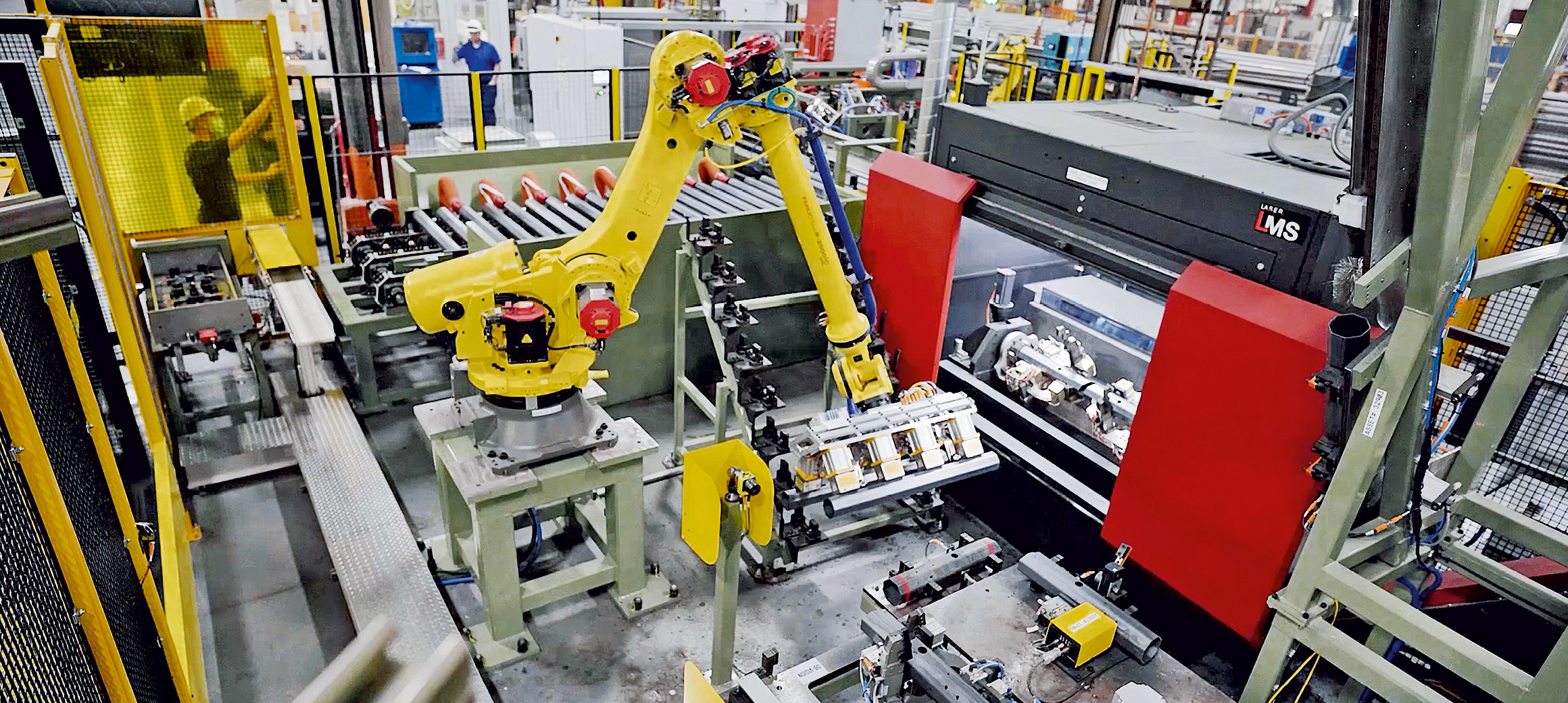
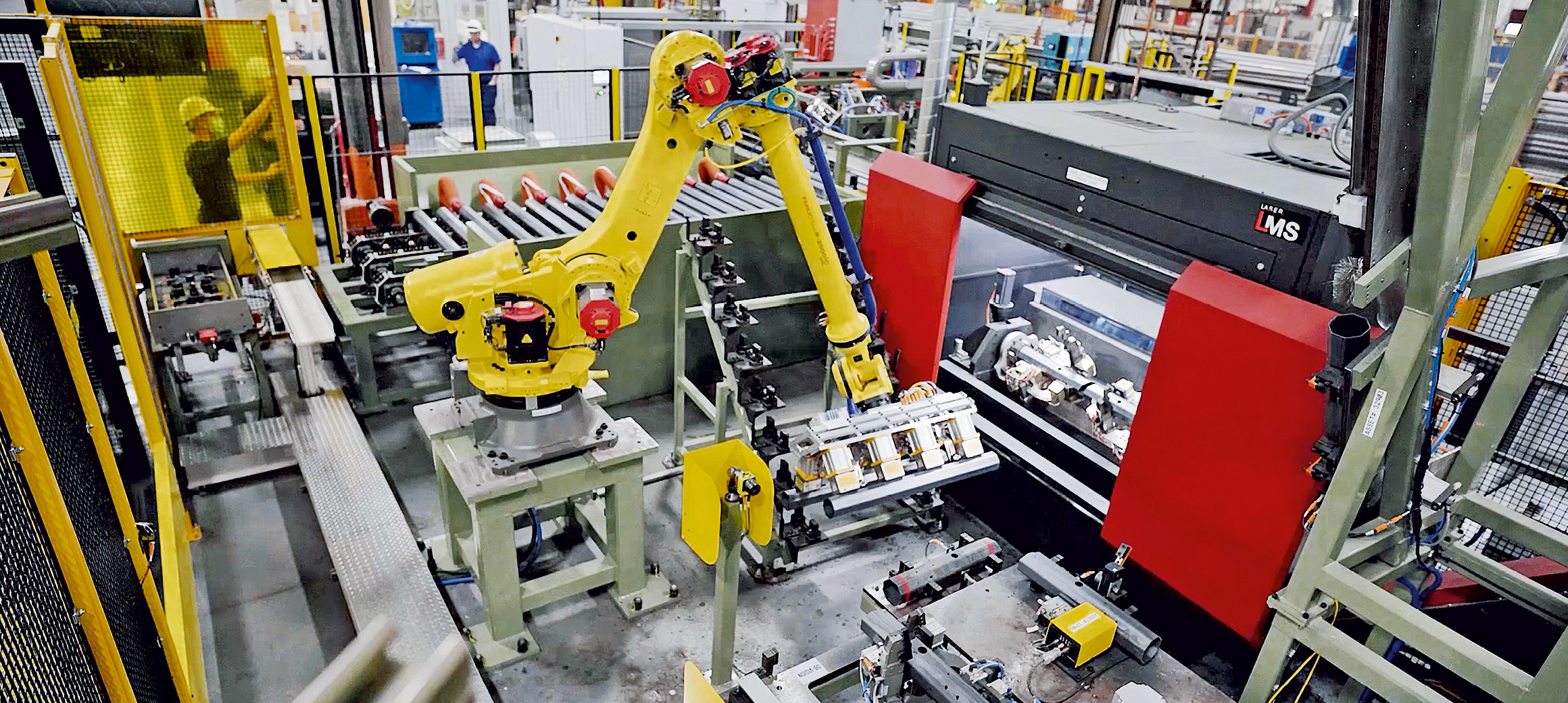
EtherCAT and PC-based automation in turnkey solution for auto manufacturer
BOS Innovations implemented its L-MS fiber laser cutting system as a turnkey solution for a leading automotive manufacturer. Drive technologies from Beckhoff enable precise coordination of the up to five cutting axes and ensure that the high-performance machine stays within tight tolerances. In addition, flexible PC-based control technology allows adaptation to different customer requirements.
As both a machine builder OEM and system integrator, BOS Innovations Inc. in Dorchester, Ontario, combines its strength in delivering turnkey machines with the ability to develop solutions to retrofit and tie into existing factory lines. “For 25 years, we have collaborated with major North American manufacturers to develop innovative, profit-driven solutions for automotive and other heavy industries,” says Ben Huigenbos, President of BOS. “We have developed core competencies in automated assembly, advanced robotics including welding, laser processing, coordinated motion technology, collaborative robots and quality inspection.”
These capabilities were clear in an implementation of the Laser-Motion System (L-MS) for a tier-1 automotive manufacturer. The L-MS is an advanced fiber laser cutting machine, equipped with a direct drive linear motion system for precision CNC processes. This high-performance machine produces complex parts with tight tolerances by leveraging up to five axes of coordinated motion. “To make this L‑MS a truly turnkey system, we needed to add a robot to load and unload the parts and move them to stations for de-burring, vision inspection and marking,” says Steve Van Loon, Technology Manager – Laser and Motion Systems at BOS.
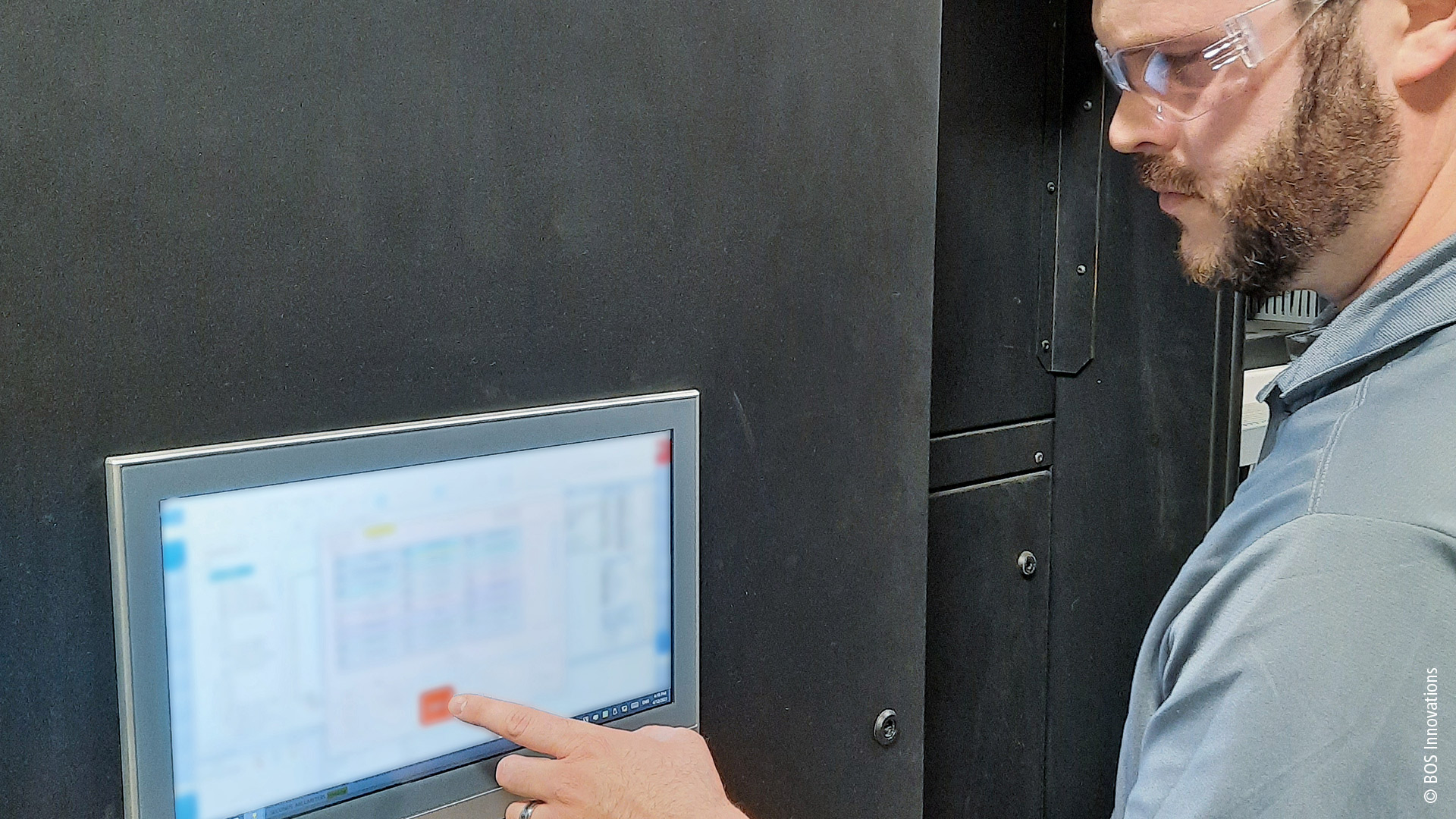
A laser focus on flexible and modular controls
To make sure the L-MS could support a best-of-both-worlds approach for many customers, BOS made flexibility and modularity top priorities in the initial design. In addition to a standard 1 kW fiber laser, the cutting head can accommodate up to two 0.5-6 kW laser sources or even welding (also remote welding). The machine has options for fume extraction equipment, automated scrap conveying, automatic doors and safety scanners for operator or robotic loading. For processing, the parts can sit on a flat bed or use a trunnion system with additional servo axes to rotate the workpiece 360 degrees. By adding such a turntable, the loading time can occur in parallel with the laser process. The flexibility even extends to footprint: The L-MS cell, a roughly 2-meter cube designed for 1,300-mm-long parts, can be expanded on all sides to accommodate workpieces of many sizes.
Providing this high degree of flexibility required robust yet above all adaptable controls and networking technologies that would allow the machine to integrate with other systems in the plant. Highly synchronized motor and drive technologies for the cutting axes were critical to ensure high part quality. Equally important was openness to enable real-time communication to the robot controller, de-burr components and vision system. To address this, Steve Van Loon worked with Mechanical Designers Riley Tomiuck and Scott McCall on the design. The team determined that the system required higher performance than a traditional fieldbus and hardware PLC could deliver, so they turned to solutions from Beckhoff.
“Anytime we face demanding servo applications, we work with Beckhoff, so it just made sense for the L-MS,” Van Loon says. BOS first implemented Beckhoff automation technologies a decade ago on a large cardboard converting system that had about 50 motion axes, and other projects followed. Then in 2018, the company used Beckhoff technology to build the first iteration of the L-MS, which was designed to cut SUV running boards, and became a standard offering in its portfolio. For this project, the team worked closely with the local Beckhoff team, Automation Sales Engineer Dean Herron and Application Engineer Rui Zhang.
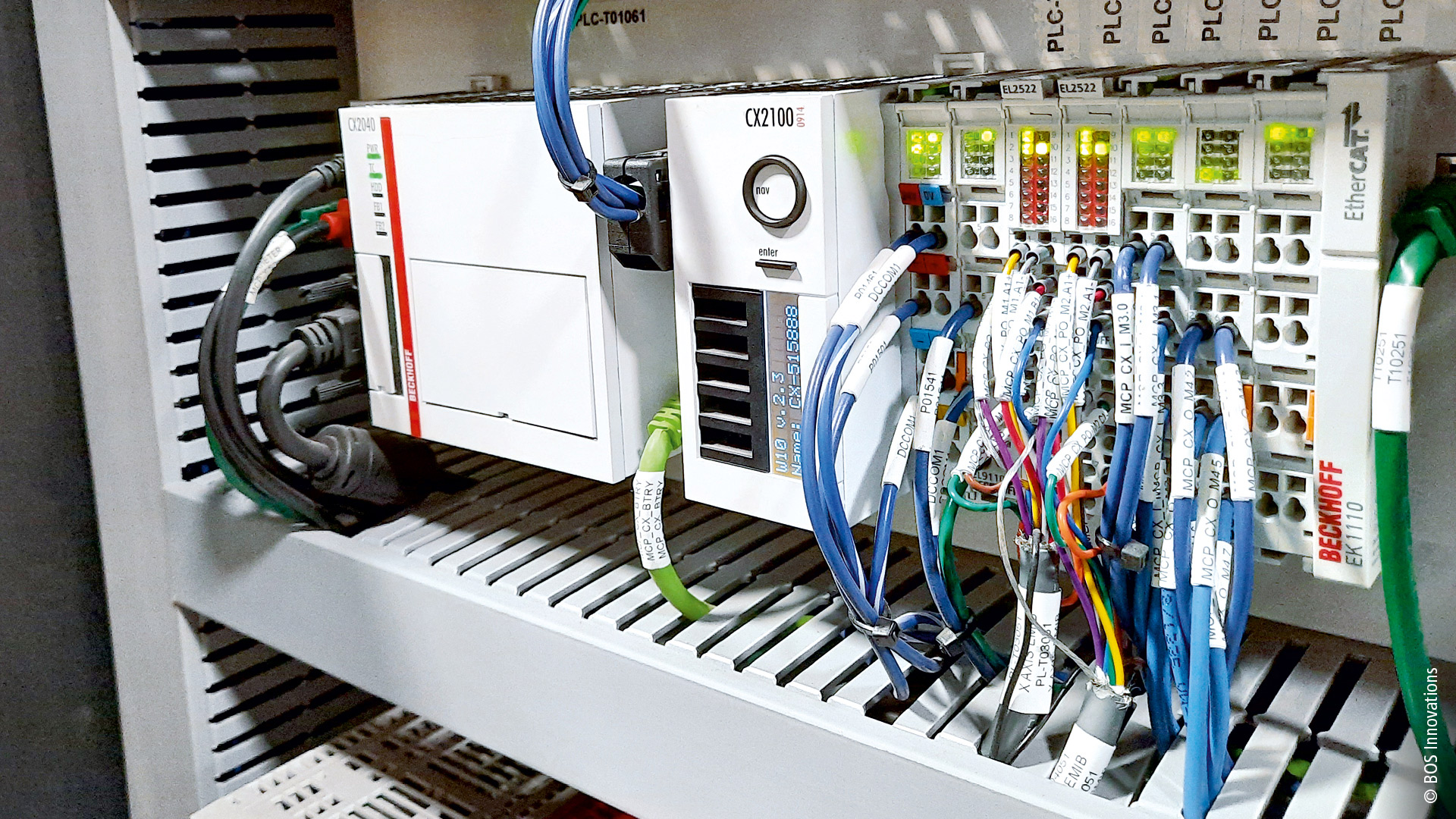
Motion control with EtherCAT makes the cut
BOS implemented precision motion control on the L-MS using a variety of rotary servomotor and direct drive solutions with EtherCAT communication. The machine processes octagonal steel tube parts of variable wall thicknesses, cuts a 21.5-degree angle on one end of each piece and handles two variants with either six or 12 holes while maintaining tight tolerances.
The horizontal axes use Beckhoff AL2800 series Linear Motors, which deliver speeds up to 6 m/s and peak forces up to 4,500 N. “The X and Y axes have highly dynamic requirements in terms of acceleration, speed and accuracy, which called for linear motors,” Steve Van Loon says. The automotive manufacturer’s machine featured a Z axis and a trunnion system, which both used AM8000 Servomotors. With fast control technology, the AX5000 Servo Drives are ideal to support the dynamic application, and they permitted easy integration of a smaller, third-party motor to control the theta axis on the cutting head. One Cable Technology (OCT) in the servomotors and the servo drives reduces the cabling effort.
“Each device uses the EtherCAT function of distributed clocks to deliver exact synchronization and jitter of less than 1 µs, which is optimal for coordinated motion systems like the L-MS,” Dean Herron explains. The broad EtherCAT I/O portfolio from Beckhoff is open to support communication to more than 30 protocols, and makes it easy to connect to other systems on the production line by adding an EtherNet/IP Bus Coupler, for example.
In addition to space-saving EtherCAT Couplers and I/O Terminals from Beckhoff, BOS also implemented TwinSAFE terminals for functional safety. This allows engineers to place safety technology directly within standard I/O segments, according to Rui Zhang: “BOS used the EL6900 TwinSAFE Logic terminal as a safety PLC on this machine. This approach allowed them to cut down the time and complexity otherwise required for hardwiring safety switches. All I/Os stay on the same rack or mount onto the machine with IP67 EtherCAT Box modules, and in addition, they could simply create safety logic in the standard TwinCAT engineering environment.”
TwinCAT allows engineers to select the programming languages they are most familiar with or that best suit the project. Here, they implemented TwinCAT PLC and CNC packages, and they appreciated the ability to use G-code, among other features. “TwinCAT Motion Designer was also very helpful for sizing the AM8000 series servomotors,” Steve Van Loon adds.
The control platform relies on a single Beckhoff CX2040 Embedded PC that features a quad-core Intel® Core™ i7 processor. A 15.6-inch CP2916 Control Panel provides multi-touch operator interface and high-resolution display, which is ideal for viewing the results from the vision inspection process, among other things.
Delivering the best of both worlds
The complete L-MS system went live in the end user’s facility in late 2020. With fast controls and automated loading, the machine achieves a part-to-part cycle time of 40 s or less. “The L-MS easily runs at 2 m/s with 1.25 g acceleration, and it cuts holes with the highest precision that the customer says they have ever seen,” Steve Van Loon sums up. “That’s due to the controller speed and the fine tuning we accomplished with TwinCAT Scope. Using the software oscilloscope, we could see all parameters on the screen and collect data from each axis, including following error, acceleration and deceleration, to optimize the system.”
“Coordinated motion requires a lot of data to be passed between the servo drives and motion planner. EtherCAT is really the only fieldbus capable of handling that,” Van Loon explains. The finished laser cutting machine met all requirements of the automotive manufacturer, and BOS is already building additional units for other customers.