Implementing Ethernet-APL with Beckhoff
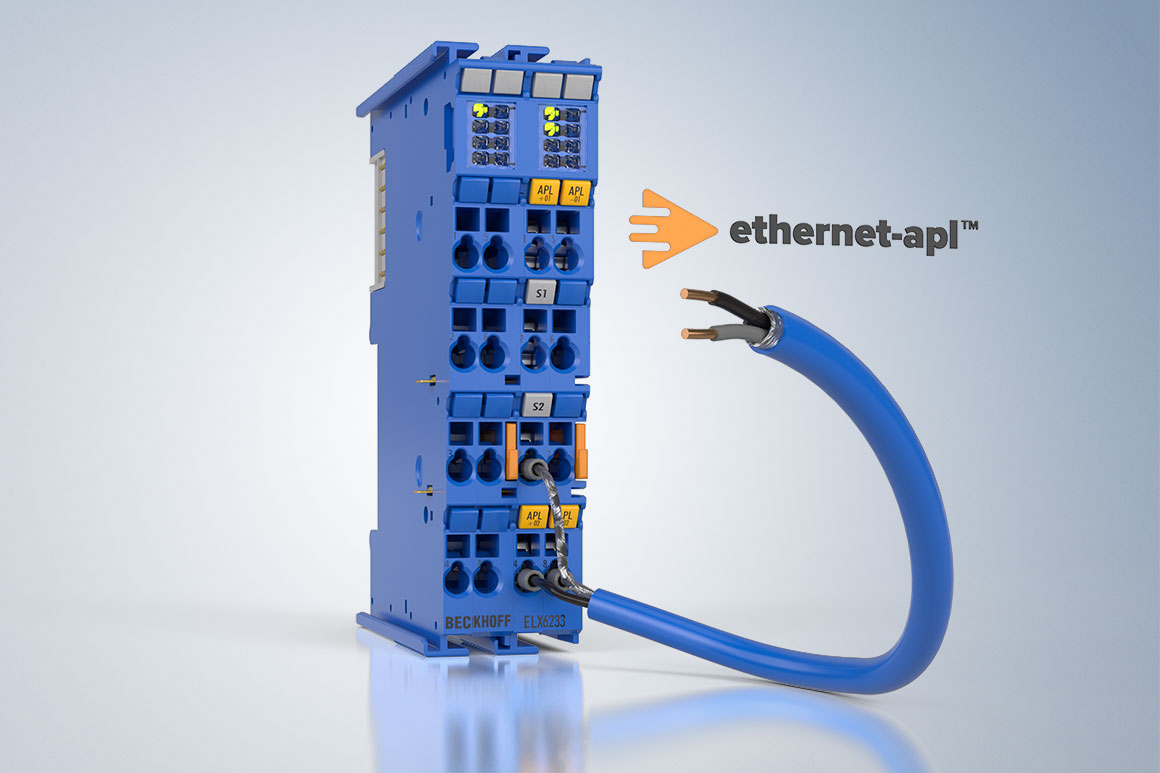
The vision of the Ethernet-APL concept is to implement the entire communication in process technology plants – from the field level to higher-level control systems – on an Ethernet basis. New Ethernet-APL-capable field devices are also required to retrofit entire plants. Since the technology is still relatively new and involves a high level of development work, the market does not yet offer a broad range of devices. The added value of a transmission rate of 10 Mbit/s is also limited for simple digital sensors.
This is why Beckhoff has made the decision to integrate Ethernet-APL technology into their modular terminal block portfolio. The compact ELX6233 can be mounted in the control cabinet in combination with other EtherCAT Terminals. Two Ethernet-APL field devices can be connected via the ELX6233 terminal. As with all EtherCAT Terminals in the ELX series, the ELX6233 enables direct connection of intrinsically safe field devices up to zone 0.
Advantages of the ELX6233 at a glance
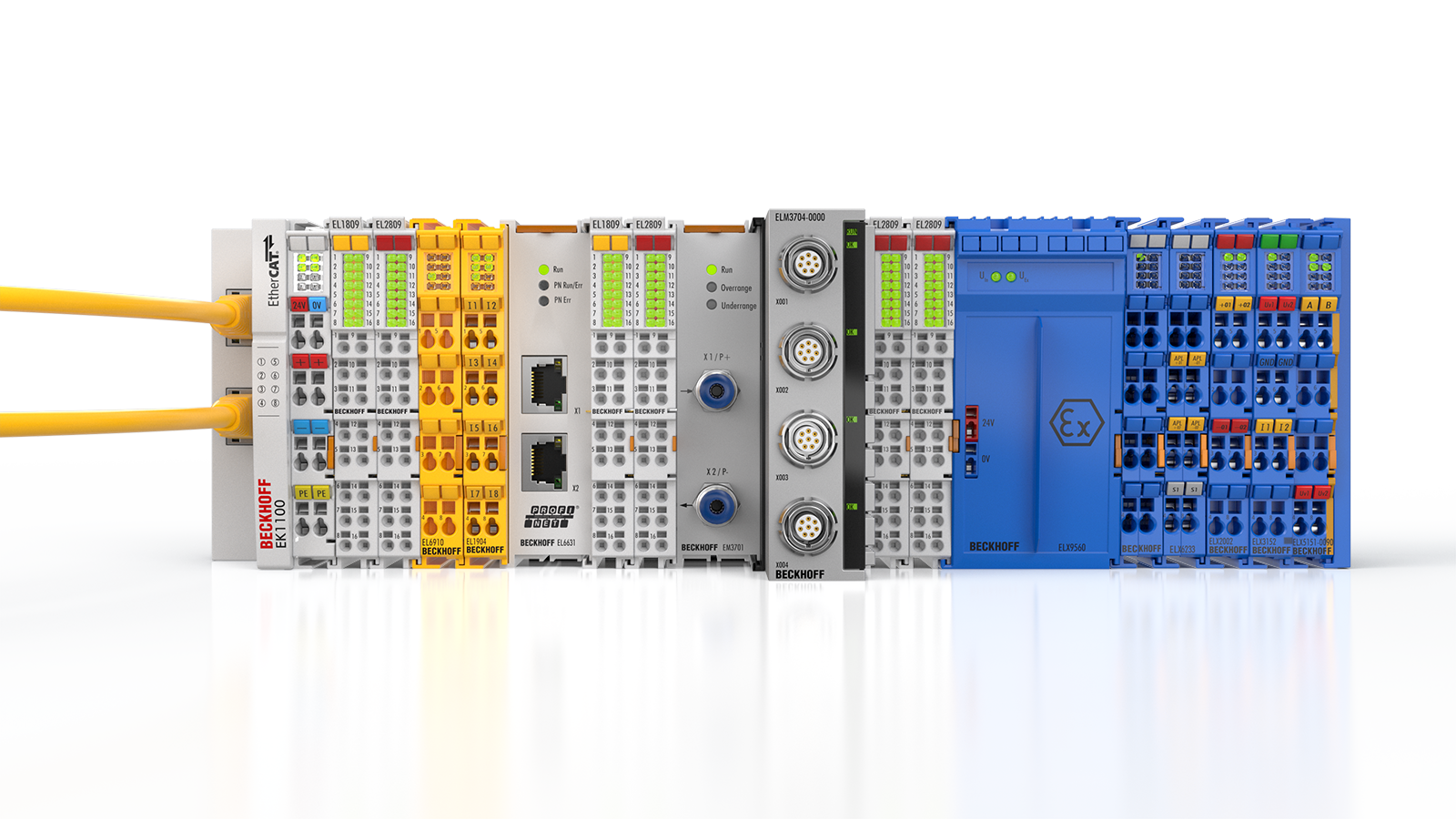
Modular and flexible combination options
The Beckhoff system solution allows all EtherCAT Terminals to be interconnected without requiring special tools. The ELX6233 features a standard housing and can therefore be easily integrated into existing terminal segments. When it comes to digitalization, the direct connection to embedded PCs in the CX series in particular offers a whole host advantages, including the ability for gateway applications to process data from the field and filter it before sharing it further.
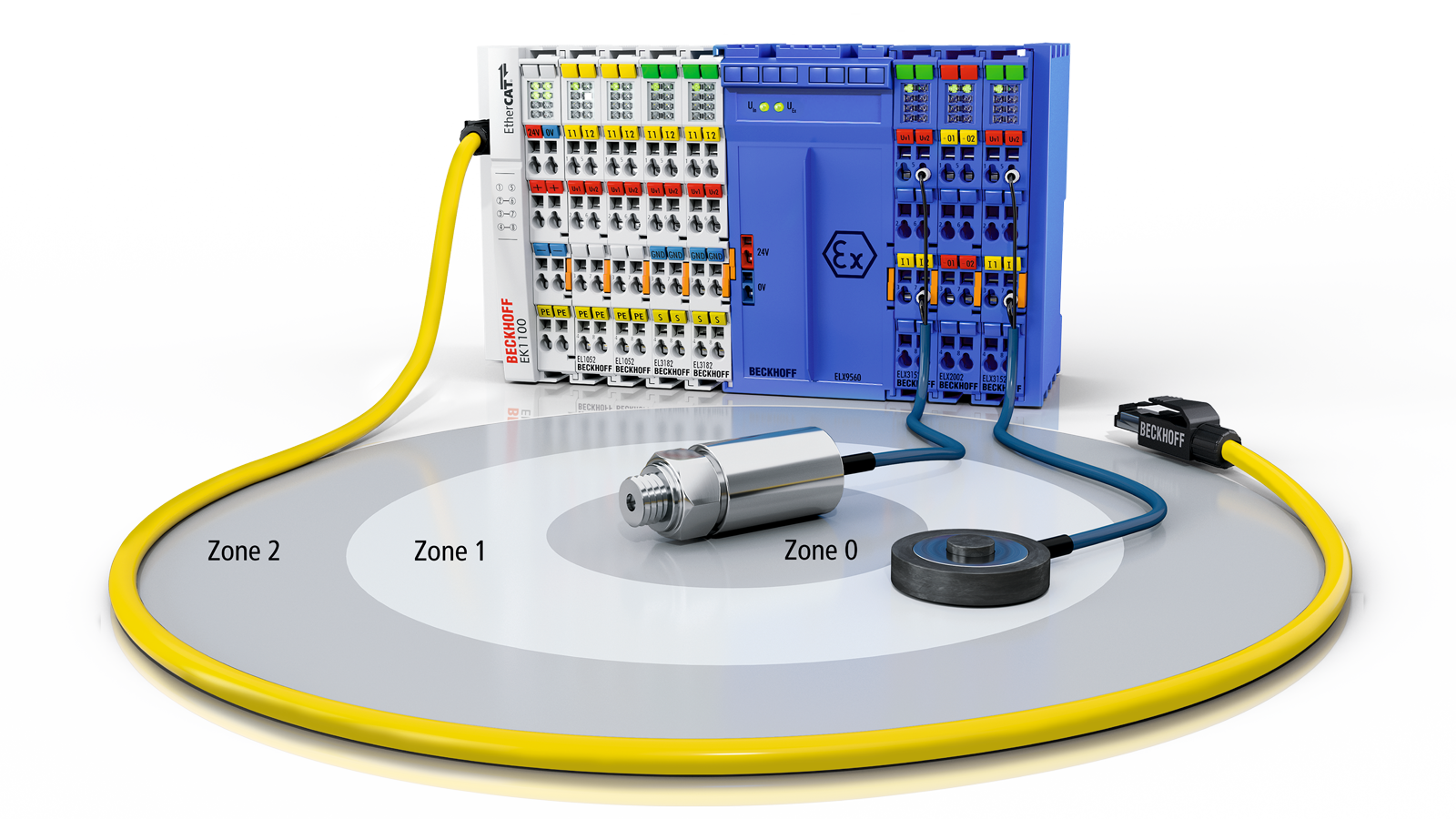
Connection of intrinsically safe field devices
Like many of our EtherCAT Terminals, the ELX6233 is suitable for mounting in zone 2 of the hazardous area. What’s more, the special circuitry means the ports offer the highest explosion protection class and allow the connection of intrinsically safe field devices from zone 0. This means the parameters are adapted to suit the specifications of IEC 60079-47 and follow the SPAA port profile.
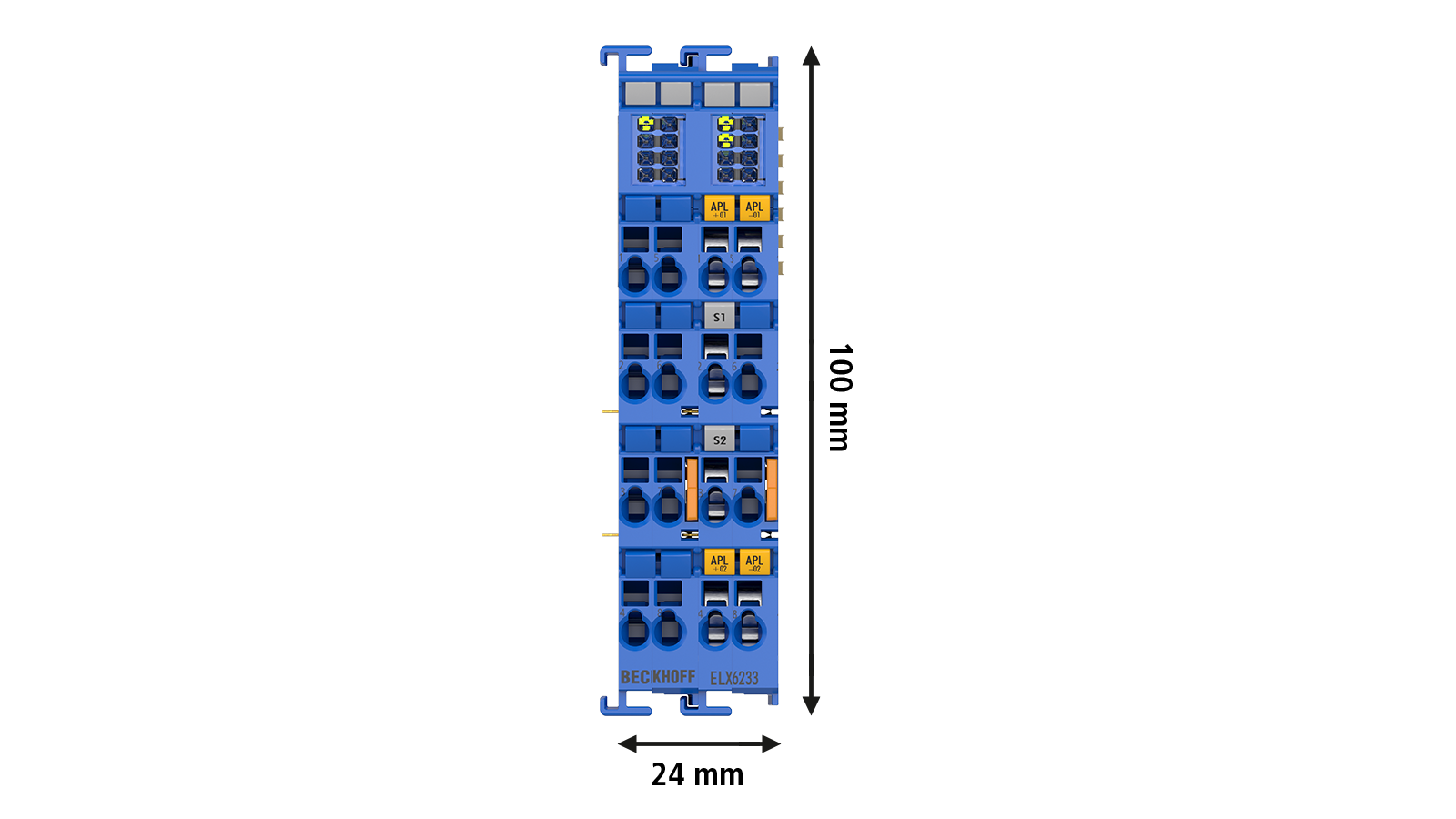
Space-saving solution
The ELX6233 allows you to create exactly the number of Ethernet-APL channels you need in your control cabinet. Its compact design not only saves you space, but also costs. And with a width of just 24 mm, the EtherCAT Terminal fits into any application, whether it’s a large process industry plant or a compact test setup.
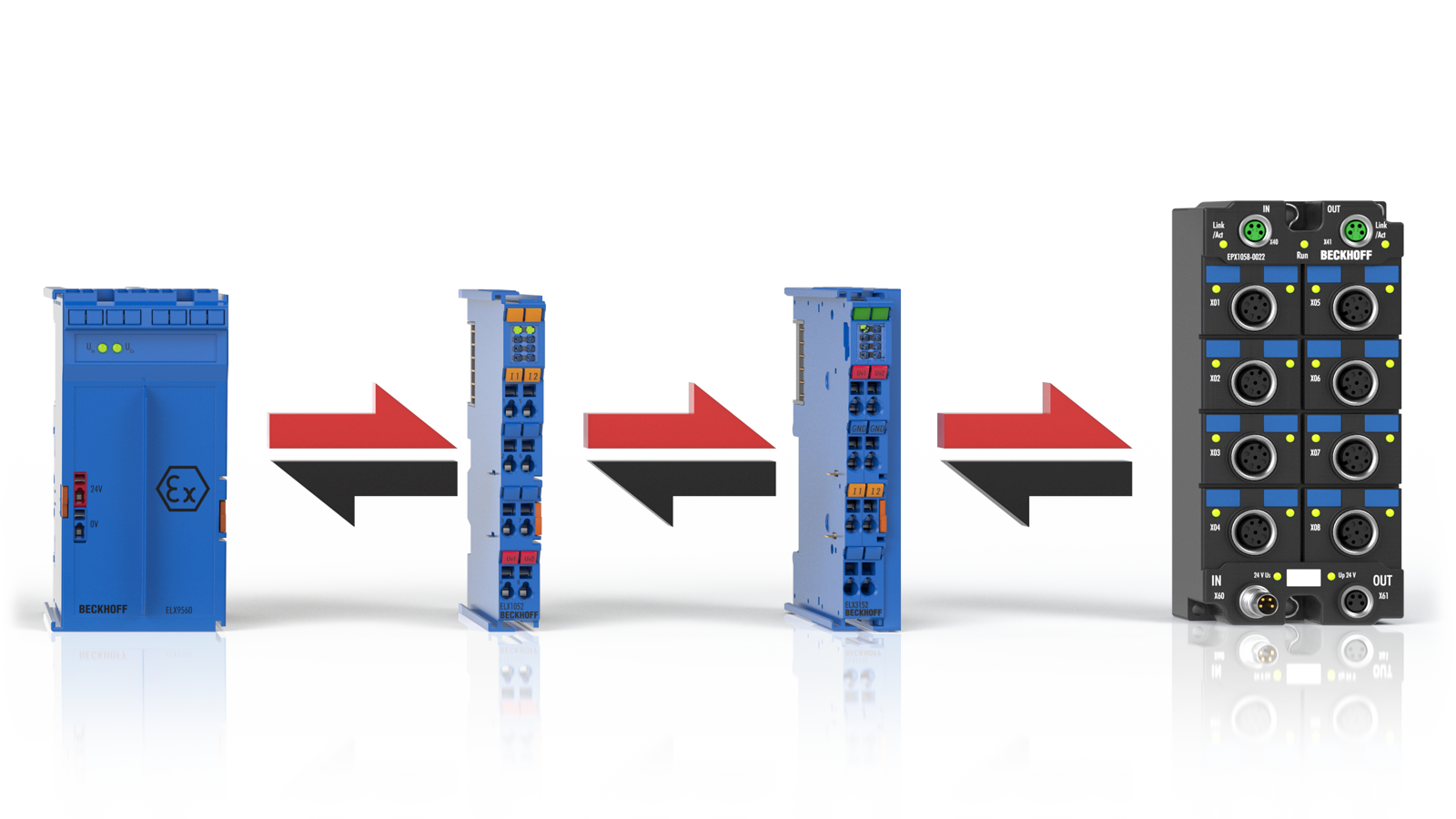
Fast communication with EtherCAT
Unlike in many PROFINET architectures, the controller is located directly in the EtherCAT Terminal and not in the higher-level controller. Since EtherCAT enables a more compact data size of the process image compared to PROFINET, the performance can be significantly increased in terms of cycle times. Data security is also higher than with classic switched networks due to the separation of individual ports and protocols.
Tutorial: Getting started with the ELX6233 (video in English)
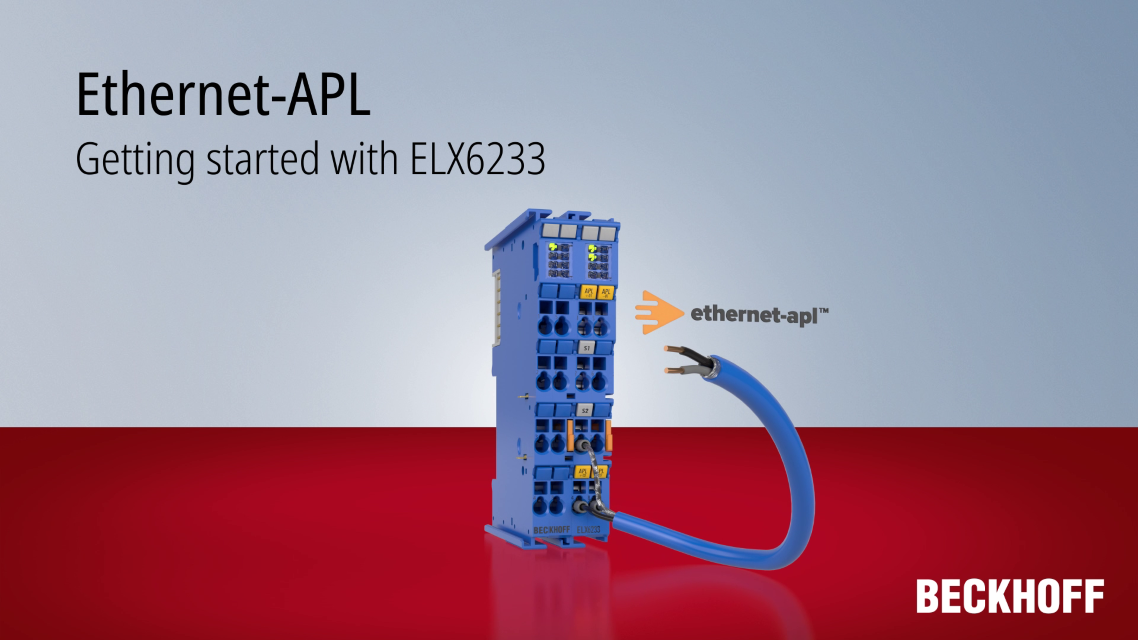
Learn how to commission the ELX6233 in TwinCAT and integrate field devices via Ethernet-APL. In this video tutorial, we guide you through the installation process step by step and provide useful tips on configuration and troubleshooting. We will show you how to effectively set up and optimize communication between the ELX6233 and connected devices.
The ELX6233 allows direct connection of Ethernet-APL-capable field devices from zone 0/20 and 1/21 hazardous areas. The sensors are supplied in accordance with the SPAA (TS10186) port profile and integrated via PROFINET. The flexible EtherCAT system architecture and ELX portfolio allow Ethernet-APL, HART, and simple digital signals to be integrated into the same terminal segment.
Further products and solutions for your systems
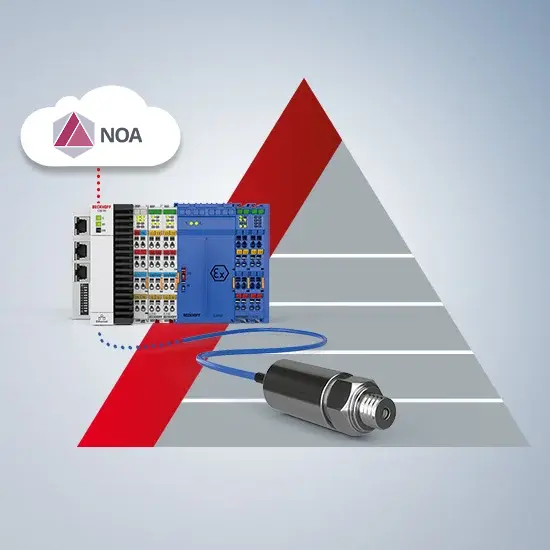
NAMUR Open Architecture (NOA)
Implementation of NOA concepts for seamless plant monitoring and data acquisition in brownfield and greenfield applications.
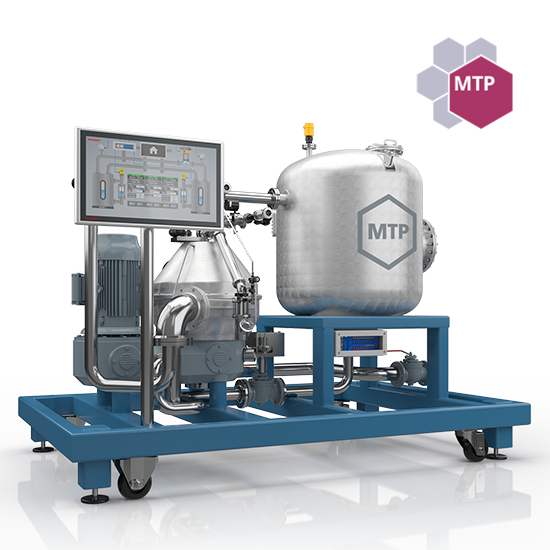
Module Type Package (MTP)
TwinCAT MTP integrates the Module Type Package concept into the engineering environment and enables efficient development of modular plants.
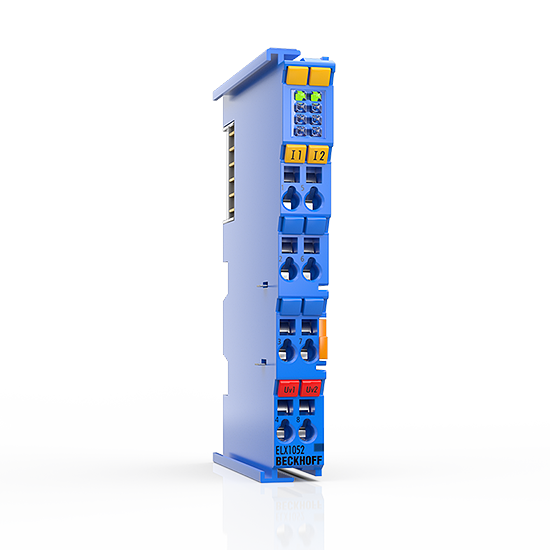
ELXxxxx | Explosion protection (Ex i)
The EtherCAT Terminals from the ELX series with intrinsically safe inputs/outputs enable the connection of field devices up to zone 0/20.
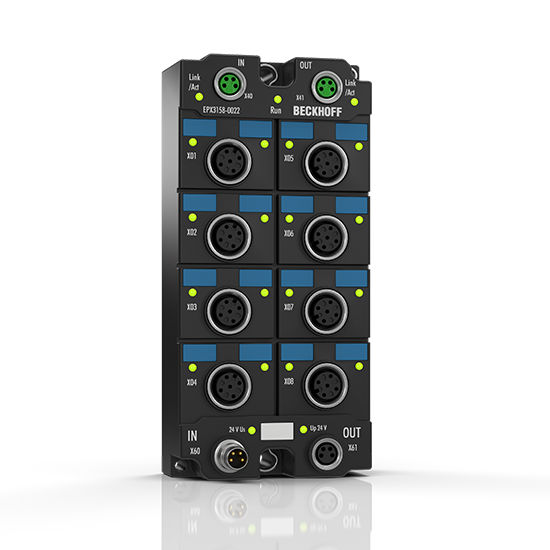
EPXxxxx | Explosion protection (Ex i)
The EtherCAT Box modules from the EPX series with intrinsically safe inputs/outputs enable the connection of field devices up to zone 0/20.