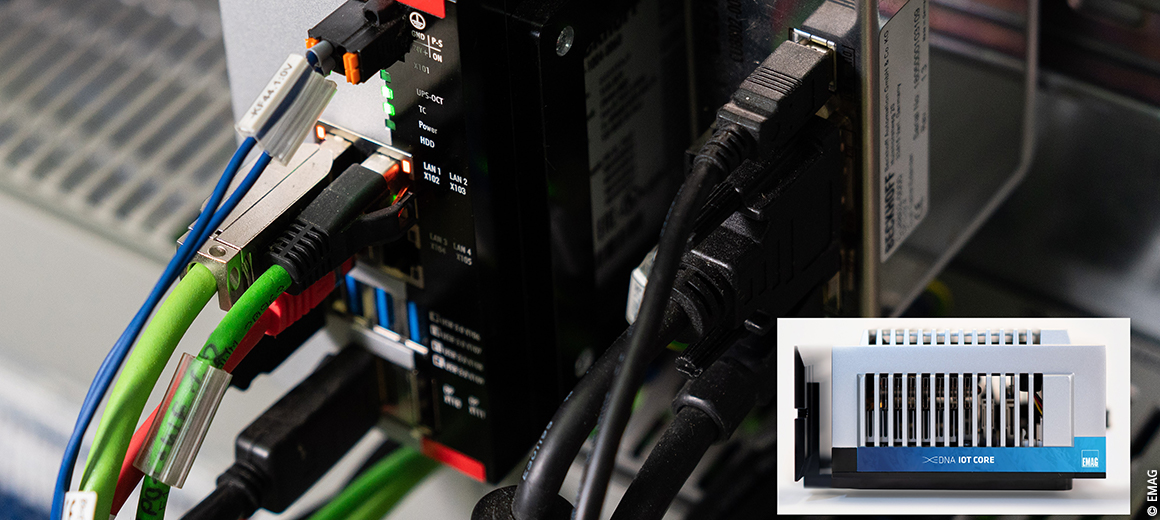
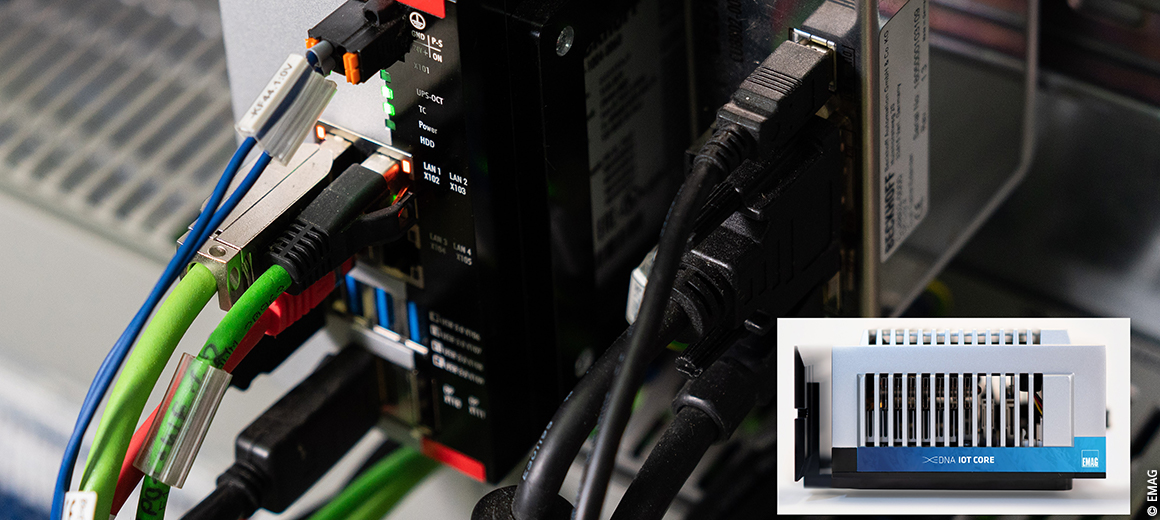
Ultra-compact Industrial PC and multi-touch Control Panel with newly developed HMI solution for machine tools
EMAG GmbH & Co. KG, based in Salach, Germany, is a specialist for flexible production solutions and offers a broad spectrum of machine tools ranging from standardized machines to customized manufacturing systems. Together with the new EDNA operating and networking concept, these now enable significantly more transparent and efficient processes. EDNA, the EMAG DNA, is a modular software ecosystem consisting of interconnected software and machine components. In an interview with PC Control magazine, Rainer Seitz, Head of Software Development & IoT, explains the specific advantages of the system as a whole, along with the customized CP3921 Control Panel and the C6030 ultra-compact Industrial PC from Beckhoff.
How long have you been using the C6030 ultra-compact Industrial PC and what was the key factor behind this decision?
Rainer Seitz: We have been using this space-saving Industrial PC from Beckhoff since 2018 because it is a highly compact IPC which even fits into the control cabinet if it is retrofitted at a later date. The ability to connect any common fieldbus system via the real-time kernel and EtherCAT provides additional benefits. The fact that we can design the factory-fitted basic image to match our requirements is another important aspect as this ensures seamless integration into our CI/CD pipeline. In practice, the C6030 has proven to be extremely robust and reliable.
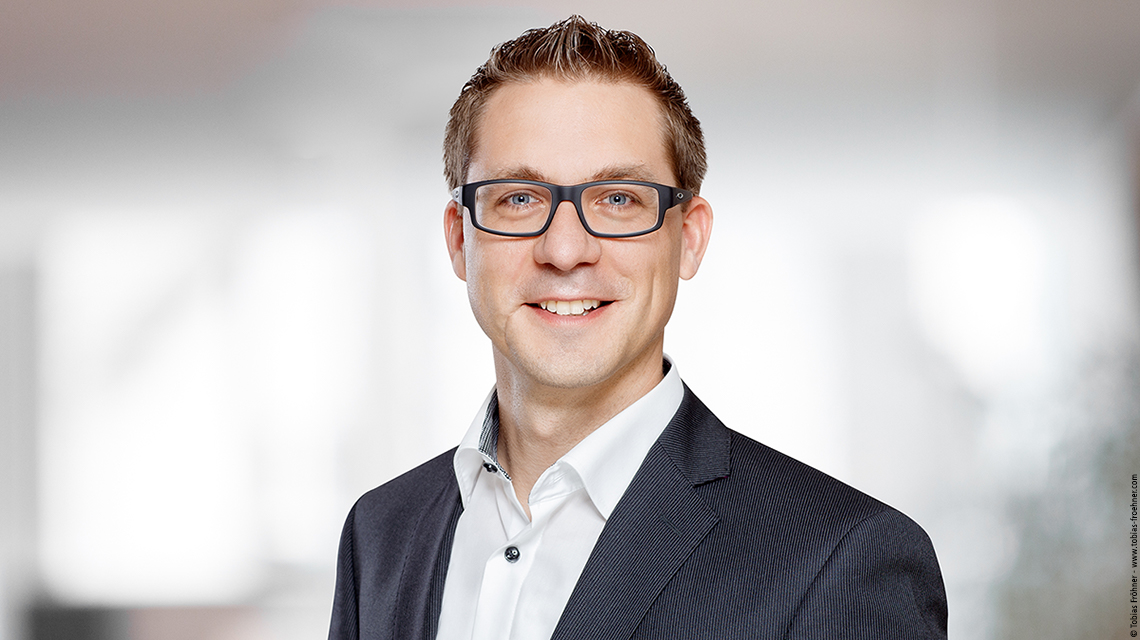
In this context, how important is the ability to create customer-specific designs and what experience is your experience with Beckhoff in this regard?
Rainer Seitz: This option is essential especially given that the collaboration has proven to be uncomplicated and cooperative. In addition to technical support, transporting EMAG’s EDNA brand is also important to us. We always receive support for the design, advice and planning directly from Beckhoff such as regarding the choice of form factor and corporate design adaptations.
What are the reasons for consistently using the customized CP3921 as your standard operator interface?
Rainer Seitz: The EDNA panel is the central user interface for the machine tool. We have tailored both the equipment and the design to meet the standardization requirements for our current diverse range of panels. This integrated approach to hardware and software has enabled us to develop a standardized panel design that is effective in every context and for a wide range of EMAG technologies and machine series. The most important global and safety functions are integrated directly into the frame. We also implement specific requirements for modern software through the flexibility of multi-touch technology. As a result, we can simplify the operation of our machines, increase uniformity and also address individual requirements using a modular approach.
When and which machines will this be implemented on and can it also be retrofitted on older systems?
Rainer Seitz: Our new MIND L-1000 induction hardening machine is already equipped with the new panel and HMI. New hob cutters and turning machines are currently in development. For 2021, we aim to deliver all of our standard lathes IoT-ready and factory-fitted with an IPC as of about the middle of the year. We are also in the process of equipping other machine types with the new panel and HMI. Retrofitting is also possible under specific conditions. However, we have to examine each individual case to address this.
How important was the wide range of multi-touch panels and the corresponding Beckhoff expertise when selecting the HMI?
Rainer Seitz: We place a lot of importance on the ability to examine both the development of the hardware and the HMI concepts interactively and cross-functionally given that both sides influence each other. The agile approach, which is already common practice in software development, has also been very successful in collaboration with Beckhoff.
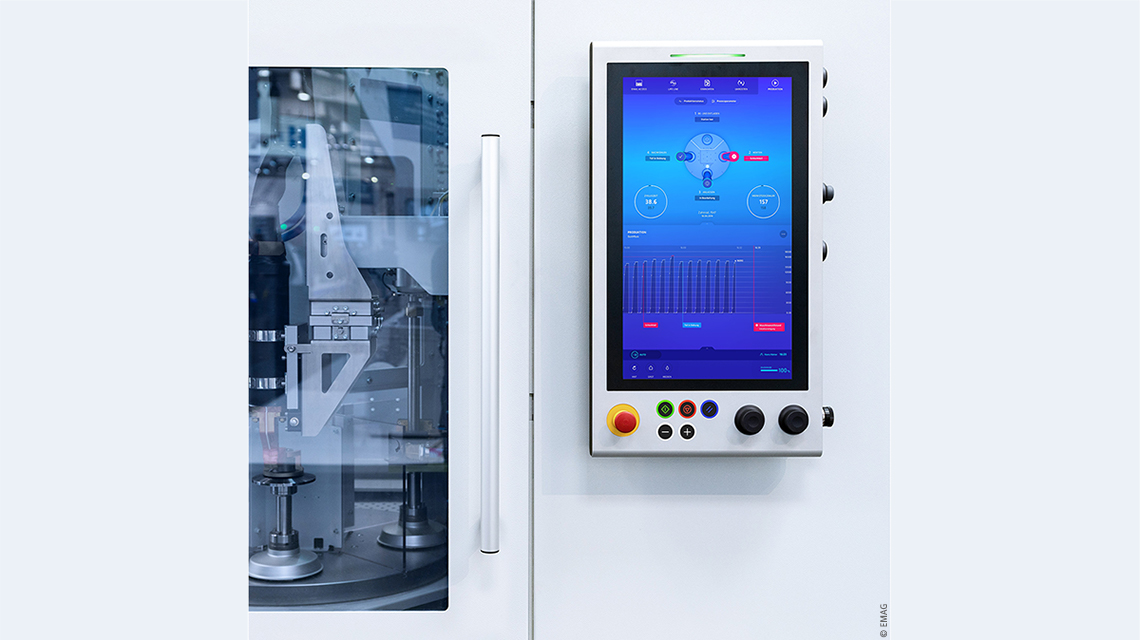
What special requirements were focal elements of the CP3921's customized design and what role does HMI design play on the whole?
Rainer Seitz: The basic requirement was: simple and reduced to the essentials. The HMI hardware needs to provide a future-proof foundation for ongoing software innovations. User Interface Design (UI) and User Experience Design (UX) were our top priority from the outset. This means that the development processes focused on the needs of our target group. Alongside the product design, this is especially important with regard to software ergonomics. Our flexible concept and proprietary software extensions enable us to guide user groups through our applications spanning different technologies by utilizing recurring patterns.
Why did you decide on the 21.5-inch widescreen format and, in particular, the portrait variant?
Rainer Seitz: The high resolution along with sufficient size to enable comfortable navigation using the touchscreen even with gloves were the deciding factors. In numerous concept variations and experiments, we decided on what might be the more exotic portrait format. In the upper half we focus on presenting and summarizing information, whereas the lower half is primarily designed for interaction and configuring various parameters. In addition to these practical reasons for the user, the portrait format also perfectly communicates the core of our EMAG brand: "Think Vertical".
What are the requirements regarding the robustness of the Control Panel?
Rainer Seitz: We have maximum durability requirements because the machines sometimes operate under extremely harsh conditions. Failure would be extremely costly.
What are the practical advantages of the EDNA concept for the machine tool industry?
Rainer Seitz: EDNA will consistently reduce the amount of time that has to be spent on commissioning, setting up and operating the machines despite the fact that manufacturing processes are becoming more complex and the demands on flexibility are increasing. Numerous, minor data-driven software enhancements will also enable the machines to produce more parts in the same amount of time while also increasing quality.
How important is Industrie 4.0 and IoT in the context of the EDNA concept?
Rainer Seitz: They are focal aspects of all developments at EMAG and define the future for us. Our strategy is to become established in the market as a digital machine tool manufacturer by 2025. Specifically, our software products focus on the value of data, providing overarching analytics tools for our customers' production. Real-time data from the machines is combined and processed to provide useful information and recommendations for action. This is about more than just passing on machine data. Rather, our Life Line products serve as a portal for data-driven services that generate valuable status messages and recommendations drawn from process knowledge and algorithms. Developing suitable dashboards to clearly visualize the data for customers is an essential aspect of this strategy. Once again, the CP3921 offers great options for displaying these dashboards directly on the machine. This gives machine operators direct feedback regarding the status of the production and also the condition of the machine itself.
You also offer the EDNA concept as a white label solution. Which customer group are you targeting with this?
Rainer Seitz: The target group consists of all machine builders who want to benefit from an innovative and comprehensive ecosystem and enrich their machines with software-based value-added services.
EDNA has already been recognized as an innovative concept. What awards have you received?
Rainer Seitz: The overall hardware and software concept received the Red Dot Award 2020: best of the best and it was also nominated for the highest award, the Red Dot: Luminary. In addition, it received special mentions including the “German Design Award Special Mention” and the “UX Design Award Special Mention”. As such, the combination of our software and Beckhoff hardware represents real added value for every user.