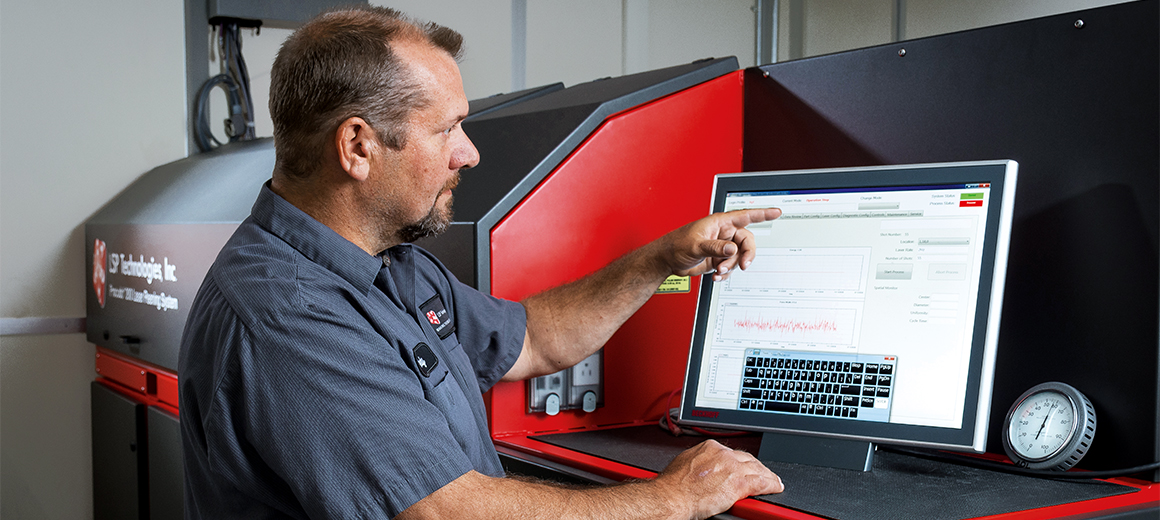
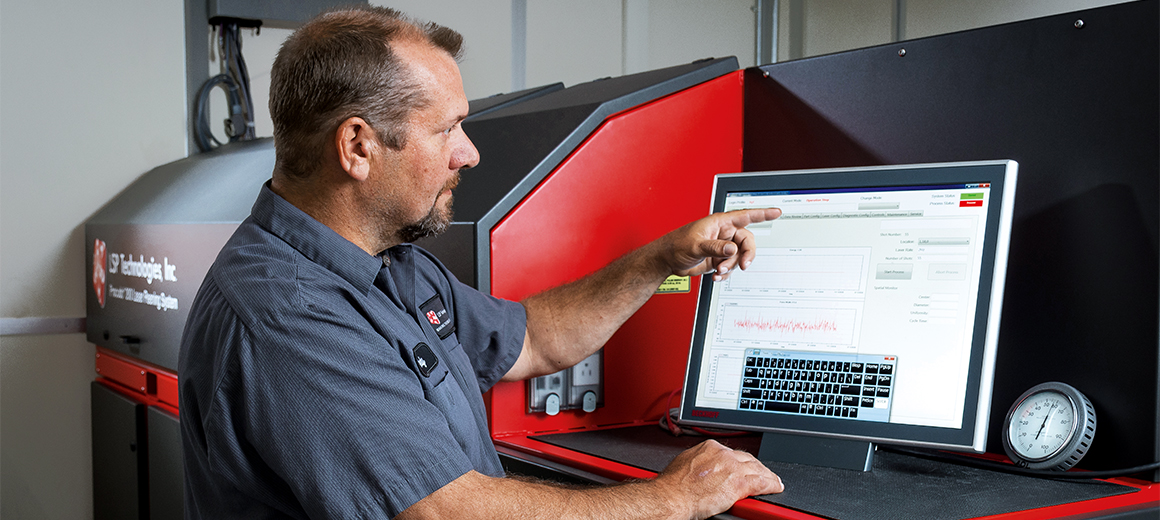
Laser peening system for surface treatment achieves highest degree of adaptability with PC Control
Whether manufacturing packaging machines or components for airliners, companies must be able to guarantee all metal parts will remain durable and dependable throughout the product’s lifecycle. Recognizing this challenge, LSP Technologies pioneered an effective method to increase the strength of metal parts: surface treatment with pulsed laser beams. One of their most recent laser peening systems relies on the flexibility of EtherCAT and PC-based control technology from Beckhoff to meet the most diverse customer requirements.
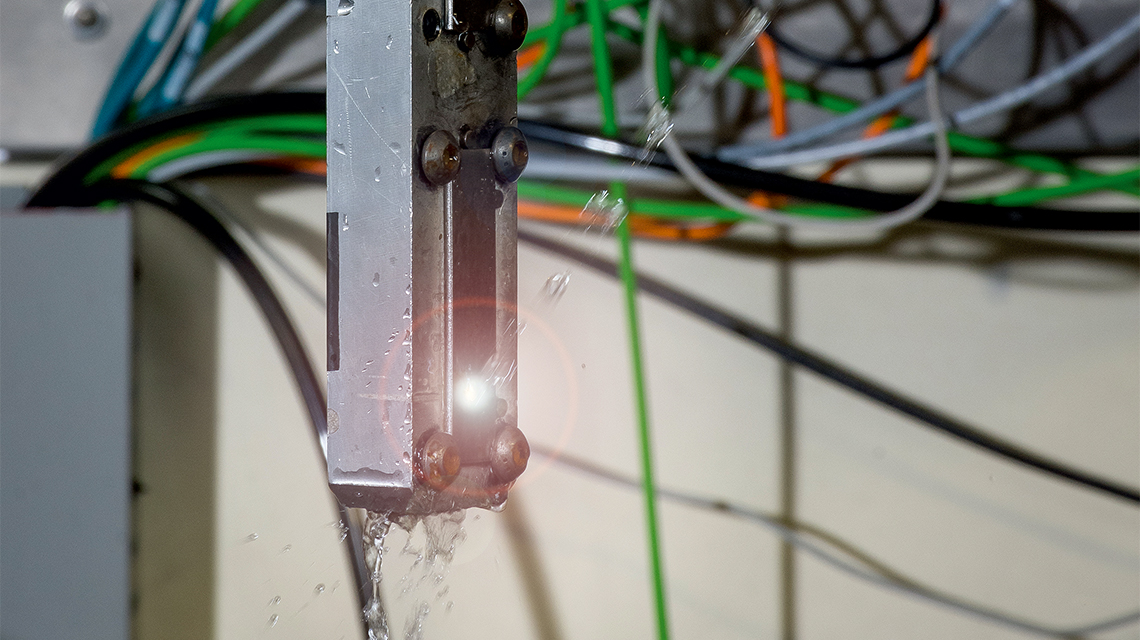
Peening in general describes the processing of metal workpieces for example with hammers, shot peening or in this case, with high-powered lasers, to strengthen the metal and mitigate the effects of material fatigue. In laser peening, also called laser shock peening, a pulsed laser beam is directed at the metal surface while a stream of water flows over the workpiece. This results in a small plasma explosion between the water and the surface enabling the shock waves to travel deep into the metal, making the material denser and stronger and increasing the fatigue life.
Founded in 1995, LSP Technologies (LSPT) has remained at the forefront of laser peening systems worldwide. The Dublin, Ohio-area company provides laser peening services and equipment for many industries, such as aerospace, automotive and maritime. One of LSPT’s most recent advances is the modular Procudo® Laser Peening System – a self-contained turnkey system that can be tailor-made for each customer. For this high level of adaptability, LSPT relies on flexible control technology from Beckhoff.
Challenges in development
The Procudo® system uses diode-pumped YLF lasers that cover a total bandwidth of 1 to 200 Hz pulse frequency and operate at 20 Hz as standard. While the compact standard system measures 142 x 173 x 335 cm (56 x 68 x 132 inches), some of the customer systems are so large that they can accommodate several articulated arm robots. In addition, it must be possible to design the equipment both for the processing of very large workpieces as well as others that focus on the smallest, most precise details.
Another problem is the synchronization of workpiece and laser positioning: Metal parts, especially large or awkwardly shaped components, are often difficult to move within a machine cell when accommodating fixed-position lasers.
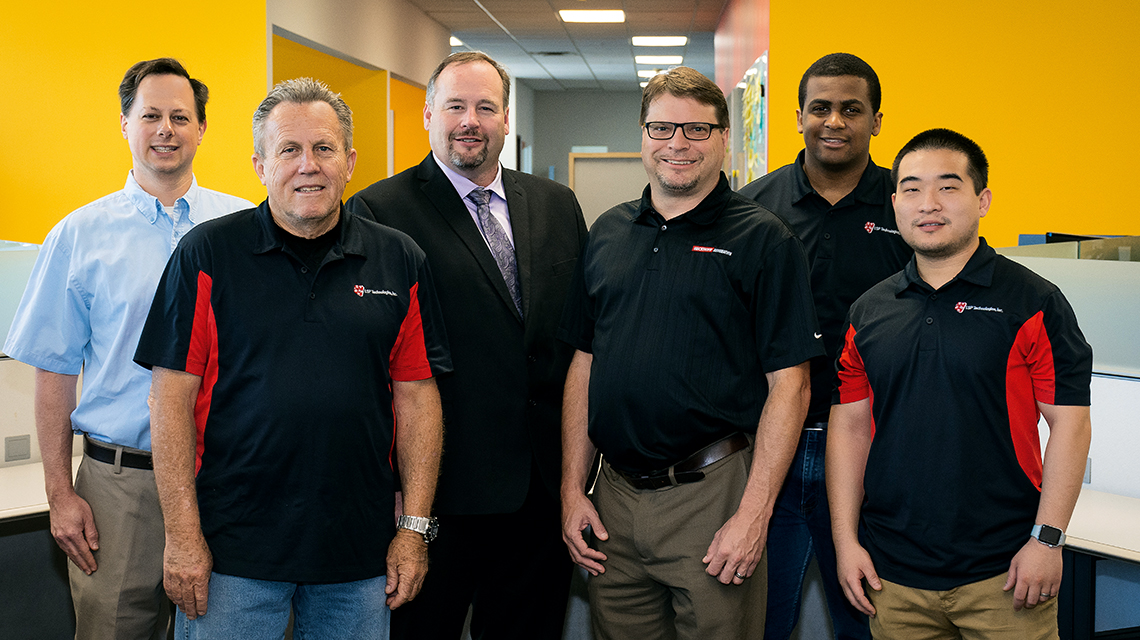
This is particularly challenging with workpieces like massive ship hulls and anchors, for example. “In the past, we generally used part-to-beam processing by aiming the laser at a fixed point in the processing cell and then moving the parts with robotics,” LSPT Vice President Business Development David Lahrman says. “To process very large parts, however, we now use beam-to-part processing, which involves moving the laser with robotic arms from KUKA to peen areas that require treatment.”
Flexible and powerful IPC technology
Initially LSPT was drawn to EtherCAT and PC-based control technology from Beckhoff because of its many interface options, including HMI hardware. Now the built-in CP2912 multi-touch Control Panel and the pole-mounted CP3913 multi-touch Control Panel offer LSPT the options needed for unique client demands, according to Controls Engineer Alex Portolese.
For control purposes, LSPT also uses the CX2040 Embedded PC, featuring quad-core Intel® Core™ i7 processors, to run HMI, connect to the cloud and communicate with higher-level systems. “We like the power and small form factor of the CX2040. With the addition of SQL databases, this allows us to maintain compact electrical cabinet footprints,” Portolese explains. However, the Procudo® Laser Peening System’s standard control hardware for robotics and other laser peening functions is the C5240 Industrial PC (IPC).
Electrical Engineer Avery Calhoun sees additional benefits in the 19-inch rack-mount powerhouse, which also boasts Intel® Core™ i7 processors: “The C5240 is very powerful and provides ample serial and Ethernet ports to connect with the EtherCAT I/O system. The IPC’s form factor is also easy to incorporate with our other rack-mount components.”
Exact synchronization ensures high efficiency
Precise motion control and EtherCAT communication are crucial for the Procudo® Laser Peening System. LSPT implements multiple articulated KUKA robots to move lasers, and sometimes also workpieces, to ensure that the beams are positioned with high accuracy.
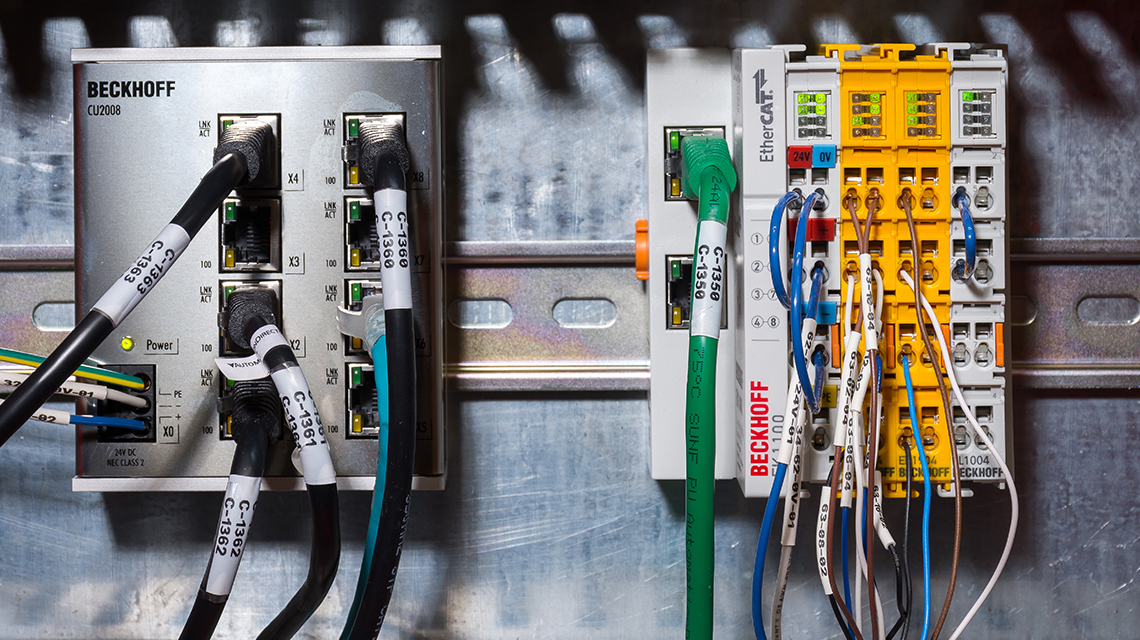
LSPT also uses AM8000 Servomotors from Beckhoff that offer a robust design with long lasting service life and are equipped with One Cable Technology (OCT), which saves space and costs by combining feedback and power in a single cable. “We have used the AM8000 Servomotors quite heavily in recent Procudo® Laser Peening System projects involving beam-to-part processing,” explains Portolese.
Based on EtherCAT, a wide range of I/O modules from Beckhoff provides scalable networking solutions for LSPT. Inside the machine cells where high moisture is present, LSPT uses IP67-rated EtherCAT Box modules and standard EtherCAT I/O terminals in electrical cabinets. LSPT also benefits from integrated safety through TwinSAFE. Safety-related programs are created in TwinCAT automation software and then transferred to TwinSAFE devices throughout the Procudo® Laser Peening System, including EL6900 TwinSAFE Logic terminals and EP1908 EtherCAT Box modules.
Powerful components strengthen the system
LSPT achieved its goals for flexibility, enabling the Procudo® Laser Peening System to suit the needs of a wide range of applications. As a result of the highly precise synchronization possible with TwinCAT and EtherCAT, the system can process up to 29 square inches (187 cm2) of material per min. Additionally, according to LSPT, the ability to synchronize motion control for the workpieces with laser control is critical to the repeatability and quality of their processes.