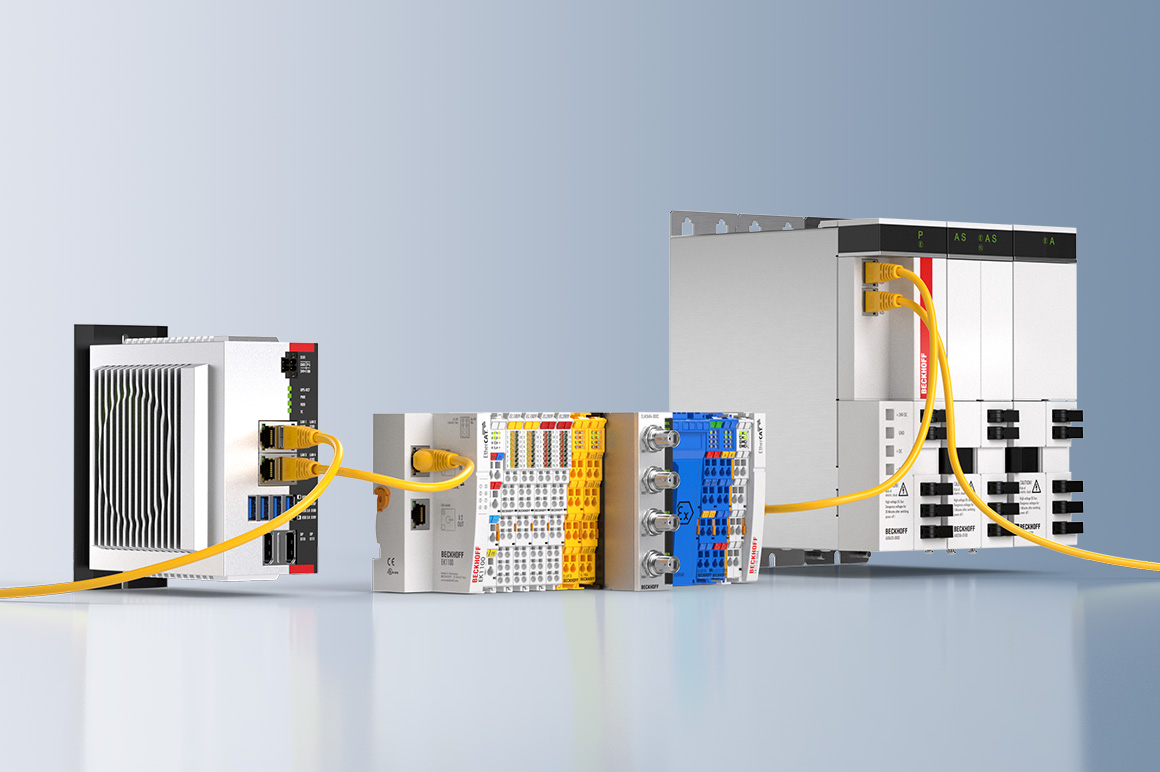
Selecting the communication technology is important: it determines whether the control performance will reach the field and which devices can be used. EtherCAT, the Industrial Ethernet technology invented by Beckhoff, makes machines and systems faster, simpler and more cost-effective. EtherCAT is regarded as the "Ethernet fieldbus" because it combines the advantages of Ethernet with the simplicity of classic fieldbus systems and avoids the complexity of IT technologies. The EtherCAT Technology Group (ETG), founded in 2003, makes it accessible to everyone. With over 7,000 member companies from 72 countries (as of March 2023), the ETG is the world's largest fieldbus user organization.
EtherCAT is an international IEC standard that not only stands for openness, but also for stability: until today, the specifications have never been changed, but only extended compatibility. This means that current devices can be used in existing systems without any problems and without having to consider different versions. The extensions include Safety over EtherCAT for machine and personnel safety in the same network, and EtherCAT P for communication and supply voltage (2 x 24 V) on the same 4-wire cable. And also EtherCAT G/G10, which introduces higher transfer rates, while the existing EtherCAT equipment variety is integrated via the so called branch concept: even here there is no technology break.
Products
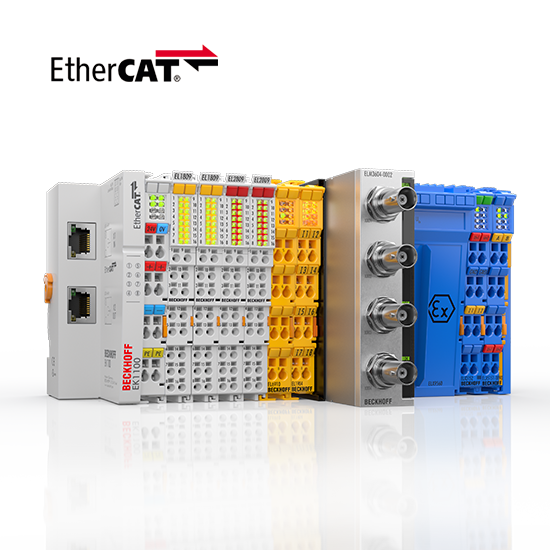
EtherCAT Terminals
The EtherCAT Terminal system provides a comprehensive range of products for all signals in the world of automation.
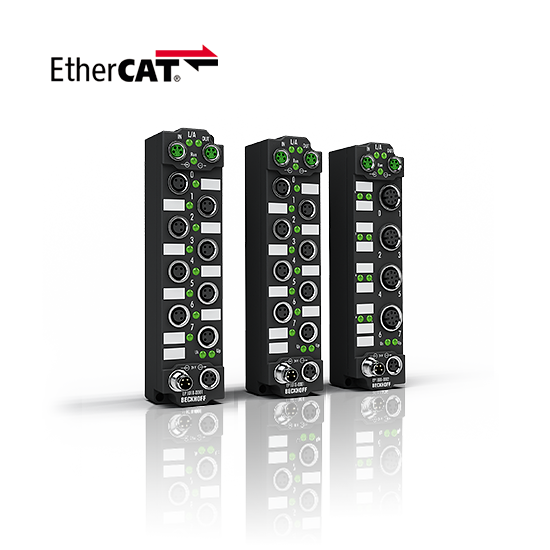
EtherCAT Box
EtherCAT high-performance directly in the field: Beckhoff offers an I/O system in IP67 with the EtherCAT Box modules.
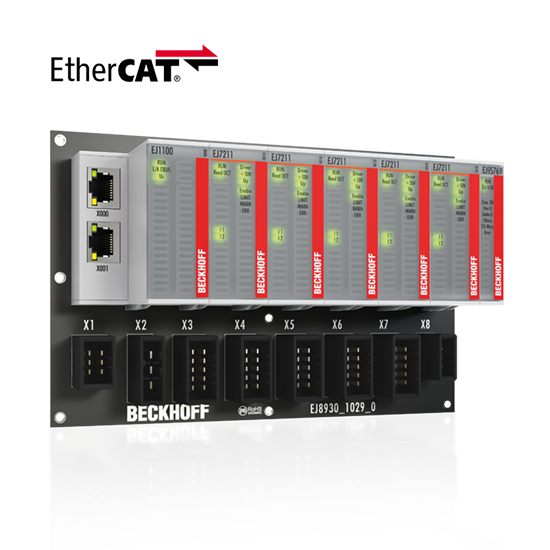
EtherCAT plug-in modules
The EtherCAT plug-in modules reduce the wiring work and system installation time with standard machines.
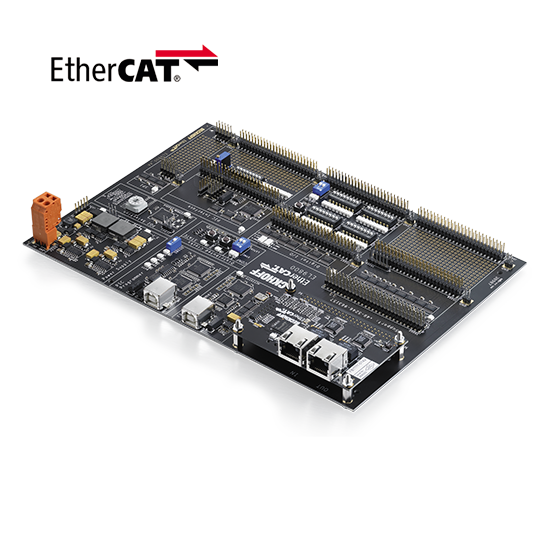
EtherCAT development products
With the EtherCAT development products a simple and cost-effective integration of the technology into own products is possible.
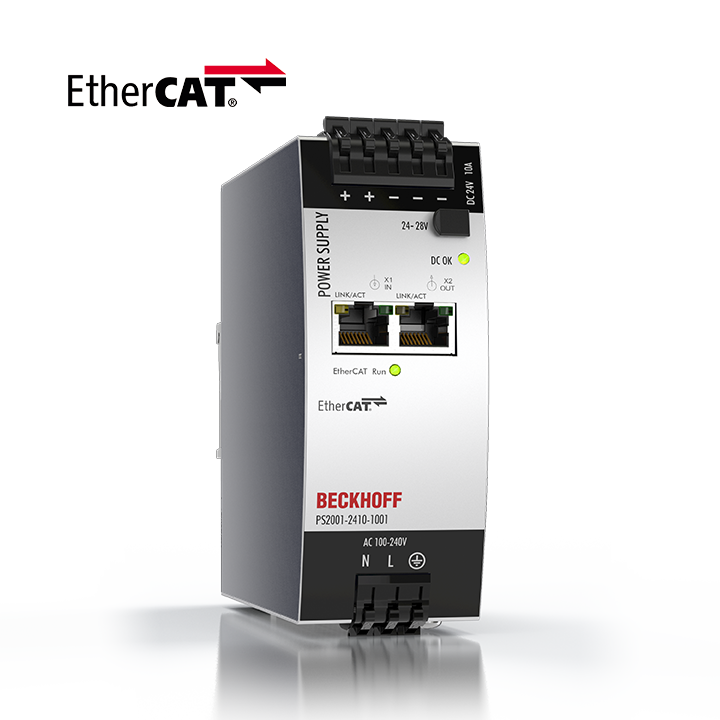
PS2000 with EtherCAT
Single and 3-phase DIN rail power supply units in compact design, can be used for the most common applications.
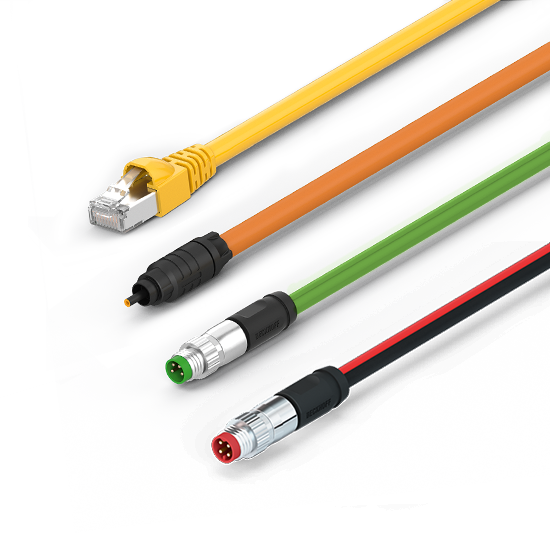
EtherCAT and fieldbus cables
The EtherCAT and fieldbus cables ensure reliable data transmission and are optimized for industrial applications and harsh environmental conditions.
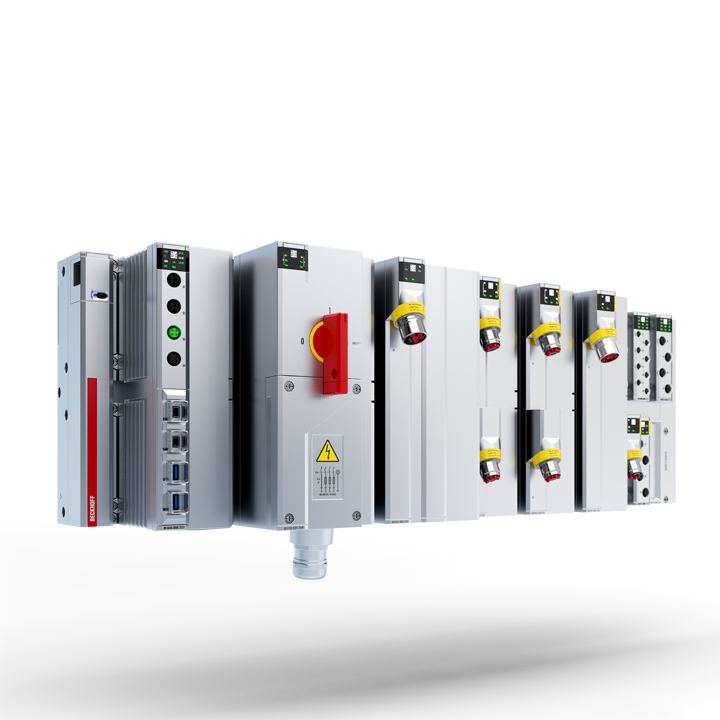
MX-System
Our MX-System combines all technological innovations in automation technology in an IP67-capable modular system.
Engineer´s choice: the 6 key benefits of EtherCAT
EtherCAT is by and large the fastest Industrial Ethernet technology, but it also synchronizes with nanosecond accuracy. This is a huge benefit for all applications in which the target system is controlled or measured via the bus system. The rapid reaction times work to reduce the wait times during the transitions between process steps, which significantly improves application efficiency. Lastly, the EtherCAT system architecture typically reduces the load on the CPU by 25 - 30 % in comparison to other bus systems (given the same cycle time). When optimally applied, the performance of EtherCAT leads to improved accuracy, greater throughput and lowered costs.
In EtherCAT applications, the machine structure determines the network topology, not the other way around. In conventional Industrial Ethernet systems, there are limitations on how many switches and hubs can be cascaded, which thus limits the overall network topology. Since EtherCAT does not need hubs or switches, there are no such limitations. In short, EtherCAT is virtually limitless when it comes to network topology. Line, tree, star topologies and any combinations thereof are possible with a nearly unlimited number of nodes. Thanks to the Hot Connect functionality, nodes and network segments can be disconnected during operation and then reconnected – even somewhere else. Line topology is extended to a ring topology for the sake of cable redundancy. All the master device needs for this redundancy is a second Ethernet port, and the slave devices already support the cable redundancy. This makes switching out devices during machine operation possible.
Configuration, diagnostics and maintenance are all factors that contribute to system costs. The Ethernet fieldbus makes all of these tasks significantly easier: EtherCAT can be set to automatically assign addresses, which eliminates the need for manual configuration. A low bus load and peer-to-peer physics improve electromagnetic noise immunity. The network reliably detects potential disturbances down to their exact location, which drastically reduces the time needed for troubleshooting. During startup, the network compares the planned and actual layouts to detect any discrepancies. EtherCAT performance also helps during system configuration by eliminating the need for network tuning. Through the large bandwidth, there is capacity to transmit additional TCP/IP together with the control data. However, since EtherCAT itself is not based on TCP/IP, there is no need to administer MAC addresses or IP addresses or to have IT experts configure switches and routers.
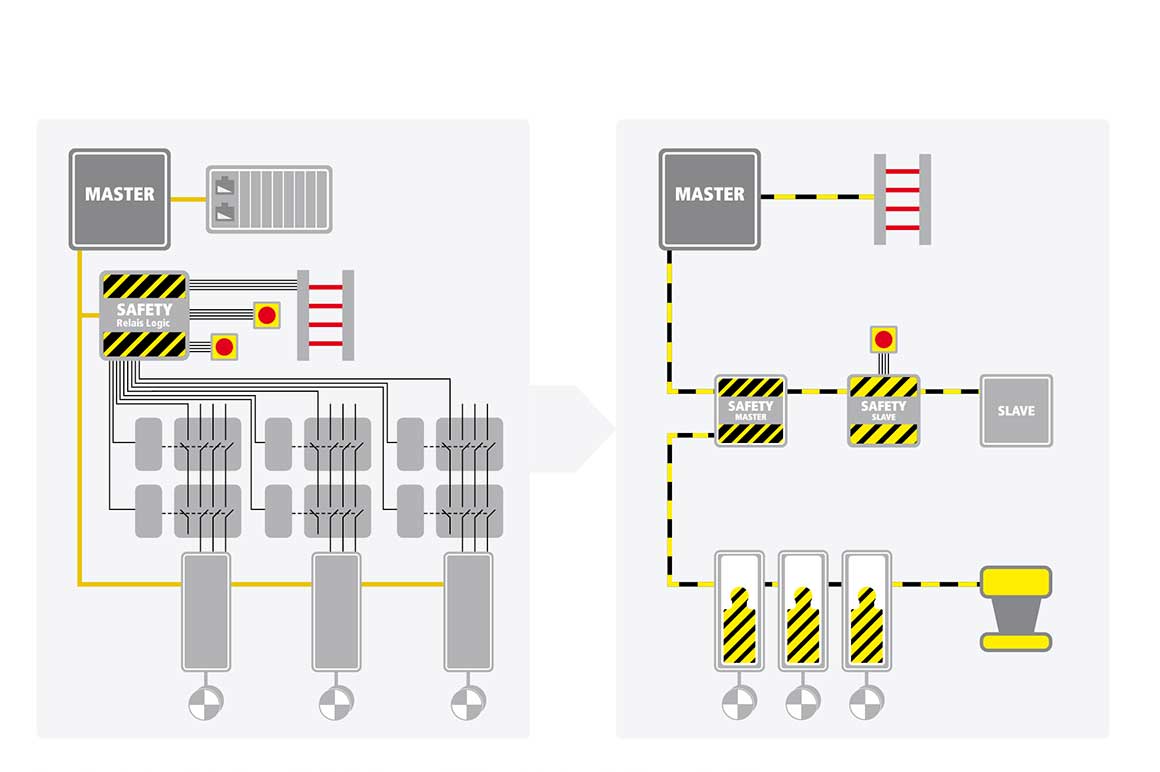
Functional safety as an integrated part of the network architecture? Not a problem with Fail Safe over EtherCAT (FSoE). FSoE is proven in use through TÜV-certified devices that have been on the market since 2005. The protocol fulfills the requirements for SIL3 systems and is suitable for both centralized and decentralized control systems. Through the Black Channel approach and the particularly lean safety container, FSoE can be used in other bus systems. This integrated approach and the lean protocol help keep system costs down. Additionally, a non-safety critical controller can also receive and process safety data.
EtherCAT delivers the features of Industrial Ethernet at a price similar or even below that of a classic fieldbus system. The only hardware required by the master device is an Ethernet port – no expensive interface cards or co-processors are necessary. EtherCAT Slave Controllers are available from various manufacturers in different formats: as an ASIC, based on FPGA or as an option for standard microprocessor series. Since these inexpensive controllers shoulder all the time-critical tasks, EtherCAT itself does not place any performance requirements on the CPU of slave devices, which keeps device costs down. Since EtherCAT does not require switches or other active infrastructure components, the costs for these components and their installation, configuration and maintenance are also eliminated.
EtherCAT is the Industrial Ethernet technology with by far the largest variety of vendors and devices on the market. And since Beckhoff invented EtherCAT, vendors try their EtherCAT products with TwinCAT, the gold standard for EtherCAT controllers. With over 1,000 EtherCAT devices, Beckhoff has the largest EtherCAT product portfolio - which can, however, be supplemented with the offerings of 3,000 officially registered vendors if required. And what is not yet available can be developed comparatively easily: the EtherCAT Slave Controller chips make it possible.
The evolution of EtherCAT
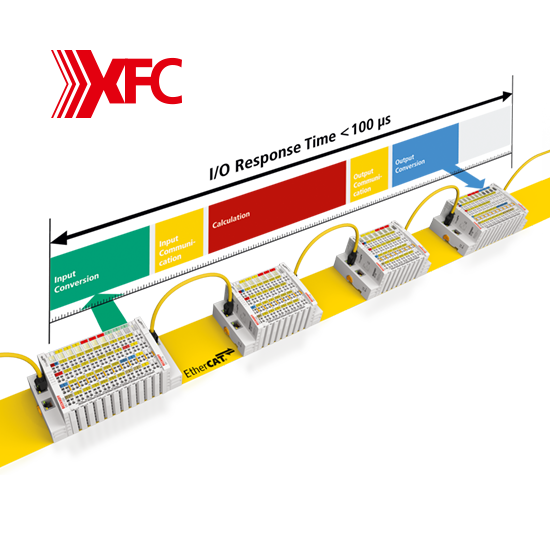
XFC
Based on an optimized control and communication architecture, XFC realizes response times of < 100 µs.
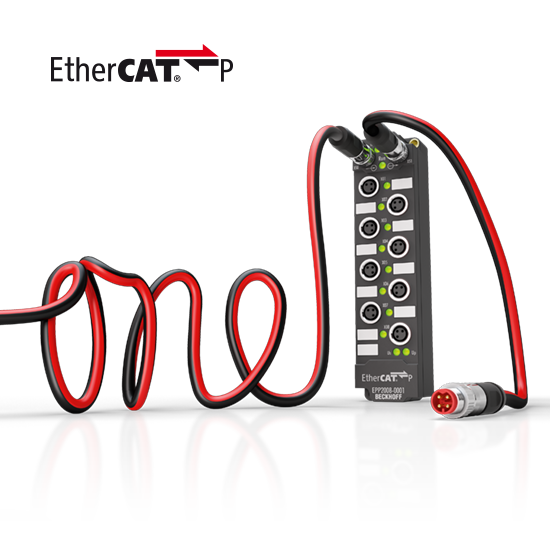
EtherCAT P
The one cable solution – One step closer to automation without control cabinets.
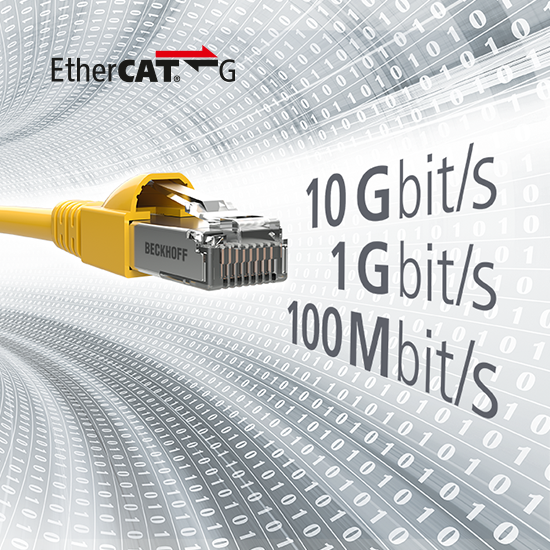
EtherCAT G
The continuation of the successful EtherCAT technology moves the available data rates up to 1 Gbit/s and 10 Gbit/s.
EtherCAT Technology Group – ETG
The EtherCAT Technology Group (ETG) keeps EtherCAT technology open for all potential users. It brings EtherCAT device manufacturers, technology providers, and users together to further the technology. They are focused on one common goal: keeping EtherCAT stable and interoperable. The ETG holds multiple Plug Fests in Europe, Asia, and America each year. The Plug Fests bring EtherCAT device developers together to test and ensure device interoperability. Using the official EtherCAT Conformance Test Tool, each manufacturer conformance tests its EtherCAT devices prior to their release. The ETG awards the manufacturer a Conformance Certificate following a successful test in an accredited test lab.
The ETG has the largest number of members out of any fieldbus organization in the world. The list of members can be found on its homepage. However, the decisive factor is not how many members there are, but how active the members are in the ETG. Both the number and variety of EtherCAT devices is unparalleled, and the adoption rate of EtherCAT across Europe, Asia, and America is outstanding.
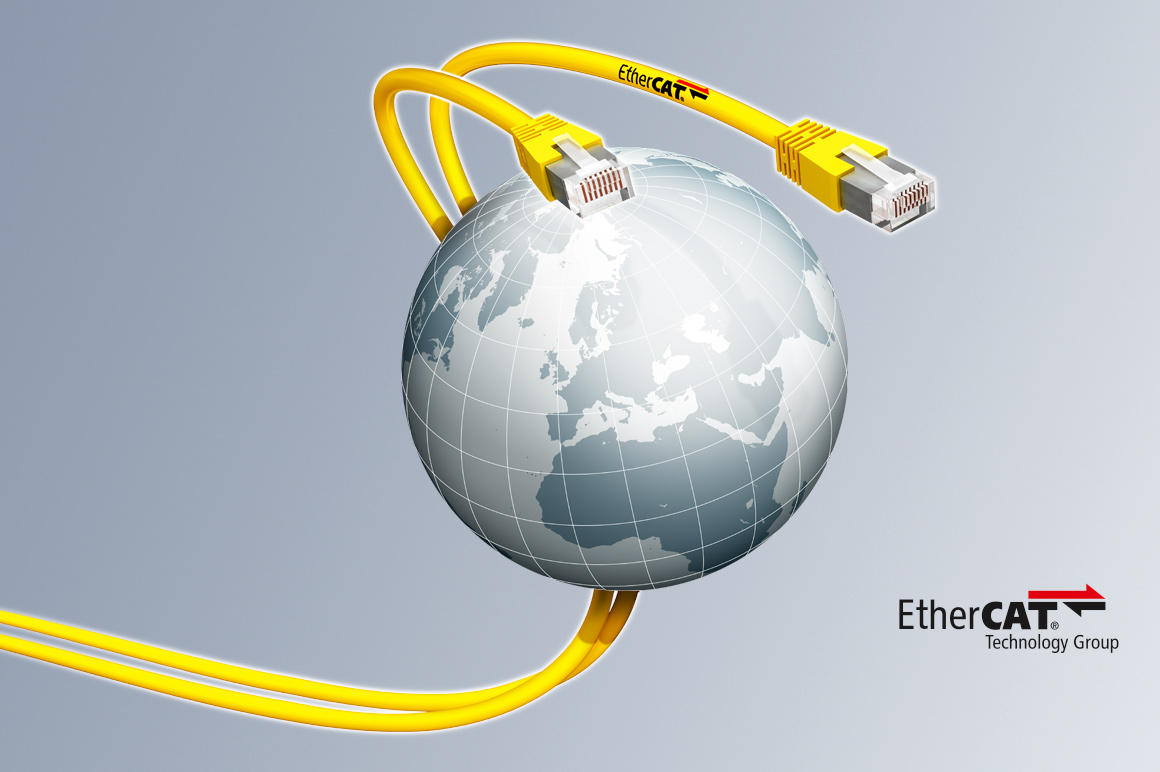
Milestones
- 2003 Introduction of EtherCAT technology at Hannover Messe
- 2003 EtherCAT Technology Group founded at SPS IPC Drives
- 2005 Safety over EtherCAT
- 2007 EtherCAT is IEC standard.
- 2016 EtherCAT P: ultra-fast communication and power via one cable
- 2019 EtherCAT G: the next performance level with 1 Gbit/s