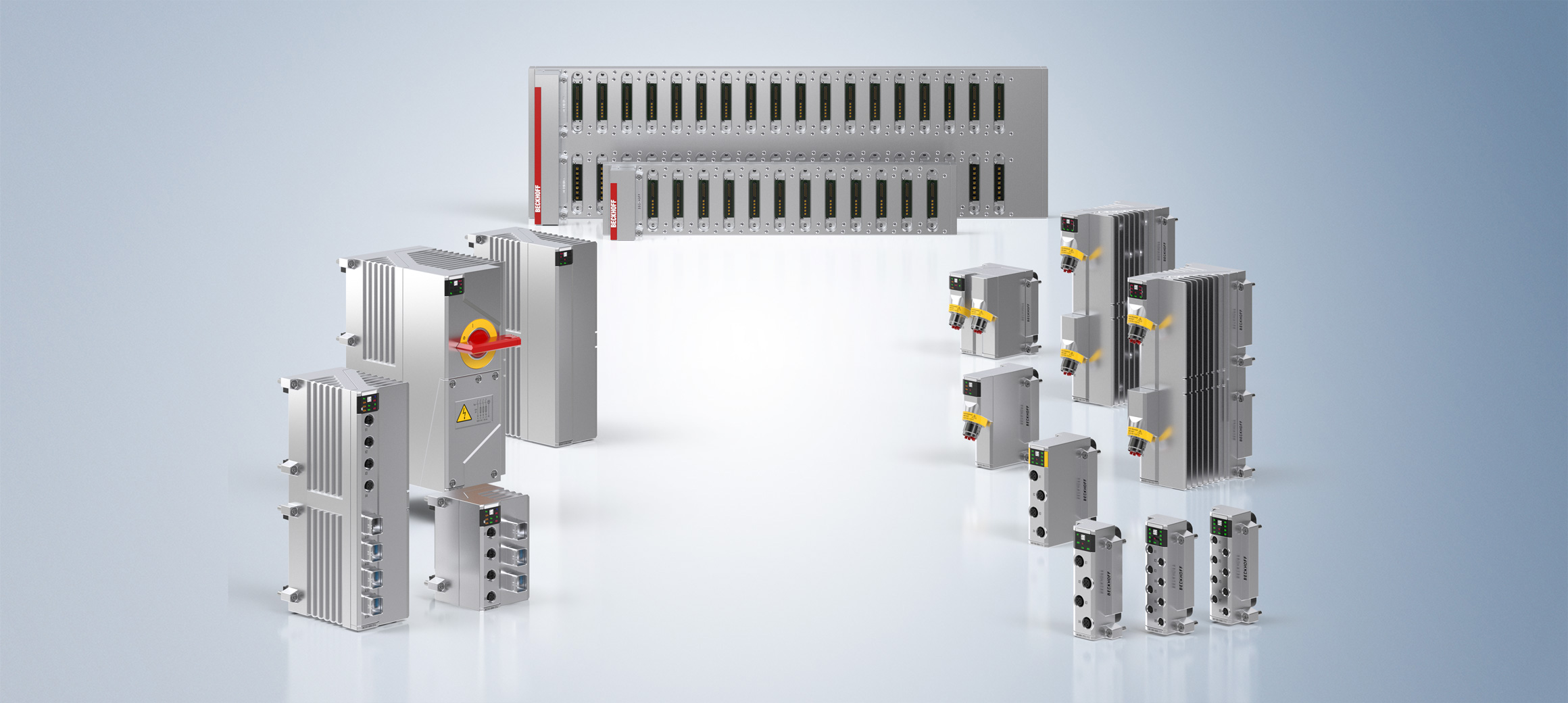
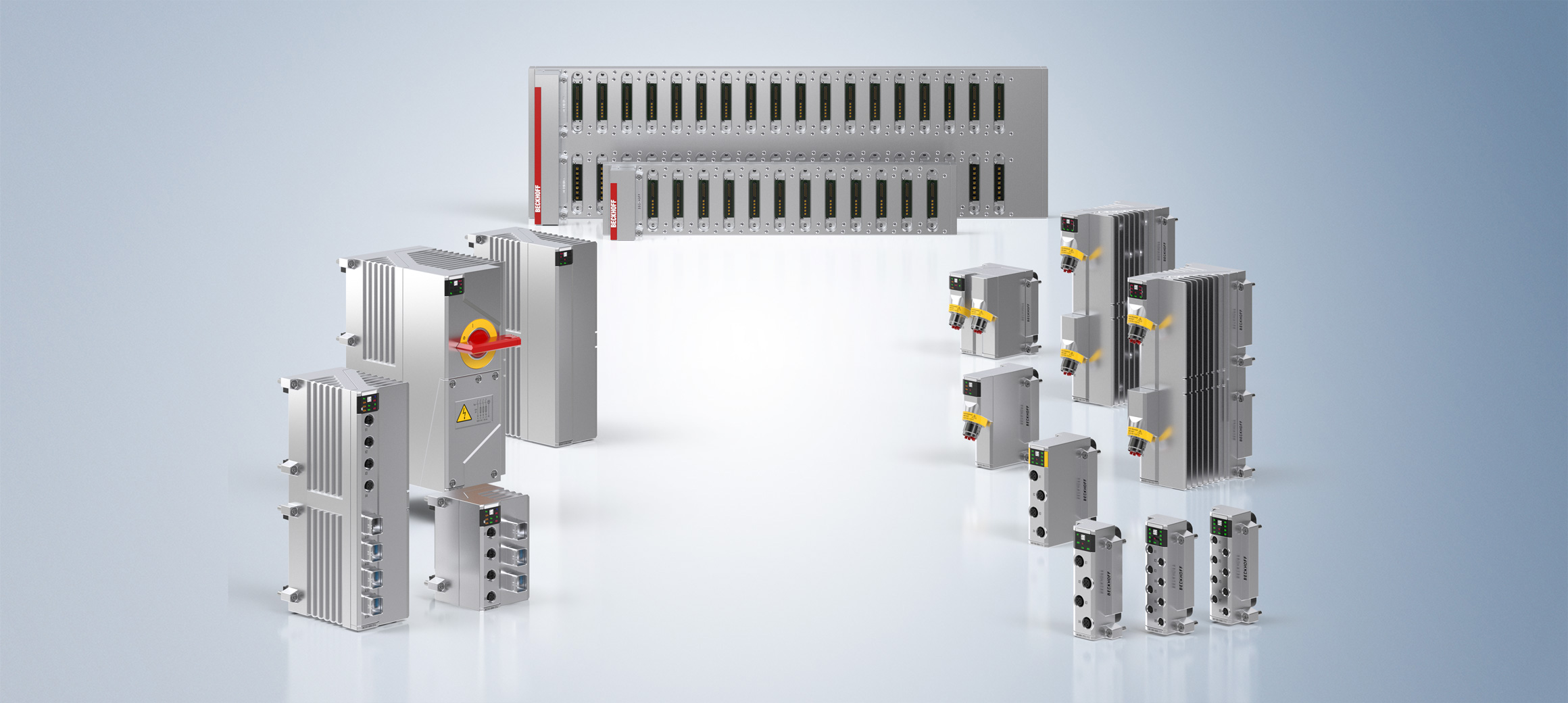
The Beckhoff MX-System: New construction kit for automation replaces the control cabinet!
The new MX-System from Beckhoff is quite simply a revolution in control cabinet construction. In this interview, Managing Owner Hans Beckhoff and MX-System Product Manager Daniel Siegenbrink explain where this claim comes from and how the conventional control cabinet can be replaced.
Beckhoff has always been synonymous with technical innovation, so what can we expect as the next development step in automation?
Hans Beckhoff: That’s right, we certainly have introduced our fair share of revolutions in the automation sector. My particular favorites include the principle of PC-based control technology in general, as well as the bus terminals as decentralized I/Os, and our EtherCAT communication protocol, which is now established as a global standard. Looking back on over 40 years of our company’s history, we have been able to build up a wide range of experience in how to fundamentally improve automation technology. What’s more, Beckhoff is not only an automation specialist, but also a successful control cabinet manufacturer with around 250 employees. We are now in the process of channeling this comprehensive expertise in both technological and practical terms into an innovative new product range that we believe will change the face of automation as we know it.
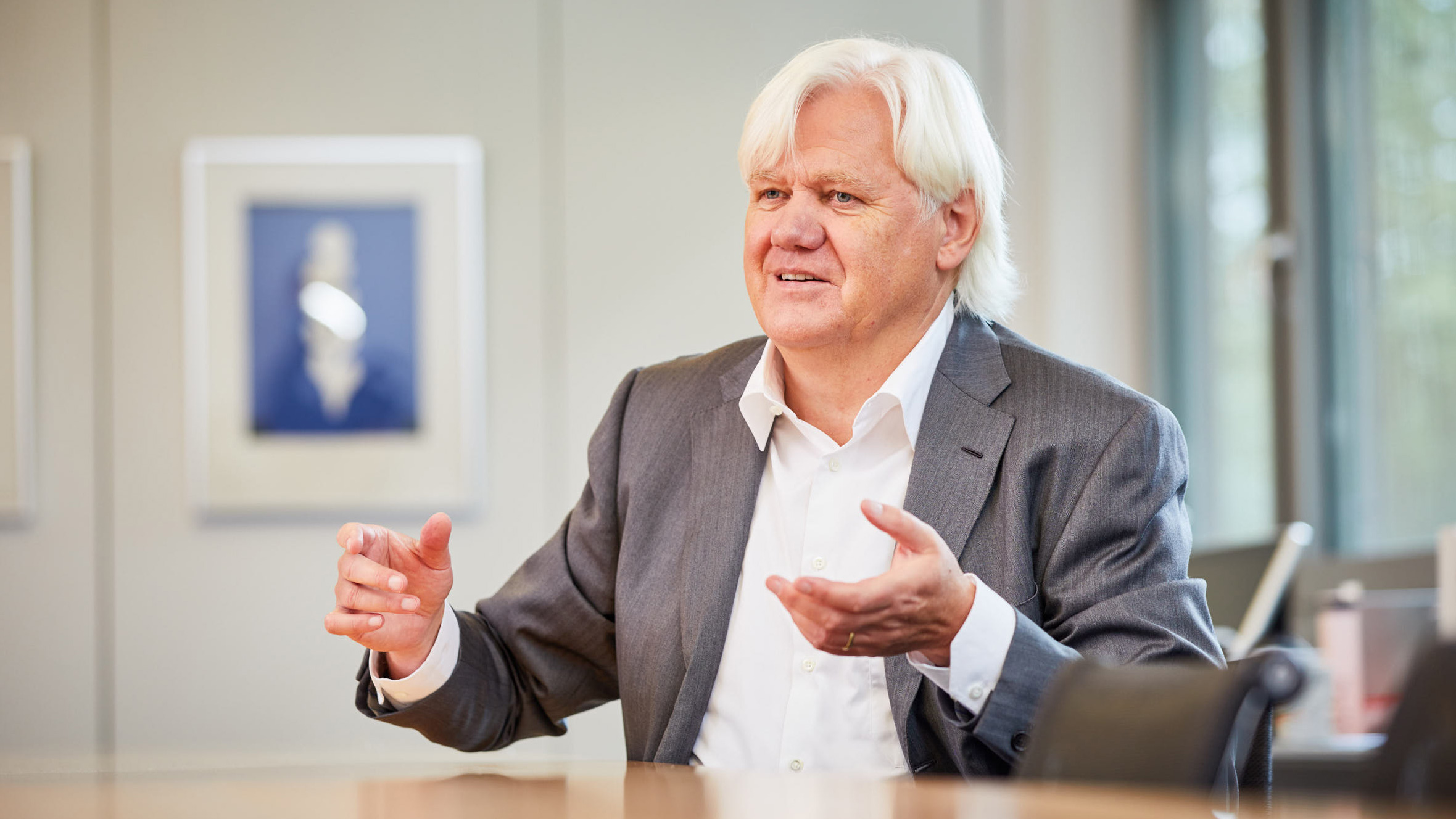
So what exactly can we expect from this new product range?
Hans Beckhoff: Well, I’ve already touched on the fact that we have extensive practical experience in the field of control cabinet construction. So we have combined this experience with our know-how in our other product areas, which covers IPCs, I/O and communication technology, drive technology, and software. The result of this is a uniform modular automation component kit that completely replaces traditionally wired control cabinets with standardized modules. All of the technical systems and functions required in the control cabinet or on the machine are combined in a single system known as the MX-System.
Daniel Siegenbrink: In principle, every control cabinet is constructed in the same way: There is always a power supply, main switch, power supply units, the controller including I/O level and fieldbus, as well as the drive technology. There’s also the power distribution, which refers to the switching of 400 V, the direct start of motors, or the supply of external units. We have standardized these recurring blocks and implemented them in a uniform concept in the form of the MX-System.
How is the MX-System structured in detail?
Hans Beckhoff: The basic requirement is an extremely robust mechanical solution offering IP67 protection that is capable of accommodating all automation modules directly on the machine in a practical and solid manner. This is what prompted us to implement what we are referring to as our baseplate concept. First and foremost, this includes the baseplate itself, which consists of a highly mechanically stable aluminum profile and, in addition to the mechanical enclosure, also includes backplanes, on the one hand for control voltages and communication, and on the other hand for supply voltages. Furthermore, various connectors – data and power connectors – are defined, which can be used to plug in function modules. This is the basis for a modular control cabinet system that can be mounted directly on the machine without the need for additional protective housings due to the robust design of the baseplate and module. A central, manually installed control cabinet is therefore no longer necessary.
How can this be used to implement a control cabinet function in concrete terms?
Hans Beckhoff: With the corresponding function module, for example, a drive can simply be plugged on a connector in the baseplate and screwed tight with robust captive screws. It is then automatically supplied with EtherCAT, i.e. the communication, the corresponding control voltages and power voltages. That’s all there is to it! A minute later and the drive is fully installed! With regard to the motor connection, our proven One Cable Technology (OCT) is – of course – available on the front of the module. The other modules are constructed in the same way, so for the electrical supply, for example, this involves a UL-compliant supply module with a main switch and integrated power supply unit. All in all, the MX-System covers every conceivable automation environment, spanning digital, analog, and safety I/Os, power supplies for a 600 V drive DC link voltage and other power output stages, right through to pluggable Industrial PCs. It really is amazing how quickly a control cabinet can be built with the MX-System! Individual, customer-specific special functions that are not covered by our standard construction kit are also supported by the MX-System. Any functions can be integrated via empty housings with a corresponding MX-System interface or via separate control boxes connected via EtherCAT.
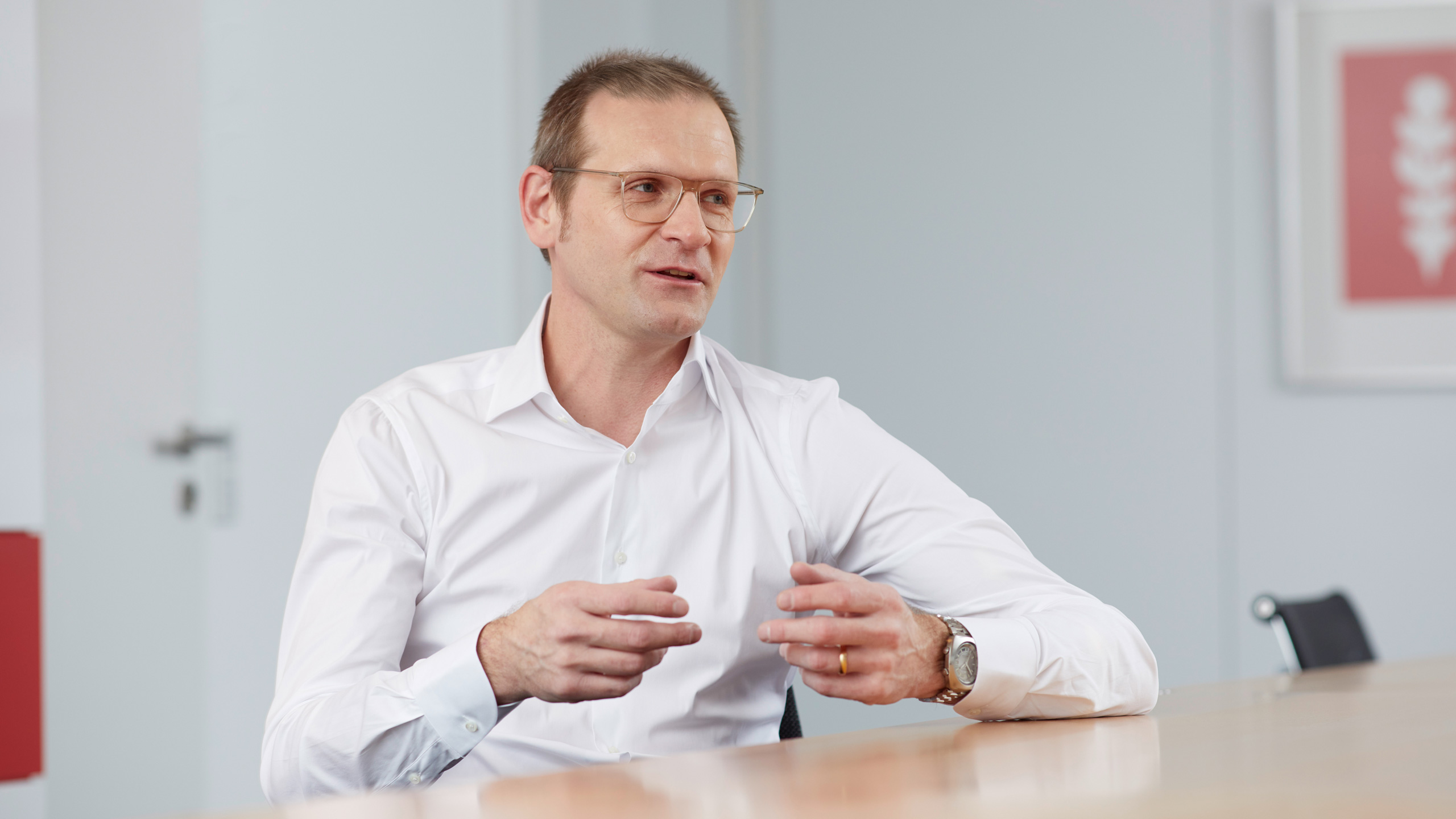
Daniel Siegenbrink: We really do cover all of the functions required on the machine. The modules – which are hot-swappable, I should point out – are divided into the PC, I/O, and Motion product areas as well as the new Relay and System segments. This also includes some new products such as frequency inverters, relays, contactors, hybrid motor starters, 24 and 48 V power supplies and power outputs.
Hans Beckhoff: It goes without saying that we benefit from the broad spectrum of our PC- and EtherCAT-based control and drive technology by being able to draw on proven technologies. Nevertheless, we have virtually reinvented the entire Beckhoff product range for the MX-System and made it pluggable from both a performance and control point of view. We have also been working with various lead customers from the very beginning, i.e. for more than three years now, in a bid to take a targeted approach to our development with the practical applications of our customers in mind. This has helped us massively with the system specification.
Speaking of specifications, what are the framework parameters for using the MX-System?
Hans Beckhoff: The MX-System is designed for a maximum rated current of 63 A and for 1-phase voltages of up to 265 V AC and 3-phase voltages up to 530 V AC. The permissible temperature range is from 0 to 50 °C, with purely passive cooling.
Daniel Siegenbrink: The following parameters apply to the individual connectors: The data connector provides EtherCAT communication as well as 24 or 48 V DC and up to 20 A, while a power connector provides the 3-phase AC voltages (plus neutral conductor and PE) as well as the DC voltages of up to 848 V for the DC link of the drive technology at a maximum of 63 A for one module. Another important aspect for practical use concerns certifications. The MX-System is a control cabinet replacement that complies with the relevant control cabinet standards. But that’s not all. Unlike conventional control cabinets, it offers a uniform solution for CE, UL CSA, and IEC. This means that machine builders can actually manufacture from stock and simply decide where in the world they will ship the machine on the day of delivery.
What other advantages are there for machine and system manufacturers?
Hans Beckhoff: The advantages of the new modular system are apparent as early as the design phase. This is because the complexity of a control cabinet with all the individual wire connections, individual wire markings and the level of design effort for the subsequent control cabinet construction is drastically reduced. With the MX-System, modules only have to be plugged onto a plate, as an electrical control cabinet terminal, so to speak, similar to a pneumatic valve terminal. According to some pilot customers, this means – for example – that 300 pages of circuit diagrams are reduced to 30 pages and the associated workload is also reduced by 90%. These are immense savings that should also translate into lower costs.
Daniel Siegenbrink: Today, our customers think in terms of compact machine modules, but they also always have to consider the control cabinet as a higher-level unit, so to speak. Not only does this require a lot of cabling work, but the modularity of the machine concepts cannot be fully represented in this way. With our system, on the other hand, this is no problem at all, as the control cabinet can be distributed around the machine on a modular basis rather than being a large monolithic block.
Hans Beckhoff: The minimized space requirements are yet another crucial factor. Machine builders can mount the compact MX-System directly on the machine body, which eliminates the need for a separate control cabinet with its own cable routes. This simplifies the installation process considerably, especially in conjunction with pre-assembled cables. It also means that the pluggable installation can now be handled by a mechanic rather than electricians only.
What does the MX-System mean for control cabinet construction itself?
Daniel Siegenbrink: Today, control cabinet construction is usually a complicated process involving a whole load of components and process sequences. There’s also a certain susceptibility to errors and high spatial requirements to factor into the equation. This is where our pluggable technology helps by simplifying not only the circuit diagram but also the level of wiring effort. Analyses have also shown that, in some cases, 90% of previous parts list items are no longer needed. This eliminates a great deal of effort when it comes to control cabinet construction.
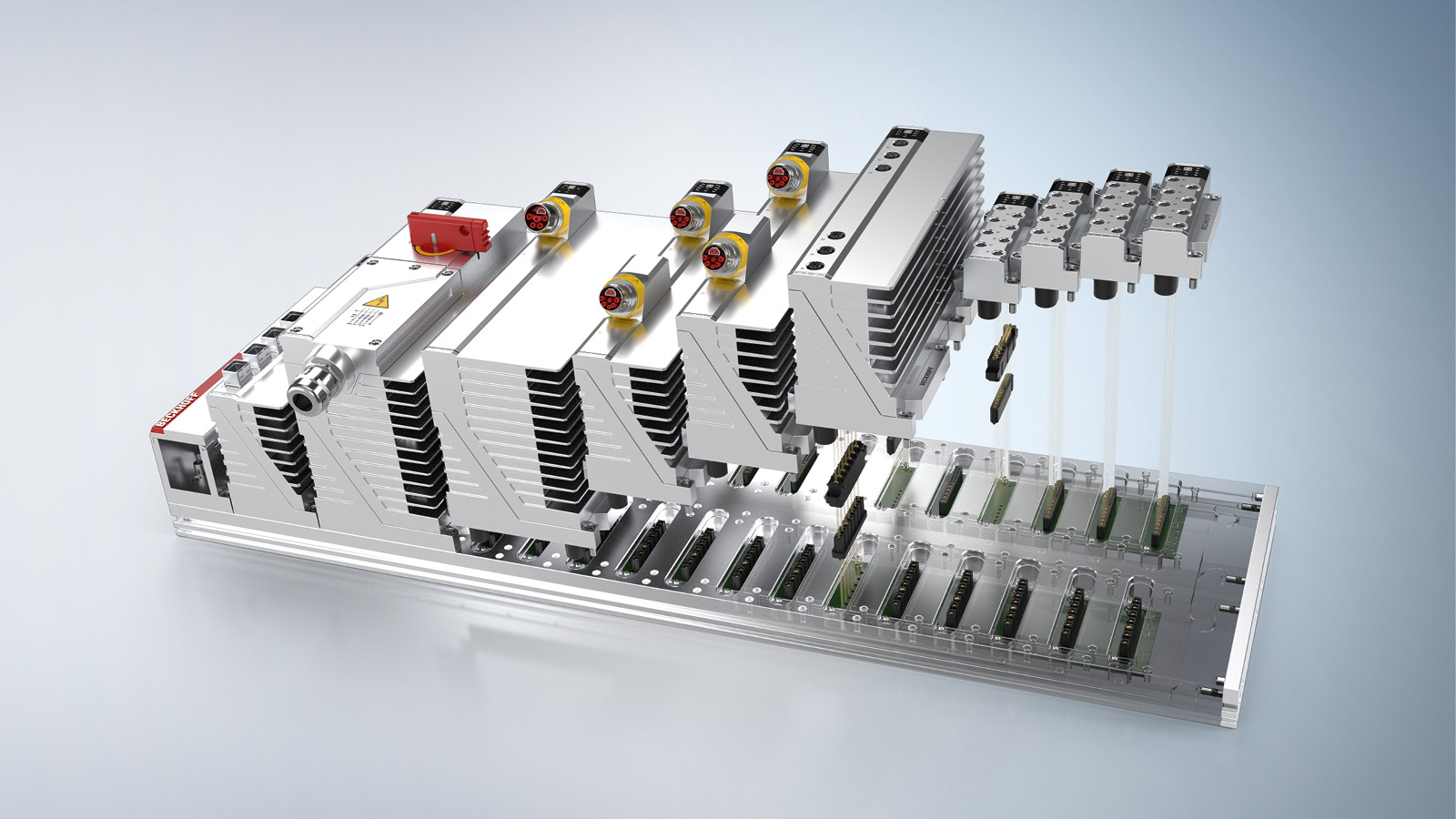
Hans Beckhoff: And just as machine planning benefits from the minimized amount of effort, so too does control cabinet construction. According to our estimates, for example, what would once have taken 24 hours for control cabinet assembly can now be cut down to around one hour of module installation. And what’s more, the quality of the control cabinet will also improve. As for the complex individual wiring, this is all replaced by a simple, error-free plug-in functionality. We have also created further cost savings by moving away from the previous manual individual production processes in favor of industrial module prefabrication. And furthermore, many machine builders will be able to simplify their logistics, since this easy-to-install technology eliminates the need for external control cabinet construction.
To what extent do end users benefit from the MX-System?
Hans Beckhoff: We believe that our MX-System will generate huge benefits, especially for the end users of the machine. By encapsulating the individual automation functions in a single module, simple diagnostics for electrical faults can be performed at module level. In the event of a fault like this, typically only the electrician is allowed to open the control cabinet to check a voltage or a contactor with the aid of a measuring device. But with the MX-System, this is no longer necessary, since the control cabinet itself no longer exists and the actual function has migrated to a module. This means that the maintenance engineer only has to determine the state of the module – using status LEDs, a smartphone and Beckhoff Device Diagnostics – to decide whether the module, the cable to the field device, or the field device itself needs to be replaced.
Daniel Siegenbrink: In many companies, there is often a lack of suitable maintenance personnel who can carry out service or repairs for the increasingly complex control technology. From this point of view, too, the easy interchangeability of the modules and the comprehensive diagnostic concept are of immense importance for the end user. Especially since, unlike in the classic control cabinet, the MX-System only uses networked components. Thus, the MX system is a complete “IoT control cabinet" that enables our customers to also integrate previously passive control cabinet components, such as a contactor or fuse, into predictive maintenance concepts. At the same time, Beckhoff Device Diagnostics is also based on the fact that each MX system module and also the baseplate is an EtherCAT device.
Could you go into a little more detail about this diagnostic concept you mention?
Daniel Siegenbrink: Well, on the one hand, this includes the extensive diagnostic options of EtherCAT that people are already familiar with. This is supplemented by a unique serial number for each module, which is placed on the front as a DataMatrix code. The code can be scanned via a smartphone app, which connects the smartphone to the controller by wireless technology and then displays the respective diagnostic data, such as the module status or error memory. In this way, the smartphone becomes a ‘universal digital voltmeter and scope’, which goes above and beyond simply replacing classic measuring devices. The maintenance or service technician benefits from precise information about the state of a function or assembly without having to measure up the hardware.
Hans Beckhoff: With this concept, we are introducing Beckhoff Device Diagnostics in general, in that every intelligent Beckhoff product is issued with a corresponding unique serial number, which can be read in externally via the DataMatrix code or internally via EtherCAT communication.
Which customers does Beckhoff want to appeal to with the new MX-System?
Hans Beckhoff: We believe that we can solve virtually all automation tasks with our new system! The MX-System is designed to cover the widest possible range of applications, just like the traditional control cabinet itself, which we ultimately want to replace with it. Of course, the MX-System is a perfect fit in terms of mechanical engineering, but the system should also offer users significant benefits when it comes to process technology, measurement technology, and much more besides. The MX-System will offer huge advantages in any scenario involving electrical energy and intelligence.