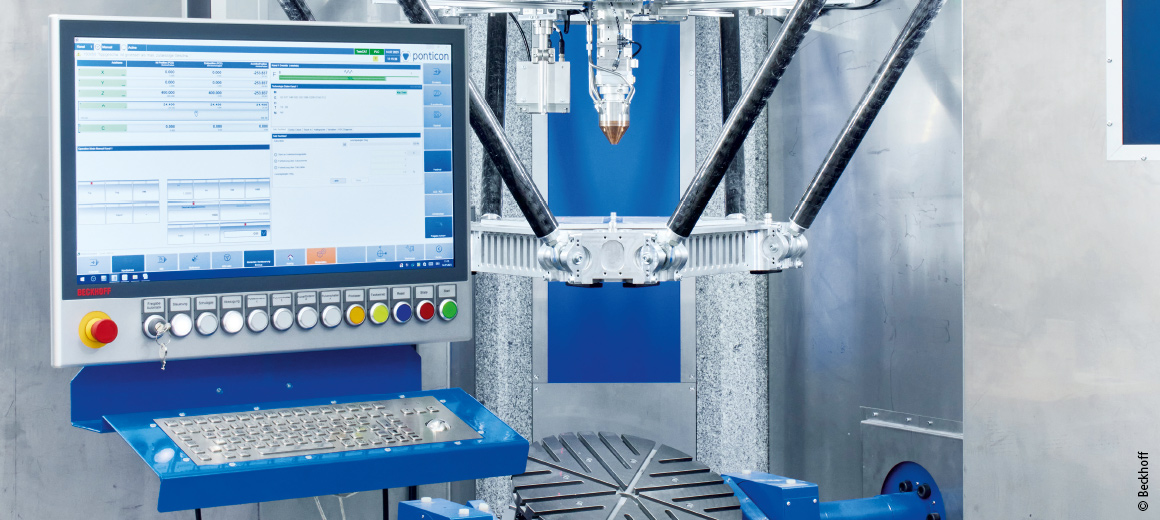
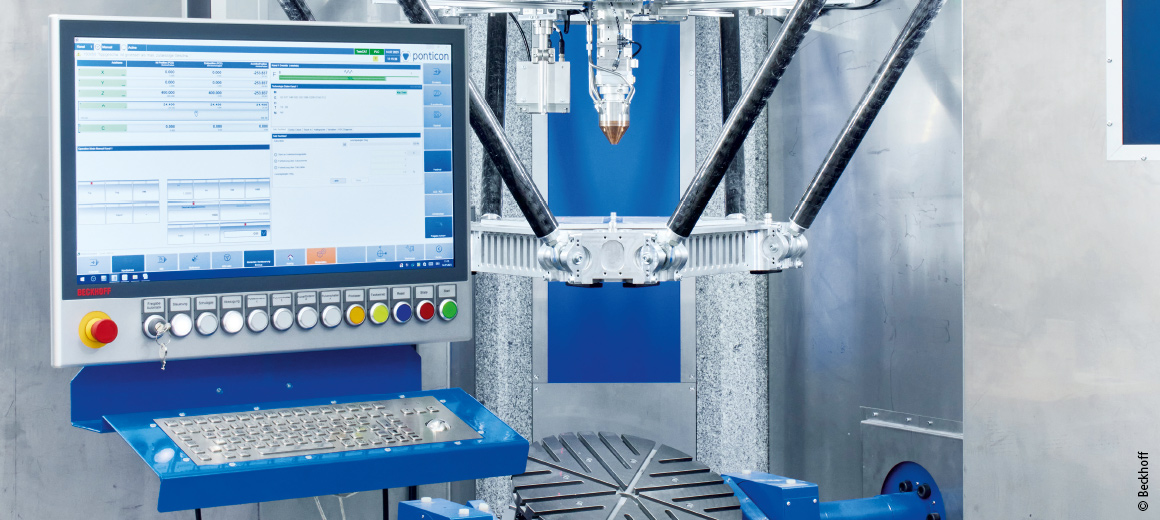
Laser cladding with TwinCAT CNC
Today, laser cladding is often used for coating rotationally symmetrical components. Ponticon GmbH, based in Wiesbaden, Germany, is expanding its range of applications to include coating and additive manufacturing of any geometries with the pE3D system. The requirements regarding the precise control and coordination of the tripod, rotary/swivel table, and laser would have been difficult to implement without TwinCAT CNC, EtherCAT, and eXtreme Fast Control Technology (XFC) from Beckhoff.
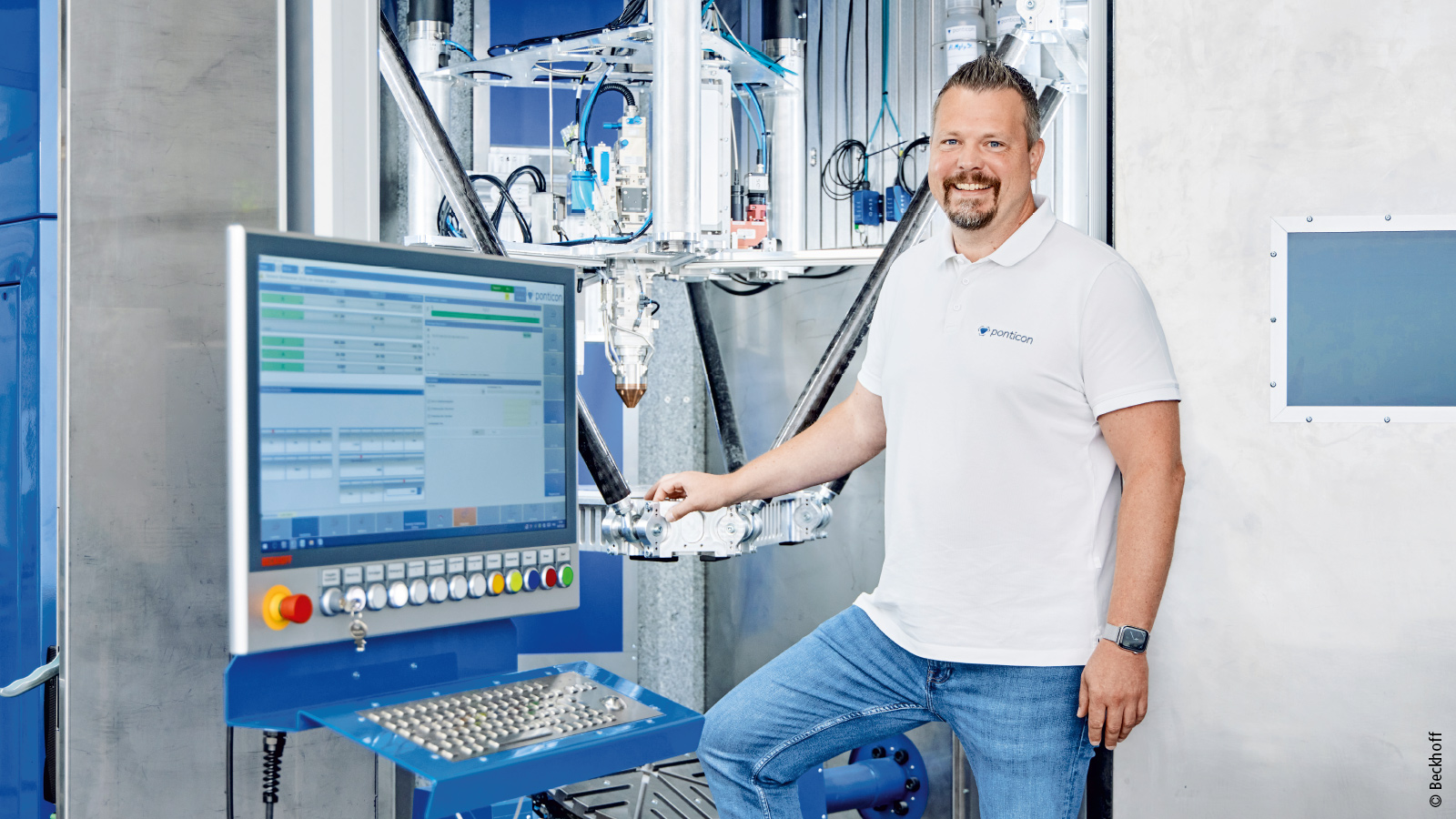
The pE3D system from Ponticon is a real heavyweight, and not just in terms of its potential industrial applications: constructed from solid granite slabs up to 20 cm thick, the base frame, which is over 3 m tall, weighs in at over 7 metric tons. “If you want to build up large components in a highly dynamic and precise process or apply an ultra-thin coating, you need a rigid structure,” explains Thomas Horr, Managing Director of Ponticon. In specific terms, components up to 700 mm in diameter and 800 mm in height can be coated with material thicknesses of only 50 to 200 µm, completely rebuilt, or repaired on the system. For the latter field of application, Ponticon recently delivered a manufacturing cell including a pE3D system to the Institute of Production Science at KIT in Karlsruhe, Germany, funded by the EU and the Ministry of Science, Research and Arts Baden-Württemberg (see info box). With the 3DMD (Dynamic Material Deposition) process developed by Ponticon, laser cladding can be used for the first time for highly productive manufacturing of complex component geometries from virtually any combination of materials. For this purpose, high feed rates with the smallest possible deviations are vital. With a path accuracy of a few hundredths of a millimeter, the pE3D system not only works with precision but also offers extraordinary dynamics, with feed rates of up to 200 m/min and acceleration of up to 5 g, says Thomas Horr.
The high feed rate results from the special design: a parallel kinematic system. Typically, parallel kinematics are very fast but not necessarily precise. By using special mechanical elements, Ponticon has eliminated this shortcoming in its tripod. The rotary/swivel unit as fourth and fifth axis provides additional flexibility for machining complex geometries.
Flexibility combined with speed
For machining in the standard operating mode, the component is clamped on the tripod and moved under the laser unit, which is in a fixed position. In the second configuration as a 5-axis CNC, however, the complete laser head is mounted on the tripod. “To do this, we simply use the frame which was previously used as a workpiece carrier,” says Thomas Horr, explaining the clever solution. The component is then clamped on the rotary/swivel unit below and can also be rotated and tilted. This allows powdered metals and alloys to be deposited on surfaces of any shape. The table is needed when, for example, the geometry of the workpiece requires reorientation to achieve overhangs or certain angles, or to build up rotationally symmetrical parts. “Our rapidly rotating rotary axis allows us to achieve feed rates of up to 200 m/min in this operating mode, too,” says Thomas Horr.
These key features place major demands on the mechanical structure. In addition, the control system must be able to keep up with the dynamics of the system, particularly with regard to the control of peripheral devices. “The most important thing is to ensure that the switching times of the laser are precise,” says Thomas Horr, “so that the laser switches at the right position and melts the material.”
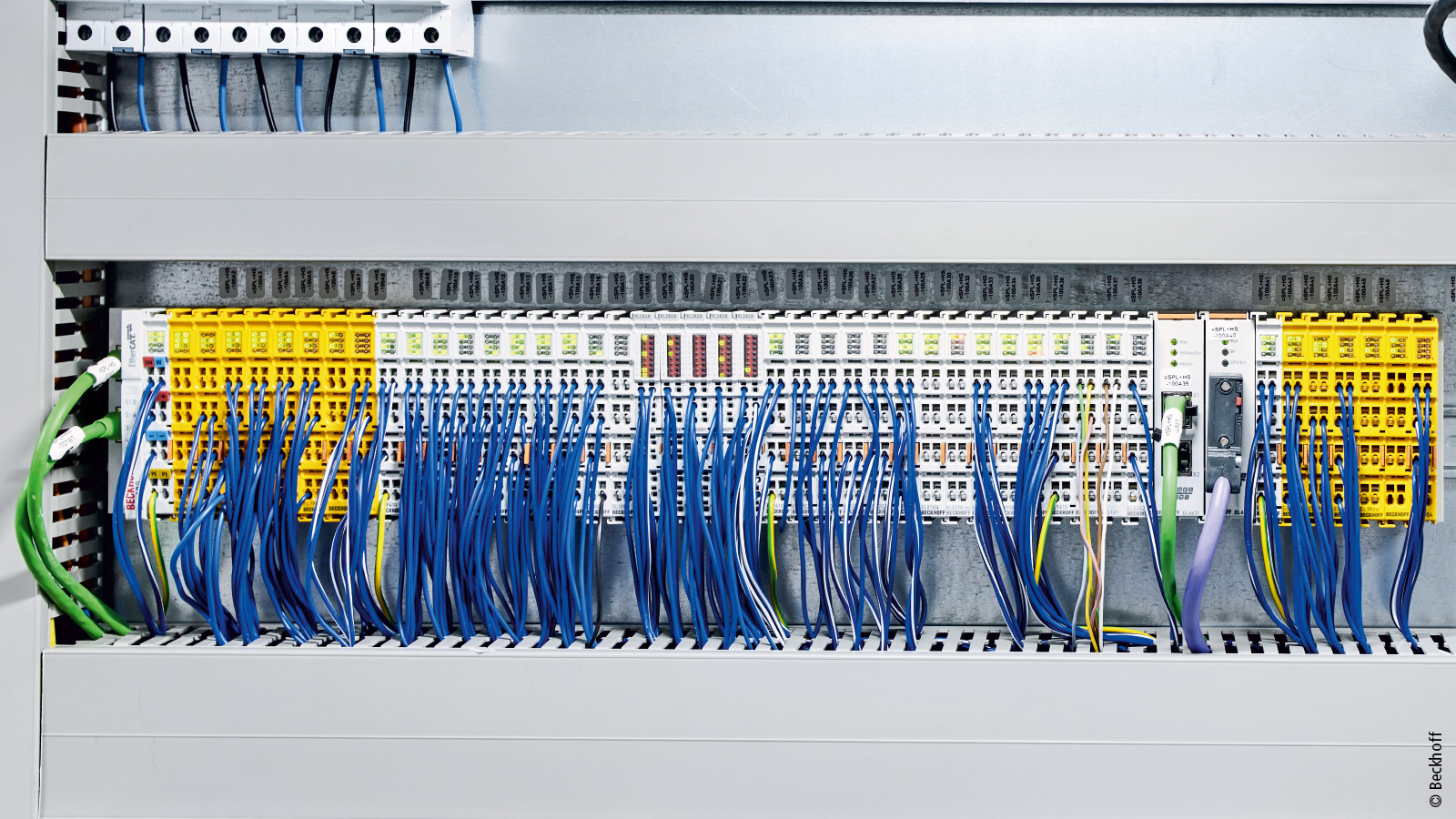
Precise laser control via XFC
In this area, Ponticon relies on XFC from Beckhoff in conjunction with the EL2262 oversampling terminals. XFC is based on an optimized control and communication architecture comprising an advanced industrial PC, ultra-fast I/O terminals with extended real-time characteristics, the EtherCAT high-speed Ethernet system, and the TwinCAT automation software. With XFC, it is possible to realize I/O response times of less than 100 µs.
In order to move the tripod dynamically, it must be possible to specify the axis setpoints at high frequency and the actual values must be returned equally quickly. EtherCAT offers the performance needed for this. In addition, Safety over EtherCAT (FSoE) facilitates the implementation of safety requirements.
Path control of the tripod and rotary/swivel table is implemented via TwinCAT CNC. For this purpose, the axis controllers are configured for maximum dynamics and operate with minimal lag. “A lot of development work has gone into the corresponding function blocks that we use for control optimization,” emphasizes Thomas Horr.
TwinCAT CNC suitable for system kinematics
The kinematic transformation for the tripod already available in TwinCAT was another reason for Ponticon to use PC-based control and TwinCAT CNC in particular. This meant the developers only needed to configure the kinematics and had no additional development work.
A flexible and modular platform is very important to Thomas Horr: “Particularly in the initial phase, when it is not possible to formulate the task so clearly, what is needed is flexibility, such as that offered by TwinCAT and the licensing model from Beckhoff. We were surprised at how quickly we were able to get everything up and running. And if there were any hurdles to overcome, support was available quickly, such as when there were questions about the implementation of the oversampling terminals. The collaboration with the experts from Beckhoff has been exactly what we had hoped for when choosing our system partner.” Prof. Frederik Zanger, Institute Director at wbk, says the same about the collaboration with Ponticon. “The project began during a period of economic uncertainty. Nobody knew what would happen to the delivery times for the various components. Today, we are delighted that everything has been extremely professional and has run smoothly in our collaboration with Ponticon.”
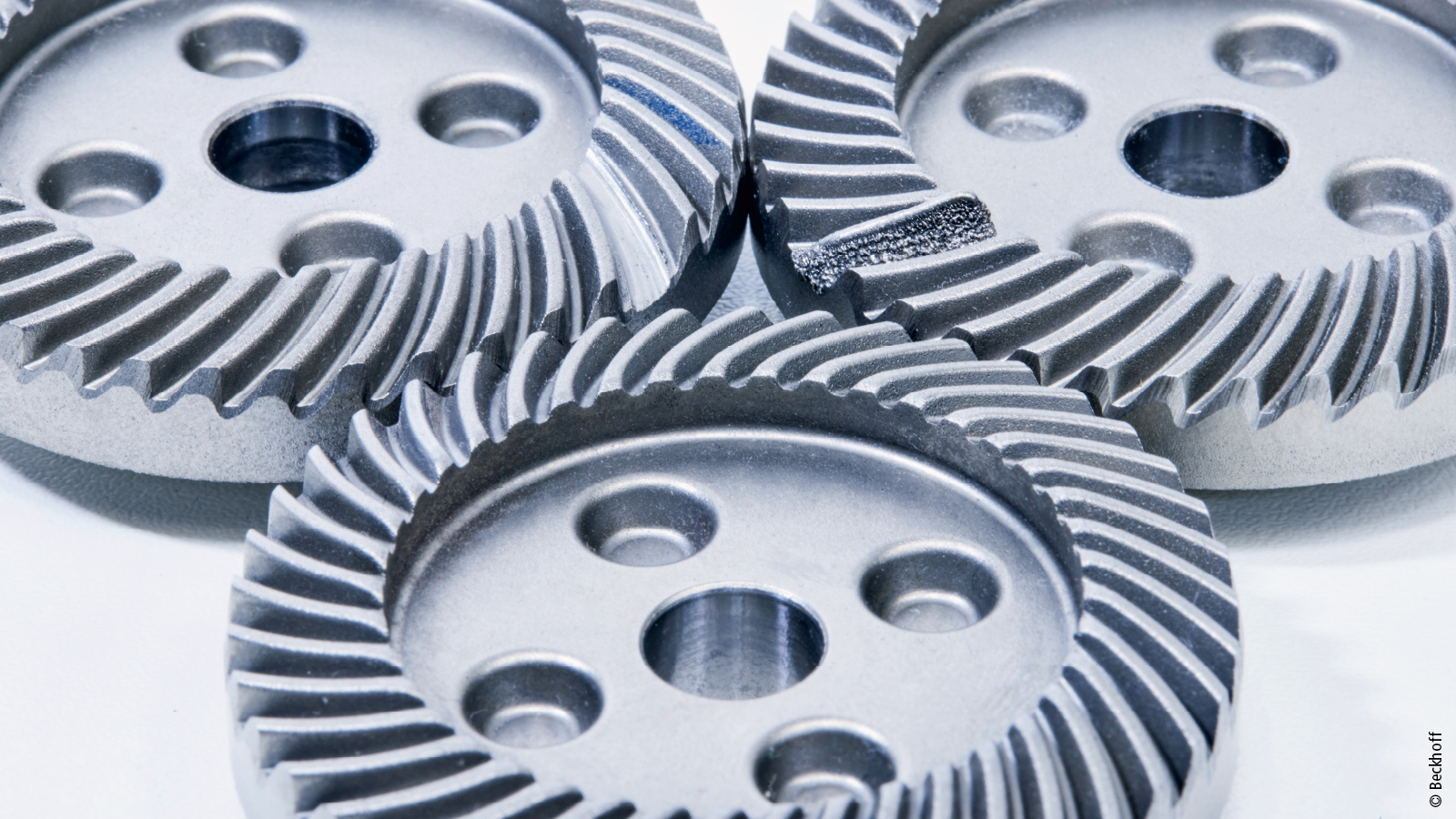
Technology transfer to other kinematics
The flexibility of PC-based control will also be useful in future projects. This is because laser cladding is not tied to any particular kinematics. “We are confident that we will be able to port the previous developments on the Beckhoff platform to other kinematics, such as a 6-axis robot.” In any case, the corresponding kinematic models are already available in TwinCAT.
Laser cladding in circular production
The Ponticon laser cladding system is an essential component of the InRePro research project launched at the wbk Institute of Production Science at the Karlsruhe Institute of Technology (KIT). InRePro stands for “Inspection and remanufacturing cell with process-integrated multi-sensor technology for a digital-autonomous manufacturing process.” The reconditioning of used subsystems and components reduces consumption of resources (raw materials and energy) and enables a new type of circular economy that can be automated and is thus suitable for large-scale production. The aim of the project, which is funded by the EU (REACT-EU) and the state of Baden-Württemberg, is to investigate the circular production of components on an industrial scale. By combining the 5-axis laser cladding system with a 5-axis machining center, it is possible to implement flexible reconditioning of components. The multi-sensor process monitoring solution integrated into the pE3D system provides immediate information about manufacturing quality during the machining process. For this purpose, corresponding sensors (OCT, quotient pyrometer, WeldWatcher) are integrated into the laser head, which enable monitoring of the melting zone. A tracked 3D laser scanner also offers the possibility of measuring the material deposition results over a geometric area immediately after the process. The system therefore makes it possible to systematically observe and investigate the causes of typical defects in the process for the first time.