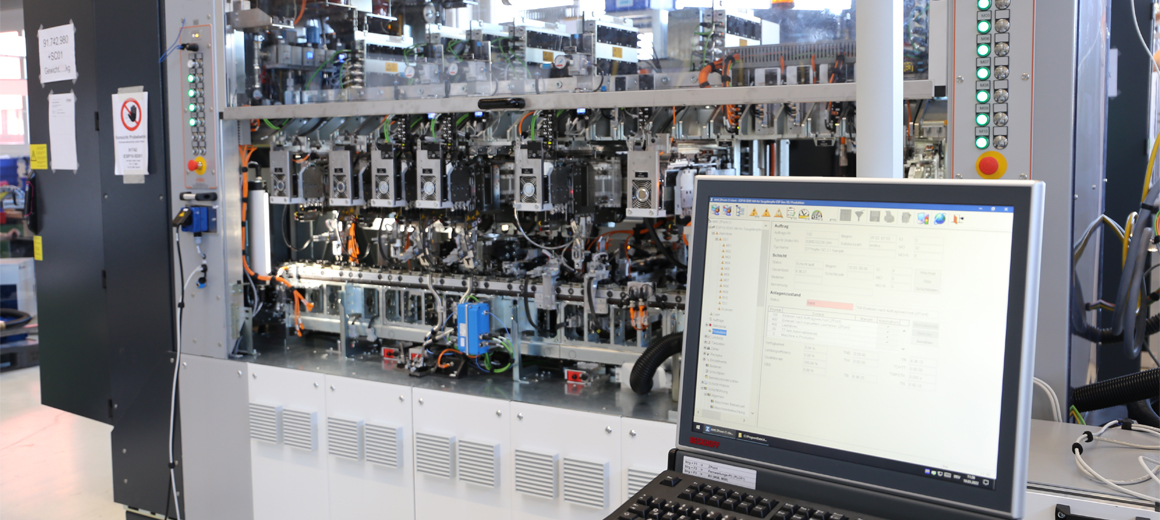
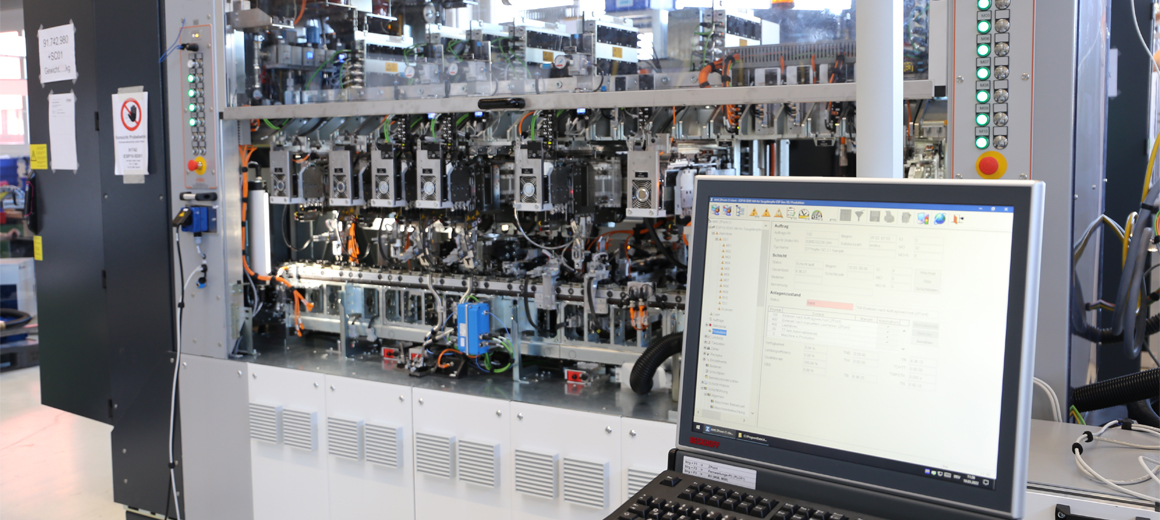
TwinCAT boosts performance in assembly system automation
To fully push the limits of what is technically feasible with computing power that can be scaled as needed, the STIWA Group has been relying on PC-based control technology from Beckhoff since the 1990s. This results in cycle times of less than one second, positioning accuracies in the hundredths of a millimeter range, and active system monitoring that uses sophisticated advanced-analytics and AI methods to ensure data-based production optimization.
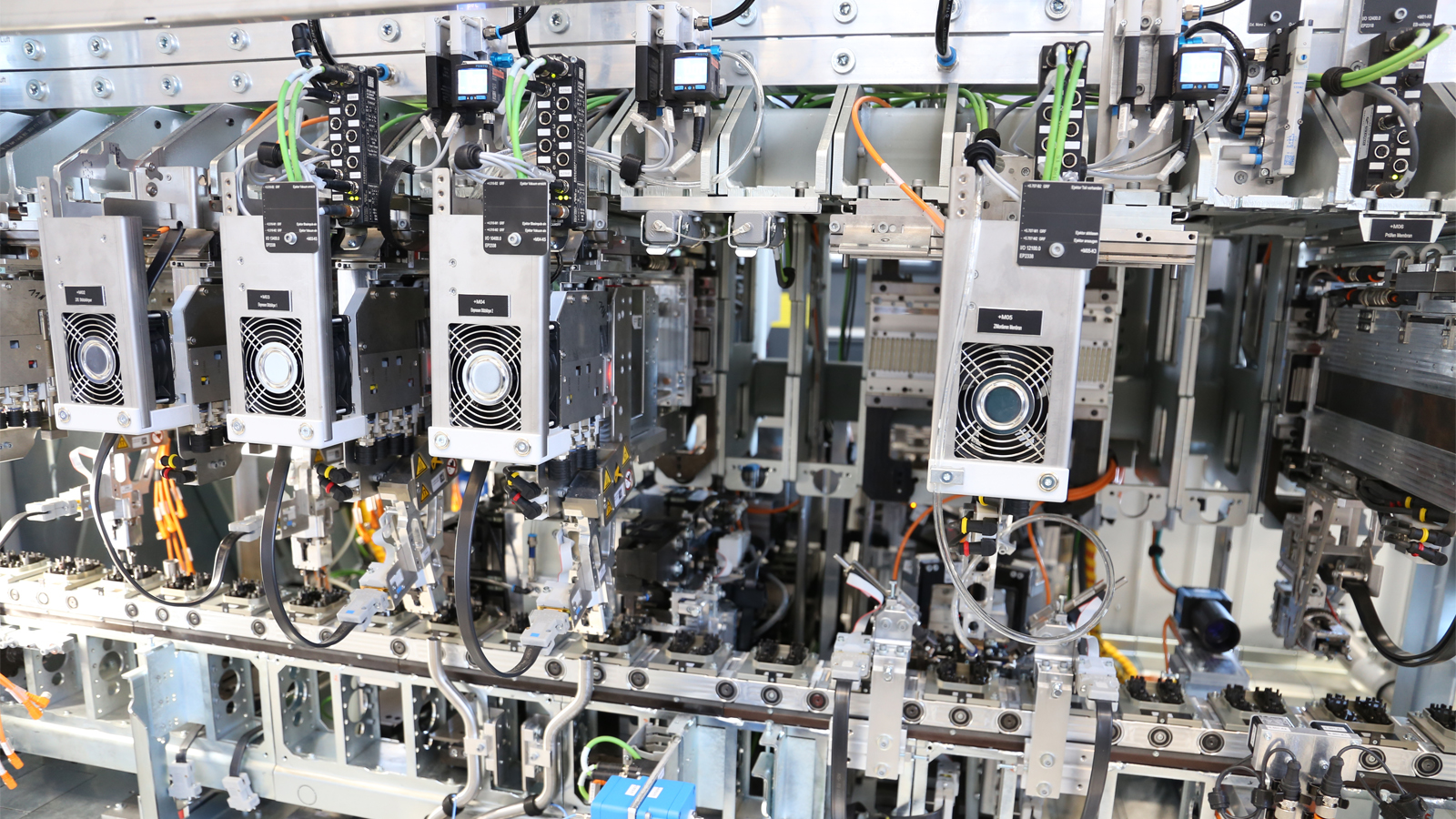
To quote the decision-makers at the STIWA Group, creating a successful company means seizing opportunities, recognizing forward-looking technologies as well as trends and implementing them in solutions. STIWA’s now 50-year history perfectly illustrates this. In other words, the rise of a small mechanical engineering company based in Attnang-Puchheim, Austria, to an internationally sought-after specialist in the field of product and high-performance automation did not come about by chance. “More than anything else, it was Walter Sticht’s personality that made this development possible. As a gifted technician with ambition and craft running through his veins, he recognized the potential of PC-based control technology at a very early stage and was one of the first to start exploring this new kind of solution, venturing into the market as early as the 1990s,” says Michael Pauditz, head of the business unit for software development and innovation at the STIWA Group, recalling the beginnings of the company’s close partnership with Beckhoff.
At that time, the automation specialist was still a newcomer, but promised one thing from the very beginning: to change the world of automation permanently with revolutionary product developments. “Since then, we have continued to join forces to push the limits of what is technically possible,” Michael Pauditz adds. In fact, there is no limit to the range of possibilities for systems made by STIWA, through its use of modular, flexibly adaptable hardware and software and a closed feedback loop within the corporate group.
Hidden champion with special qualities
One of the STIWA Group’s unique selling points is that, through its work with STIWA Automation GmbH as a machinery manufacturer, STIWA AMS GmbH as a software developer and STIWA Advanced Products GmbH as a producer for markets including the automotive industry, it is both a manufacturer and an operator of high-performance automation. This means that the Austria-based group can use its own production environment for proof-of-concept work. Continuously recording all relevant machine and process parameters and analyzing them in detail ensure that the experience gained from ongoing operation is immediately fed back to the development departments as suggestions for optimization. “This close interaction with our production site in Gampern helped us build up our in-depth process expertise, without which automation at such an advanced level would not be possible,” says Michael Fuchshuber, CEO of STIWA Automation GmbH, alluding to the fact that every microsecond, every hundredth of a millimeter and generally every extra ounce of performance really counts in STIWA systems.
“We purposefully push our systems beyond conventional limits,” Michael Pauditz adds, confirming that the group’s status as a globally recognized hidden champion in the high-performance automation segment makes it feel obliged to offer the maximum possible in every case. Translated into technical key figures, this means the following for the LTM-CI, a linear (L) transfer system (T) with a miniature design (M) designed for ultra-fast assembly of small parts up to 30 x 30 x 30 mm in size: laser welding, screwing, press-fitting, labeling, testing, measuring, and feeding and positioning with 0.08-millimeter precision can be carried out in the sub-second range with up to 24 processing modules per system as required – and all this with three to five degrees of freedom.
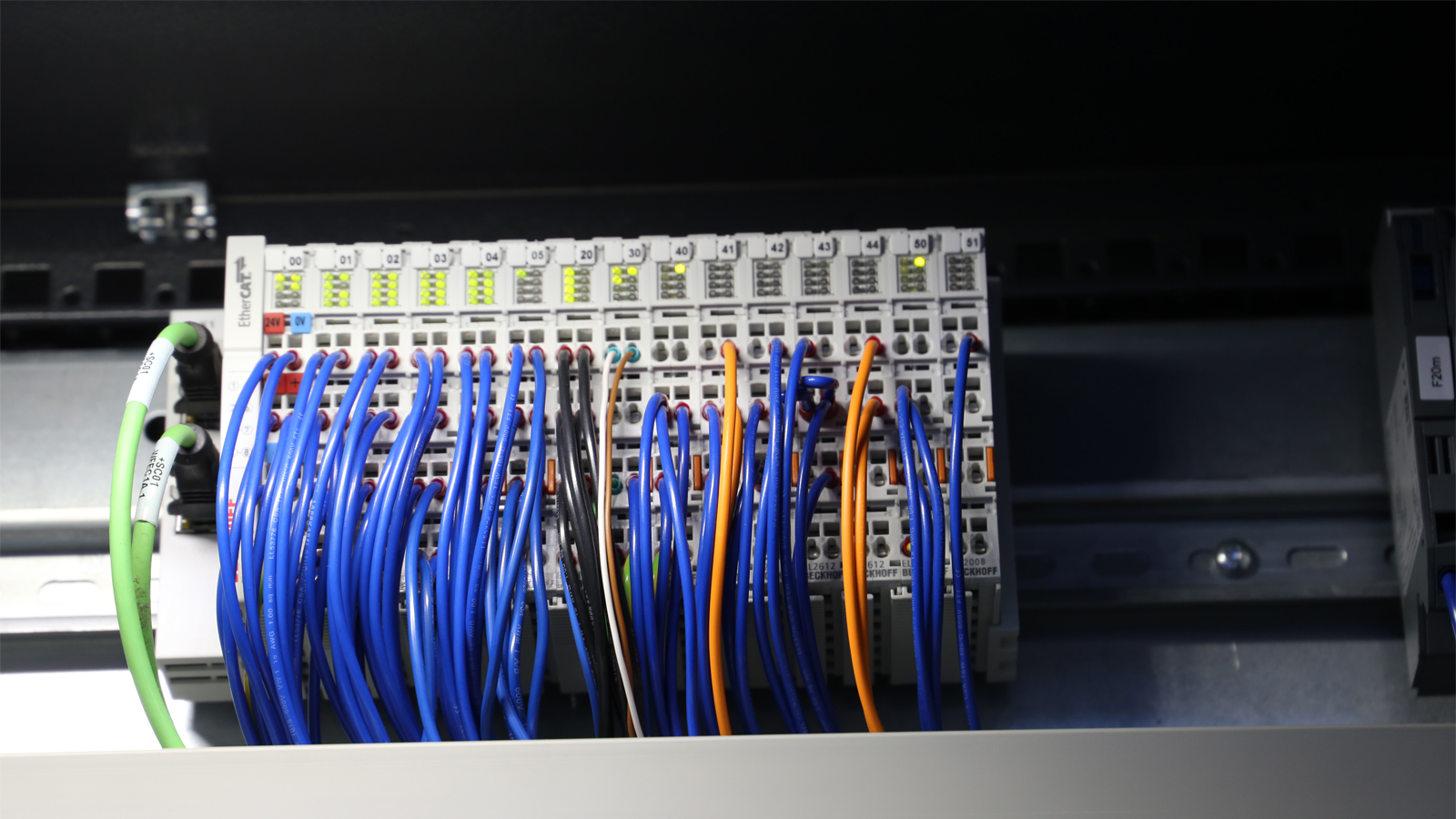
High-performance, standardized software architecture
In Beckhoff, STIWA says it has found the perfect sparring partner for implementing such high-tech solutions, which are extraordinary in many respects. With their collaborative innovation mindset, the companies created a modularly designed PLC framework based on TwinCAT, which can be used to respond quickly to customer-specific requirements. “In total, we spent around 500 person-years of basic development to design a high-performance all-in-one solution that can be used in mechanical engineering as well as in building, process or laboratory automation,” says Michael Pauditz, describing a system landscape that is 97% based on the Completely Integrated software architecture that is consistent and thus extensively tested. Only the remaining 3% have to be tailored to the application. Any storage or computing capacity that Beckhoff makes available with its open, PC-based control technology is fully utilized.
“With cycle times of 0.5 s, we orchestrate up to 50 NC axes via an Industrial PC. At the same time, every single axis movement is monitored to make event-driven adjustments to production processes possible and perform further analyses,” details Michael Pauditz. The technological foundation for PLC conversions from axis positions to real-time values and vice versa was created by Beckhoff using EtherCAT and the principle of distributed clocks. STIWA uses this, among other things, to identify workpiece carriers traveling at transport speeds of up to 3 m/s to the next processing station as they pass by. Various EtherCAT oversampling terminals from Beckhoff and the EP1258 EtherCAT Box (8-channel digital input) with time stamp functionality demonstrate their high signal processing capability.
In a typical STIWA system, more than 10 MB of raw data have to be forwarded to a wide variety of system devices every 0.5 s. For this purpose, the Automation Device Specification (ADS) protocol provides a transport layer within the TwinCAT system that enables direct communication between the TwinCAT NC and the TwinCAT PLC. The control algorithms for the individual production processes, such as the control of the scanner mirrors in laser hardening, are stored in the PLC itself. Any deviations from the target times are detected and reported as an indication of a suspected error in order to implement active error monitoring. “Some features that have found their way into TwinCAT were originally developed for a specific need of the STIWA Group – including the FIFO function blocks for non-cyclically recurring processes, in which the current axis positions can be permanently ‘refilled’ by a PLC program,” reveals Andreas Bernreitner, sales representative at Beckhoff Austria.
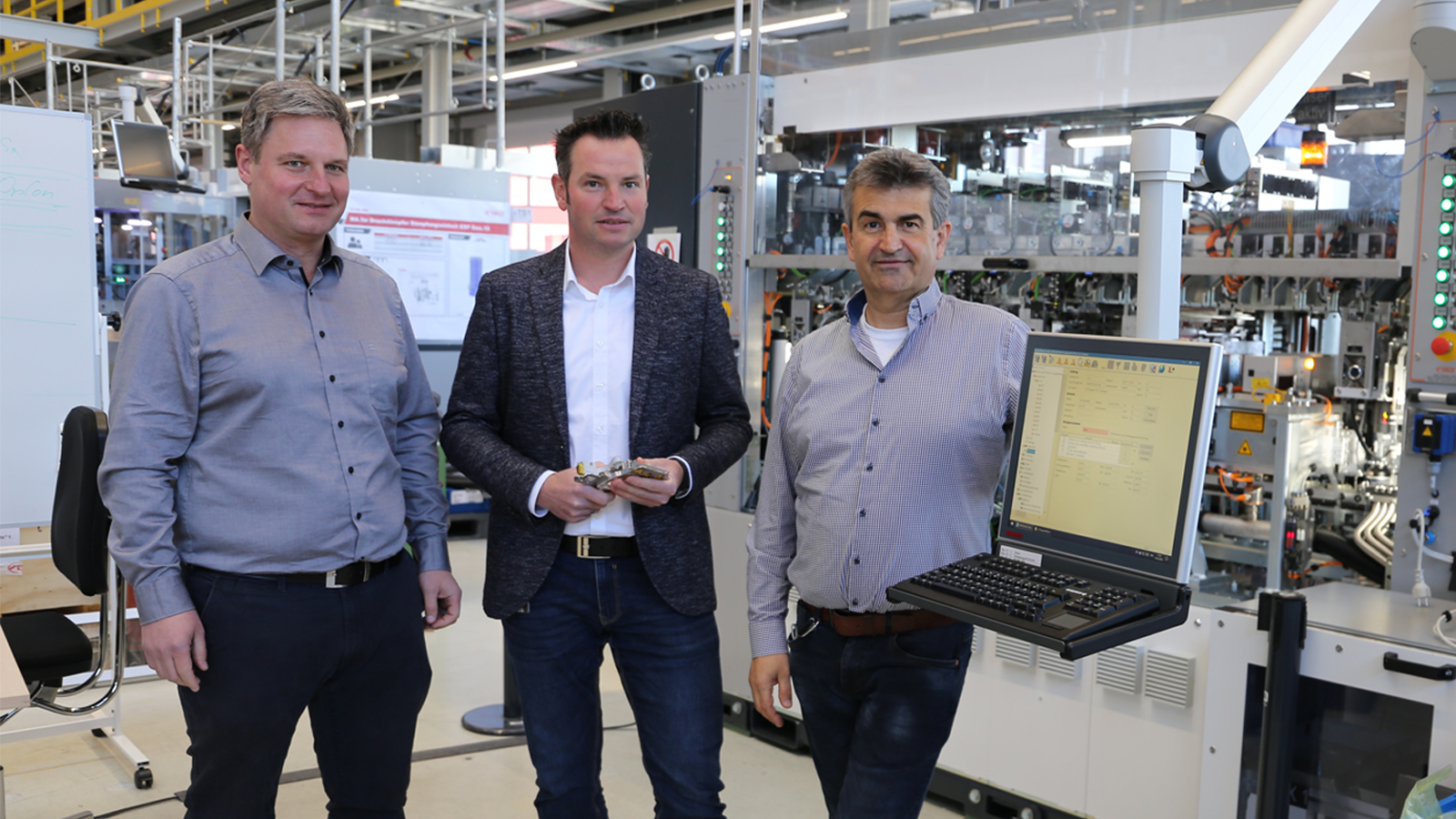
From classic contract manufacturer to innovation driver
The secret of success for today’s STIWA Group lies, according to the company itself, in the fact that it has not just been a contract manufacturer during its 50-year history – it has always been a driver of innovation. This began with a very early switch to software-based PLC technology, which at the time was only recognized as forward-looking by a few pioneers, and then continued in a digitization strategy that the company has consistently pursued. Through the use of artificial intelligence (AI) and machine learning (ML), this has delivered results such as active system monitoring and automatic process optimization at STIWA plants. The major added value is a fully integrated system that sustainably brings significant cost advantages and competitive advantages for customers. The huge demand from regular customers as well as further growth in new markets and industries justify the direction STIWA has taken: “We definitely have a lot of plans for the future and TwinCAT is an important part of our solutions. Otherwise, we would never be able to regulate the highly complex processes with the levels of quality that we achieve today,” emphasizes Michael Fuchshuber.
While STIWA’s status as a classic machine builder meant that it previously responded primarily to specific customer requirements (using a build-to-print approach), in the future, as a group of companies, it intends to focus mainly on its own product development, explains Michael Fuchshuber: “The automotive industry crisis and other global challenges have clearly shown in recent years that we are facing a very dynamic market and technology environment. This is what we need to respond to. We are therefore increasingly pushing the in-house production of highly innovative new solutions. With STIWA Advanced Products, we create innovative product ideas from prototype to series production at our site in Gampern. To this end, in recent years we have also established a joint venture with the Vorarlberg-based innovation hotbed Inventus.” In addition, the company XeelTech, founded in 2019, is developing revolutionary new products such as a rotary encoder based on magnetorheological fluids (MRF). This provides the operator with haptic feedback, with the type of feedback pattern freely programmable via the software.