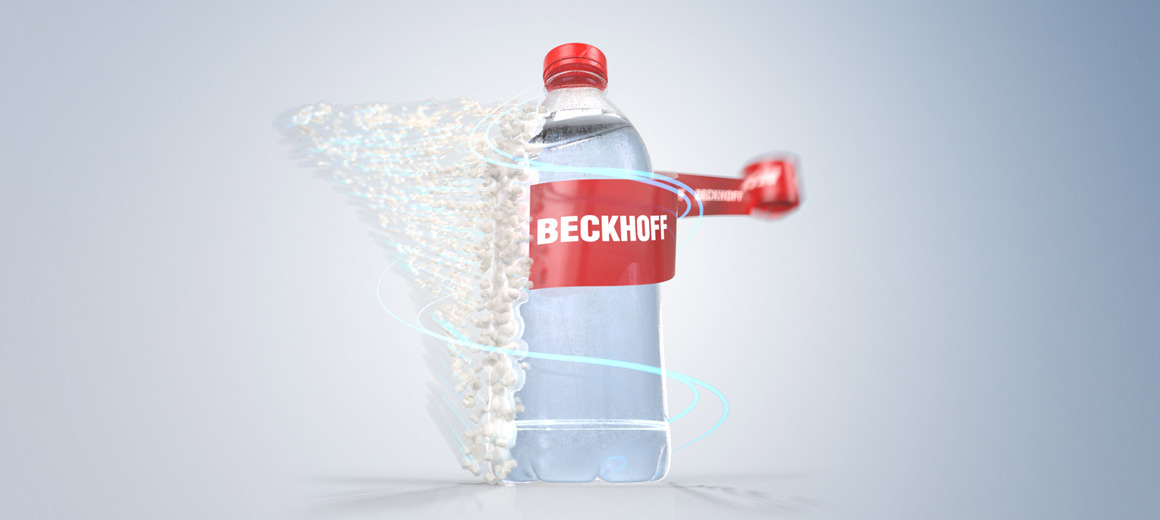
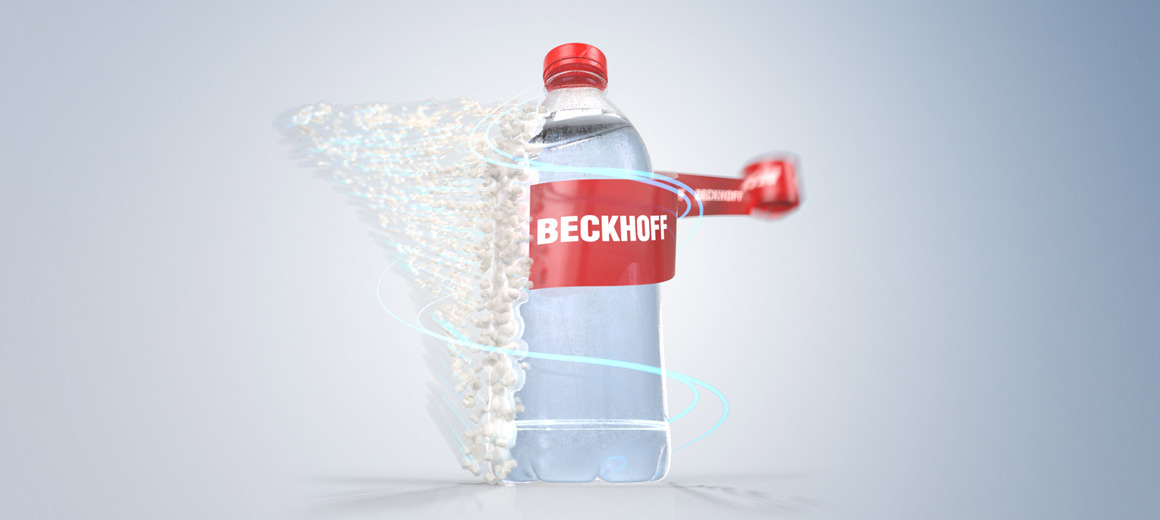
Interview with two industry experts on automation synergies in the plastics and packaging industry
PC- and EtherCAT-based control and drive technology from Beckhoff is a universal solution that transcends industry and application boundaries. This standardized and scalable automation platform offers numerous advantages, from integrated, open EtherCAT communication through to simplified handling in the context of development, service, and warehousing. In this interview, industry experts Christian Gummich and Frank Würthner delve into how machine builders and end users in the plastics and packaging industry can capitalize on these advantages, particularly when working in close collaboration.
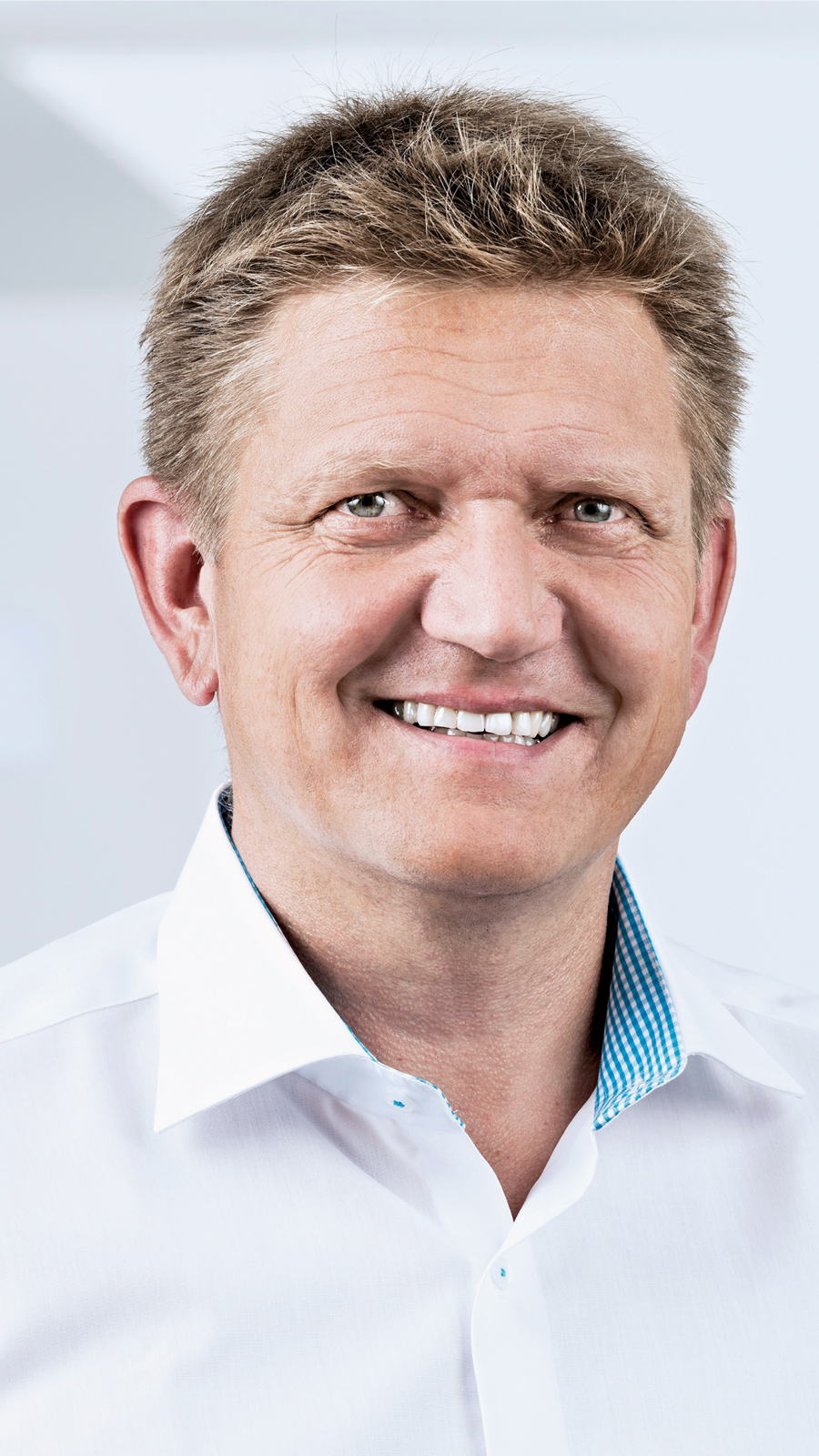
PC-based control is a universal technology that has proven its worth time and again on account of its impressive performance – especially in the challenging packaging sector. What are the main advantages that a Beckhoff solution offers for a typical packaging line?
Frank Würthner: The key here is integration, meaning we can technologically map the entire machine with our TwinCAT software. Our PC-based control technology is also extremely fast, which is an absolute must in this demanding industry. The high-performance EtherCAT communication system provides the perfect fieldbus backbone for this. With its mechatronic products and innovations, such as the XTS and XPlanar transport systems, Beckhoff continues to have a significant influence on machine building concepts.
Plastics machines benefit from PC-based control in a similar way. What are the key aspects of this mechanical engineering sector?
Christian Gummich: Its outstanding performance, coupled with the open, PC-based automation technology concept, helps our customers to develop their own innovations. The option of a scalable platform also plays a key role here, allowing the control system to be chosen in line with system requirements and customer needs.
In addition to technical insight, how important is it to offer comprehensive industry expertise? What makes Beckhoff stand out here?
Frank Würthner: Comprehensive industry expertise is hugely important for an automation specialist. After all, this is the only way to fully comprehend what machine builders need for their projects. This fundamental understanding of specific customer needs is not only essential for providing machine builders with optimal support, but it also paves the way for the most technically appropriate solutions.
Christian Gummich: I couldn’t agree more. Industry expertise is incredibly important. After all, if you want to engage in meaningful discussions and fully comprehend every aspect of your customer’s requirements, in-depth application knowledge is simply indispensable. This, in turn, is essential to properly align any developments and have a positive impact going forward. In line with customer requirements, we have developed a Plastic Framework for the plastics machinery sector that is based on the TwinCAT 3 Engineering environment. This framework offers additional functions tailored to plastics applications in both the HMI and PLC areas, and enables customers to seamlessly integrate our cross-technology products, such as electric and hydraulic axes. It also includes industry-specific HMI controls and templates with sample code to cut down on development times.
The universal nature of PC-based control simplifies the implementation of cross-industry automation solutions. How does this end-to-end control impact packaging and plastics machinery, which is commonly closely interconnected, particularly in terms of comprehensive production processes?
Christian Gummich: There are many factors that can be mentioned here, ranging from the overall appearance across applications or departments through to even larger, but not visible factors such as the consistent use of EtherCAT and TwinCAT in both engineering and service. As far as customers are concerned, there are so many benefits to this approach.
Frank Würthner: In the packaging sector in particular, there are many points of contact with other industries, such as process and printing technology, and especially with the plastics industry. One of the major strengths of our solutions is Beckhoff’s ability to cater to various vertical industries, drawing on its specialized expertise while also consistently tapping into the same reliable technical foundations. As we have already mentioned, notable aspects include the high-performance EtherCAT fieldbus and our TwinCAT tool as a modular and fully comprehensive "Swiss army knife" of automation.
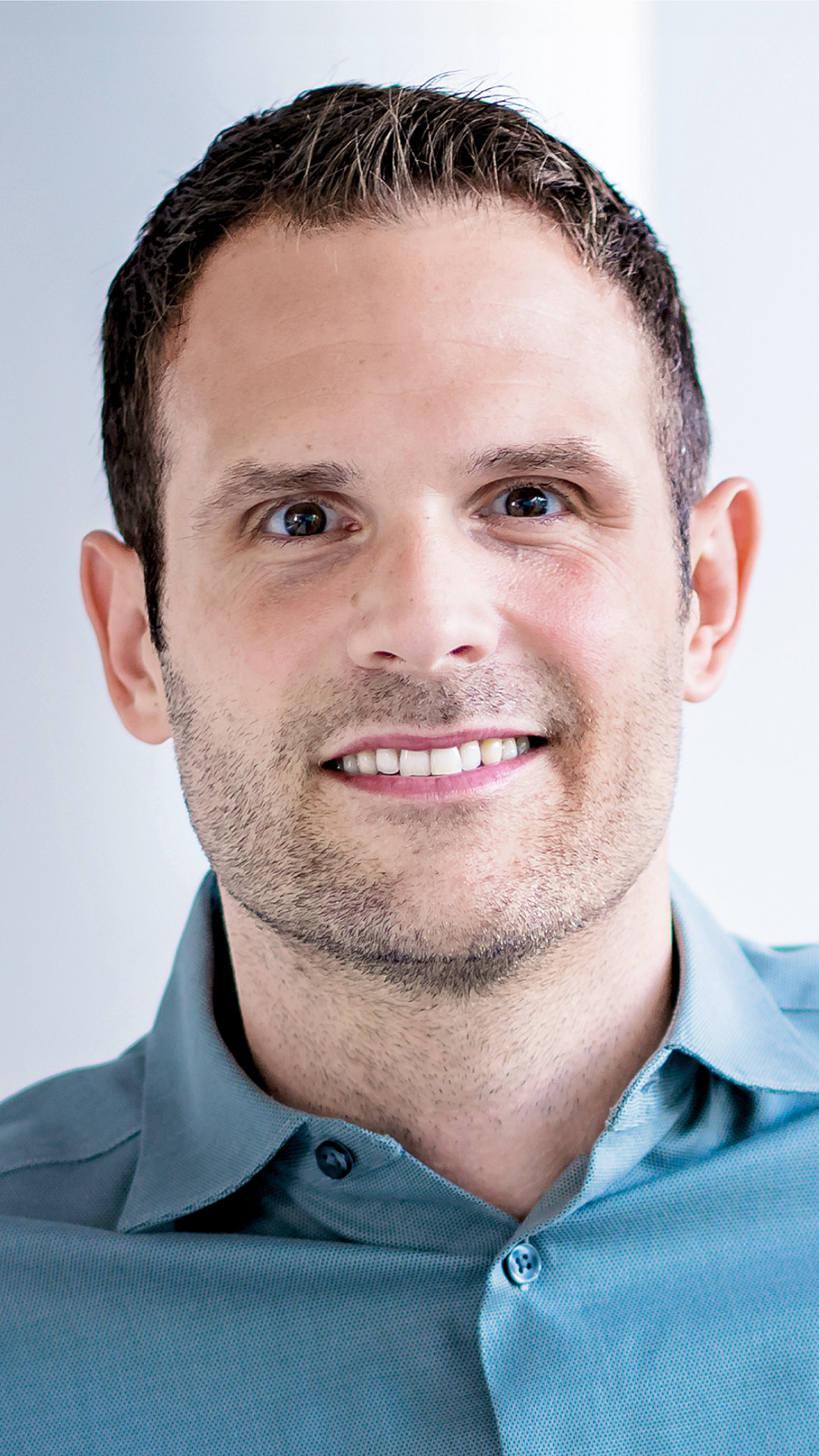
What are the general advantages for respective machine builders and end customers?
Frank Würthner: Here, too, the main advantage is TwinCAT, as the software team only has to be trained on one system. This keeps necessary investments to a minimum and means employees can provide support in other areas as required without a great deal of training.
Christian Gummich: And on top of the training benefits, there are further advantages in terms of supply chains and warehousing, as components can be used across applications and departments. This creates even more advantages in terms of purchasing and maintenance processes. And then, of course, there are the technical benefits: As an end-to-end solution, EtherCAT eliminates the need to support multiple different communication protocols, which may only cooperate to a limited extent and require significant effort from personnel in terms of training, commissioning, and servicing. EtherCAT is also open for the integration of subsystems.
Frank Würthner: That’s right, we have found that end customers are now becoming more and more focused on integration, particularly when it comes to maintenance, where it is especially important. With this in mind, end customers are increasingly mindful of selecting the same automation provider across all industries.
How do end customers stand to benefit from a technical point of view – for example, through the optimally scalable Beckhoff solution in software and hardware, the universal EtherCAT communication, and the continuously evolving portfolio including innovations such as XTS and XPlanar?
Christian Gummich: The comprehensive solution approach and the deep integration of various innovative products into a single development environment are crucial to success, particularly where end customers are concerned. The latest innovations, such as Beckhoff Vision, the MX-System as a solution for control cabinet-free automation, and the ATRO modular industrial robot system, enhance the portfolio considerably. This opens up completely new application possibilities, which – in combination with established products such as IPC, motion, and I/Os – also make life easier for the end customer. As a result, functions that were previously integrated externally can in many cases now also be mapped in TwinCAT.
Frank Würthner: The Beckhoff innovations we have talked about here are of notable interest to end users. Major brand manufacturers, for example, are increasingly recognizing that the XTS transport system in particular can significantly influence and optimize their product handling processes. As a result, they are demanding this level of machine functionality from machine builders, which accelerates the implementation of these innovations in machine design.
PC-based control for packaging
In the field of packaging machinery, the Beckhoff PC-based control system, TwinCAT, boasts numerous features that offer distinct advantages. Notable examples include:
- TwinCAT MC3: This new motion control generation is notably characterized by its modular architecture and consistent multi-core and multi-task support
- OMAC PackML: TwinCAT offers the OMAC PACKML PLC library, providing convenient access to the standardized Packaging Machine Language.
- Collision avoidance: TwinCAT 3 Collision Avoidance (TF5410) enables active collision avoidance when operating multiple axes in linear and/or translatory dependency. This function can also be used to accumulate axes in a controlled manner during linear movements – for example, with the XTS product transport system.
- PLCopen function blocks: TwinCAT offers a wide range of PLCopen-compliant motion control modules, allowing for quick and easy handling of motion tasks.
TwinCAT Plastic Framework
The TwinCAT Plastic Framework offers all the software features required for the automation of plastics machines and integrates essential industry-specific and customized control functions and HMI controls. It comprises four components:
- TwinCAT 3 Plastic Processing Framework (TF8540): The software library brings together Beckhoff’s many years of expertise in plastics, seamlessly integrating essential industry-specific control functions into the familiar TwinCAT environment. It enables comprehensive software-based temperature control in plastics processing, including a software temperature controller that is specifically designed to handle slowly responding control loops in plastics applications.
- TwinCAT 3 Plastic HMI Framework (TF8550): This software library is a TwinCAT HMI package specially developed for the plastics industry, enabling visualizations and full-featured HMI applications with minimal development effort. Graphic objects can be configured for visualization in extrusion systems, in blow molding technology, and for injection molding machines.
- TwinCAT 3 Plastic Technology Functions (TF8560): This technology package includes field-proven, pre-developed standard blocks for typical motion applications in plastics machines. The available motion functions are specially prepared to offer an integrated safety solution with TwinSAFE, while the intuitive axis commissioning and virtual commissioning are supported through integrated simulations.
- TwinCAT 3 PLC Plastic Application: This application consists of both an HMI and PLC project and includes the conversion of generic technology functions for specific axes as well as sample code for extrusion, blow molding, and injection molding machines.