
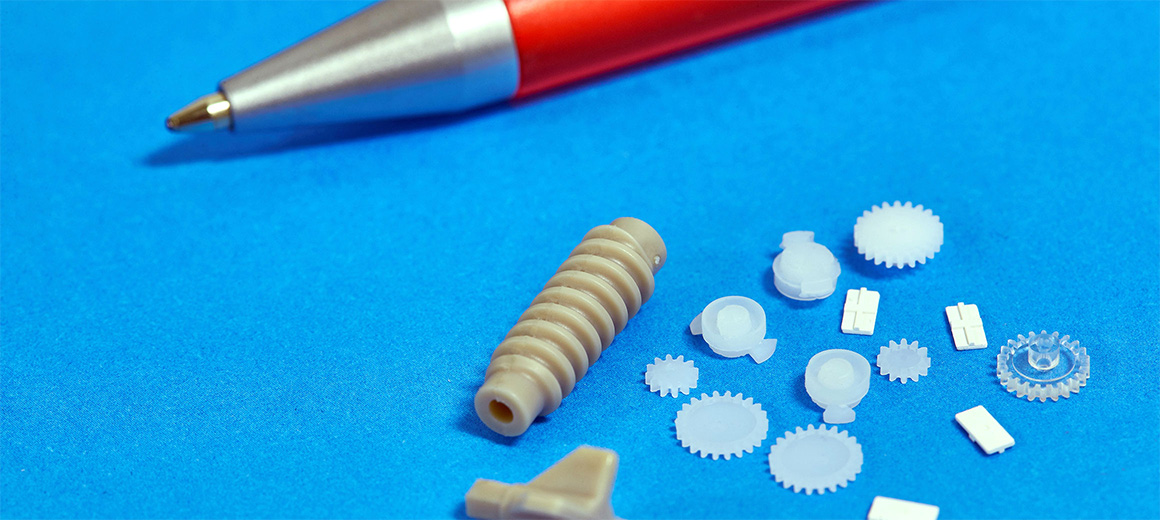
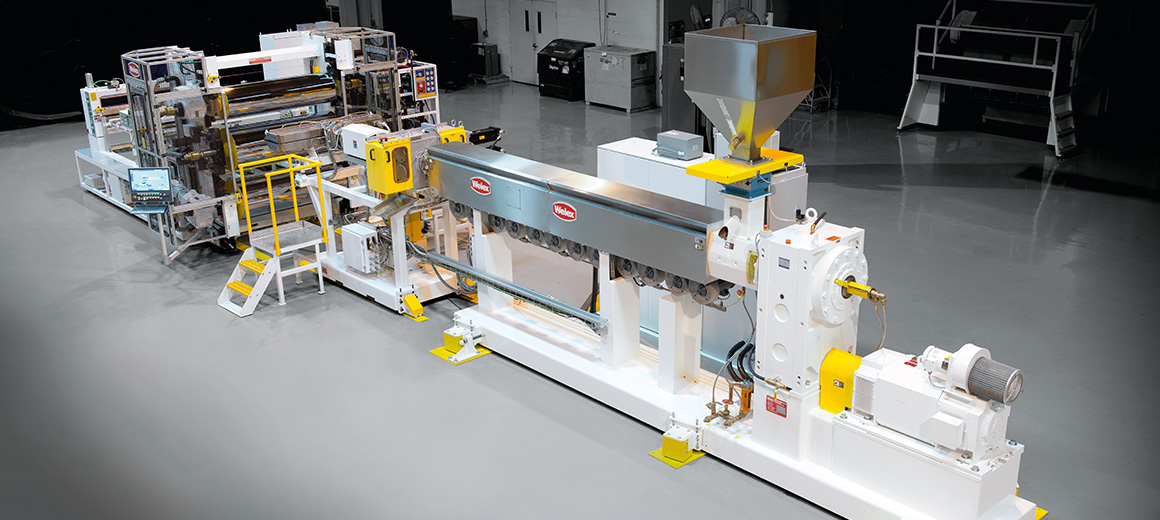
PC-based control becomes the standard for sheet extrusion applications
Graham Engineering, Pennsylvania, USA
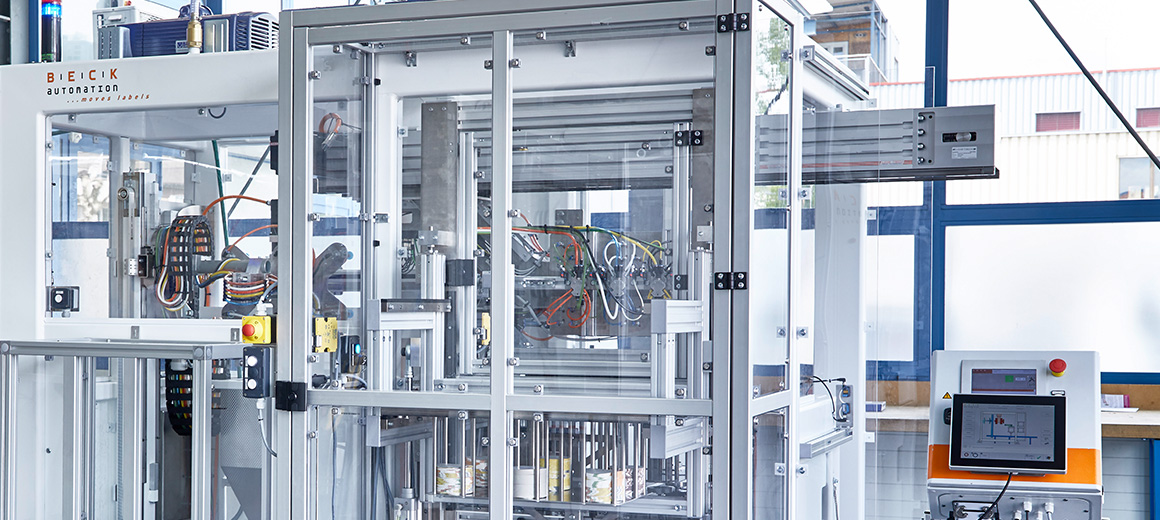
Headquarters United States
Beckhoff Automation LLC
+1 952 890-0000
beckhoff.usa@beckhoff.com
www.beckhoff.com/en-us/
Graham Engineering, Pennsylvania, USA
It's impossible to imagine the world without plastic products and demand continues to rise. Even the ongoing discussions around resource conservation and sustainability have not initiated a U-turn – plastics processing continues to gain in importance globally. However, demands for the sustainable production of plastics and a circular economy are increasingly becoming drivers of innovative technologies and processes in the industry. The requirements for plastics machines with regard to high product quality and productivity, but at the same time with a reduction in resource consumption, are met in all applications with innovative control technology from Beckhoff: from injection molding and blow molding to extrusion and thermoforming.
Your head start in the plastics industry with Beckhoff:
With the TwinCAT 3 Plastic Framework, we offer a modular software solution for controlling plastics machinery that minimizes development work and maintains the open nature of Beckhoff architecture. The TwinCAT 3 Plastic Framework brings together our many years of expertise in plastics, seamlessly integrating important industry-specific functions into the established TwinCAT environment. As a result, plastics machinery can be programmed, visualized, and controlled on a single platform.
The TwinCAT 3 Plastic Framework offers both software packages and application solutions for PLC and HMI which act as a launchpad for developing a specific application solution. The Plastic Processing Framework (TF8540) offers comprehensive software-based temperature control, the Plastic Technology Functions (TF8560) provide motion function blocks, and the Plastic HMI Framework (TF8550) consists of elements and functions that allow a machine to be mapped out visually. All software packages are specifically developed for use on plastics machinery and can be seamlessly integrated into TwinCAT 3. The TwinCAT 3 Plastic Application project, consisting of a PLC and HMI, combines all software packages into the ideal application solution for plastics machinery. Application-specific templates already included in the HMI project, sample code in the PLC project, and the TwinCAT 3 Plastic Base Application library offer free sample integration and facilitate project planning and programming for various plastics applications.
TF8540: Plastic Processing Framework
TF8550: Plastic HMI Framework
TF8560: Plastic Technology Functions
TwinCAT 3 Plastic Application
HMI project:
PLC project:
Open automation technology with EtherCAT: ideally suited for injection molding machines
Open automation technology: minimizes the energy consumption of electric blow molding machines
Open automation technology with fieldbus diversity: ideally suited for extrusion lines
Open automation technology with EtherCAT: perfectly suited to the additive manufacturing of plastic parts
Open automation technology with EtherCAT: perfectly suited to the handling of plastic parts
PC-based control optimizes the post-processing and further processing of plastic parts