Products
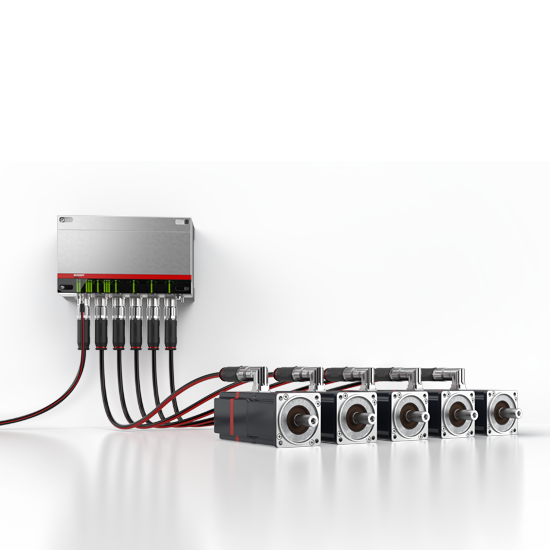
AMP8000 | Distributed servo drive system
Synchronous servomotor with integrated servo drive for control cabinet-free modular machine concepts.
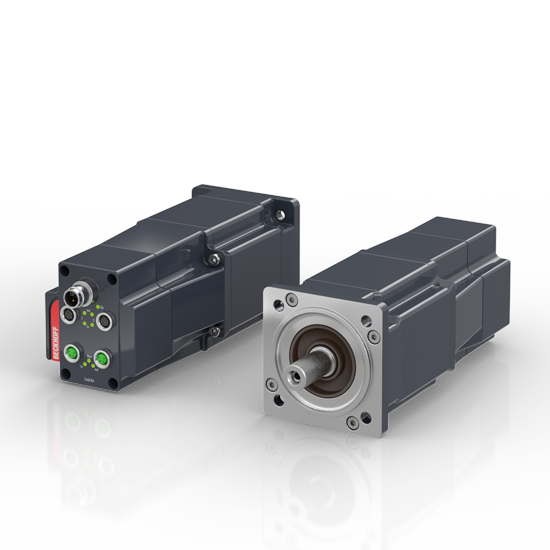
AMI8100 | Compact integrated servo drives
Synchronous servomotor with integrated servo drive for the realization of machine concepts without a control cabinet in the low voltage range.
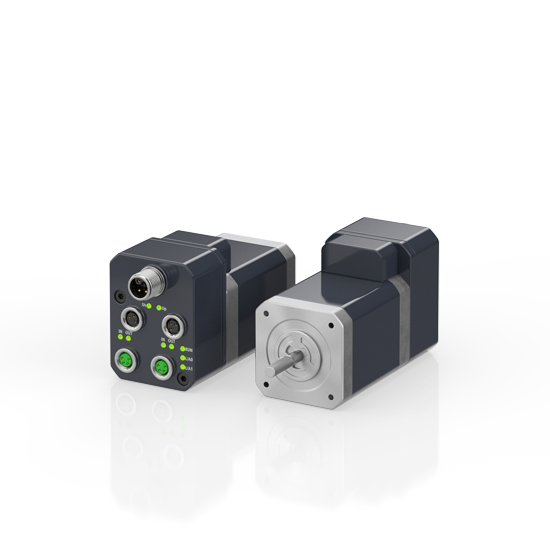
ASI8100 | Compact integrated stepper motor drives
Stepper motors with an integrated stepper motor output stage for low-voltage control cabinet-free machinery concepts.
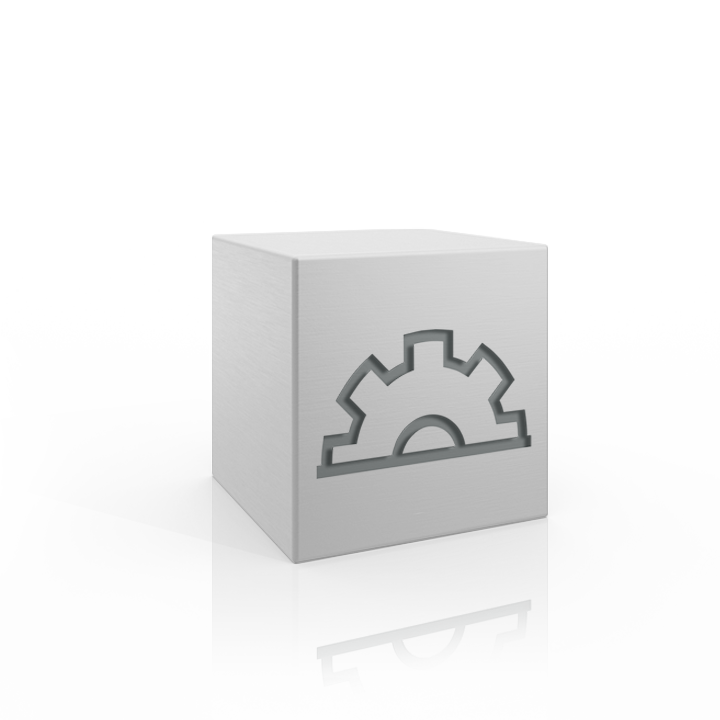
Software
The motion software products optimally support the selection and commissioning of suitable hardware components for drive solutions.
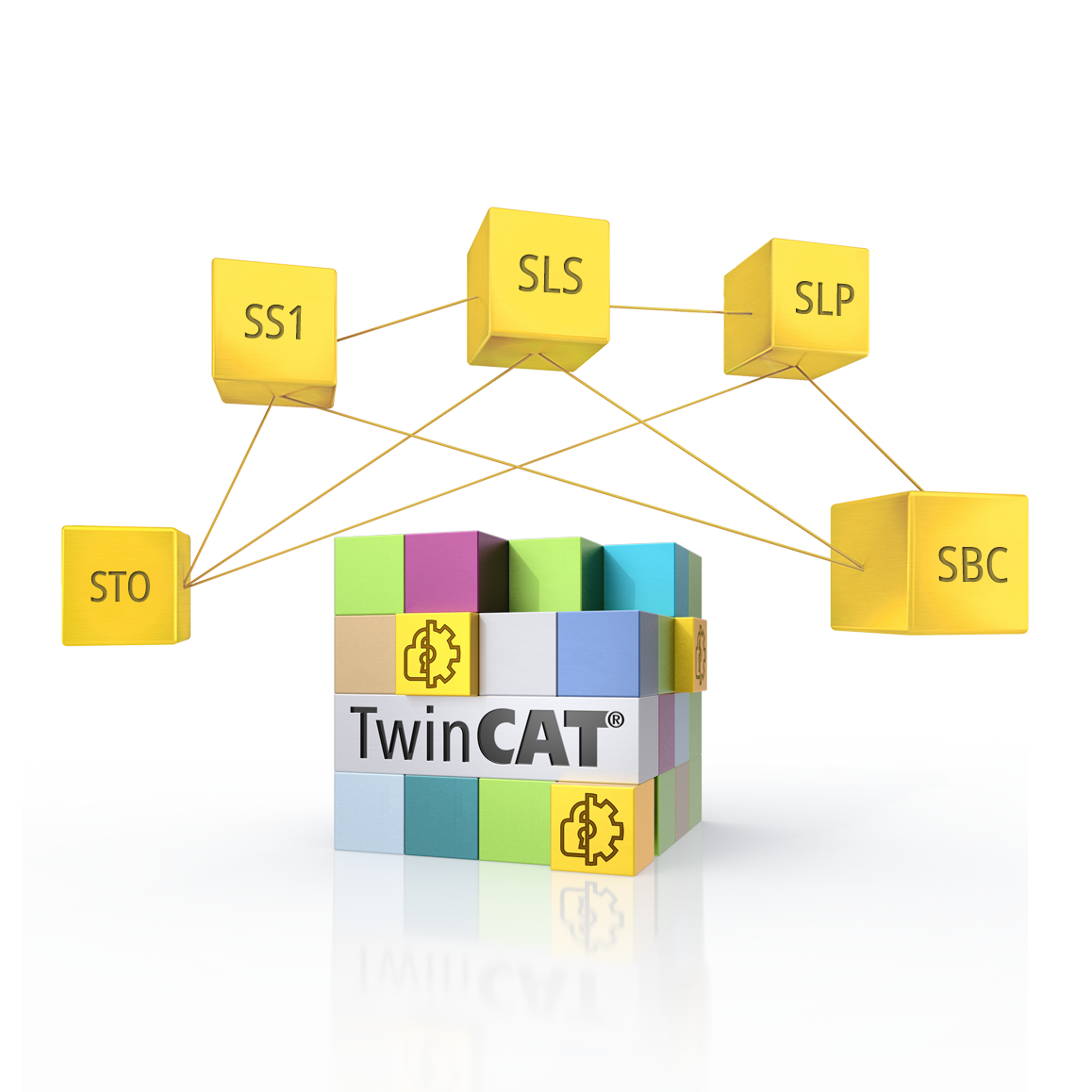
TwinSAFE safe drive technology
With the TwinSAFE safe automation technology, both basic functions and complex safety functions are available for all our drive solutions.
What is distributed drive technology?

In recent years, distributed drive technology has become a key part of automation and drive technology. It offers significant advantages over traditional centralized approaches, especially in terms of flexibility, scalability, and efficiency. Distributed drive technology moves drive components, such as servo drives or stepper motor terminals, out of the control cabinet and into the machine.
In contrast to centralized drive technology, in which all control and regulation components are housed in a central control cabinet, the components involved in distributed drive technology are installed directly in the housing of the motor.
Your head start with distributed drive systems from Beckhoff:
- control cabinet-free concepts
- space-saving, straightforward, and smaller footprint
- reduced material and labor costs
- simple wiring and low installation and commissioning costs
- EtherCAT system
- high level of modularity for system adaptations or extensions
- connection of additional I/O signals in IP65 configurations possible
The technology behind distributed drive technology
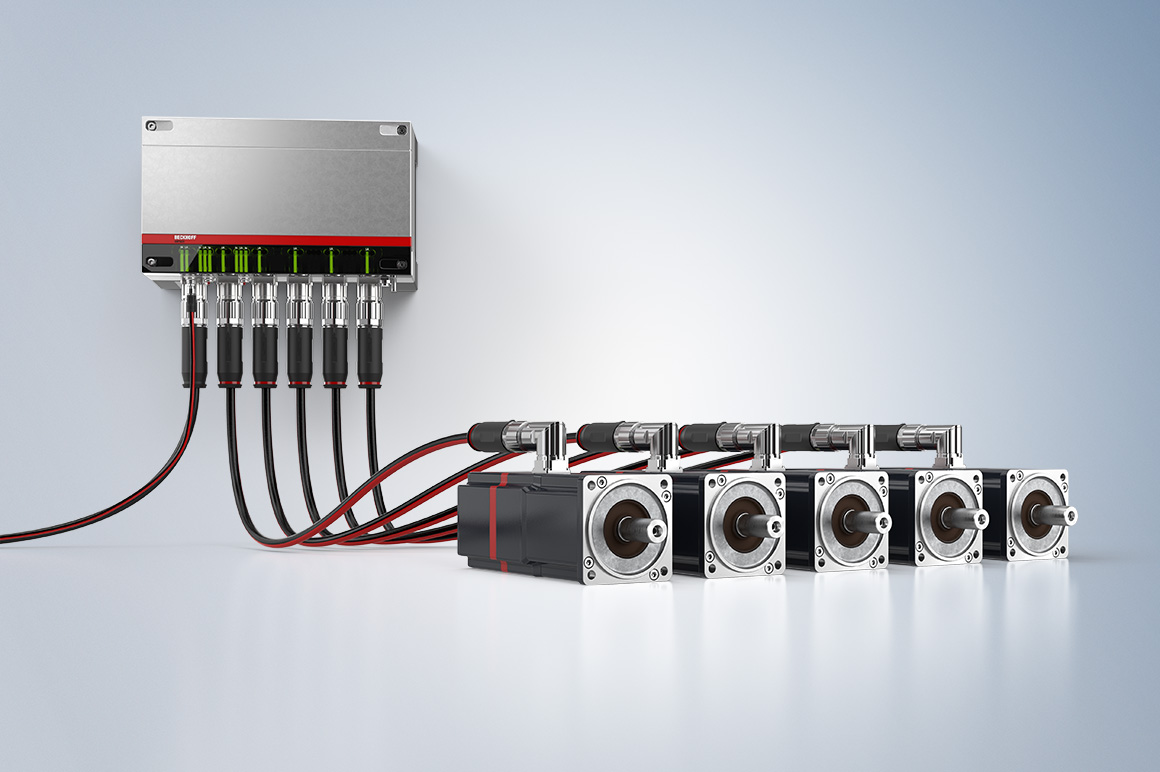
AMP8000 | Distributed servo drive system
- Power
- distributed servo drive: up to 2.6 kW
- distributed power supply module: 11 kW
- Standstill torque up to 11.8 Nm
- Voltage range
- 1 x 120…240 V AC
- 3 x 200…480 V AC
- Wiring
- Star wiring
- OCA wiring
- Safety
- TwinSAFE STO/SS1 or TwinSAFE Safe Motion
- via FSoE (FailSafe over EtherCAT)
- integrated TwinSAFE Logic
- Sizes
- F3, F4, F5
- Special features
- available with holding brake and additional inertia
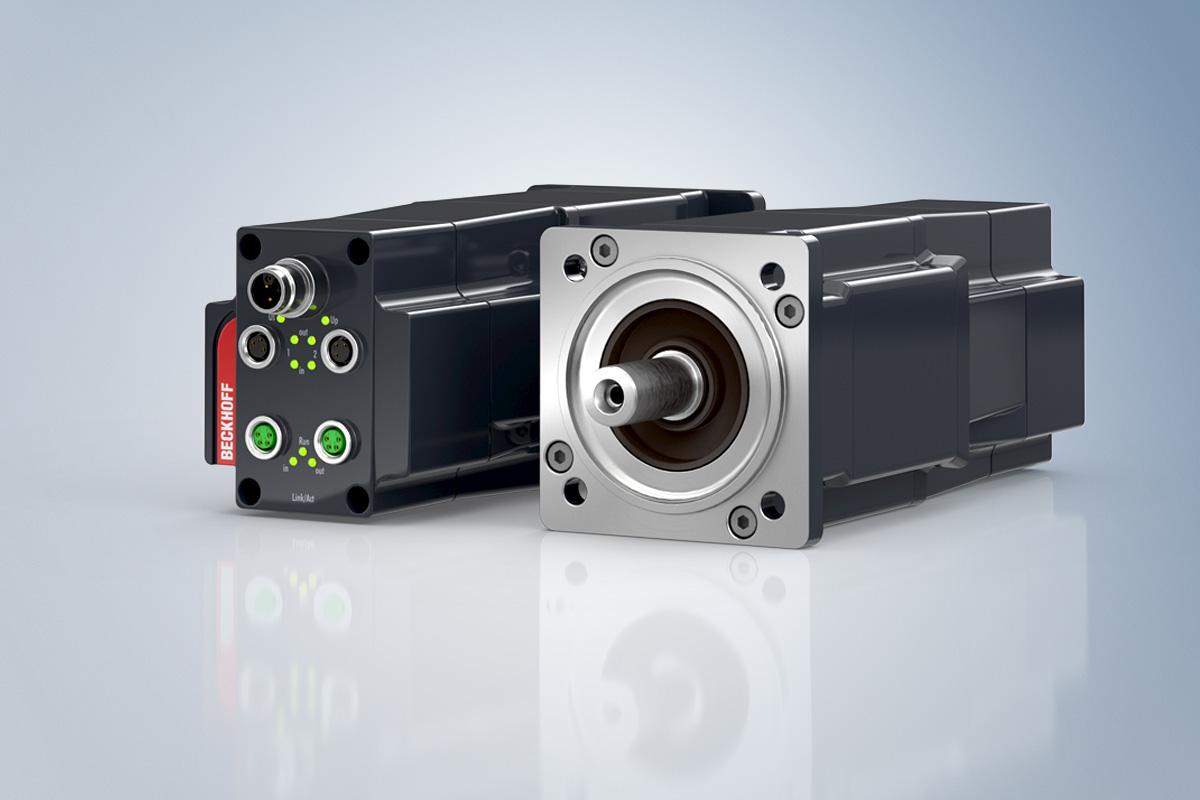
AMI8100 | Compact, integrated servo drives
- Power up to 0.35 kW
- Standstill torque up to 2.85 Nm
- Voltage range up to 48 V DC
- Wiring
- Daisy-chain wiring and star wiring possible
- Safety
- TwinSAFE STO/SS1
- via FSoE (FailSafe over EtherCAT)
- integrated TwinSAFE Logic
- Sizes
- F2, F3
- Special features
- two additional I/Os for drive-related functions with a voltage of 24 V DC
- integrated travel path control: direct control without NC possible via MDP protocol
- Operation on third-party masters is possible with DS402 protocol.
- available with holding brake
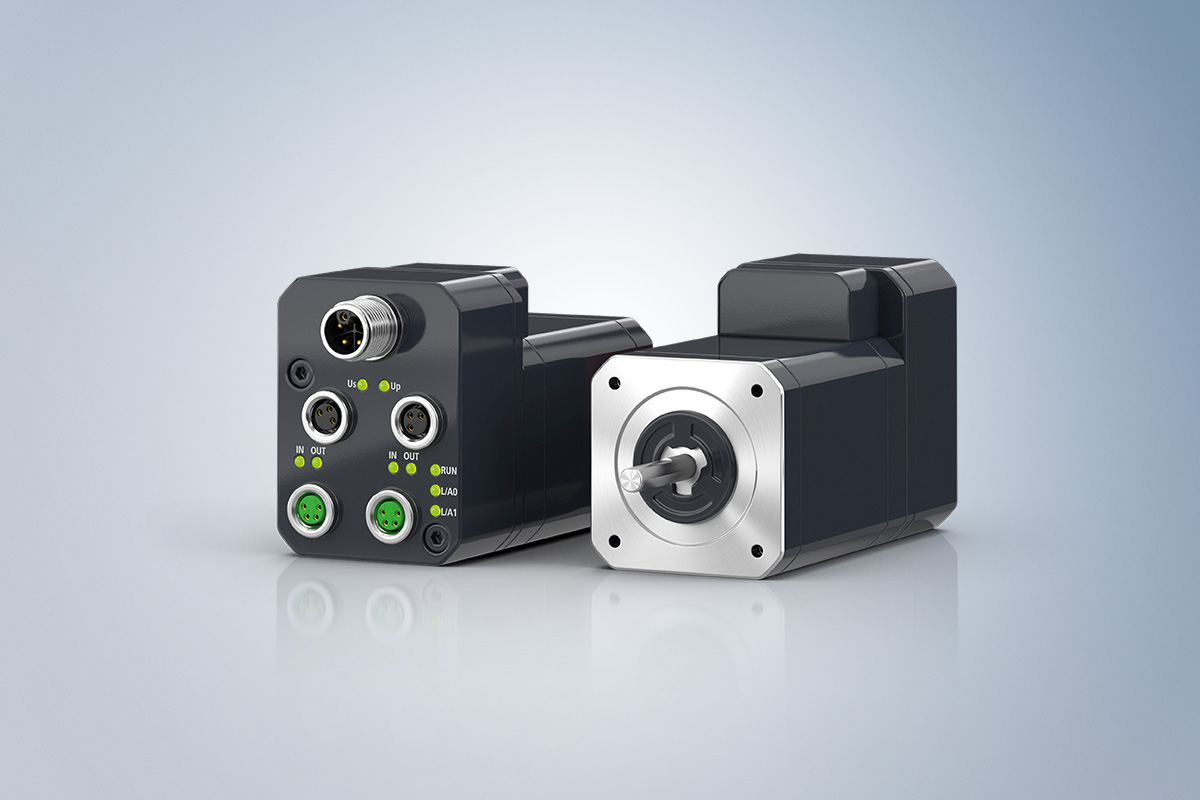
ASI8100 | Compact, integrated stepper motor drives
- Power up to 0.25 kW
- Holding torque up to 2.5 Nm
- Voltage range up to 48 V DC
- Wiring
- Daisy-chain wiring and star wiring possible
- No safety
- Sizes
- NEMA 17, NEMA 23 (in preparation)
- Special features
- two additional I/Os for drive-related functions with a voltage of 24 V DC
- integrated travel path control: direct control without NC possible via MDP protocol
- Operation on third-party masters is possible with DS402 protocol.

- Braking resistors
- AX2090-BW65 | External braking resistors for AMP8000
- EP9576-1032 | EtherCAT Box, brake chopper box for AMI8100 and ASI8100
- Power distribution
- ZS2030-4812 | T splitter for AMI8100 and ASI8100
- EP9208-1035 | Passive power distribution box for AMI8100 and ASI8100
- Pre-assembled cables
- Hybrid cables for AMP8000
- EtherCAT and fieldbus cables for AMI8100 and ASI8100
- Power cables for AMI8100 and ASI8100
- Sensor cables for AMI8100 and ASI8100
- Hybrid connector accessories for AMP8000