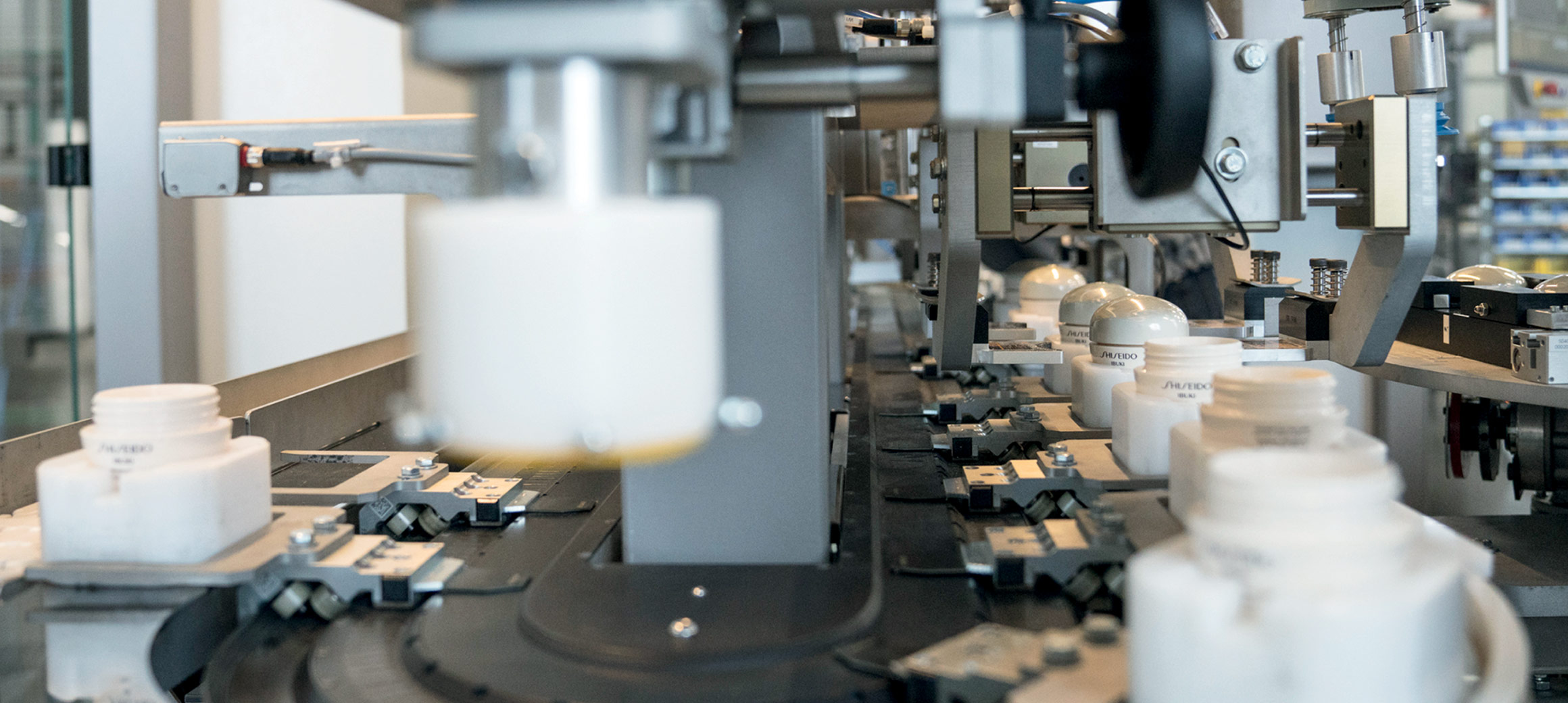
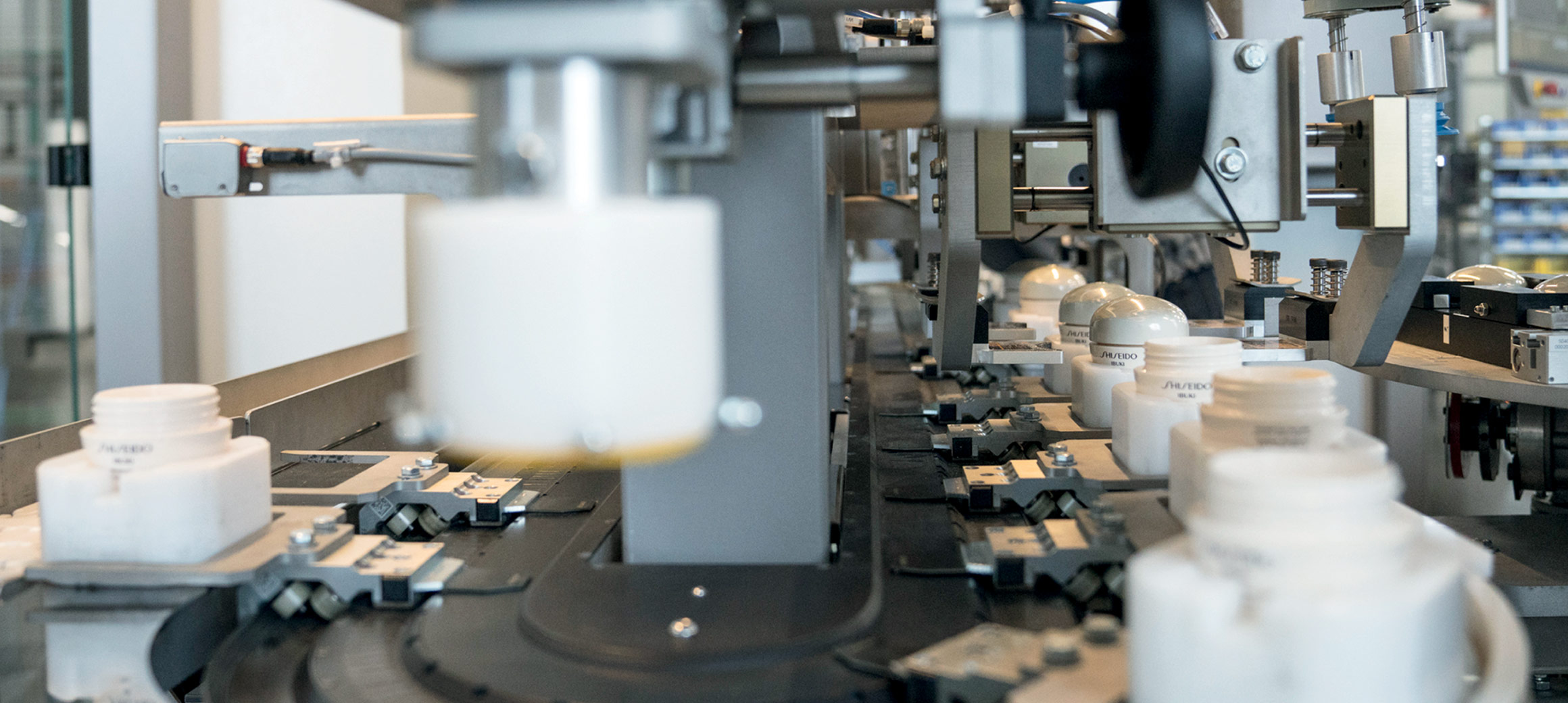
Linear transport system XTS provides the basis for compact and flexible packaging system with minimized conversion times
End customers in the cosmetics industry require their suppliers to provide them with packaging systems that feature maximum adaptability and flexibility because the market demands ever-faster changes in product presentation and packaging. To meet the needs of cosmetics company Shiseido, equipment manufacturer Unista developed an innovative solution based on the eXtended Transport System (XTS) and other automation components and software from Beckhoff.
Shiseido is a Japanese maker of high-end cosmetics with an international presence. Founded in 1872 in Tokyo, it is one of the world’s oldest cosmetics companies. Its European headquarters and two manufacturing plants have been based in France for thirty years. Machine manufacturer Unista, located in the Nantes region, was selected by Shiseido to develop and build two packaging machines. Since Shiseido uses containers in many sizes and shapes for its diverse portfolio of products in the luxury segment, the equipment had to deliver a maximum of flexibility.
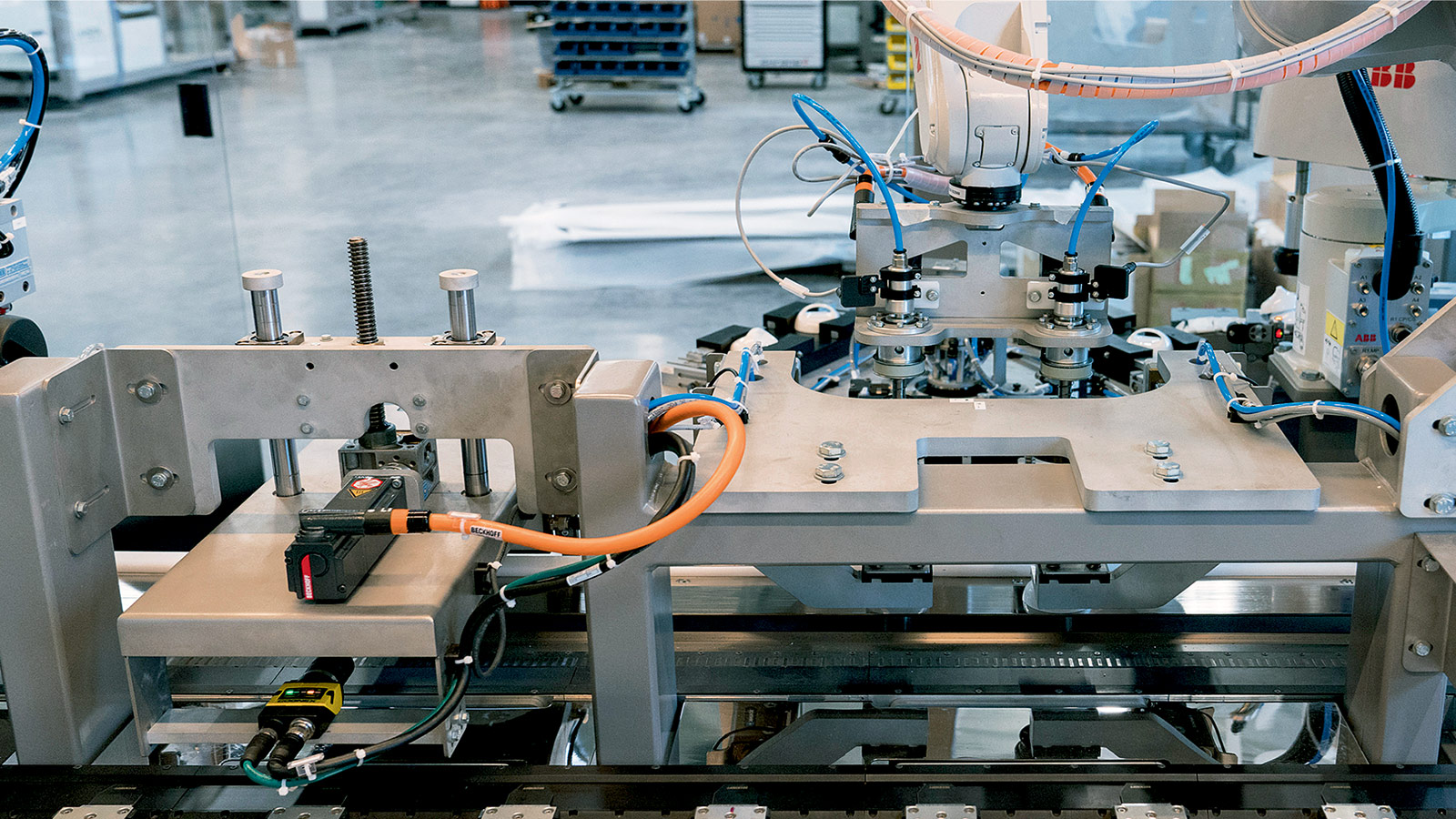
Unista has produced packaging lines for ten years and specializes in robot-supported equipment. The newly developed machine model supports many different container types and lot sizes while keeping setup changeover times to a minimum.
Keyword: Flexibility
Unista’s goal was to meet the central demand for flexibility without compromising the engineering, the motion controls and the production process. Anthony Forget, Managing Director of Unista France, explains: “To accommodate the broad product portfolio of Shiseido, we needed an extremely flexible machine”. “Unista’s needs were very much in line with the properties of our XTS transport system, which now functions as the machine’s central component and makes the production much more flexible,” says David Ranchy, Sales Engineer at the Beckhoff office in Nantes.
Unista employed an XTS with a track length of 4 m, which enabled them to keep the machine compact and put the available floor space to its best use. The transport solution is supplemented by two 6-axis robots for product handling. The first robot takes care of the loading and unloading. It places the filled cosmetics jars on the XTS, which uses 11 movers to transport them to the respective processing stations. The second robot places lids on the containers and lightly screws them in before they are fully closed with a specific torque and rotation angle at the following handling station. At the final quality control station, the containers are sorted into good and reject units. One of the key requirements involved was protecting the high-value cosmetics containers against any kind of damage to ensure that the packaged products are in line with the high quality standards of the Shiseido brand.
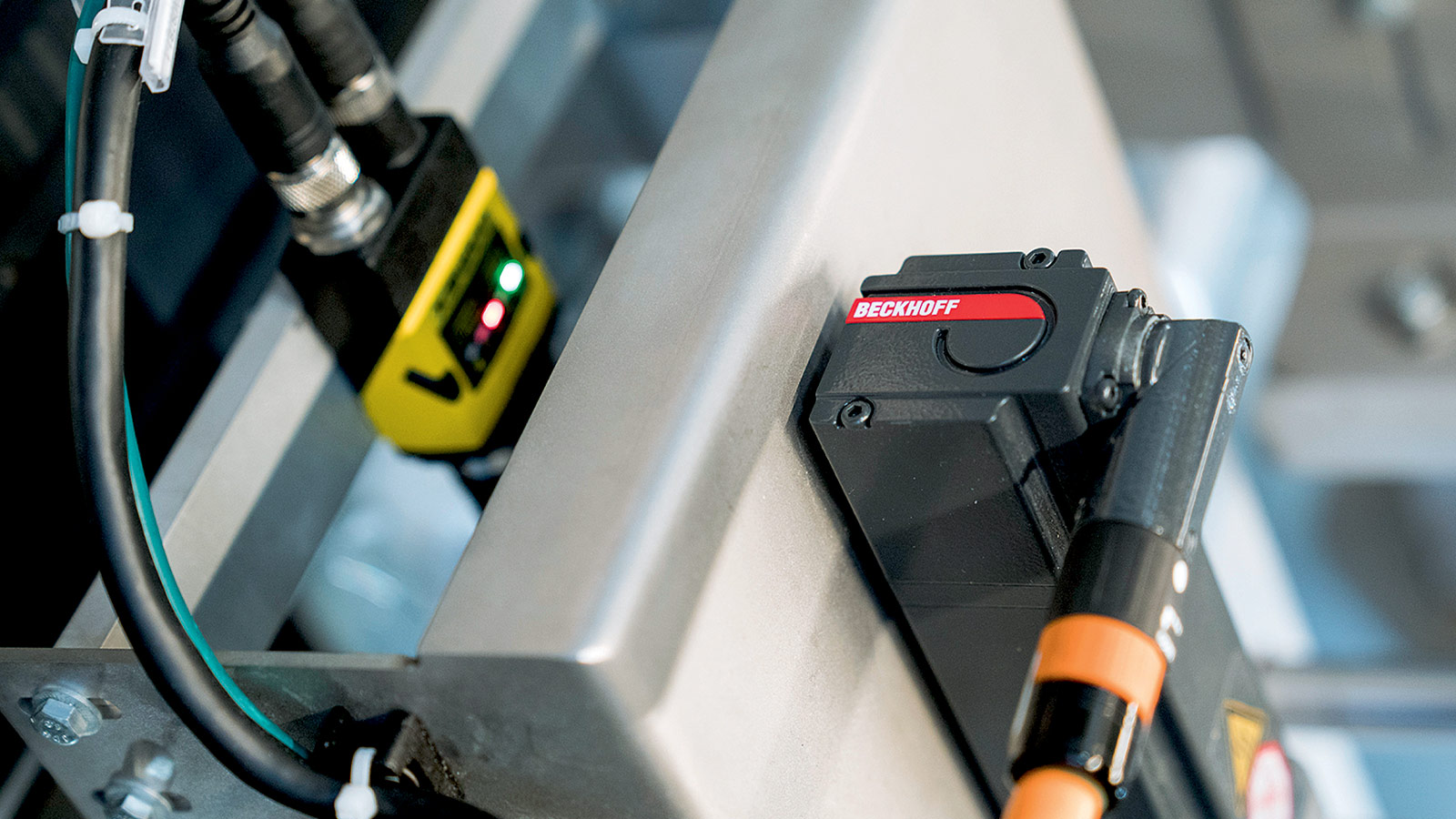
Benefit: Operational agility
One key advantage of the XTS in that context is the individual product transport, which is not subject to rigid synchronization between the processing stations. As a result of the individual and highly precise positioning with the movers, the machine delivers maximum throughput paired with gentle product handling.
In addition, the software-based control functions make it easy to adapt the system to changing formats, such as container diameters, on the fly. All it takes is a change in the software parameters instead of a complex and expensive machine reconfiguration.
A universal hardware and software platform
Besides the XTS, Unista also employs servomotor terminals and servomotors from Beckhoff for the handling unit that screws on the lids. Other components from the Beckhoff portfolio include EtherCAT Terminals for the communication between the control components as well as TwinSAFE products for machine safety. The benefits are readily apparent. Sourcing all components from a universal hardware and software platform means a single point of contact and fast and easy integration.
The entire machine is controlled by a space-saving, cabinet-mounted CX5140 Embedded PC that runs TwinCAT 3 automation software. The drive technology of the handling unit features an especially compact design. EL7211 servomotor terminals control the dynamic AM8100 servomotors, which are connected via One Cable Technology (OCT). This reduces the cabling costs by 50 percent and gives the machine a very tidy appearance. A CP3918 Control Panel displays Unista’s own user interface.
Simplified engineering and reduced time to market
The simple engineering and straightforward commissioning with XTS and PC based control enabled the experts from Unista to complete a ready-to-operate machine in less than ten weeks, as they say. With its short time to market and high degree of operational flexibility, the XTS application for Shiseido represents a prime example of mechanical engineering in the age of Industrie 4.0 that is at the forefront of cosmetics packaging.