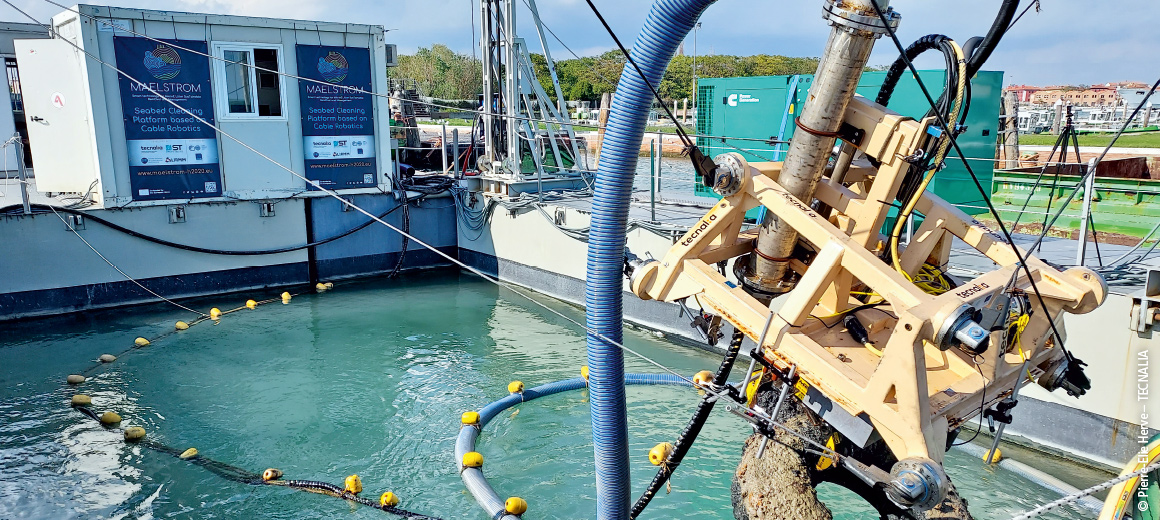
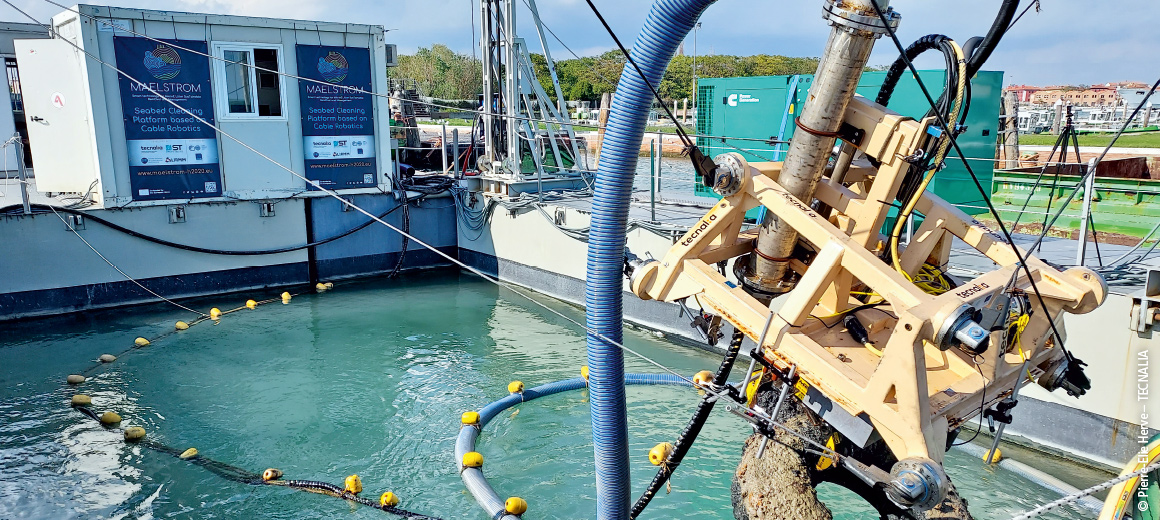
PC-based control in the marine and environmental sector
Around 70% of the waste in waters sinks to the bottom of the oceans or decomposes into micro- and nanoplastics – in total several 10 million tons. Based on an AI-based system, the MAELSTROM research project developed an autonomous robot for waters up to 20 meters deep that selectively identifies and collects objects. The system, which is automated with PC-based control, passed its test run in the canals of Venice in September 2022.
If you want to prevent trash from poisoning fragile underwater ecosystems or micro- and nanoplastics from entering our bodies through food chains, you need to both prevent further pollution of water bodies and collect the trash that is already underwater. This is exactly what the European Horizon 2020 – MAELSTROM project aims to do: develop and integrate technologies to identify, remove, sort, and convert all types of marine debris into raw materials. To this end, an international research team with representatives from TECNALIA (Spain), CNRS-LIRMM (France) and Servizi Tecnici (Italy), has developed the "Robotic Seabed Cleaning Platform". Its core component is an underwater robot equipped with a gripper and a suction device that moves flexibly in six degrees of freedom with the help of eight winches.

Using sensors and cameras, the robot detects trash on the seabed, automatically positions itself above it, and can lift objects weighing up to 130 kg (including bicycles, tires, boxes, and nets). Smaller parts or plastic pieces floating in the water are recovered by suction. “Since we operate from the surface and activate grabs or suction cups only when needed, we achieve high selectivity, minimizing the impact on the seabed ecosystem,” explains Mariola Rodríguez, project manager of MAELSTROM at TECNALIA.
The positioning winches are synchronously controlled via AX5118 Servo Drives and AM8071 servomotors from Beckhoff. “To ensure robust, accurate, and fast positioning, we chose brushless synchronous servomotors,” points out Jose Gorrotxategi, electronics engineer of TECNALIA's Cable Robotics Team. Another advantage can be found in the One Cable Technology (OCT) of the drives, which reduces the wiring effort and space requirements at the winches. The steel cables of the winches allow the robot frame to be precisely positioned underwater and held in place with high stability, despite the sometimes strong currents. Encoders on the motor shafts detect the angular position and revolutions of the cable drums, which indirectly allows them to establish the length of the coiled cable.
Electromagnetic brakes and monitoring of cable tensions by means of force sensors ensure the required safety. If the measured values are outside the permissible range, the cable robot stops immediately and an error message is displayed.
Sensor clusters above and below water
For control and monitoring purposes, the frame of the underwater cable robot contains a number of sensors and cameras for manual, automatic, and remote operation. “The cameras and lights allow manual control provided the visibility underwater is not too low,” adds Pierre-Elie Herve, mechanical and control engineer of TECNALIA's Cable Robotics Team. The operator can click on interesting locations on the seabed in the camera image, which the robot then approaches autonomously. A pressure sensor on the robot frame detects the diving depth, and an inertial measurement unit (IMU) regulates its position in the water. The distance of the mobile platform to the seabed and its relative velocity to it is recorded by a Doppler Velocity Log (DVL) via four sonar sensors.
Other sensors are located on the pontoon at the water surface, including a pressure sensor to compensate for atmospheric pressure changes during depth control. Two real-time kinematic GPS units determine the position and vertical orientation of the barge in real time. All data from these different systems is incorporated into the control and position regulation of the robot. Based on these values, the robotic platform can perform tasks such as precisely approaching and holding the positions previously selected on depth maps (bathymetry map), which speeds up the robot’s work. “This ability has proven to be a key feature in the very turbid waters of the Venetian Lagoon,” Mariola Rodríguez points out.
Control and communication of the cable robot
With its total of twelve axes – eight winches and four vertically movable slides on the pontoon masts – the underwater cable robot is controlled by TwinCAT 3, installed on a C6650 control cabinet Industrial PC. This is installed in the main control cabinet located in a control room. In addition to the cable force monitoring, several emergency stop buttons along the system (control room, radio control, and winches) ensure safe operation. The corresponding safety logic is executed by an EL6910 EtherCAT Terminal with TwinSAFE Logic. The servo drives with integrated brakes are integrated into the safety application via AX5805 TwinSAFE drive option cards.
A further four distribution boxes, mounted decentrally on the cable winches, contain the I/O interface modules and the electronics for cable force measurement. The connection between the control cabinet and the distribution boxes is established via Ethercat P. According to Jose Gorrotxategi, “This extension of the EtherCAT technology makes it possible to transmit both the DC supply and the EtherCAT real-time communication in a single cable.”
Robot platform control
When controlling the cable robot by joystick, the operator uses the estimated position of the mobile underwater platform and the cameras located on the mobile platform. Using the HMI, the operator can select the various control modes and monitor all functions based on the sensor values – in addition to visual control via underwater cameras.
The camera system for underwater perception mainly enables visual servo control: As soon as the operator sees marine debris (at a relatively short distance from the camera due to the water turbidity), they can click on it in the camera image and the mobile platform of the cable robot will automatically approach the debris.
Also integrated into the HMI is a depth map created with the DVL system and cameras. The operator can select any point in this image, which the mobile platform then moves toward. In addition to manual operation, the rack can also autonomously identify, target, and collect trash. “This works on the basis of artificial intelligence, which is able to identify the marine debris and select the most appropriate removal device,” specifies Pierre-Elie Herve.
The software developed for the robotic platform for cleaning the seabed calculates in real time the geographic position of the robot thanks to real-time GPS (real-time kinematic – or RTK) and the inertial measurement devices – devices that measure and report the position or orientation and simultaneously monitor and control the winches. In addition, the position of the robot is displayed on the map of the seabed, which also shows the position of the waste. The robot can move either in automatic mode, with the software then determining the "trajectory in the water", or in manual mode controlled via joystick. While the robot is moving, a camera combined with an acoustic sensor scans the seabed to measure the depth (bathymetry) and detect trash. This data is georeferenced and overlaid on the map in real time.