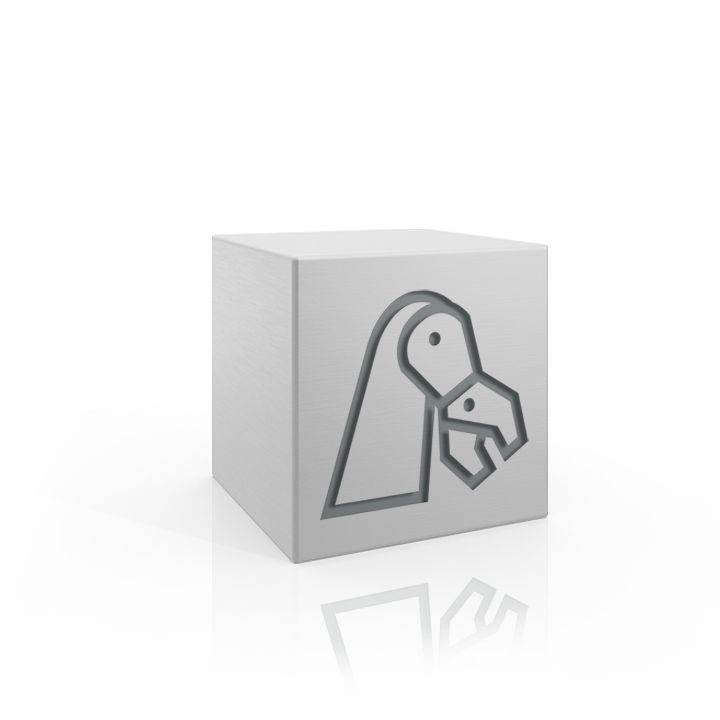
TF5113 | TwinCAT 3 Kinematic Transformation L4
Extension of the TwinCAT Kinematic Transformation L1/L2/L3 with additional kinematics:
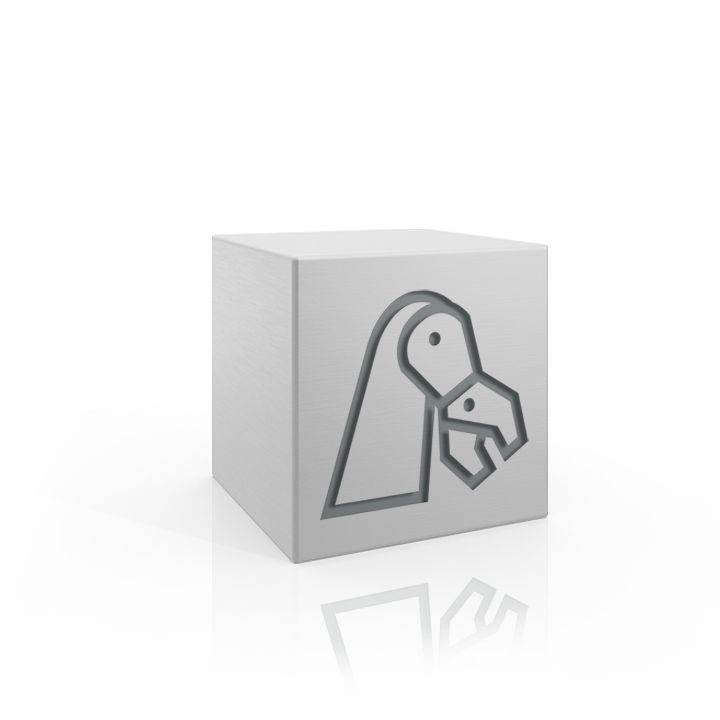
TF5120 | TwinCAT 3 Robotics mxAutomation
TwinCAT 3 Robotics mxAutomation allows direct communication between the PLC and a KUKA robot control via a common interface. The robot movements can be programmed directly in the PLC, and the actual values of the robot can be synchronized in real time. TwinCAT 3 Robotics mxAutomation combines PLC control and robot on a single platform and enables programming from an existing system without knowledge of a specific robot programming language.
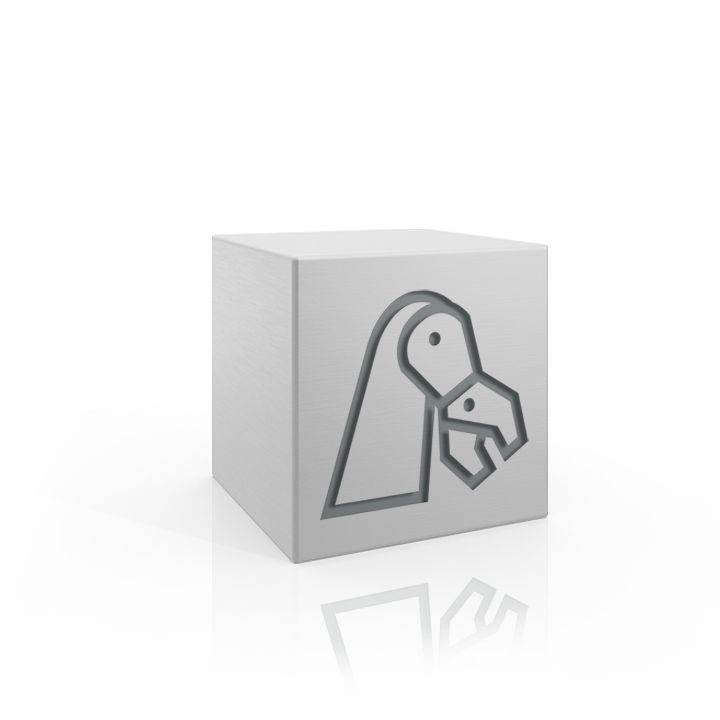
TF5130 | TwinCAT 3 Robotics uniVAL PLC
The TwinCAT 3 Robotics uniVAL PLC allows direct communication between the PLC and the robotics controller from Stäubli via a common interface. The robot's movements can be programmed directly in the PLC and compared with the robot's actual values in real-time. The TwinCAT 3 Robotics uniVAL PLC combines PLC control and robotics on a single platform and enables programming from a single system without having to know a special robot programming language.