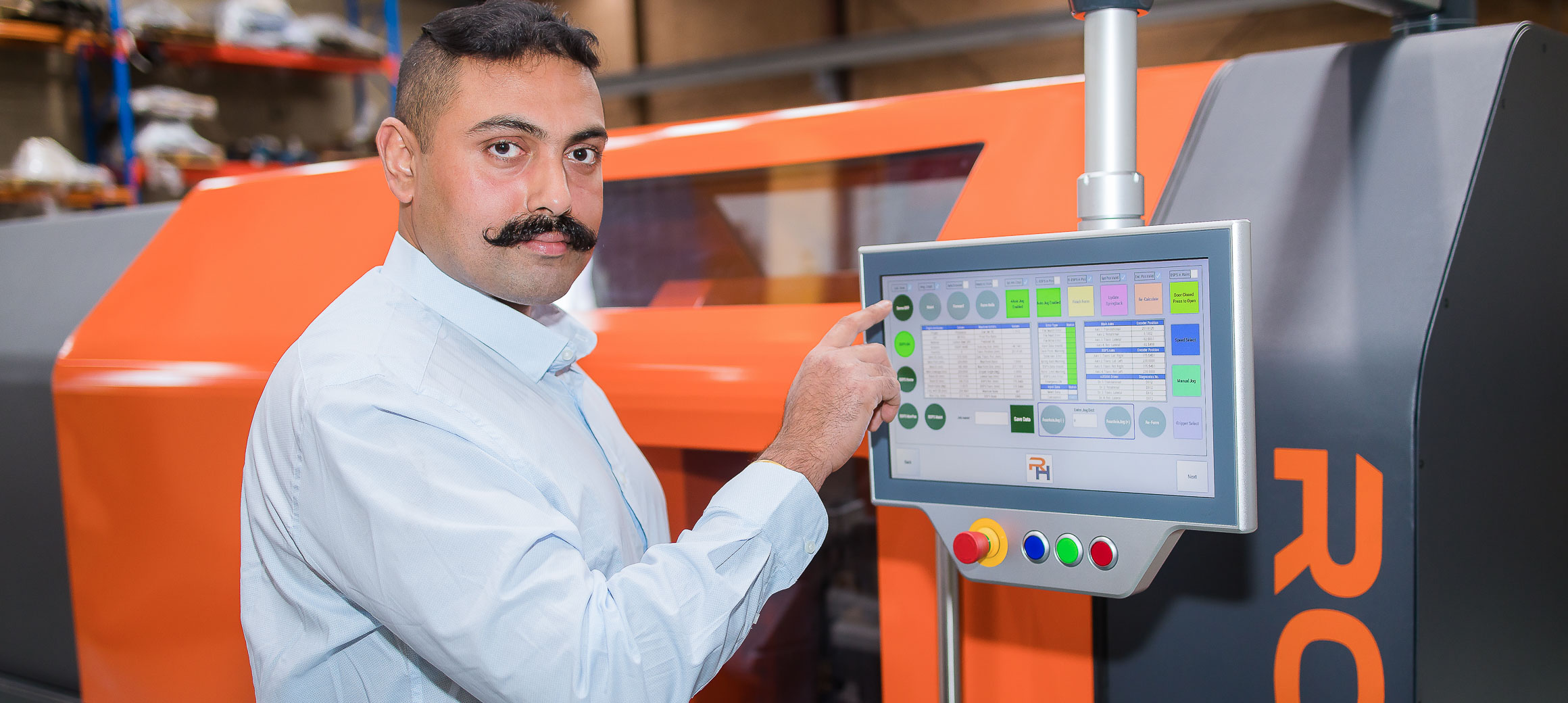
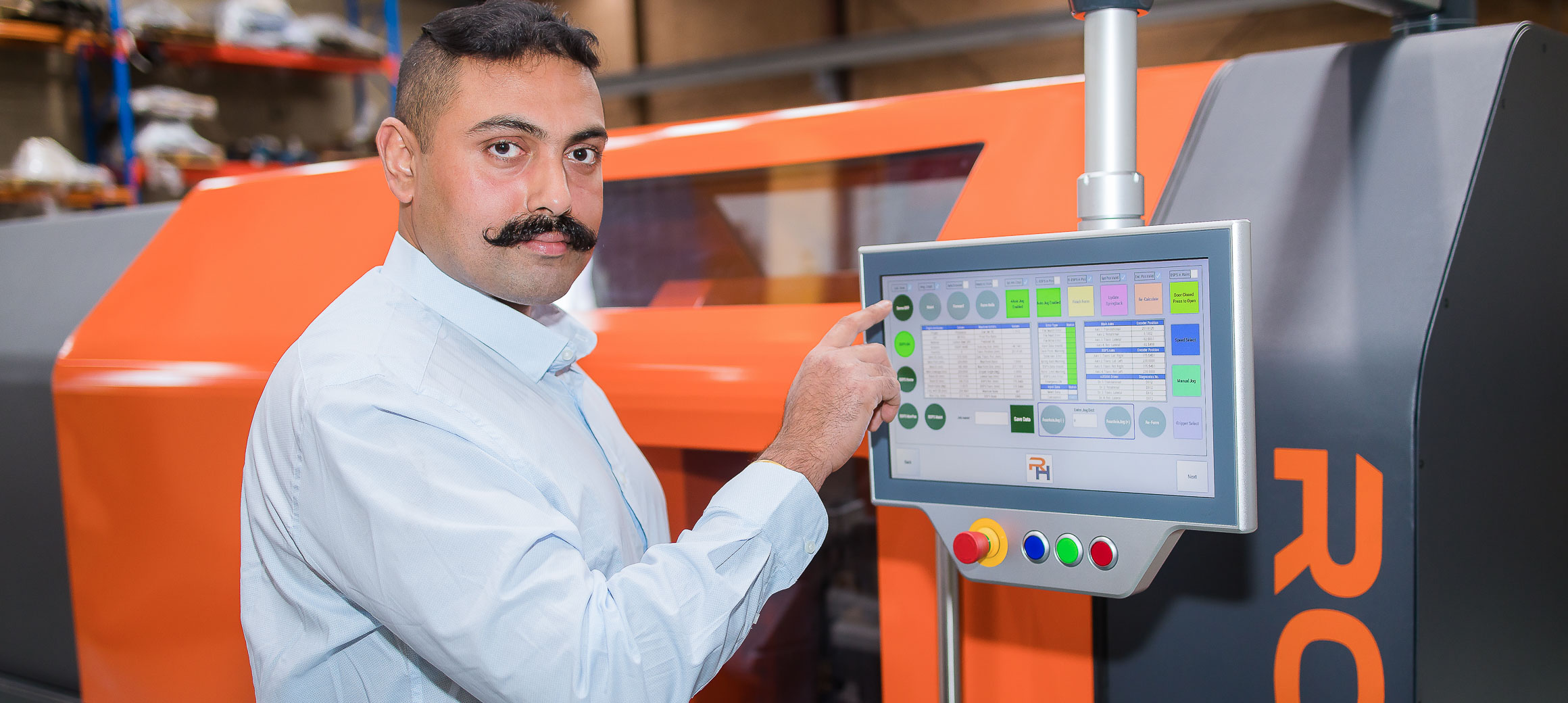
PC-based control automates traditional helical-flight formation process
Hydraulic presses have been used in the traditional helical flight forming process for use in agriculture, food processing or mining. RoboHelix from Sydney, Australia, replaced the laborious process with a newly developed robotic machine. Comprehensive integration of Beckhoff technologies has enabled RoboHelix to achieve higher performance and precision, yet it simplified the control technology and made it flexible across the range.
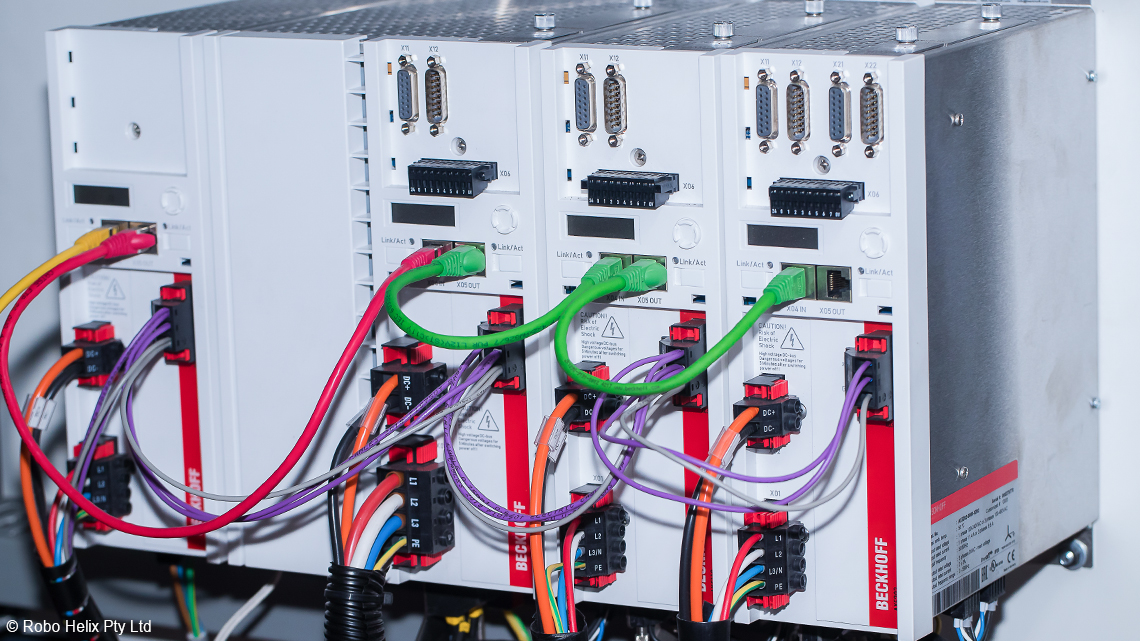
Since its inception in 2015 as a startup, RoboHelix has changed the way industries dealt with flight-formation by developing the first robotic machine. Hydraulic presses, the traditional flight-forming machines, use dies that correspond to the physical parameters of a flight. The conventional process therefore needs many of these expensive and bulky dies, and depending on the size of the die, tooling and setup time often take half an hour to an hour. RoboHelix's founder and CEO, Hayel Smair, comments: "This manufacturing process has been around since the industrial revolution." The company targeted on the reduction of batch processing time from hours to minutes. With a rich background in robotics, Smair explains: "I realized there are precise movements that a helical flight takes when it is transformed into shape from a flat disc, I then utilized a robotic system to mimic these movements."
Beckhoff drive technology was selected to realize the servoaxes in the new production system after an evaluation phase. Dr Budhaditya Majumdar, engineer responsible for electrical design, integration and programming of the RoboHelix machines, says: "There are very few players in the market that can provide us with servomotors, both precise and powerful, as well as economical. Our relationship with Beckhoff took-off from there, and now they cover not only motion controls and safety, but HMI as well!"
PC-based control for easy adaptation between machine variants
The RoboHelix series has multiple variants, and easy porting of the PLC program is crucial for batch production. Dr Budhaditya Majumdar explains: "We did not want to change the program each time there is an electromechanical design change of gear-ratios or screw leads. The TwinCAT and PC-based control structure allowed us to change the drives, motors and electromechanical parameters without touching the PLC code."
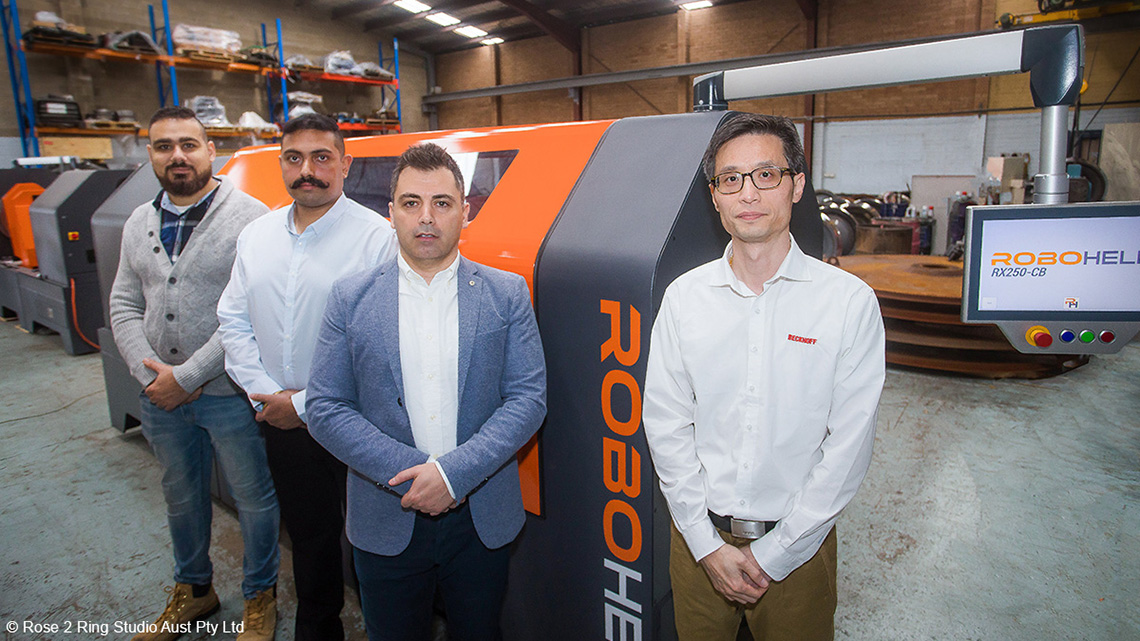
RoboHelix machines use the CX5140, an Embedded PC with a quad-core processor. The program runs on tables calculated based on material properties of the helix. "Our previous hardware was stretched out, and the table computation was taking 30 s. In the CX5140, only one core is dedicated to the PLC program, and it does the job at a fraction of a second. Another core is dedicated for the motion controls, and the rest are shared for between the operating system, TwinCAT runtime and the TwinCAT HMI Server", explains Dr Majumdar.
Dynamic drive technology for fast production
The second-generation RX250 from RoboHelix' line of machines has a linear force requirement of 25,000 kg. Hayel Smair explains: "We wanted a precise servo-based design that was powerful, fast, and efficient. Traditional hydraulics-based design is messy and fails to provide precision control." With eight NC axes integrated into the sophisticated machine space, One Cable Technology (OCT) enabled Beckhoff drives and motors require less wiring and improve electrical assembly timeline. Dr Majumdar adds: "In our previous machine, we used a pulse driven motion control. Each of the motor drives had four differential pairs for motion and four differential pairs of encoder feedback to the PLC, and it took an eternity to set the wiring for eight motors. With OCT, however, it was just a click away, with the AX5000 drives, and the AM8000 servo motors". AS2023 stepper motors along with EL7041 stepper motor terminals are used for low torque motors.
RoboHelix machines require high precision synchronous motion control. User-generated data is downloaded into the device from a cloud-based software, HelixNinja. The information is then further processed to generate coordinates in the 3D plane that emulates the process of creating a flight from a blank. The motors synchronously follow these coordinates to produce the flight. "On our previous machine, the synchronous motion was achieved at the cost of performance and flexibility", Dr Budhaditya Majumdar says. "With the electronic cam plate function in TwinCAT NC Camming (TF5050), relative synchronous motion is possible anywhere anytime. Sizes and tolerances are no longer a concern, once the motors and drives are calibrated."
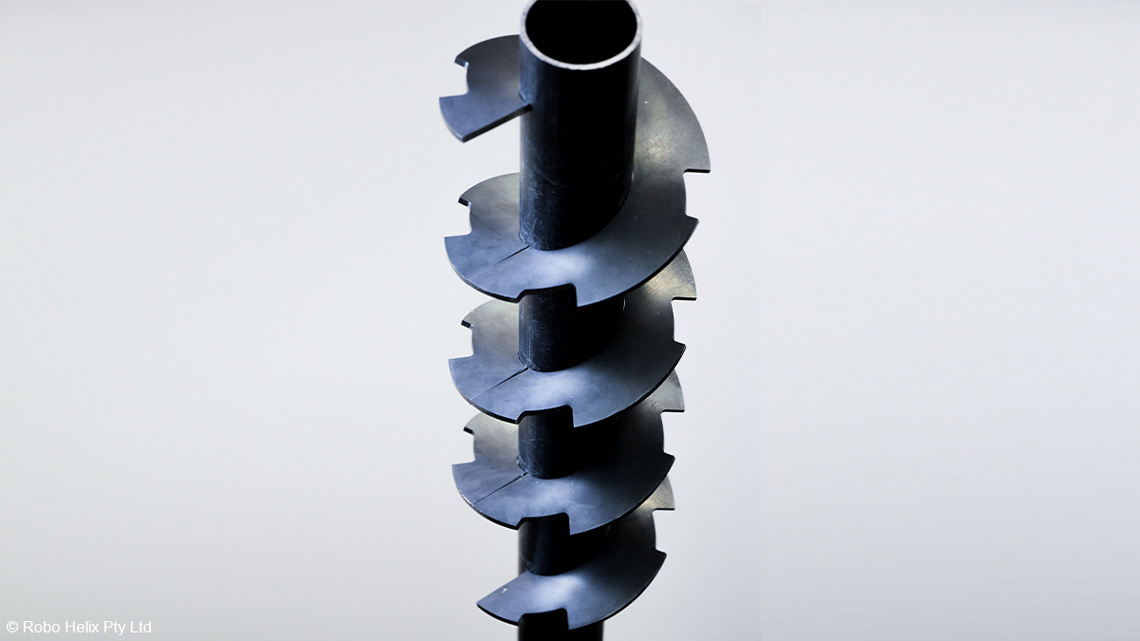
Convenient machine operation and integrated machine safety
Users may need to operate the machine from more than one side. "The machine is designed to allow the operator to insert the blank and extract the flight from either the left-hand side or right-hand side of the machine. It is more accessible for the operator to switch sides of the machine depending on the required flight rotational direction, be it a clockwise or anticlockwise rotation", says Hayel Smair. "The benefit for having the CP3916 multi-touch Control Panel on a swivel-arm is to allow the operator to maneuver the touchscreen to keep it within proximity." According to Dr Budhaditya Majumdar, the same applies to the push-button extension with E-Stop, which is provided directly at the bottom of the screen and is therefore safely accessible to the operator at all times.
The operator interface for the RoboHelix machines is based on TwinCAT HMI. The CX5140 Embedded PC also additionally hosts the TwinCAT HMI Server and the CP3916 is connected to it, with the browser running in kiosk-mode. Dr Majumdar explains: "Previously we had an HMI which itself was a computing device that required programming. The use of a purely passive panel, on the other hand, reduces the effort. In addition, the operator interface may also be viewed over the browser of a cell-phone or a network-connected PC if desired."
Safety in machine automation is of utmost concern. Use of TwinSAFE integrated safety solution has reduced the safety-related wiring needs. Dr Majumdar agrees: "Any safety trigger from sensors or E-Stop will disable the motor drives, without the requirement of any hard-wired safety wiring! At some operating stage, the operator might have to open the door, while the motor is still activated and under torque. Here, the AX5805 TwinSAFE option card helps us meet safety requirements using the inbuilt SOS (Safe Operating Stop) feature. Implementing this in the previous machines was difficult and came with a lot of overhead costs of speed-monitors. Above all, whatever is being programmed, the PLC, Drive, HMI or Safety; everything is through the same TwinCAT platform."
At a glance
Solutions for food processing, materials handling, and allied industries
- robotic machine for creating helical flights
Customer benefit
- increased efficiency with fast turnaround time for production of flights
- reduced operating costs
- high level of operator safety
- no requirement of specific dies
Applied PC Control
- PC-based control and drive technology as a flexible and scalable system
- TwinCAT as a universal platform for all functionalities
- TwinSAFE for functional safety without complexity
- TwinCAT HMI for flexible and hardware independent visualization technology
- AX5000 Drives and AM8000 motors for precision motion control
- CX5140 and CP3916 as a flexible, high-performance, multi-touch-capable control platform