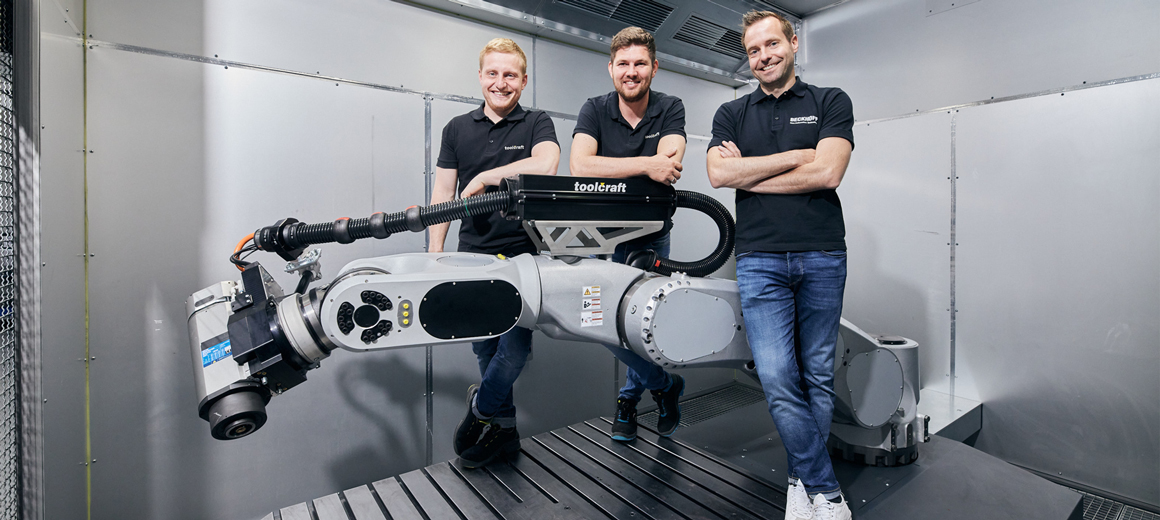
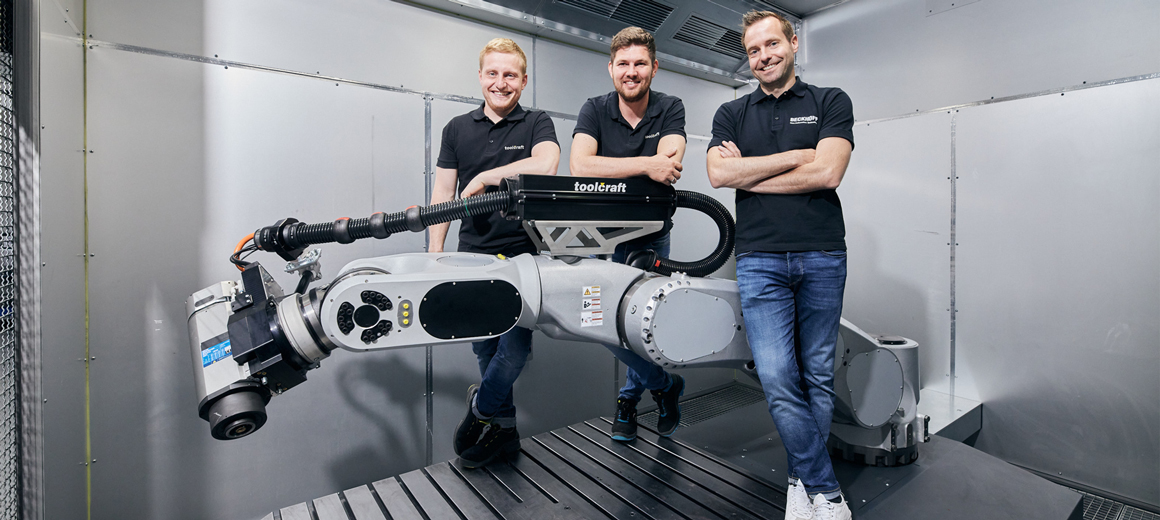
TwinCAT CNC and drive technology in machining
Some claim that hard materials cannot be precisely machined with jointed-arm robots – but toolcraft will prove them wrong. Daniel Distler and Andreas Bauer use TwinCAT CNC and PC-based control from Beckhoff to implement robot cells for precise machining of components – including solid blocks of silicon carbide and gray cast iron.
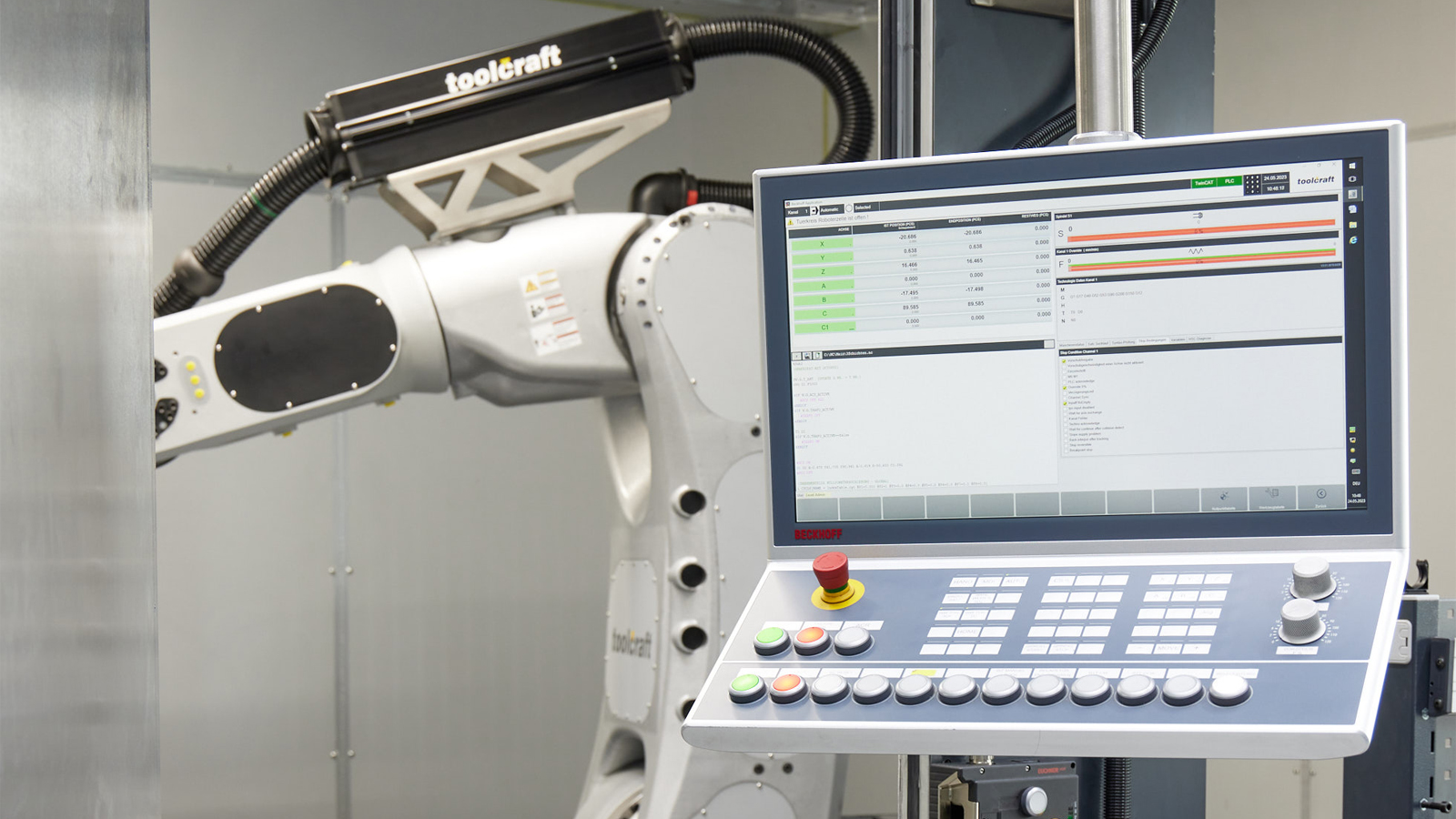
toolcraft understands exactly what the processing industry needs, which processes and technologies work in practice, and which do not. That’s because toolcraft not only manufactures on behalf of customers using its 60 CNC machines, but also designs, plans, and builds turnkey production systems for companies in various industries.
Founded in 1989 as a contract manufacturer, the company gradually added further competencies in various manufacturing technologies, including injection molding and mold making in 2005 and additive manufacturing technologies in 2011. In 2015, robotics became the newest technology division at toolcraft. “No matter what technology we operate in, we always want to have the expertise needed to offer complete solutions,” explains Daniel Distler, division manager for robotics with a focus on sales and human resources.
The range extends from simple devices to complex systems with integration into existing systems at the customer site. “Connecting machines with new technology to existing controllers at the end customer’s site is not always the easiest method, but it works when you use flexible control technology,” said Andreas Bauer, division manager for robotics with a focus on engineering at toolcraft.
One automation platform for every application
This is why Andreas Bauer and Daniel Distler rely on PC-based control, including in the production cells with 7-axis milling robots for machining components at CNC level. “The TwinCAT CNC was the first controller with an integrated interface to the Stäubli robot controller (TwinCAT Robotics uniVAL PLC, TF5130). This technology package made a lot of things easier for us when implementing the project,” recalls Andreas Bauer. Using the machining cell designed by toolcraft, one user now mills base frames for wafer production from large silicon carbide and gray cast iron blocks. “toolcraft was already using our TwinCAT CNC in this case,” adds Alexander Klos from Sales at the Beckhoff office in Nuremberg.
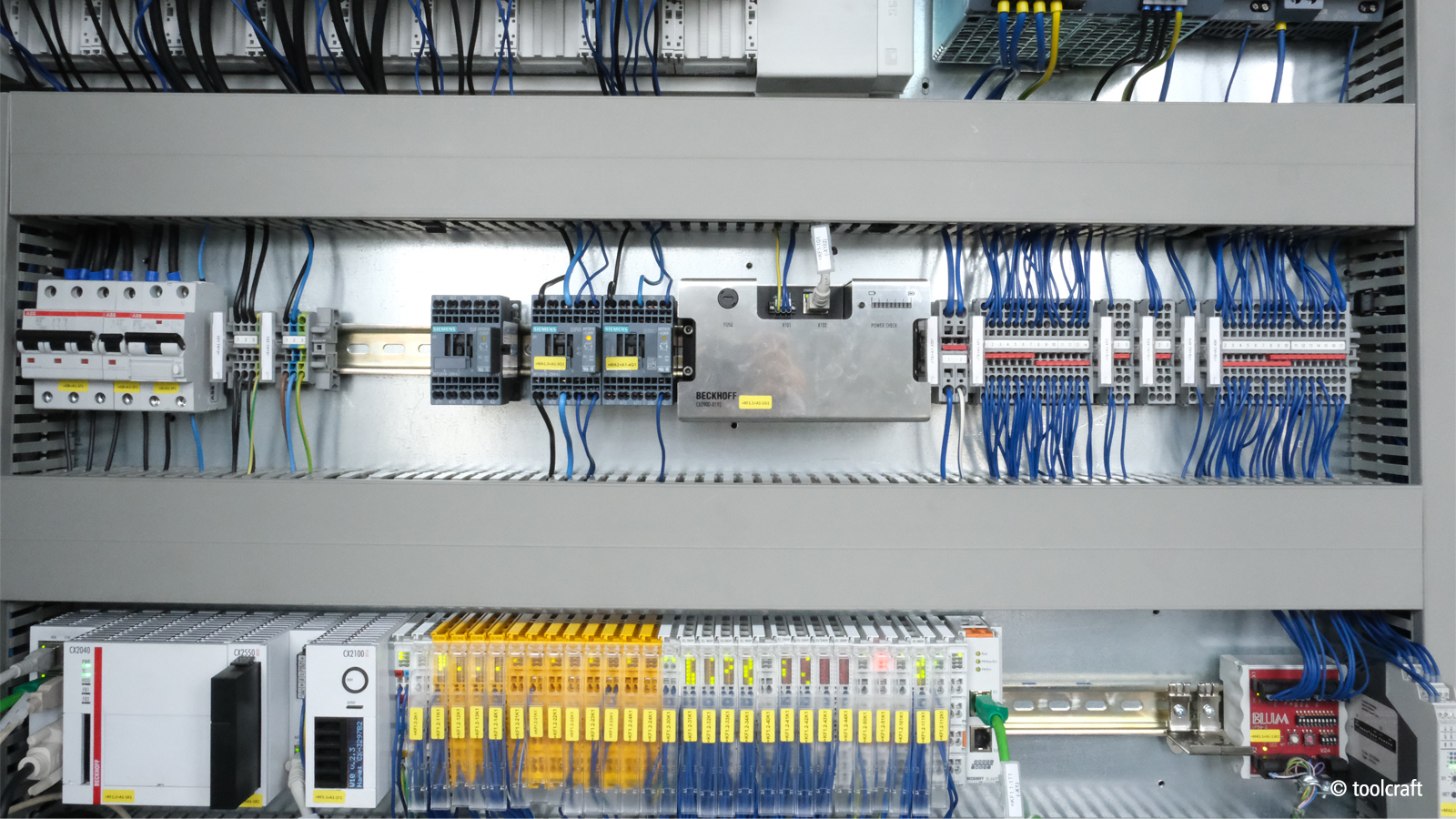
Initially, the customer was still machining the blocks with conventional 5-axis CNC machines. But milling the hard material produces ultra-fine dust that penetrates every joint, linear guide, and bearing, causing huge problems in a short time. The CNC machines quickly became worn out and required a major overhaul. “We knew that with the TwinCAT CNC we could achieve the required accuracy of 2/10 mm within a machining area of up to 1 m³, as well as seal the Stäubli robots and apply overpressure,” emphasizes Daniel Distler. This knowledge comes from various projects in which, for example, robots have been completely dismantled and sealed in such a way that they still function reliably even at water depths of up to 20 m.
Next-generation CNC robot
The potential of robots in parts processing is enormous, but where should the focus be? “We thought long and hard about where we wanted to go with robotic milling and, of course, how to get there,” explains Daniel Distler. The aim was not only to further increase the machining quality and raise it to a new level, but also to ensure that there were no changes for users when creating the machining programs. At the start of the project in 2018, all components of a machining cell were examined in a “best of breed approach”: robot, rotary table, tool changer, milling spindle, and, of course, the control technology. Andreas Bauer: “Based on our expertise over the last eight years, we know the exact strengths and weaknesses of the various kinematics and designs.” This expertise was applied in collaboration with a robot supplier to develop kinematics that increase stiffness, dust/water resistance, payload, and reach.
The result is the current configuration of a machining cell with a high-end CNC robot based on new kinematics. “In the new generation, toolcraft also uses servo drives and servomotors from Beckhoff in addition to TwinCAT CNC,” adds Alexander Klos. The robot was equipped with double-bearing gears on all axes and encoders on the drive and output sides. In addition, the spindle mount was modified. The control technology basis of the milling robot is formed by the powerful CX2040 Embedded PC in combination with the CP3921-1502-0010 CNC multi-touch Control Panel, which is connected to the embedded PC via CP-Link 4 with only one Ethernet cable (CAT.6A). The system is rounded off by the AM8000 servomotors and the AX8000 multi-axis servo system as well as TwinCAT CNC. Other positive side effects of the new design include the internal hose assemblies, which simplify handling. In addition, no separate robot controller is required, freeing up space in the control cabinet and reducing the complexity of the project.
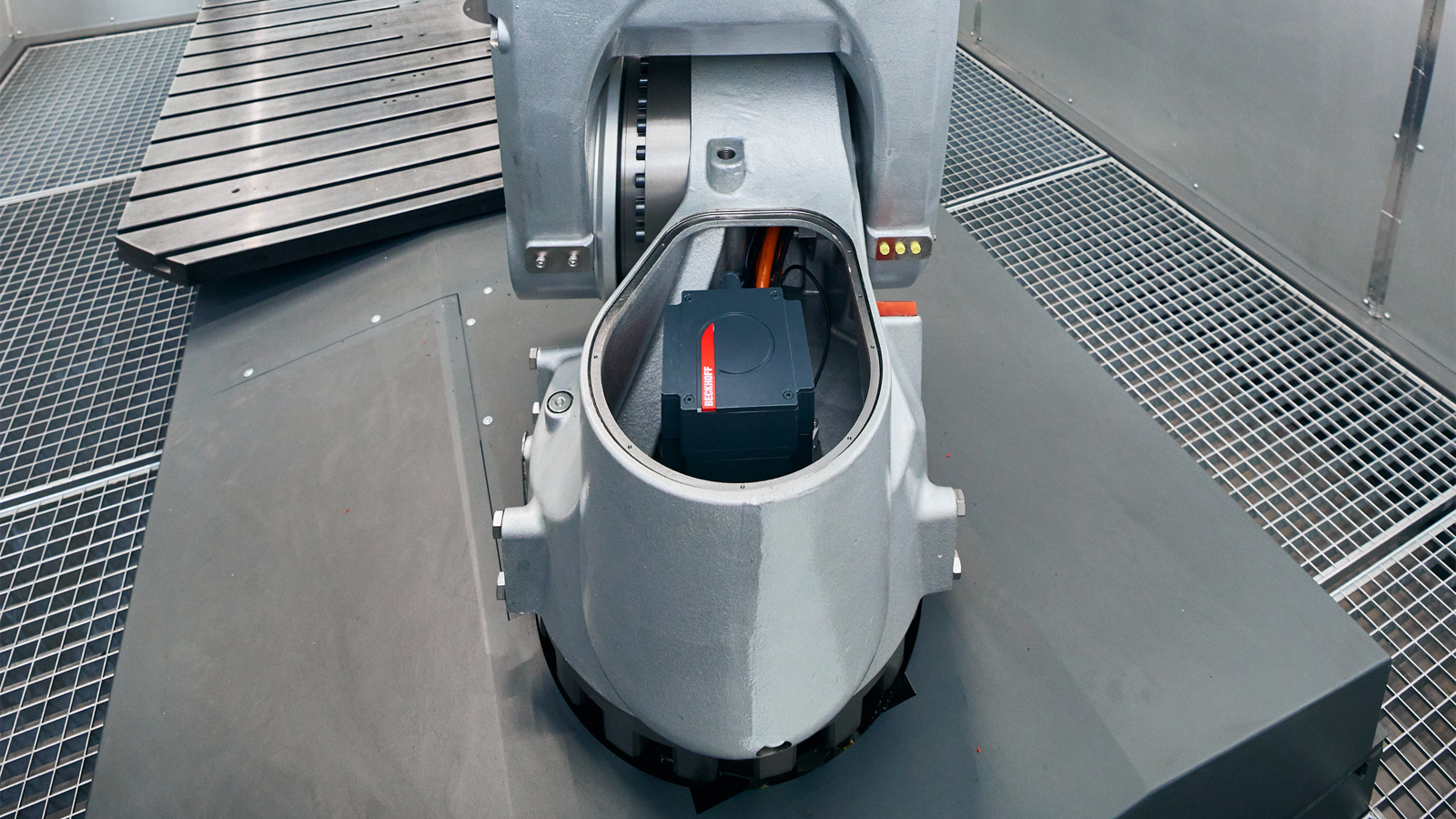
Straightforward conversion of the drive technology
“Although toolcraft started with TwinCAT CNC and TwinCAT Robotics uniVAL PLC, it was quickly possible to switch to another robot type with different mechanics, kinematics, and our drive and servo drive technology,” says Alexander Klos, pointing out two important properties of PC-based control – openness and flexibility. For example, it was possible to integrate the drive-side and output-side encoders of the robot axes into the software function blocks of the axis controllers without any problems. And with the integrated Beckhoff portfolio, ranging from CNC to servo drives and motors, toolcraft benefits from completely different optimization options. “Direct access to all parameters and process settings has played a large part in the further improvement of the accuracy,” says Andreas Bauer. For example, the low but still detectable hysteresis of the gearing was further compensated via the output-side encoders and appropriate control algorithms. Even when high forces are applied, e.g., during solid milling or depending on the position of the tool center point (TCP) in the working area, the axes are tracked with speed and precision. “And the integration of measurement and calibration cycles ensures consistent properties,” adds Daniel Distler.
toolcraft also retains flexibility in its choice of feedback systems and use of other technologies: the servo drives support many encoder interfaces and additional options are available via EtherCAT. “We are always thinking ahead and are considering integrating camera systems to detect and automatically load components,” says Andreas Bauer.
Post-processors and coordinate transformation included
It is very important for manufacturing companies to have a functioning process chain, from the CAD drawing to the machining program. As Daniel Distler says: “Our approach is to take away users’ fear of operating and programming the robots, while at the same time providing more freedom in machining.” PC-based control also helps in this area: post-processors and coordinate transformation are run on the embedded PC in parallel with the path control of the CNC robot. The machining programs can therefore be programmed in G-Code as normal and generated from the usual CAD/CAM programs. Daniel Distler explains: “We want the robot to work perfectly with the user’s CAM software.” toolcraft also has a flexible control platform for this purpose in the shape of PC-based control.