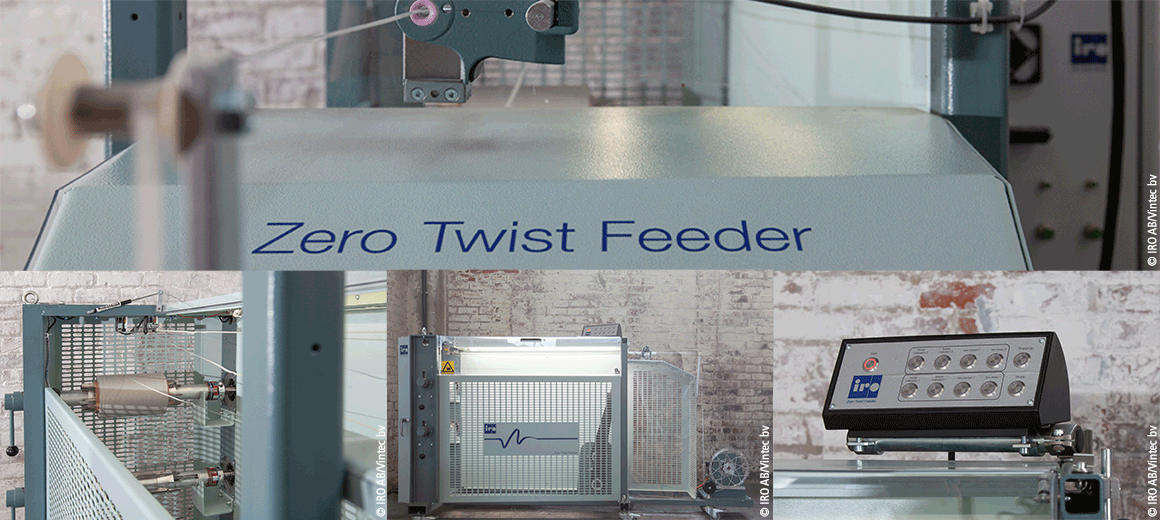
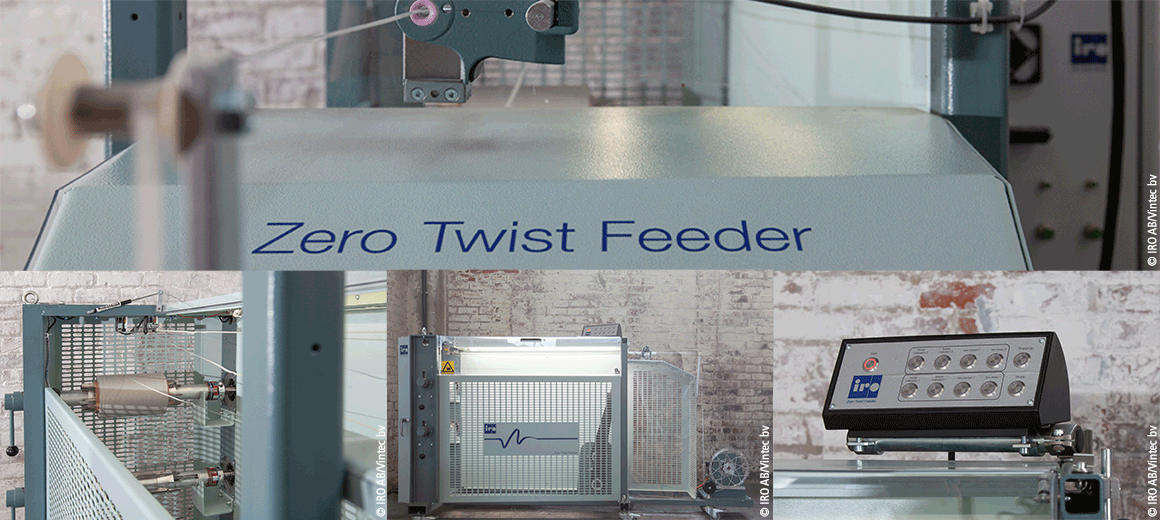
TwinCAT 3, Simulink® modeling and digital twin help modernize textile looms
The Zero Twist Feeder textile feeder from the company Vandewiele Sweden AB delivers ribbon yarn to looms without any twisting. The basis for this is an extensive simulation model from Belgian specialist Vintecc, which has been deeply integrated into the Beckhoff control software via the TwinCAT 3 Target for Simulink®. In this way, the bobbin speed can be precisely synchronized with the gripper movement.
"A big player in a small niche," says Pär Josefsson, head of Vandewiele's R&D department, describing the company based in Ulricehamn (east of Gothenburg) that supplies more than 60% of the world’s textile feeder market. "The fact that we place a strong focus on innovation is demonstrated by more than a hundred active patents." For the development of the Zero Twist Feeder, however, Vandewiele wanted to break new ground with the integration of simulation into the machine controller, which is why they sought exceptional external support. This was found in the Belgian company Vintecc, which specializes in model-based software development and is located in Roeselare, close to the headquarters of the Vandewiele parent company. Both development partners also agreed that Beckhoff PC-based control with TwinCAT 3 software would be the best technology to meet the demanding requirements of the application.
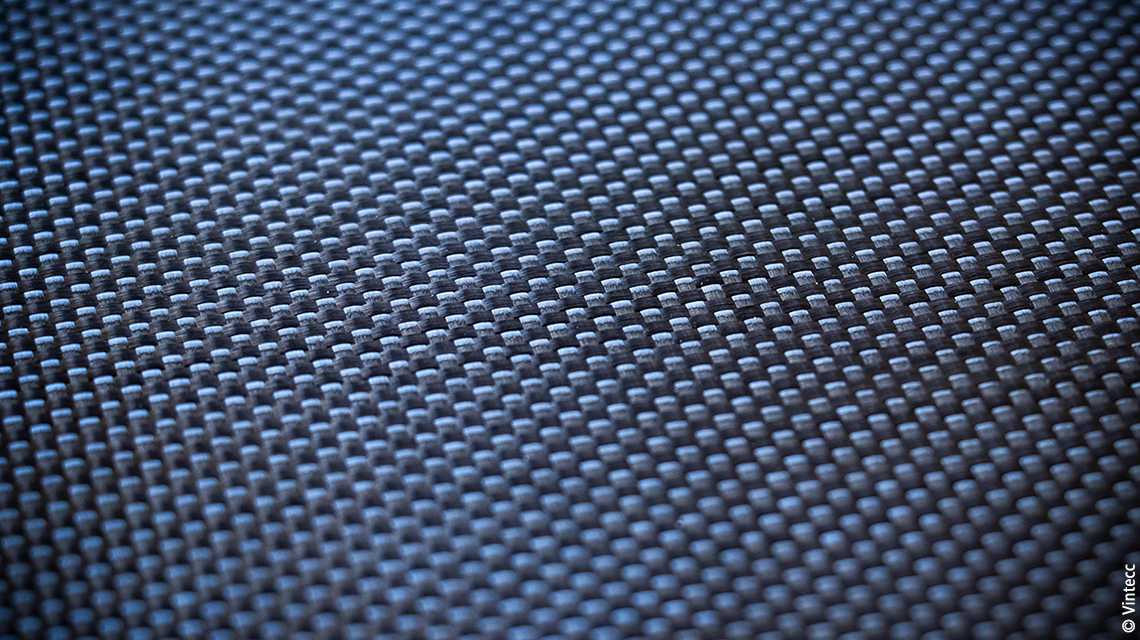
Defect-free textile fabric is the goal
When weaving carbon fiber, glass or plastic fiber into ribbon yarn, twisting or balling up of the supplied yarn is one of the biggest problems. The resulting defects would not only be visible but would also mean a weakness in the fabric. From Pär Josefsson's point of view, conventional thread guides do not offer a solution here: "In such machines, the thread must be pulled off at a constant velocity. However, looms operate at high velocities and tend to pull on the bobbin at very irregular intervals."
The Vandewiele team therefore developed a machine from scratch. The idea was to use an arm made of carbon fiber as a buffer between the bobbin and the gripper. Pär Josefsson explains: "The bobbin delivers the yarn at an average velocity. The buffer arm then buffers the yarn, which is unwound at a continuous velocity from the bobbin, and keeps it constantly under tension. It is essential to find the perfect balance for the yarn tension – strong enough to avoid sagging, but sufficiently flexible to prevent the yarn from tearing. The buffer arm then delivers exactly the right amount of yarn to the looms at the right velocity."
Simulation model integrated directly into the controller
In order to create a controller for this process, Vintecc implemented its extensive modeling expertise in a corresponding Simulink® model. The responsible project manager, Brecht Vermeulen, explains: "First of all, we created a digital twin of the machine in which all the software was programmed in Simulink®. The model includes several sub-models, each representing one aspect of the machine design, such as parameters, security, alarms and HMI." From his point of view, the combination of Simulink® with the TwinCAT control software has a particular advantage: "No separate PLC code is required. Instead, the TwinCAT 3 Target for Simulink® seamlessly integrates, visualizes and tunes the model directly and seamlessly, and automatically connects to the I/Os and drives. Changes to the parameters, whether in the model, in TwinCAT or in the hardware, are immediately transferred to a non-volatile memory module. All parameters are stored securely and reliably in this way. This kind of deep integration is only possible with the Beckhoff platform."
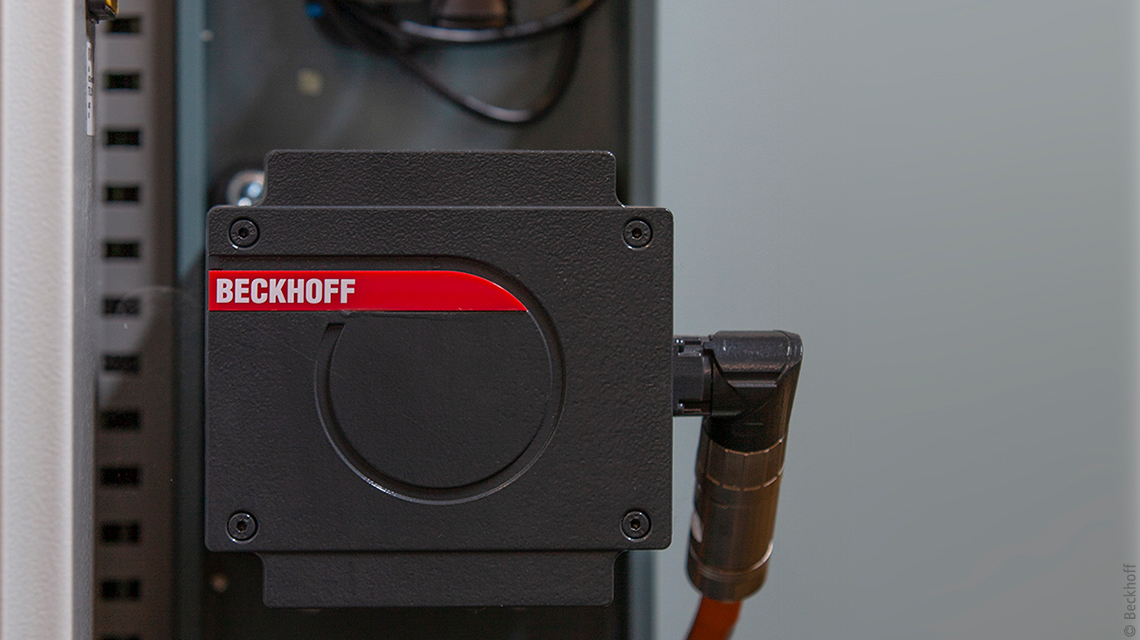
The decisive factor in the implementation was the high precision required. The buffer arm is about 650 mm long and must provide an accuracy of ±1.5 mm in order to constantly achieve the perfect angle control. In practice, velocities can reach up to 850 m/min. "Before production begins, the machine must therefore perform two calibration steps based on the Simulink® model in slow motion – to calibrate the bobbin diameter and the movement of the buffer arm. This is done by calculating the feed curve as well as the actual velocity and tension required for feeding the machine. During the entire insertion cycle, the model also compensates for changes in the bobbin diameter and the tension in the arm according to the data from two sensors," explains Brecht Vermeulen. The entire process and the performance of the machine can be visualized and analyzed conveniently via TwinCAT HMI.
According to Brecht Vermeulen, the Zero Twist Feeder benefits in particular from the Beckhoff Industrial PC, dynamic drive technology together with powerful EtherCAT communication and I/O terminals: "The AX8000 multi-axis servo system with the AM8000 servomotors and EtherCAT is the optimal combination to meet the required short cycle times. Another important element was the precise drive tuning, which we could always count on support from Beckhoff to accomplish, both in Belgium and Sweden. Safety functions were implemented directly in the drives with TwinSAFE, so that no separate safety PLC was required – another way to increase flexibility and save costs. That's the nice thing about this application: the functionality of standard hardware is further enhanced by the deep integration of a Simulink® model into TwinCAT without additional hardware requirements."
Virtual commissioning
Extensive simulations were carried out in Belgium before the algorithms were tested on the real hardware in Sweden. Each prototype was analyzed using measurements displayed on the TwinCAT Scope software oscilloscope in order to mechanically optimize the Zero Twist Feeder. Pär Josefsson sums up: "The cooperation with Vintecc and Beckhoff went very smoothly. Vintecc combines a high level of modeling knowledge with very direct and fast communication, so that we were able to advance quickly in the development of the Zero Twist Feeder. Our team also received all the necessary support from the Swedish branch office of Beckhoff. This was our first experience with the direct implementation of a simulation into the machine controller, and it was virtually the only way to achieve the desired results. Today, the first Zero Twist Feeders are already proving themselves in the field with our customers – as a single-channel device with one buffer arm or as a weft thread mixing version with two buffer arms."