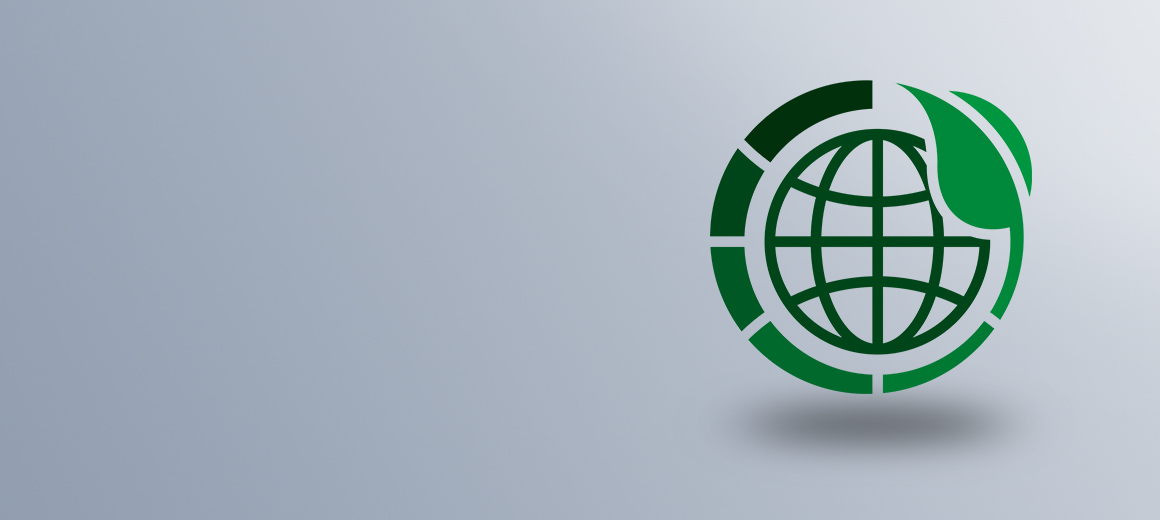
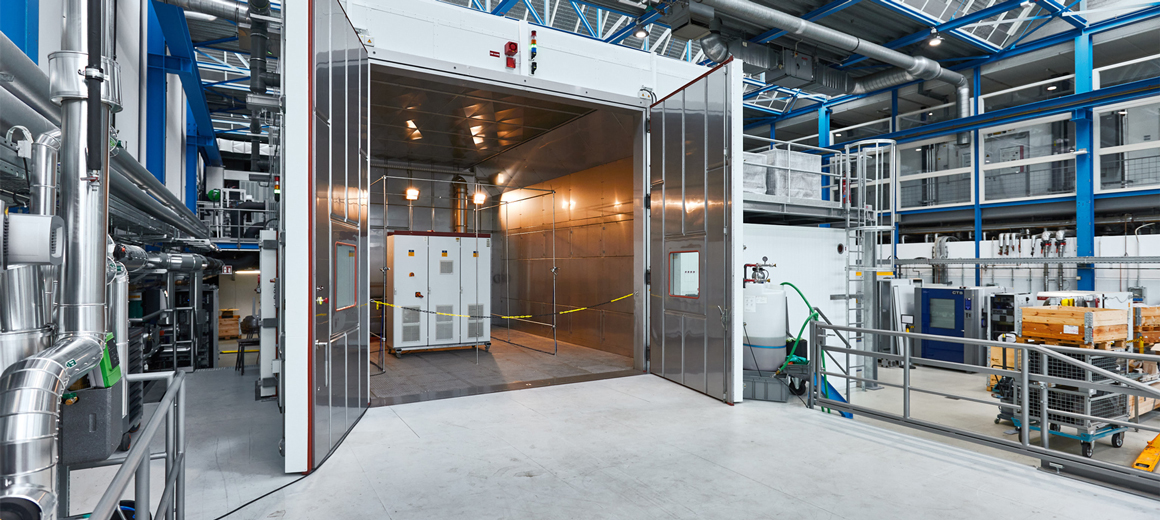
Precisely controlled stress tests increase availability
Beckhoff automates test bench for wind turbines
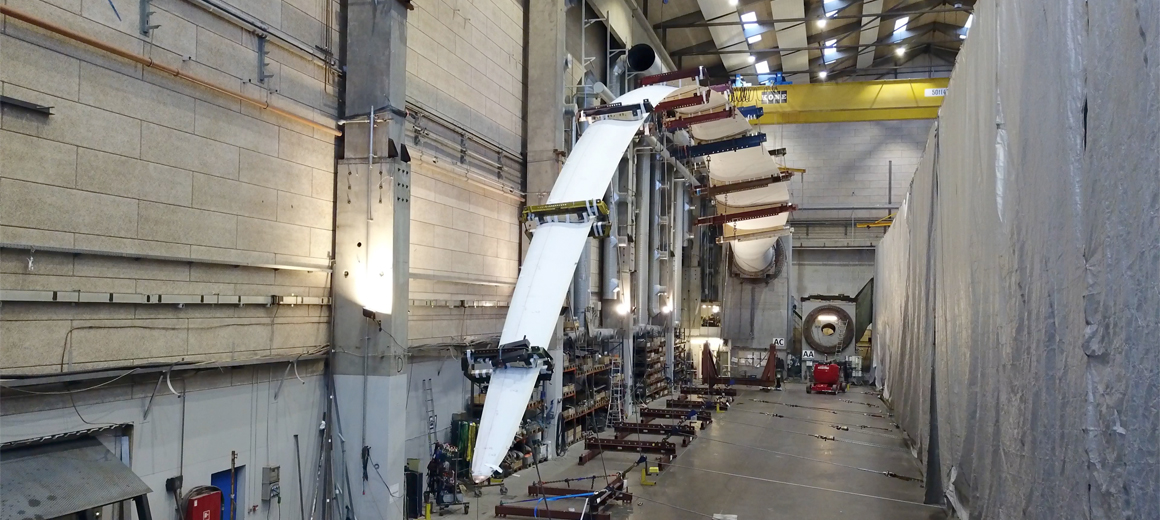
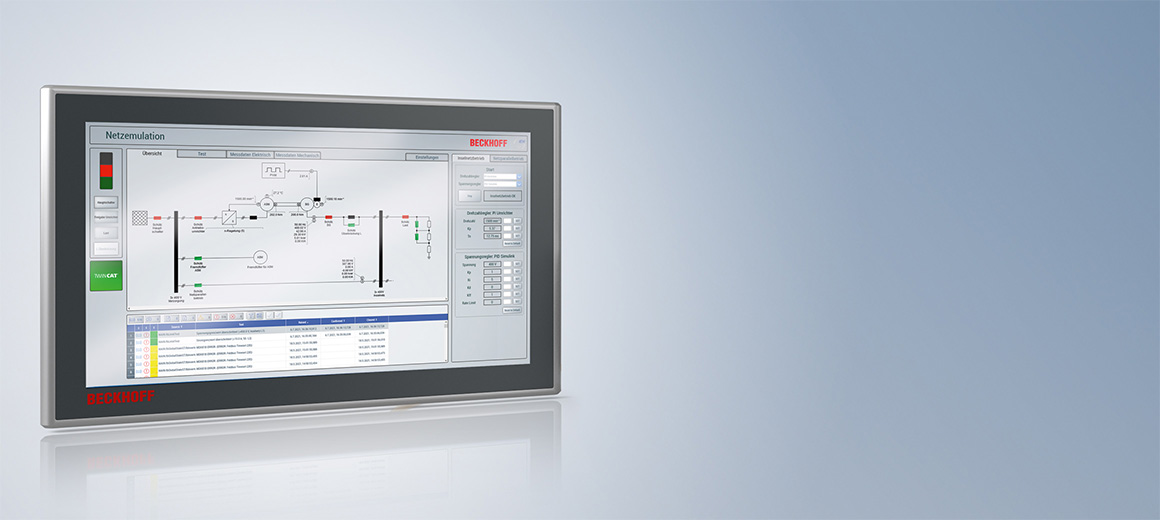
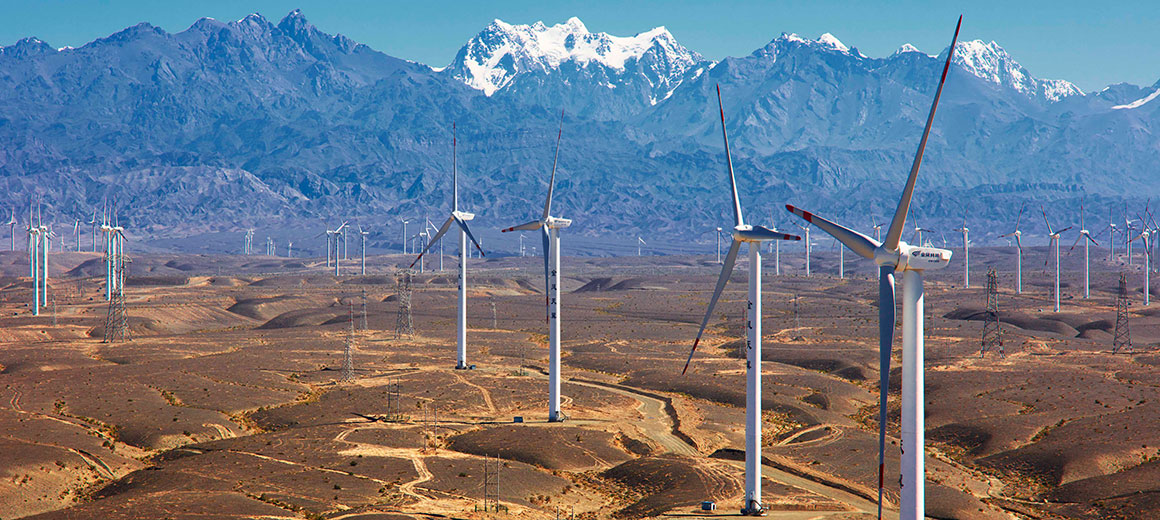
Online fault diagnostics improve wind turbine availability
Goldwind, China
Headquarters United States
Beckhoff Automation LLC
+1 952 890-0000
beckhoff.usa@beckhoff.com
www.beckhoff.com/en-us/
Precisely controlled stress tests increase availability
Goldwind, China
On the basis of the PC-based control and EtherCAT technology, Beckhoff makes system solutions available for wind turbines that have been tried and tested worldwide: more than 100,000 wind turbines all over the world up to a size of 16 MW have been automated using Beckhoff technology. In this respect, our control architecture is perfectly suited to the requirement profile of the industry: openness and scalability, flexibility in the design of the controller and a high degree of integration. All processes, from the operational management and control of pitch, converter, gearbox and brakes through to wind farm networking, are executed in software on an industrial PC. Safety technology and condition monitoring are integrated seamlessly into the terminal segment via corresponding I/O modules. A separate CPU can thus be dispensed with. The real-time Ethernet system EtherCAT offers full Ethernet compatibility and outstanding real-time characteristics. Beyond that, it is characterized by flexible topology and simple handling. In the new TwinCAT 3 Wind Framework, the turbine manufacturer has a software tool at its disposal that gives it optimum assistance in the programming of its facilities and ports the Industrie 4.0 approach to wind energy. Another advantage: Lower-level fieldbuses such as CANopen, PROFIBUS and Ethernet TCP/IP can be relocated to the field via fieldbus master or slave terminals for the control of subsystems. Software libraries and hardware components specially developed for the wind power industry round out Beckhoff’s wide range of solutions.
The expertise acquired over more than 20 years of collaboration with turbine manufacturers in the wind energy industry makes Beckhoff a reliable partner with high solution competence. Together with the international Beckhoff subsidiaries, our expertise team in Lübeck offers worldwide support for all areas of wind turbine control: The services offered range from developing application-specific software libraries to support during the commissioning phase and control cabinet construction. According to the customer’s specifications, the Beckhoff engineering department takes on the complete control cabinet construction, starting with wiring diagram design through to prototype or serial production.