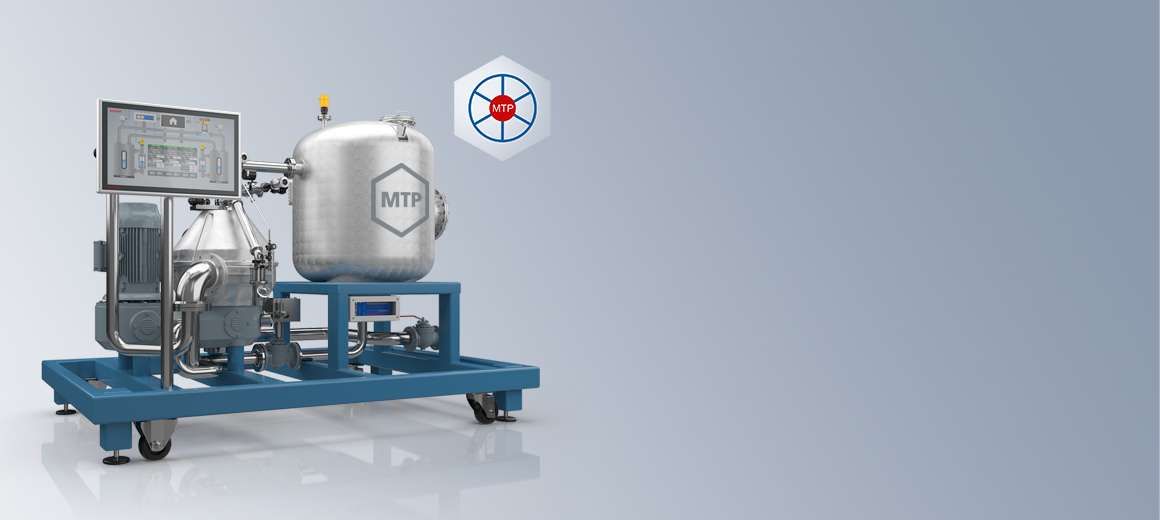
Module Type Package (MTP)
Headquarters United States
Beckhoff Automation LLC
+1 952 890-0000
beckhoff.usa@beckhoff.com
www.beckhoff.com/en-us/
Module Type Package (MTP)
Modular automation makes it possible to build and adapt flexible process engineering plants with little effort. As a result, inflexible automation systems that have operated unchanged for many years are gradually becoming a thing of the past: Customization and flexibility are the way forward for the process industry. Module Type Package (MTP) is a concept that can leverage optimization potential in process plants across the board, from planning to operation. This makes the MTP a crucial element in the development of future-proof modular automation solutions.
Benefits of Module Type Package (MTP)
Benefits of TwinCAT MTP
Defining the module
As a possible first step, a pre-existing P&ID can be imported into TwinCAT MTP via open interfaces. The associated services and further aspects of the MTP can then be defined.
Exporting the MTP
The MTP is exported and can be used by a Process Orchestration Layer (POL) to control the module. This information is also stored for automatic code generation.
Programming the module
In the next step, TwinCAT generates a customizable PLC template that pre-projects the requirements of the directive as far as possible. The code generated in this way is finally completed manually through state programming of the predefined services – i.e., the process-specific functionality of the module.
Activating the module
When activating the configuration, TwinCAT automatically ensures that the OPC UA communication can be established by the POL as described in the MTP.
Engineering the plant
The MTP exported from TwinCAT is imported into a POL for plant engineering. A user interface (HMI) is automatically generated from the P&ID information stored in the MTP. The functionalities of the module are integrated into the overall context as part of the orchestration process. The connection to the module via OPC UA is established with the information already contained in the MTP.
In TwinCAT, the Module Type Package (MTP) concept is built into the products TwinCAT MTP Runtime and TwinCAT MTP Engineering. TwinCAT Engineering provides project management capabilities, which incorporate TwinCAT MTP Engineering as a specific project type. This project type supports source code generation for PLC projects, which use TwinCAT MTP Runtime to create a standard-compliant interface in a process plant module.
Using the TwinCAT XCAD Interface option, code generation can be customized and the information made usable in other processing. Any changes made subsequently in the MTP project management system are incorporated through automatic project comparison.
The project can then be activated. The variables for the interfaces defined are provisioned to the POL automatically through TwinCAT OPC UA.
An MTP (Module Type Package) is a communication interface between a higher-level control system (e.g. process control system) and a modular plant. The MTP describes the interface of visualization, provided services and other features of a module, so that a simple orchestration of the modules to form a complete plant can be done easily and quickly in the higher-level control system.
An MTP (Module Type Package) is a communication interface between a higher-level control system (e.g. process control system) and a modular plant. The MTP describes the interface of visualization, provided services and other features of a module, so that a simple orchestration of the modules to form a complete plant can be done easily and quickly in the higher-level control system.
TwinCAT 3 XCAD Interface is the latest version of the interface between ECAD tools and TwinCAT 3. Based on the standardized AutomationML (AML) format, I/O topologies created in ECAD tools can easily be imported into TwinCAT and created automatically. This saves the effort required for manual transfer to TwinCAT and avoids the associated possible sources of error and therefore increases the efficiency in the engineering process.
OPC UA is a platform-independent, service-oriented communication architecture for reliable, secure and multisupplier data transport from the production level to the production planning and ERP system or to the cloud.
The CPX27xx and CPX37xx Panel PC series for use in zone 2/22 offer multi-touch technology and multi-core performance.
The Control Panel series CPX29xx and CPX39xx offer multi-touch technology for distances of up to 100 meters for use in zone 2/22.
The DIN-rail-mountable, fanless Embedded PCs from the CX5100 series are equipped with Intel Atom® multi-core processors.
The EtherCAT Terminals from the ELX series with intrinsically safe inputs/outputs enable the connection of field devices up to zone 0/20.