eXtended Transport System (XTS) bei der Qualitätsprüfung von zylindrischen Blechteilen durch optische Inspektion
Gefasoft entwickelte eine besonders kompakte Prüfanlage zur optischen Kontrolle von zylindrischen Blechteilen. Mit ihr werden Diffusoren für Kfz-Airbags in insgesamt elf Kamerastationen mit variablen Inspektionszeiten zuverlässig geprüft. Dabei konnte man durch den hochflexiblen Bauteiltransport per XTS die einzelnen Prüfprozesse des komplexen Testablaufs parallelisieren und so den Produktausstoß optimieren.
Typischerweise sind bei der automatischen optischen Bauteilinspektion eine Reihe von Kameras in mehreren nachgeschalteten oder parallelen Kontrollstationen erforderlich, um bei komplexen Bauteilgeometrien alle Prüfkriterien abdecken zu können. Dies gilt auch für die Prüfanlage Sova-VIS 16 der Gefasoft Automatisierung und Software GmbH in Regensburg, die Diffusoren für Kfz-Airbags prüft. Diese becherförmigen, tiefgezogenen Stahlblechbauteile, in verschiedenen Varianten mit etwa 60 mm Durchmesser, müssen als sicherheitskritische Bauteile vor der Weiterverarbeitung einer umfangreichen Oberflächenkontrolle der Innen- und Außenseite unterzogen werden.
XTS gleicht Zeitunterschiede aus und erleichtert Erweiterungen
Während manche der Prüfaufgaben lediglich eine einzige Aufnahme erfordern, setzen andere Anforderungen aus dem Fehlerkatalog eine ausgeklügelte Beleuchtungstechnik mit mehreren Bildaufnahmen voraus. Vor allem die Innenwand des Diffusors ist eine kritische Funktionsfläche, die detailliert auf kleinste Fehlstellen mit Abmessungen von einigen 10 μm in der Stahloberfläche geprüft werden muss. Um die dafür erforderliche Bildauflösung zu erreichen, werden Zeilenkameras eingesetzt, vor denen das Werkstück abgedreht wird. Speziell das vollständige Abdrehen des Werkstücks erfordert etwas mehr als 2 s Aufnahmezeit. Damit ergibt sich eine sehr inhomogene Verteilung der Bildaufnahmezeiten zwischen den einzelnen Prüfstationen.

Wären alle Kamerastationen mit einem starren Transportsystem – z. B. mit einem Rundschalttisch – verkettet, würde die Station mit der längsten Bildaufnahmedauer die kürzeste Taktzeit des Transportsystems bestimmen und damit den Produktausstoß limitieren. Mit XTS als äußerst flexibler Lösung lassen sich hingegen schnellere Prüfstationen sequenziell bedienen, während langsamere und daher mehrfach vorhandene Stationen entsprechend parallelisiert mit Bauteilen versorgt werden. Dazu erläutert Gefasoft-Marketingmanager Georg Schlaffer: „Bei der Prüfanlage Sova-VIS 16 führte die sehr heterogene Bildaufnahmezeit der einzelnen Prüfschritte zur Suche nach einem Maschinenkonzept mit flexiblem, asynchronen Bauteiltransport, mit dem die gestellte Aufgabe bei begrenzten Platzverhältnissen elegant gelöst werden kann. XTS von Beckhoff mit seinen unabhängig ansteuerbaren Movern erfüllt diese Anforderungen auf überzeugende Art und Weise. So kann, trotz einzelner Prüfstationen mit längeren Testzeiten, insgesamt eine mittlere Taktzeit von 1,9 s pro Bauteil erreicht werden. Durch den Einsatz von XTS war es zudem möglich, einen gegenüber anderen Lösungen deutlich kleineren Anlagen-Footprint zu realisieren und so den Platzanforderungen des Endkunden zu entsprechen.“
Christian Schärtl, Direktor Engineering von Gefasoft, ergänzt: „Der Endkunde hat wegen des hohen Bedarfs an diesen Bauteilen eine Taktzeit von unter 2 s vorgegeben. Zwei der Prüfungen dauern aber fast 4 s, d. h. diese Stationen mussten dupliziert und parallelisiert werden, um die Vorgabe erfüllen zu können. Durch die Flexibilität von XTS ist dies auf einfache Weise möglich. Alle Lösungen mit Werkstückträgern und Weichen, auf der Basis von Bändern oder Ketten, wären mechanisch ungleich komplexer gewesen und sie hätten bei deutlich mehr Platzbedarf die 2 s Taktzeit vermutlich nicht erreicht.“
Aufgrund der vielen erforderlichen Kamera-Prüfstationen ergibt sich eine umlaufende Länge der XTS-Transportstrecke von ca. 11 m, auf der insgesamt 30 Mover bewegt werden. Die Transportstrecke wurde wegen der vergleichsweise schweren Mover mit einem speziellen Führungssystem von Hepco ausgerüstet. Die bewegte Masse von ca. 4 kg pro Mover ergibt sich aus den Anforderungen an die Bauteilaufnahme mit Hub- und Dreheinheiten. Denn die Diffusoren müssen sich vor den Zeilenkameras exakt drehen und für die Kontrolle der Ober- und Unterseite in zwei Lagen („Hut“ oder „Becher“) transportieren lassen.
Ziel war von Anfang an eine einzige Prüfmaschine, mit der sich die bisherige visuelle Prüfung der Diffusoren vollständig automatisieren lässt, beginnend mit der automatisierten Entnahme aus einer Palette bis hin zum Abstapeln bzw. Sortieren per Roboter. Eine alternative Auftrennung der Prüfaufgaben in mehrere unabhängige Anlagen war für den Endkunden nicht wirtschaftlich darstellbar. Neben der komplexen Logistik zwischen den Anlagen und dem erhöhten Platzbedarf wären hier auch die Vereinzelung und Zuführung der Diffusoren aus Schüttgutbehältern sehr aufwändig. Außerdem bietet XTS laut Georg Schlaffer einen zusätzlichen Vorteil: „Mit XTS lassen sich weitere Arbeitspositionen entlang der Strecke flexibel einbinden. Damit ist eine Anpassung an mögliche künftige Aufgabenstellungen sichergestellt.“
Eine Prüfanlage für den kompletten Prozess
Die Bauteile werden der Prüfanlage in Schüttgut-Gitterboxen zugeführt, nachdem zuvor die Oberfläche entfettet wurde. Ein Greifer übergibt sie dann einzeln von einem Zuführband an das XTS. Dabei erfordert die Werkstückaufnahme im XTS-Mover eine Ausrichtung der Drehlage des Bauteils. Hierfür ist eine Kamerastation in der Übergabeposition integriert, mit der die Winkelausrichtung des Werkstücks detektiert sowie zusätzlich die Typvariante des Diffusors überwacht wird. Auf der Oberseite des Diffusors ist ein Zeichen zur Chargenkennung eingeprägt, welches in einer ersten Kamerastation überprüft wird.
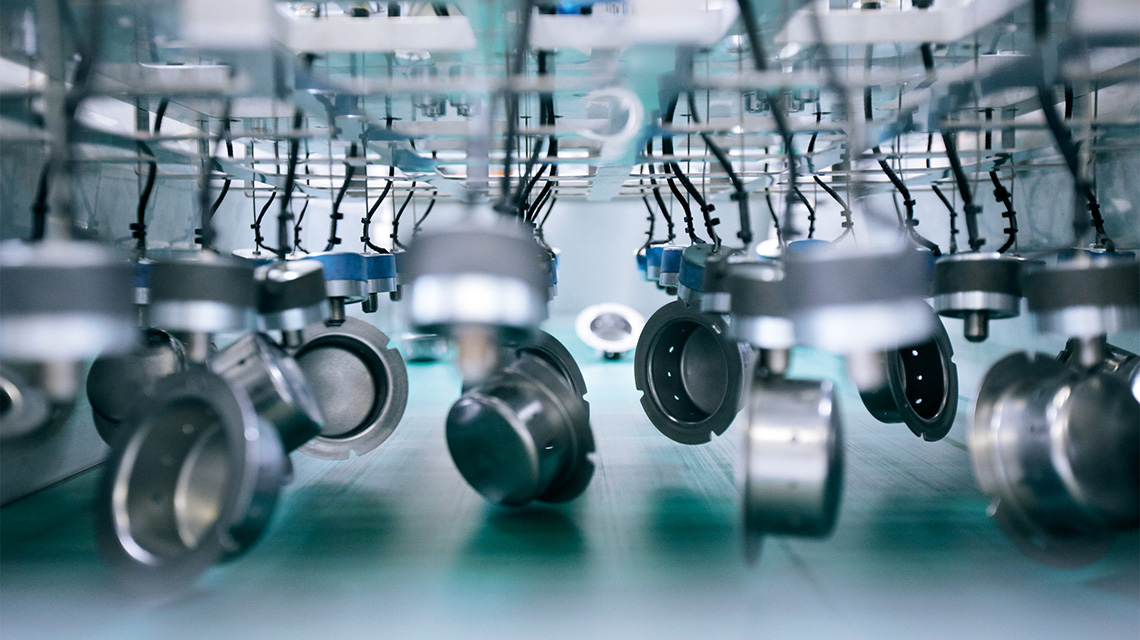
Nach der Kontrolle der Chargenkennung wird die Innenseite des Diffusors kontrolliert. Dazu ist es zunächst erforderlich, die Bauteile im Mover zu drehen, von der „Hut“- in die „Becher“-Ausrichtung, also mit der Öffnung nach oben. Die Bauteile werden dazu mit einem Greifer vom Mover abgehoben, um 180° gedreht und wieder auf dem Mover abgesetzt. Zwischenzeitlich wurde bei diesem der Innendorn zurückgezogen, sodass das Bauteil über seinen Außendurchmesser zentriert und auf dem Flansch aufliegend fixiert ist. Der Oberflächenkontrolle dient hier eine Zeilenkamera, vor der die Innenwand des Bauteils abgedreht wird. Dazu Christian Schärtl: „Eine Herausforderung war der eingeschränkte Platz, weil vier Beleuchtungsrichtungen und die Kamera innerhalb des innen ca. 60 mm durchmessenden Bauteils Platz finden mussten. Die Lösung bestand einerseits im Design einer integrierten Beleuchtungs- und Kameraeinheit, die in das Bauteil eintaucht, während ein Servomotor von außen an den drehbaren Dorn im Mover ankoppelt. Hinzu kam die Entwicklung einer schnellen Ansteuerungselektronik für die Beleuchtung. Das Zustellen der Beleuchtungseinheit in das Bauteil und das Abdrehen dauern etwas mehr als 2 s. Für das Erreichen des Linientaktes von 1,9 s ist diese Prüfstation daher doppelt ausgeführt.“
Auf die Wendestationen folgen eine Kontrollstation für Materialabweichungen auf der Innenseite und eine Station zur Prüfung des Diffusorbodens. In einer letzten Kamerastation an diesem ersten linearen Abschnitt des XTS-Systems wird der Flansch des Bauteils auf Fehler geprüft. Damit gibt es sechs Kamerastationen entlang des ersten linearen Abschnitts, wobei die Zeilenkamera-Stationen zur Innenwandkontrolle ebenso wie die Wendestationen doppelt vorhanden sind – insgesamt sind also neun Arbeitspositionen realisiert.
Nachdem die Mover die 180°-Kurve des XTS durchfahren haben, werden auf der rückläufigen linearen Strecke weitere Kamerastationen sowie eine Druckstation zum Markieren der geprüften Bauteile bedient. Zunächst werden die Teile am Mover von der „Becher“- in die „Hut“-Orientierung gewendet, bevor in einer ebenfalls doppelt ausgeführten Zeilenkamerastation die Außenwand des Bauteils abgedreht wird. Abschließend folgen die Prüfung der Flanschoberseite, ein mit der Bewegung der XTS-Mover synchronisierter Inkjet-Drucker zur kameraüberwachten Kennzeichnung fehlerhafter Bauteile und ein Laser-Beschrifter zur Codierung der Gut-Teile. Am Ende der zweiten linearen XTS-Strecke werden die Bauteile von einem Fastpick-Roboter Stäubli TP80 dem Mover entnommen und für die Weiterverarbeitung abgelegt.