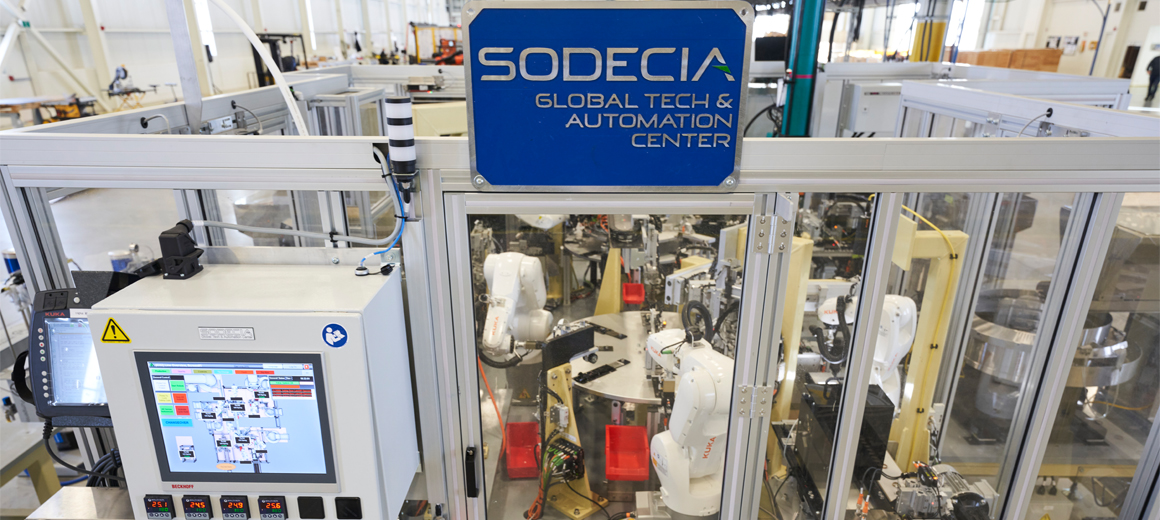
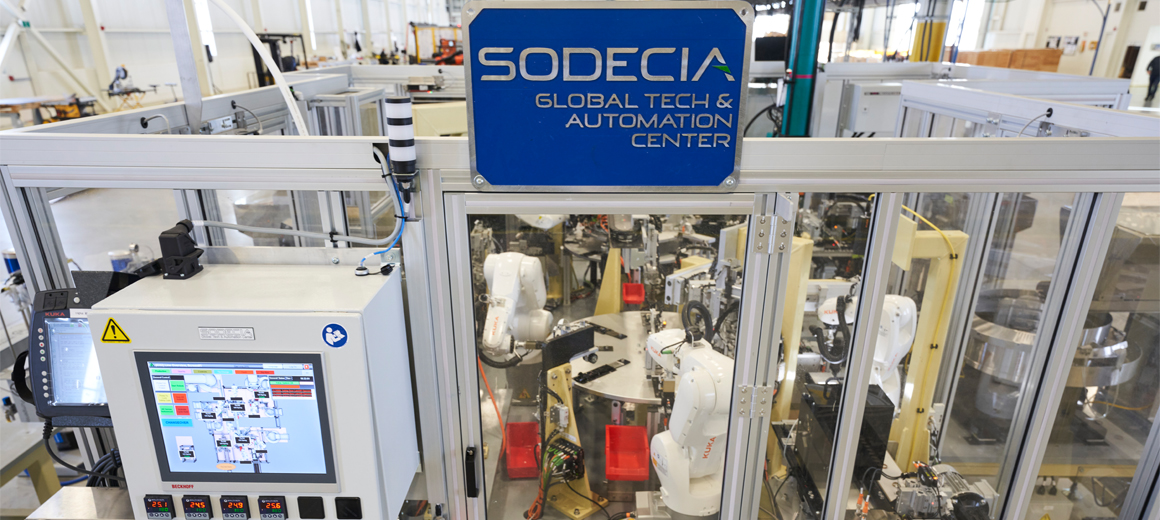
Automotive-Sondermaschinen standardisiert auf EtherCAT und PC-based Control
Bei dem Bau von Sondermaschinen für die anspruchsvolle Automobilindustrie wendet das Global Tech and Automation Center (GTAC) von Sodecia erfolgreich Prinzipien aus der Serienproduktion an. Die Modernisierung einer Montageanlage für Sicherheitsgurte zeigt dabei als Paradebeispiel die Vorteile der beim Automotive-Spezialisten als Standard eingesetzten PC- und EtherCAT-basierten Steuerungs- und Antriebstechnik von Beckhoff.
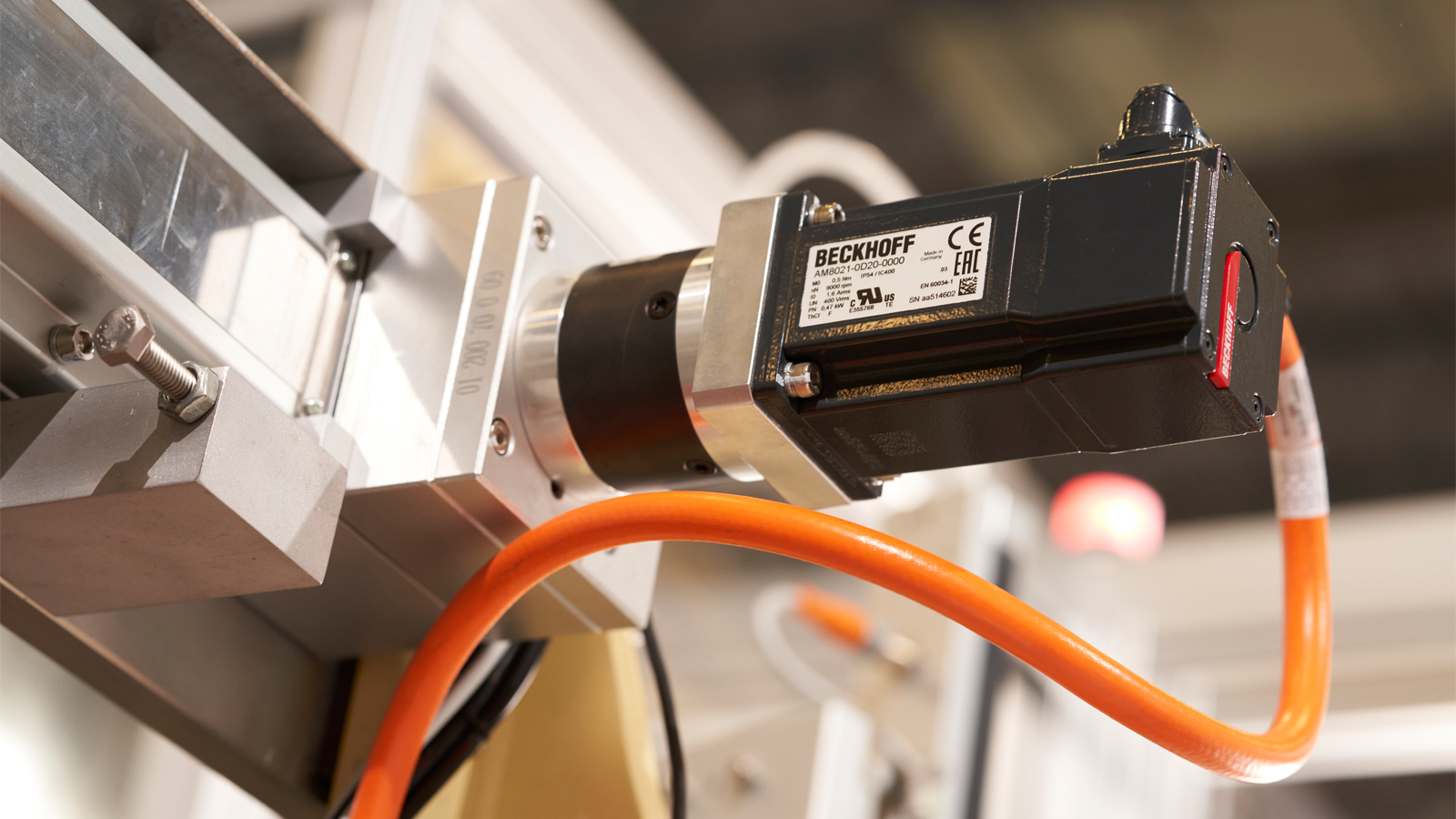
Sodecia GTAC ist eine in London, Ontario, ansässige Automatisierungsgruppe unter dem Dach des portugiesischen Industriekonzerns Sodecia. 2021 erhielten die Automatisierer den Auftrag, eine Maschine für einen global agierenden Automobilhersteller weiterzuentwickeln. Die dritte Version des Montageautomaten für Sicherheitsgurt-Baugruppen sollte einen höheren Durchsatz liefern, und die Entwicklungszeit dafür war begrenzt.
Seit Jahren investiert GTAC Zeit und Ressourcen in die Entwicklung von standardisierten Steuerungsarchitekturen und modularem, wiederverwendbaren Code. „Auf der Grundlage unseres Bestands an Steuerungscode können wir Projekte, die normalerweise acht Monate bis ein Jahr dauern würden, in nur drei bis vier Monaten abwickeln“, sagt Chris Drees, Steuerungstechniker bei Sodecia GTAC. „Es bedeutet außerdem, dass jeder unserer Ingenieure problemlos Fehler im Code von Standard- oder Sondermaschinen beheben kann.“
So ist Sodecia für die pünktliche Einhaltung von engen Lieferfristen bekannt. Ein Wettbewerbsvorteil, der laut Brent Lekx-Toniolo, einem der Gründer des vormals eigenständigen Unternehmens GTAC, aus der Not heraus geboren wurde. „Um das Jahr 2000 herum entwickelten wir das Framework-Konzept, weil unsere Kunden häufig Maschinen mit einer sehr kurzen Time-to-Market bestellten“, erklärt Lekx-Toniolo. Im Jahr 2007 entdeckte GTAC die Vorteile der Steuerungs- und Netzwerktechnologie von Beckhoff für das geplante Framework. „Nach einigen Fehlversuchen mit anderen Steuerungsplattformen erwies sich PC-based Control dann als ideal“, fügt Brent Lekx-Toniolo hinzu. „Seitdem ist Beckhoff bei uns im Haus der Standard.“
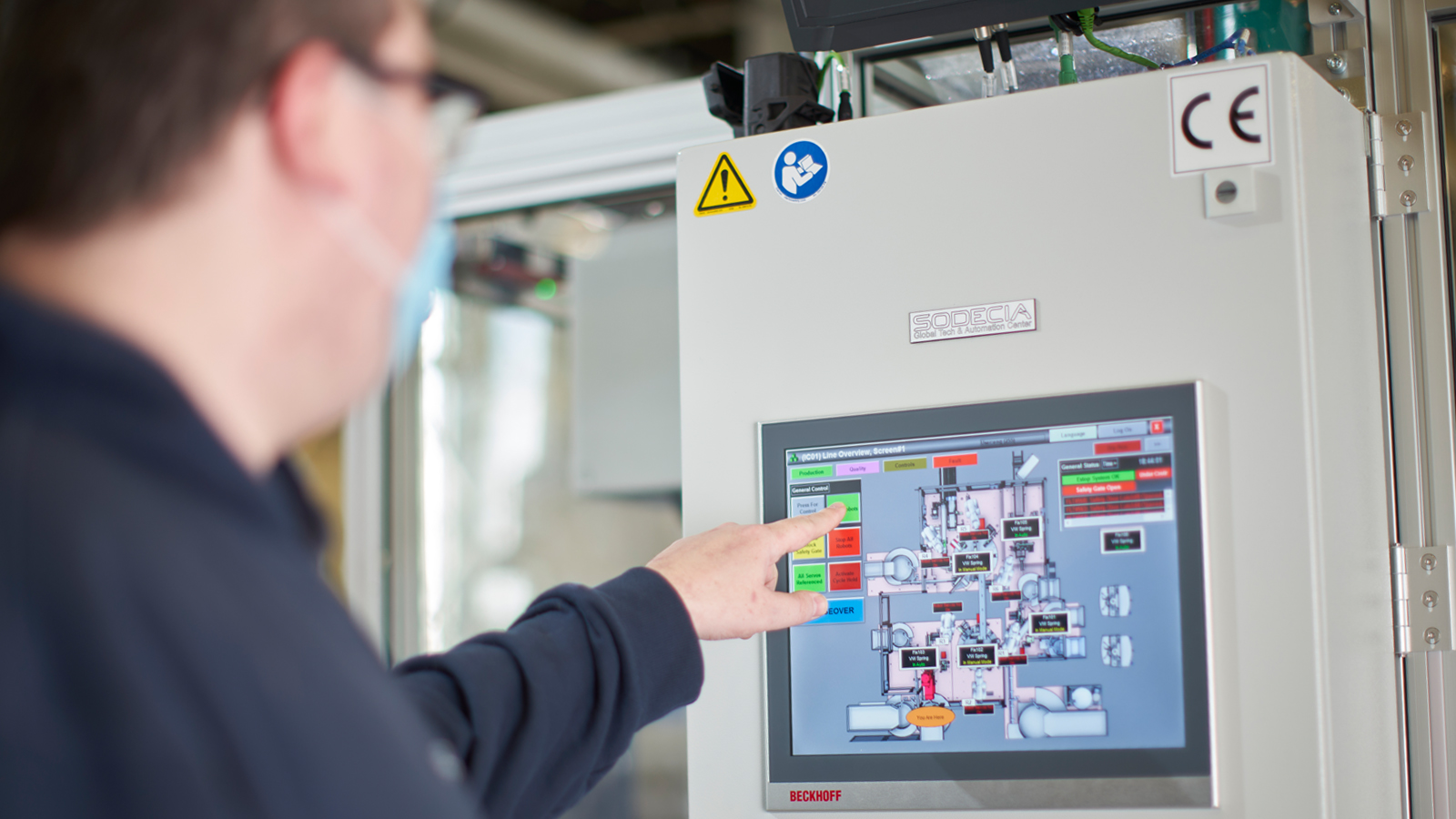
Finetuning mit Standardcode
Der Mutterkonzern Sodecia übernahm viele Innovationen der Automatisierer in seine eigenen Standards für die fast 40 Fertigungsstätten des Unternehmens in aller Welt. Dort haben sich diese bei Konstruktion, Programmierung und Inbetriebnahme automatisierter Montage- und Schweißlösungen für den Automobilmarkt bewährt. „Im Vergleich zu den Schweißmaschinen mit großen Robotern zeichnet sich der Seat Belt Height Adjuster (SBHA#3) jedoch durch wesentlich schnellere Montageprozesse auf kleinerer Grundfläche aus“, sagt Jessy Underhill, SPS- und Robotikingenieur bei Sodecia GTAC. „Aber durch Anpassungen unseres Standardcodes konnten wir auch solche Funktionen abdecken, z. B. für die Steuerung des Rundschalttischs mit servobasierten Antrieben und die Datenübertragung.“ Chris Drees fügt hinzu: „Außerdem wollten wir die jüngsten Updates aus unserem Standardcode nutzen, um die Verfügbarkeit, die Gesamtanlageneffektivität und andere Eigenschaften zu verbessern sowie die Funktionalität zu erweitern.“
Die neue Anlage besteht aus fünf Abschnitten. In zwei Unterstationen wird der Knopf zur Aktivierung der Gurtverstellung montiert – ein kleiner Aktuator mit einer Feder. Anschließend wird diese Baugruppe in eine kleine Stahlplatte mit einer Mutter eingesetzt, die später auf einer Stahlschiene auf- und abgleitet. Im vierten Abschnitt wird diese Baugruppe in die Schiene zur Montage am Fahrgestell des Fahrzeugs eingebaut. Der letzte Abschnitt dient der Qualitätssicherung durch Höhen- und Belastungsmessungen an den Komponenten. Dazu verfügt das System über zwei Servoantriebe und vier Servomotoren, zwei Bildverarbeitungskameras, fünf Frequenzumrichter, sechs KUKA-Roboter, 13 Druckluft-Magnetventilinseln und mehr als 100 I/O-Komponenten. Eine effiziente Echtzeitsteuerung und -kommunikation war dafür entscheidend.
Ursprünglich bestand die Montageanlage aus separaten Zellen, die durch Einrichtungen für den Transport der Werkstücke verbunden waren. Bei der ersten Modernisierung reduzierte GTAC die Grundfläche der Maschine bereits auf fast die Hälfte, d. h. nur noch etwa 6 x 6 m. „Die ersten beiden Modelle produzierten alle 5,4 s ein Teil, aber bei der neuen Version sollten wir diese Zeit auf 5,1 s senken“, erklärt Chris Drees.
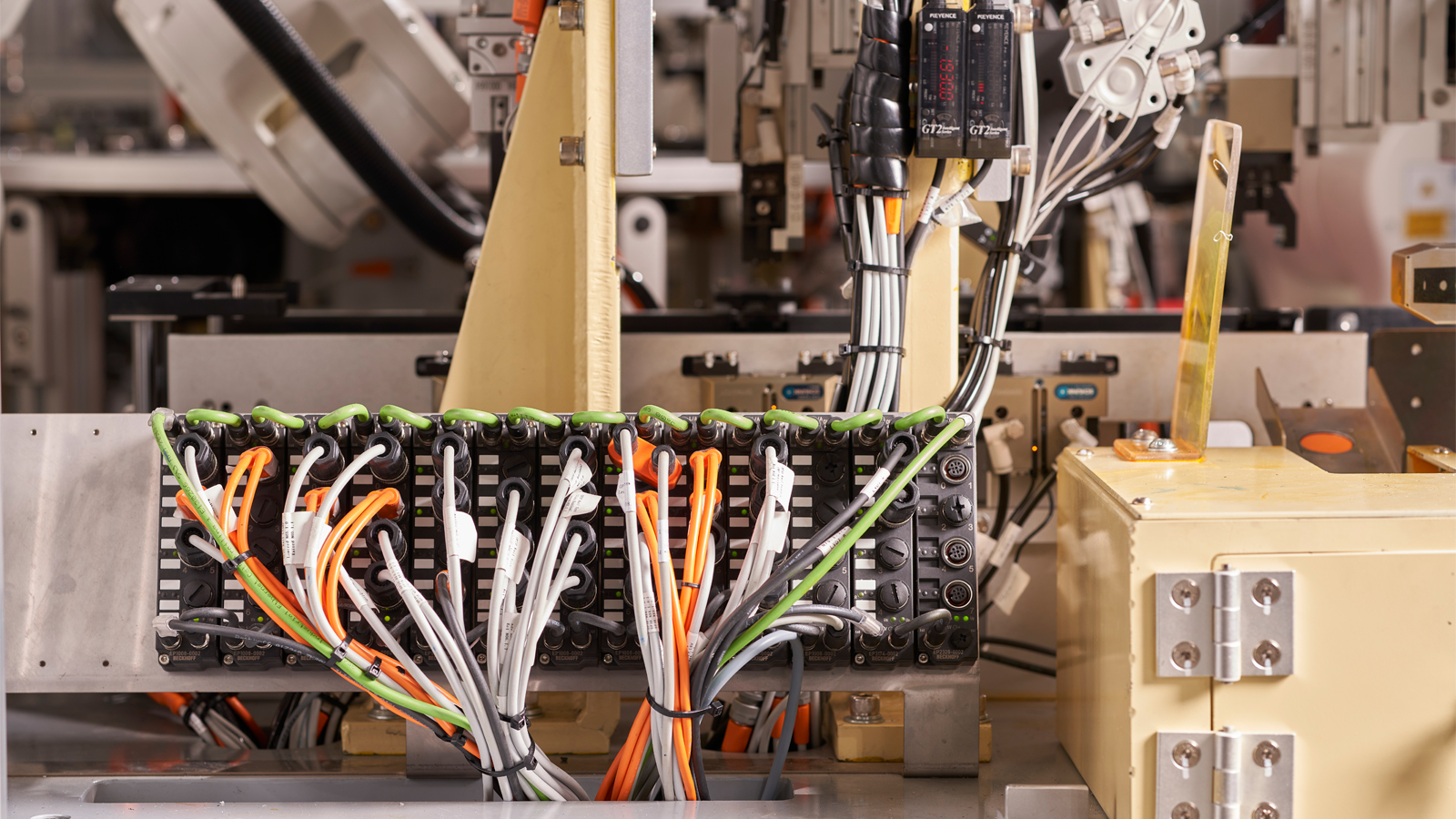
PC- und EtherCAT-basiert steuern und bewegen
Die PC-basierte Automatisierung nutzt die Software TwinCAT 3 als flexible Plattform zur Steuerung aller Maschinenprozesse von SPS und Roboterkinematik bis zu funktionaler Sicherheit und IoT. Neben TwinCAT kann auch andere Software auf der PC-basierten Maschinensteuerung laufen. Die TwinCAT-Engineering-Umgebung ist vollständig in Microsoft Visual Studio® integriert. Sie ermöglicht es den GTAC-Ingenieuren auch, in den Sprachen zu programmieren, mit denen sie am besten vertraut sind oder die sich am besten für die jeweilige Anwendung eignen. Die TwinCAT-Runtime läuft auf einem Panel-PC CP2215 von Beckhoff, der gleichzeitig als Maschinensteuerung und Benutzeroberfläche dient. Der 15-Zoll-Multitouch-Bildschirm unterstützt die intuitive Bedienung, Diagnose sowie Fehlersuche im SPS-Code.
Als idealer Motion-Bus bildet EtherCAT die Grundlage für kurze Zykluszeiten der Beckhoff Servoverstärker AX5000 sowie für Frequenzumrichter von Drittanbietern und die KUKA-Roboter. „KUKA setzt auf EtherCAT, was nicht nur die Kommunikation vereinfacht, sondern wir können auch Safety over EtherCAT (FSoE) für die Maschinensicherheit nutzen“, so Chris Drees. Das TÜV-zertifizierte Sicherheitsprotokoll macht festverdrahtete Sicherheitssteuerungen an jedem Not-Halt, jeder Lichtschranke und anderen Sicherheitseinrichtungen überflüssig. Zudem verschlankt FSoE die Verkabelung, denn es nutzt für die Übertragung von Sicherheitsdaten die gleichen Ethernet-Kabel wie für Standard-I/O-Daten. Die AX5000-Antriebe sind mit einer TwinSAFE-Optionskarte AX580x für Sicherheitsfunktionen direkt im Antrieb ausgestattet.
Die GTAC-Ingenieure sehen in der robusten Diagnosefunktion von EtherCAT einen weiteren großen Vorteil. „Als ich auf EtherCAT umgestiegen bin, war ich erstaunt, wie einfach es war, Störungen und Fehler zu beheben“, sagt Danilo Silva, Leiter der Steuerungsabteilung bei Sodecia GTAC. „Bei anderen Feldbussen war das sehr schwierig. Mit EtherCAT kann man jedes Problem diagnostizieren, genau lokalisieren und es beheben.“ Mit Schnittstellen zu mehr als 30 bekannten Feldbussen und Kommunikationsprotokollen vereinfacht EtherCAT auch die Integration anderer Geräte, wie z. B. der Bildverarbeitungskameras über EtherNet/IP durch den Einsatz eines Buskopplers EK9500. Zusammen mit einer Vielzahl von EtherCAT-I/Os in hutschienenmontierbarer IP20- oder maschinenmontierbarer IP67-Ausführung lieferte dies die richtige Lösung für alle Anforderungen der Anlage.
Gurtmontage auf Hochtouren
Die GTAC-Ingenieure erzielten beeindruckende Ergebnisse mit der neuen Sondermaschine. Die Automatisierungssoftware TwinCAT ermöglichte es Sodecia, wichtige Aktualisierungen am vorhandenen Code vorzunehmen, und diese erwiesen sich als wirksame Vorteile. Die SBHA#3 erfüllt die geforderte Durchsatzrate von 5,1 s pro Teil bei beeindruckenden Abtastraten von 125 µs in der Maschinensteuerung. Auch der enge Zeitplan wurde eingehalten: Start war im September 2021, Inbetriebnahme im März 2022.
Bei dem Projekt arbeitete Sodecia eng mit dem lokalen Team von Beckhoff Kanada – dem regionalen Vertriebsleiter Dean Herron und Applikationsingenieur Jim Fallowfield – zusammen. „Beckhoff und Sodecia wurden beide in den 1980er-Jahren gegründet, und wir verfolgen ähnliche Ansätze der kontinuierlichen Technologieentwicklung“, erklärt Dean Herron. „Der modulare und flexible Ansatz von Sodecia geht Hand in Hand mit unserer PC-basierten Steuerungsphilosophie. Dadurch konnte das Team von Sodecia die Soft- und Hardwareentwicklung erheblich einfacher gestalten.“