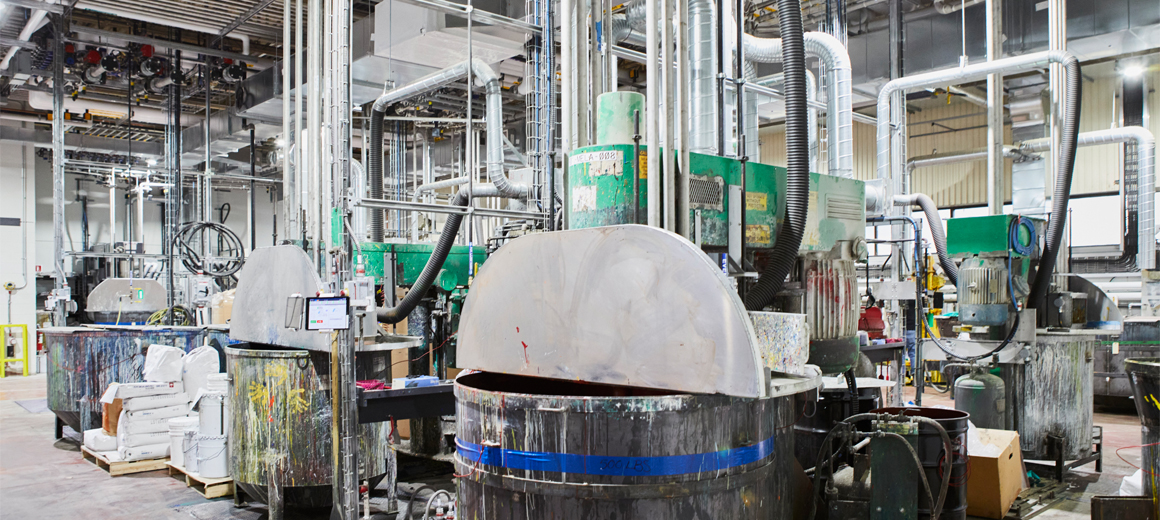
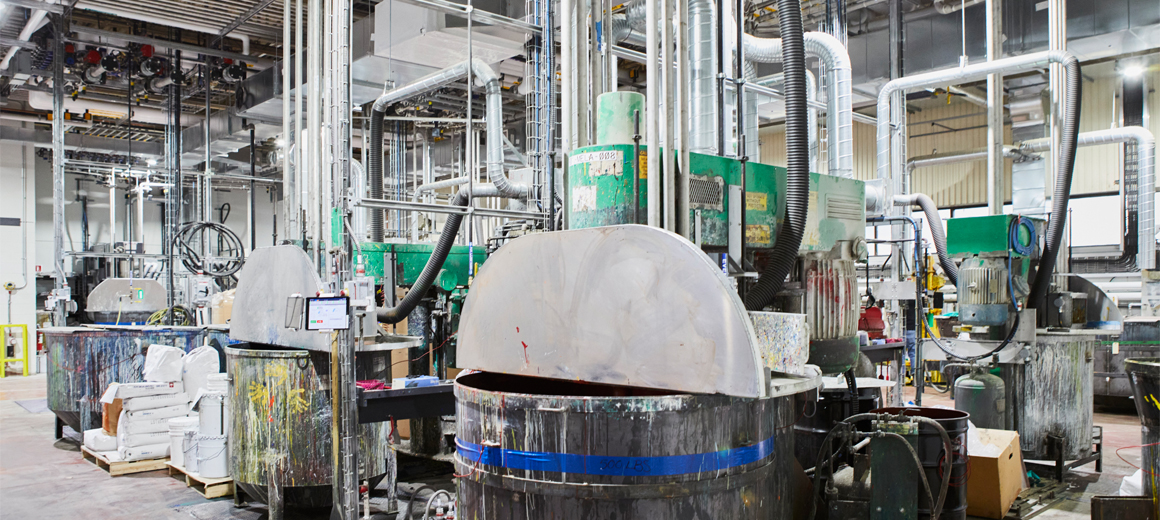
PC-based Control and EtherCAT increase process automation and data transparency
Pépin Industries Ltd. has been producing industrial paints in Canada since 1958. To automate traditional production processes when Pépin moved to a larger facility, system integrator Centris Technologies relied on the open control technology from Beckhoff. It enables continuous communication from the field level to IT, ensuring maximum transparency in all processes.
Industrial paints are critical for equipment used in harsh environments from small air compressors to heavy machinery. Paint quality and consistency directly affect surface protection, branding and more. Traditional manufacturer Pépin Industries specializes in producing solvent-based industrial paints with incredibly short turnaround times. Its batch sizes may be considered small by industry standards – typically several hundred gallons (1 Canadian gallon ≈ 4,5 l) – but this approach allows customers to order exactly what they need, when they need it.
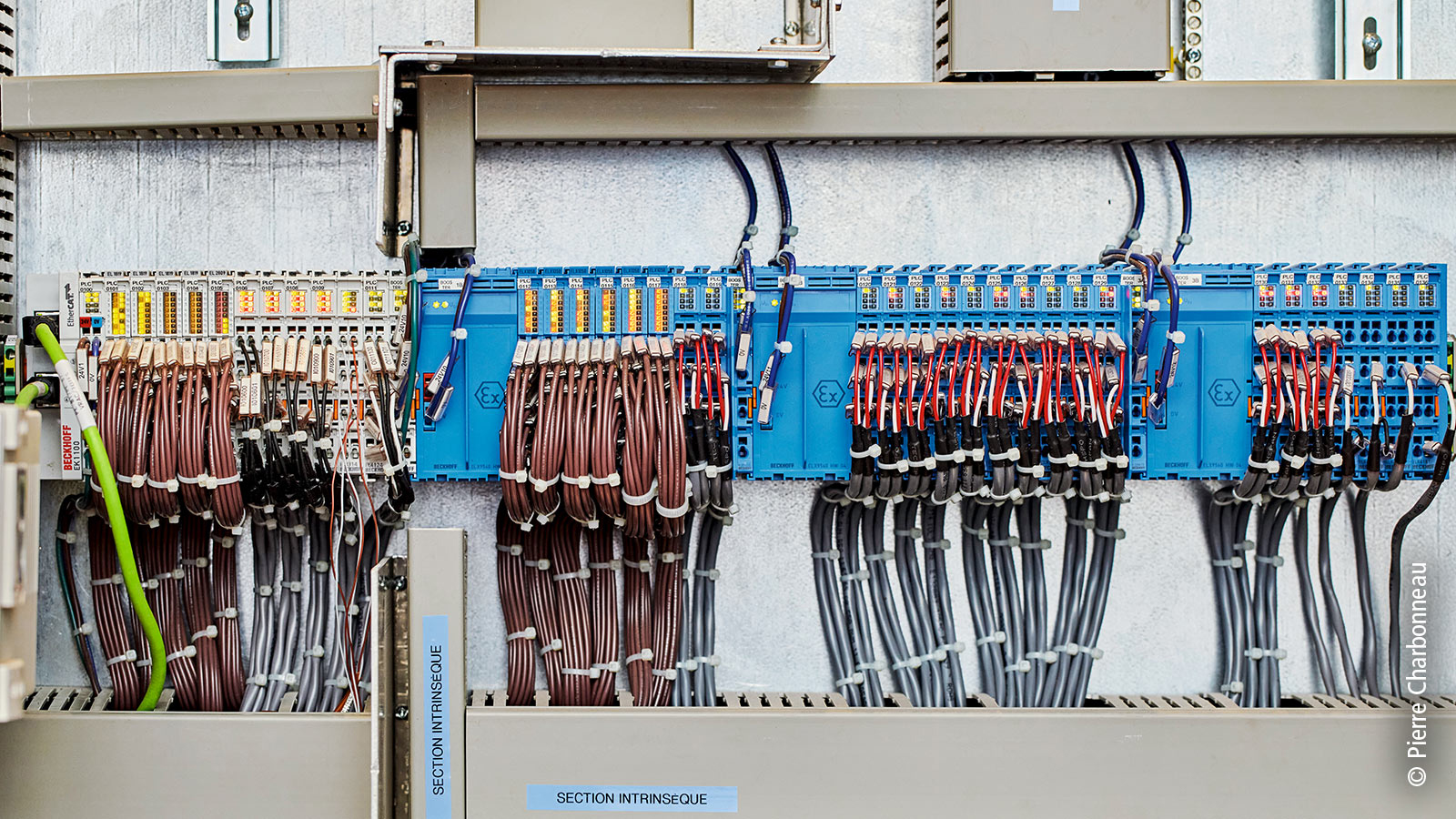
In the past, however, lingering manual processes limited order traceability, efficiency of plant staff and, as a result, the company’s ability to scale. When Pépin moved to a new facility in Cowansville, Quebec, the family-owned company turned to Centris Technologies to digitally transform its traditional operations with innovative automation solutions. The Montreal-area systems integrator had built its reputation in this market since an initial paint plant retrofit in 2010. “Over the years, we have grown our smart factory services to include automation and control, industrial software like MES or SCADA, and ERP bridges and web services integration,” says Eric Thibaudeau, Co-President of Centris.
PC-based control increases production efficiency
The technology update aimed to increase accuracy and transparency, as well as production throughput. Issues in these areas had persisted prior to the implementation, according to Hélène Daigle, Production and Lab Director at Pépin: “In the past, our highly manual process made it difficult to track everything that went on during production. The operators had work orders, but it was hard to tell how closely they followed the steps and ingredient quantities during the mixing process.” This led to rework of paint that didn’t pass quality inspection or throwing out a batch due to poor coloring, incorrect ingredient mixtures or contamination. The lack of digital records made it tough to determine what happened and correct the issue going forward. This is where Centris stepped in. The engineering team uses its IT and automation technology (AT) expertise to implement advanced concepts, including increased traceability, machine monitoring, predictive maintenance and more.
In paint plants specifically, machine control and data acquisition become more complex due to explosion hazards posed by certain chemicals. In addition, the Centris team had long relied on Industrial PC technologies but faced difficulties with their previous vendor from controller obsolescence, unreliable performance and lack of interoperability. Based on the success of a previous project implemented with Beckhoff Canada, Centris switched to PC-based control technologies from Beckhoff, and the Pépin application was no exception. “Centris offers a blend of traditional systems integration and IT solutions, so it was a natural fit for them to work with Beckhoff,” says Ted Sarazin, Regional Sales Manager at Beckhoff Canada.
Optimized mixing process through automation
Pépin’s new production facility features six bulk tanks for the most common paint ingredients and additional totes for a variety of others, including additives, resins, sands, etc. The automated system transfers materials from the tanks and totes to the correct mixing station, and it replenishes tanks from incoming shipments. The system controls temperature and pressure while monitoring ingredient levels and other factors. As such, it ensures there is enough of each ingredient and that they maintain the right viscosity during transfer. In the past, operators had to push around large vats and measure out ingredients by hand before mixing, but now they initiate and manage the processes at each mixer. Tablets – either handheld or mounted on the workstation – offer simple control, insights and alarms when needed.
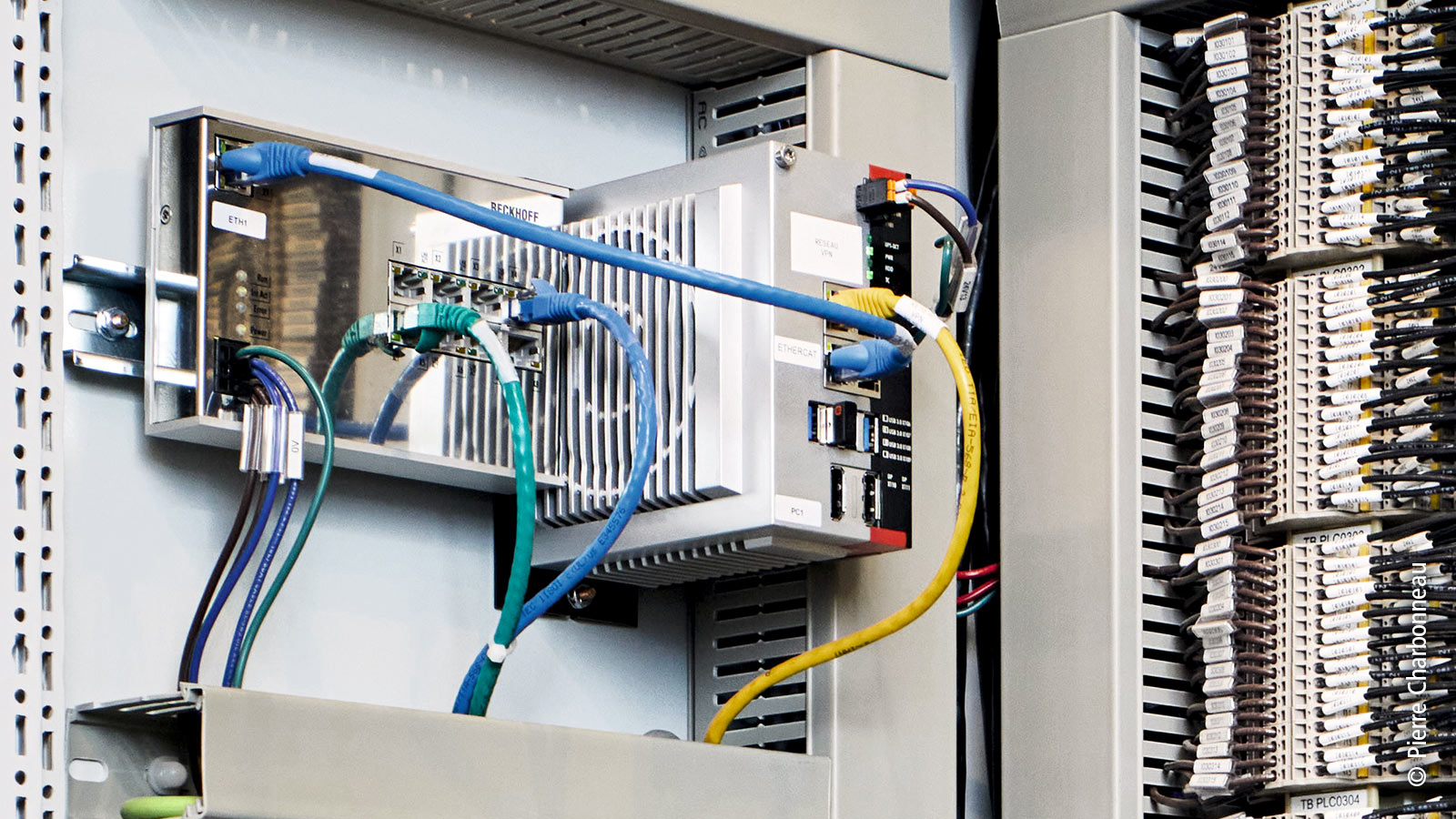
A C6030 ultra-compact Industrial PC from Beckhoff serves as the central controller. “Beckhoff Industrial PCs are very powerful and offer fast cycle times,” says Marc-André Duguay, Industrial Software Developer at Centris. “It’s easy to access data, and the programming and troubleshooting are simple in TwinCAT software, especially with Structured Text.”
The openness and connectivity of Beckhoff PC-based control enables communication with the Centris-developed SCADA via OPC UA. It also simplified integration of the plant’s local network via TCP/IP for communication between the controller and the tablets. The continuing ERP upgrade will also benefit from the technologies’ AT-IT convergence.
Efficient networking with EtherCAT even across hazardous areas
EtherCAT provides continuous field-level communication. ELX series EtherCAT Terminals from Beckhoff allow installation in the same segment with standard I/O for direct connection with field devices through to zone 0 hazardous areas. This approach eliminates the costs and labor requirements for additional explosion-proof enclosures and safety barriers needed in traditional explosion protection concepts.
“EtherCAT is also very easy to configure: We just connect the I/Os, click ‘Scan’ and TwinCAT finds all of the nodes,” Marc-André Duguay adds. Apart from the ELX terminals, Centris leveraged numerous IP20-rated EtherCAT Terminals from Beckhoff, including the TwinSAFE terminals for integrated functional safety. Remote segments connected via EK1100 EtherCAT Couplers communicate to pneumatic valves, large compressors, variable-frequency drives for mixing paints and other devices. EtherCAT supports free selection of topology, including line, star and tree. Ring topology, in particular, provides the necessary cabling redundancy for the Centris system, according to the software developer.
In addition, the open Ethernet fieldbus simplifies communication across multi-vendor architectures. Beckhoff provides gateways and bus couplers to more than 30 prominent communication protocols for this purpose. The Beckhoff CU2016 16-port Ethernet switch, for example, easily incorporated scales for measuring raw materials over EtherNet/IP. Moreover, TwinCAT enables communication to the gas detection and ventilation system via BACnet. In addition, the simple integration of building automation and industrial automation allows the customer to see all ventilation information in the SCADA, Marc-André Duguay explains: “If chemical fumes reach certain levels, it’s very dangerous. The plant has alarms to protect operators, but the visualization provides additional critical information.”
Automation and IT technologies mix to yield impressive results
The digital transformation at Pépin increased throughput by more than 150%. “With the new system, we increased production from eight to 12 batches per day – some days, as many as 15 – and our average batch size increased from 180 gallons to 300 gallons,” Francis Pépin, Director of Operations, reports.
The industrial paint producer achieved greater transparency while optimizing production scheduling and its ability to analyze and improve processes based on actionable data insights. Increases in accuracy have greatly reduced post-production adjustments and related material waste. “Having better control of the production process allowed us to decrease our number of batches put in rework from two to three per month to just one per quarter,” Hélène Daigle says. “Our workers spend less time looking for raw material in the warehouse as most ingredients for a batch are either pre-weighted or come from the automated system.”
For Centris, the use of PC- and EtherCAT-based automation technologies continues to enhance the team’s efficiency in a wide variety of projects. Commissioning times have accelerated since the company’s transition to the Beckhoff technology, even in complex systems. “Having Beckhoff as our main control platform partner is reassuring, since they remain on the leading edge of automation and continue to enhance their technology offerings,” says Michel Kakos as one of Centris’ founders.