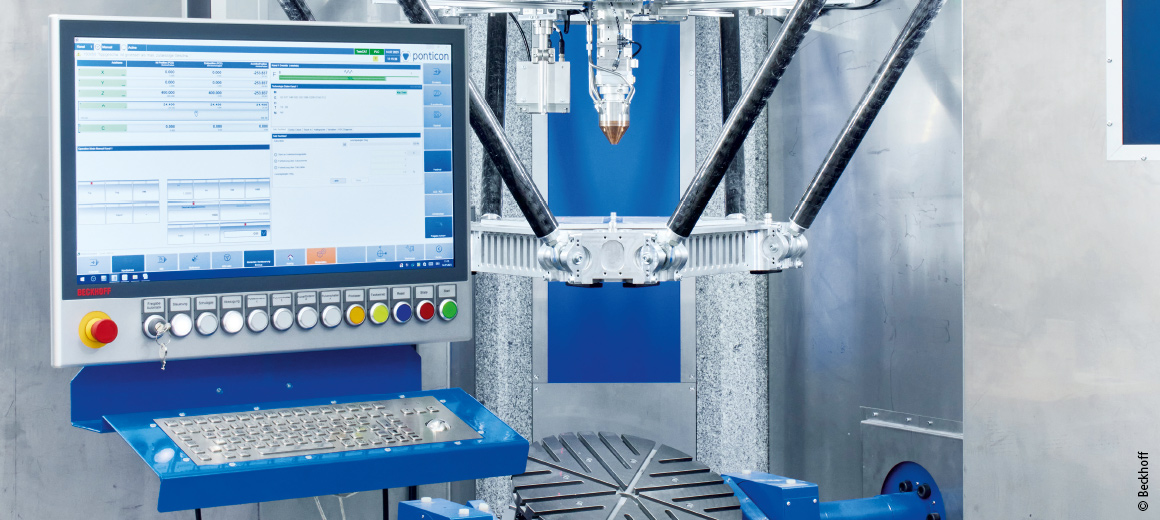
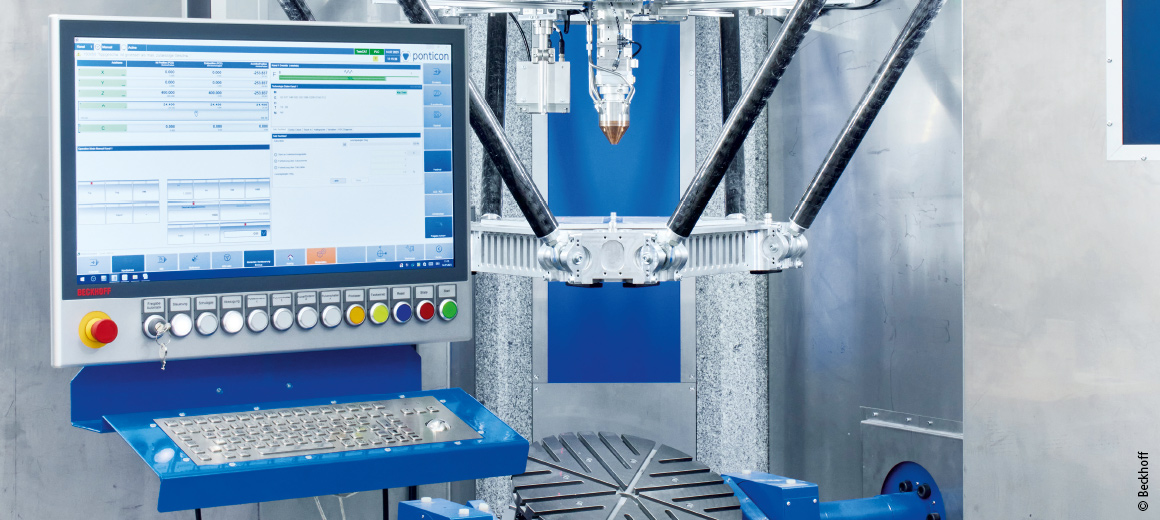
Laserauftragschweißen mit TwinCAT CNC
Laserauftragschweißen kommt heute oft bei der Beschichtung rotationssymmetrischer Bauteile zum Einsatz. Mit der pE3D-Anlage erweitert die Ponticon GmbH, Wiesbaden, das Einsatzspektrum um die Beschichtung und Additive Fertigung beliebiger Geometrien. Ohne TwinCAT CNC, EtherCAT und die eXtreme Fast Control Technology (XFC) von Beckhoff wären die Anforderungen an die präzise Ansteuerung und Koordination von Tripod, Dreh-/Schwenktisch und Laser nur schwer zu realisieren gewesen.
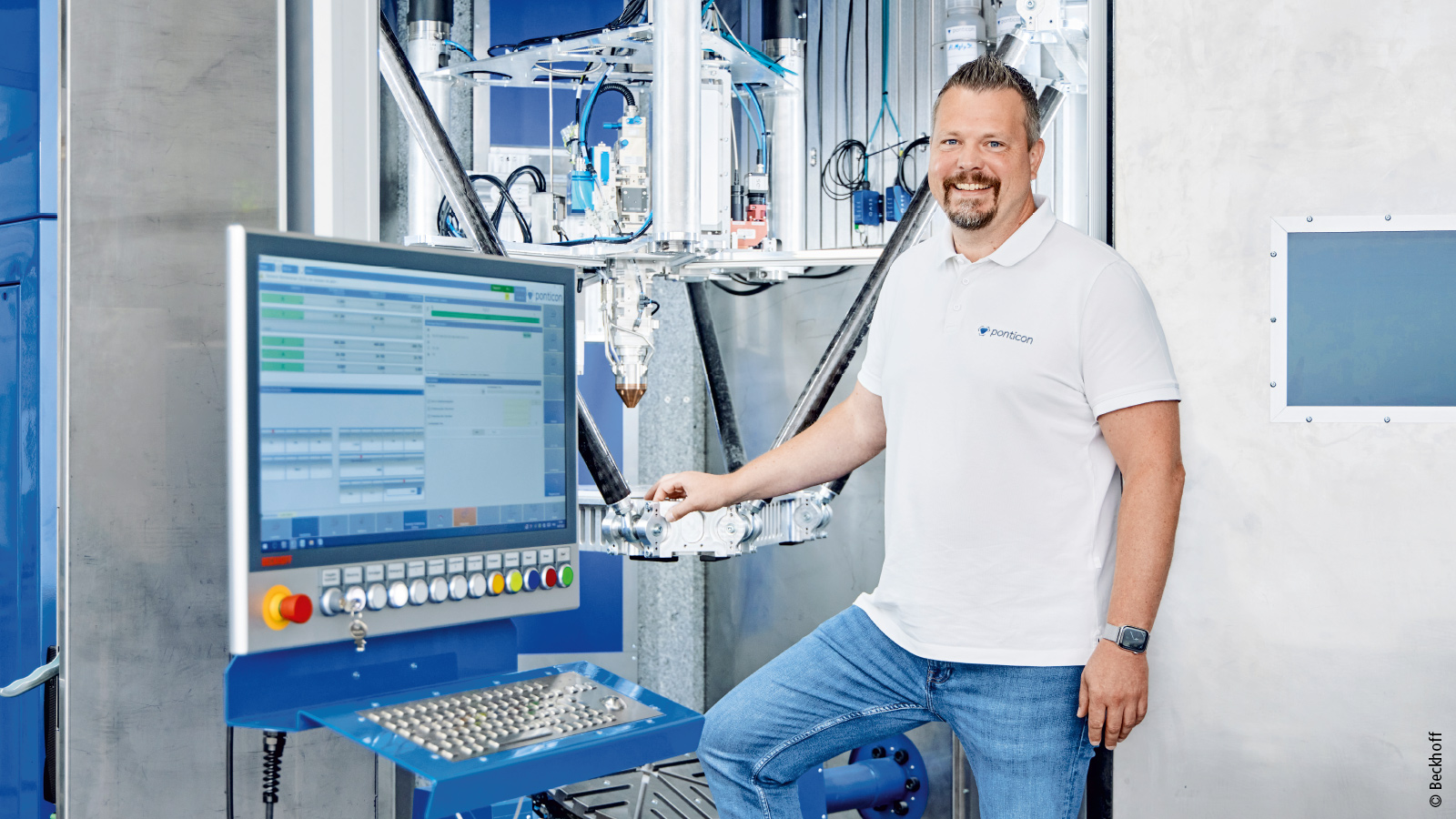
Die pE3D-Anlage von Ponticon ist nicht nur im Hinblick auf die möglichen industriellen Anwendungen ein echtes Schwergewicht: Aus massiven, bis zu 20 cm dicken Granitplatten aufgebaut, bringt das über 3 m hohe Grundgestell über 7 t auf die Waage. „Wer große Bauteile mit hoher Dynamik und Präzision aufbauen oder hauchdünn beschichten will, braucht eine steife Konstruktion“, erklärt Thomas Horr, Geschäftsführer von Ponticon. Konkret können auf der Anlage Bauteile bis 700 mm Durchmesser und bis zu 800 mm Höhe mit 50 bis 200 µm dünnen Materialstärken beschichtet, komplett neu aufgebaut oder repariert werden. Für letzteres Einsatzgebiet hat Ponticon kürzlich eine aus Mitteln der EU und dem Ministerium für Wissenschaft, Forschung und Kunst Baden-Württemberg finanzierte Fertigungszelle inkl. pE3D-Anlage an das Institut für Produktionstechnik am KIT in Karlsruhe geliefert (s. Infobox S. 22). Mit dem von Ponticon entwickelten 3DMD-Verfahren (Dynamic Material Deposition) kann das Laserauftragschweißen erstmalig zur hochproduktiven Fertigung komplexer Bauteilgeometrien aus nahezu beliebigen Materialkombinationen genutzt werden. Dazu sind insbesondere hohe Vorschubgeschwindigkeiten bei kleinsten Abweichungen unabdingbar. Mit einer Bahngenauigkeit von wenigen Hundertstel Millimetern arbeitet die pE3D-Anlage nicht nur präzise, sondern mit bis zu 200 m/min Vorschubgeschwindigkeit und bis zu 5 g Beschleunigung laut Thomas Horr auch außerordentlich dynamisch.
Die hohe Vorschubgeschwindigkeit resultiert aus dem speziellen Aufbau: einer Parallelkinematik. Üblicherweise sind Parallelkinematiken zwar sehr schnell, aber nicht unbedingt präzise. Mit speziellen mechanischen Elementen hat Ponticon dieses Manko bei ihrem Tripod beseitigt. Die Dreh-/Schwenkeinheit als vierte und fünfte Achse sorgt für zusätzliche Flexibilität bei der Bearbeitung komplizierter Geometrien.
Flexibilität mit Geschwindigkeit kombiniert
Zum Bearbeiten wird das Bauteil in der Standard-Betriebsart auf dem Tripod eingespannt und unter der feststehenden Lasereinheit bewegt. In der zweiten Konfiguration als 5-Achs-CNC ist dagegen der komplette Laserkopf auf dem Tripod befestigt. „Dazu nutzen wir einfach den vorher als Werkstückträger genutzten Rahmen“, erklärt Thomas Horr die clevere Lösung. Das Bauteil wird dann auf der darunterliegenden Dreh-/Schwenkeinheit eingespannt und kann zusätzlich gedreht und geneigt werden. Somit lassen sich pulverförmige Metalle und Legierungen auf beliebig geformten Oberflächen auftragen. Der Tisch wird benötigt, wenn beispielsweise die Geometrie des Werkstücks eine Umorientierung verlangt, um Überhänge oder bestimmte Winkel zu erreichen oder um rotationssymmetrische Teile aufzubauen. „Unsere schnell drehende Rotationsachse erlaubt uns auch in dieser Betriebsart Vorschubgeschwindigkeiten von bis zu 200 m/min“, so Thomas Horr.
Diese Eckdaten stellen nicht nur hohe Ansprüche an den mechanischen Aufbau. Die Steuerung muss die Dynamik der Anlage ebenso mitgehen können, besonders was die Ansteuerung der Peripheriegeräte betrifft. „Das Wichtigste sind die exakten Schaltzeitpunkte des Lasers“, stellt Thomas Horr heraus, „damit der Laser an der richtigen Position schaltet und das Material aufschmilzt.“
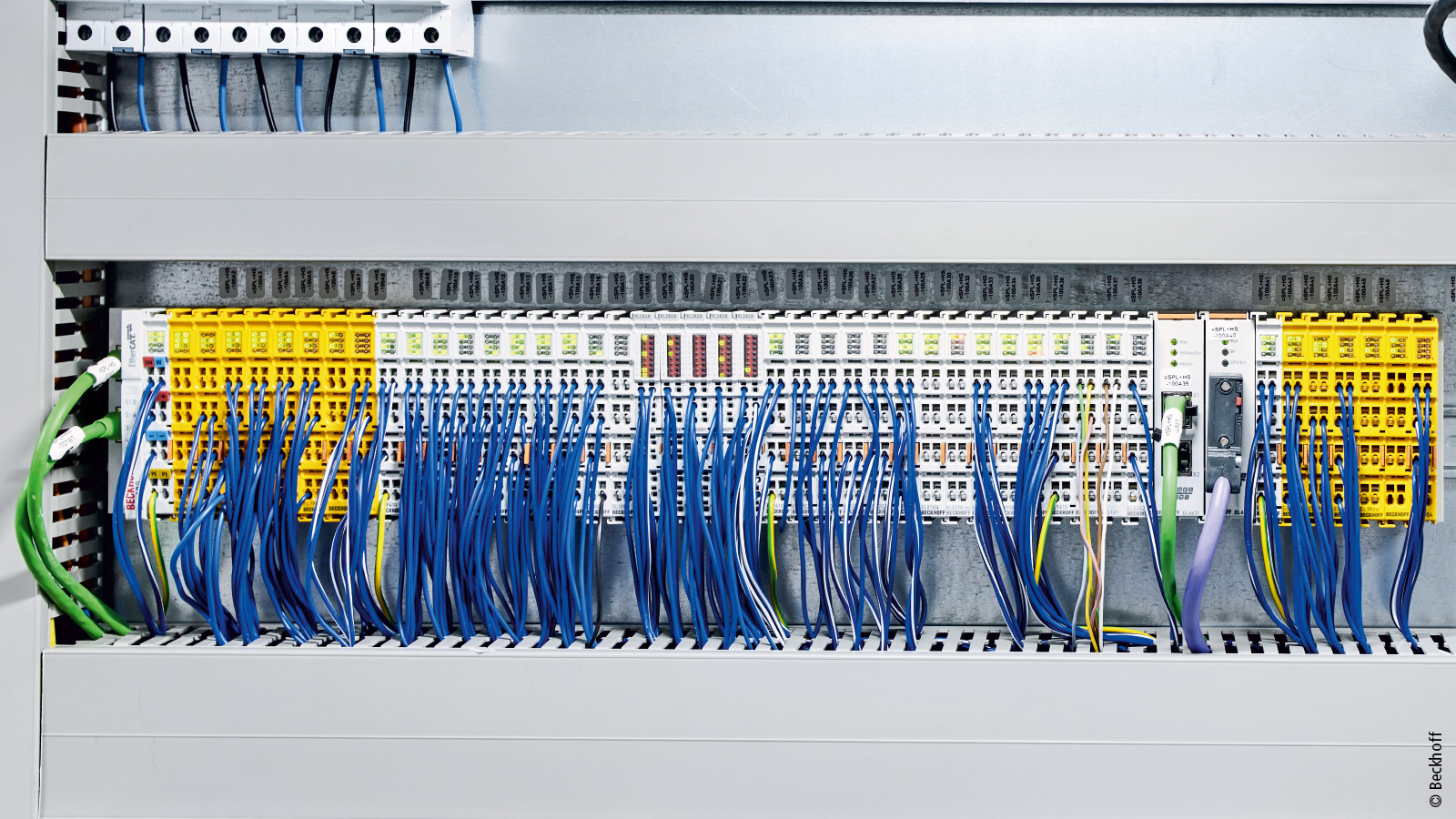
Exakte Laseransteuerung über XFC
Hier setzt Ponticon auf XFC von Beckhoff, in Verbindung mit den Oversampling-Klemmen EL2262. XFC basiert auf einer optimierten Steuerungs- und Kommunikationsarchitektur, die aus einem modernen Industrie-PC, ultraschnellen I/O-Klemmen mit erweiterten Echtzeiteigenschaften, dem Highspeed-Ethernet-System EtherCAT und der Automatisierungssoftware TwinCAT besteht. Mit XFC ist es möglich, I/O-Response-Zeiten unter 100 μs zu realisieren.
Den Tripod dynamisch verfahren zu können, setzt voraus, dass sich die Achs-Sollwerte mit hoher Frequenz vorgeben lassen und die Istwerte entsprechend schnell zurückgeliefert werden. EtherCAT hat die dafür benötigte Performance. Zudem erleichtert Safety over EtherCAT (FSoE) die Umsetzung der Sicherheitsvorgaben.
Die Bahnregelung von Tripod und Dreh-/Schwenktisch erfolgt über TwinCAT CNC. Die Achsregler sind dazu auf maximale Dynamik getrimmt und arbeiten mit sehr geringen Schleppabständen. „In den entsprechenden Funktionsbausteinen, mit denen wir die Ansteuerung optimieren, steckt viel Entwicklungsarbeit von uns“, betont Thomas Horr.
TwinCAT CNC passt zur Anlagenkinematik
Die in TwinCAT bereits vorhandene kinematische Transformation des Tripods war ein weiteres Argument für Ponticon, PC-based Control und insbesondere TwinCAT CNC zu nutzen. So brauchten die Entwickler die Kinematik nur zu konfigurieren und hatten keinen zusätzlichen Entwicklungsaufwand.
Ganz wichtig ist Thomas Horr eine flexible und modulare Plattform: „Gerade in der Anfangsphase, wenn die Aufgabenstellung noch nicht so deutlich formulierbar ist, braucht es Flexibilität wie sie TwinCAT und das Lizenzmodell von Beckhoff bieten. Wir waren überrascht, wie schnell wir alles in Betrieb nehmen konnten. Und wenn einmal Hürden zu überwinden waren, war der Support schnell zur Stelle, etwa bei Fragen zur Implementierung der Oversampling-Klemmen. Die Zusammenarbeit mit den Experten von Beckhoff war und ist so, wie wir es uns bei der Wahl unseres Systempartners gewünscht hatten.“ Gleiches bestätigt Prof. Frederik Zanger, Institutsleiter am wbk, über die Zusammenarbeit mit Ponticon. „Das Projekt begann während einer wirtschaftlich unsicheren Phase. Niemand wusste, wie sich die Lieferzeiten der unterschiedlichen Komponenten entwickeln werden. Wir sind heute sehr froh, dass in der Zusammenarbeit mit Ponticon alles äußerst professionell ablief und reibungslos funktioniert hat.“
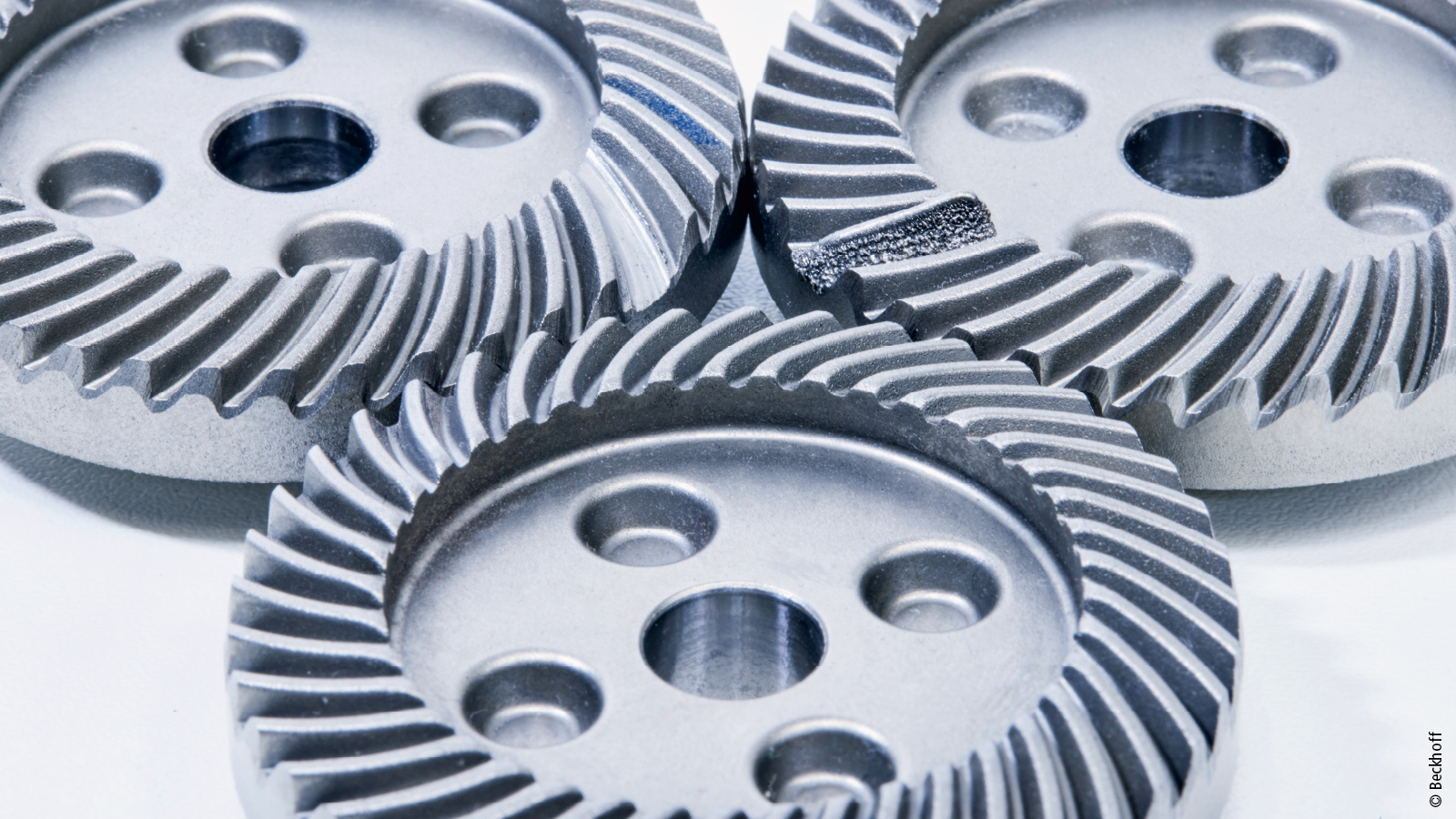
Technologie-Transfer auf andere Kinematik
Die Flexibilität von PC-based Control wird auch in künftigen Projekten von Nutzen sein. Denn das Laserauftragschweißen ist nicht an eine bestimmte Kinematik gebunden. „Wir sind sicher, die bisherigen Entwicklungen auf der Beckhoff Plattform auch auf andere Kinematiken portieren zu können, etwa auf einen 6-Achsroboter.“ Die entsprechenden kinematischen Modelle stehen in TwinCAT jedenfalls bereits zur Verfügung.
Laserauftragschweißen in der zirkularen Produktion
Die Laserauftragschweißanlage von Ponticon ist ein wesentlicher Bestandteil des am wbk Institut für Produktionstechnik des Karlsruher Institut für Technologie (KIT) aufgebauten Forschungsprojekts InRePro. InRePro steht für „Inspektions- und Remanufacturingzelle mit prozessintegrierter Multi-Sensorik für einen digital-autonomen Fertigungsprozess.“ Die Aufarbeitung gebrauchter Teilsysteme und Komponenten verringert den Ressourcenverbrauch (Rohstoffe und Energie) und ermöglicht eine neue, automatisierbare und damit großserientaugliche Form der Kreislaufwirtschaft. Ziel des von der EU (REACT-EU) sowie des Landes Baden-Württemberg geförderten Projekts ist es, eine zirkulare Produktion von Bauteilen in industriellem Maßstab zu untersuchen. Durch die Kombination der 5-Achs-Laserauftragschweißanlage mit einem 5-Achs-Bearbeitungszentrum ist eine flexible Aufarbeitung von Komponenten realisierbar. Die in die pE3D-Anlage integrierte multisensorielle Prozessbeobachtung gibt während der Bearbeitung direkte Rückschlüsse auf die Fertigungsqualität. Dazu sind in den Laserkopf entsprechende Sensoren (OCT, Quotienten-Pyrometer, Weldwatcher) integriert, die eine Überwachung der Schmelzzone ermöglichen. Ein nachgeführter 3D-Laserscanner bietet darüber hinaus die Möglichkeit, das Ergebnis des Materialauftrags direkt nach dem Prozess flächig geometrisch zu vermessen. Das System ermöglicht damit erstmals eine systematische Beobachtung und Ursachenforschung bei der Entstehung prozesstypischer Defekte.