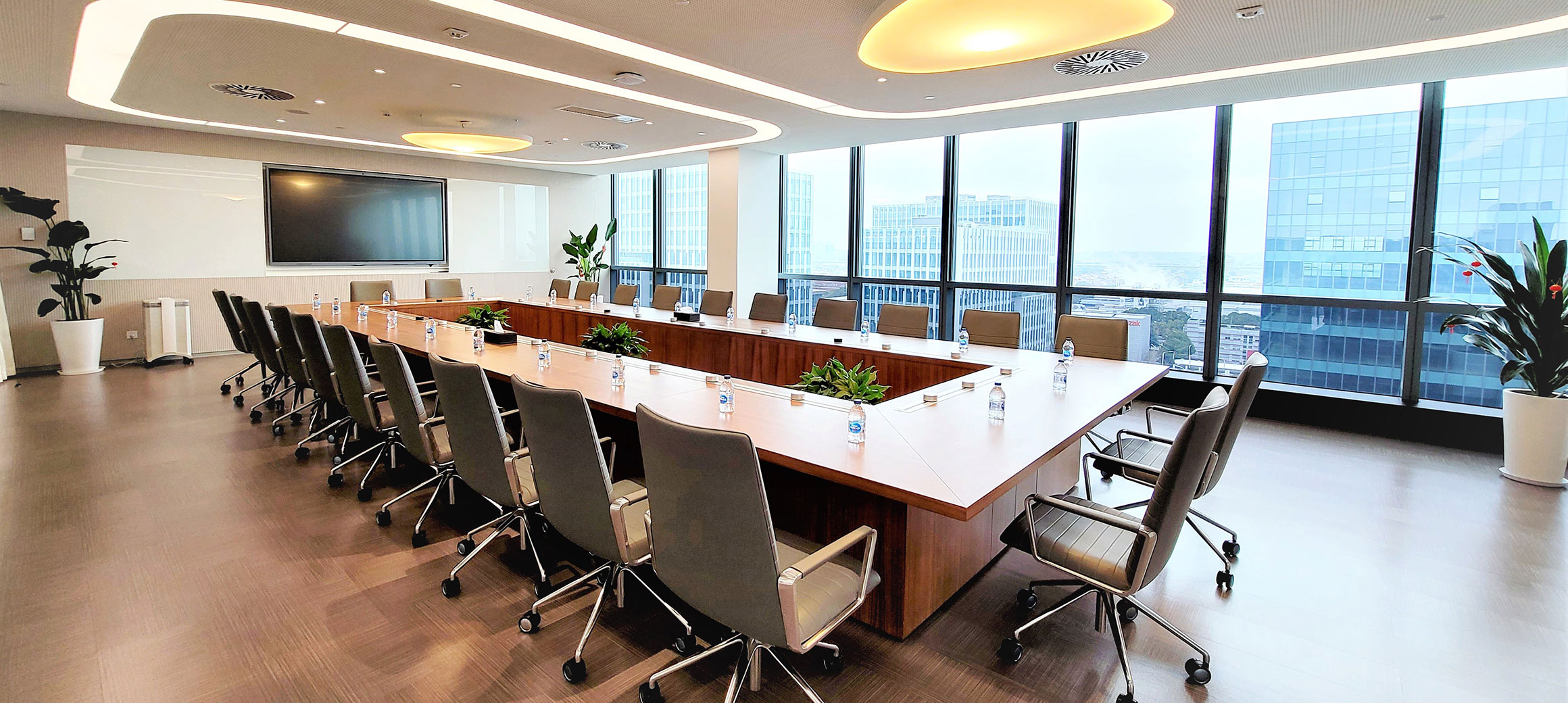
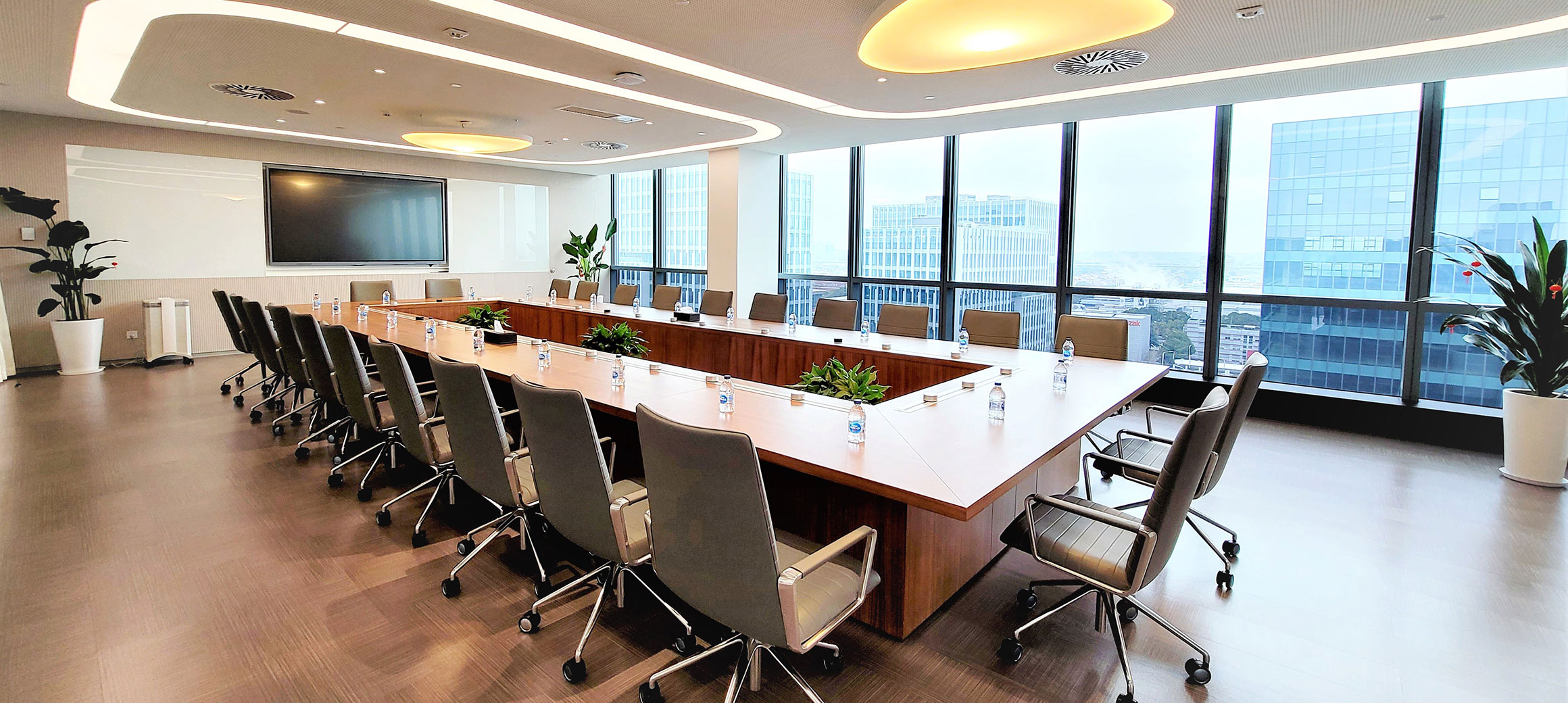
Beckhoff control technology implemented at the One Clariant Campus
Embedded PCs, bus terminals, EtherCAT and TwinCAT ensure precise blind control at Clariant’s new R&D center in Shanghai.
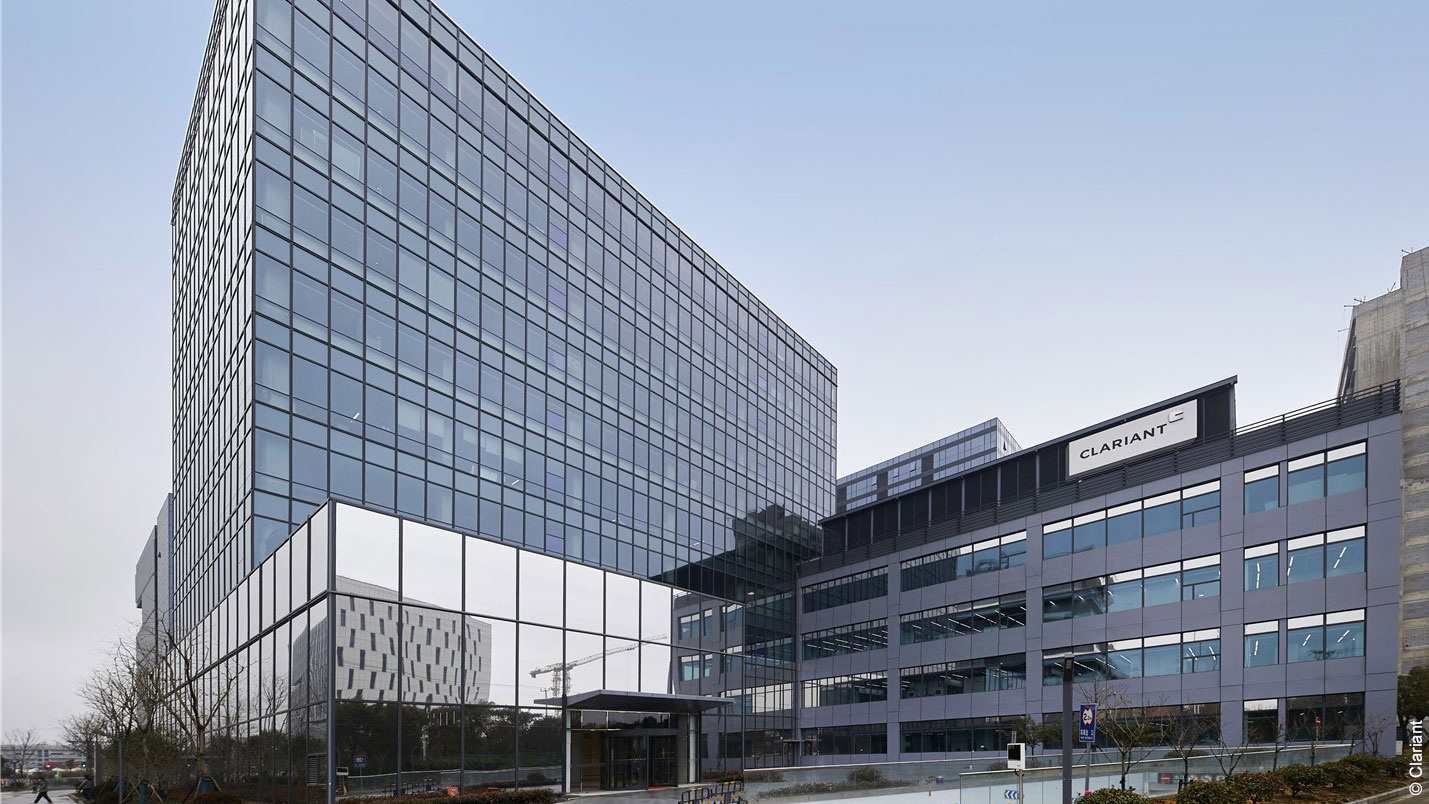
Clariant, one of the world’s leading specialty chemical companies, has opened a new state-of-the-art R&D center at its One Clariant Campus (OCC). Located in Shanghai’s Xin Zhuang Industrial Park, the new One Clariant Campus spans over a total of approximately 24,000 m2, consisting of slightly more than 12,000 m2 of laboratory area and close to 11,000 m2 of office and conference center buildings. It serves as the principal office location for about 350 employees. Sustainable building design was an important element in the construction of the One Clariant Campus. The campus has been awarded a LEED Gold certificate (Leadership in Energy and Environmental Design, the most widely used green building rating system in the world) as well as the Green Building Label (highest Chinese green building certification).
The Beckhoff control system was commissioned by Tsino-Dynatron Electrical Technology Co., Ltd. in the beginning of 2021. Beckhoff embedded controllers and I/O terminals are used throughout the building for precise blind positioning to make optimum use of sunlight, keep external heat load outside when there’s a cooling demand and vice versa. In addition to optimizing the effect of heat radiation, the blind control exposes another great potential when used in combination with the lighting control: The diffused natural light from the special lamellas of the blinds also makes it possible to reduce the lighting level of the rooms. Two CX5120 Embedded PCs combined with a total of 482 KL2722 mutually locked triac output terminals distributed over EtherCAT are connected to 482 electronical motors for controlling the lamella angle. Precise position is given every 15 minutes throughout the day, all year round. All position data is configured using Excel sheets that are read by the automation software TwinCAT for correct control. This way, changes in the configuration can be made any time. To achieve correct control in changing weather conditions, the CX5120 controllers communicate with a weather station using the serial interface.