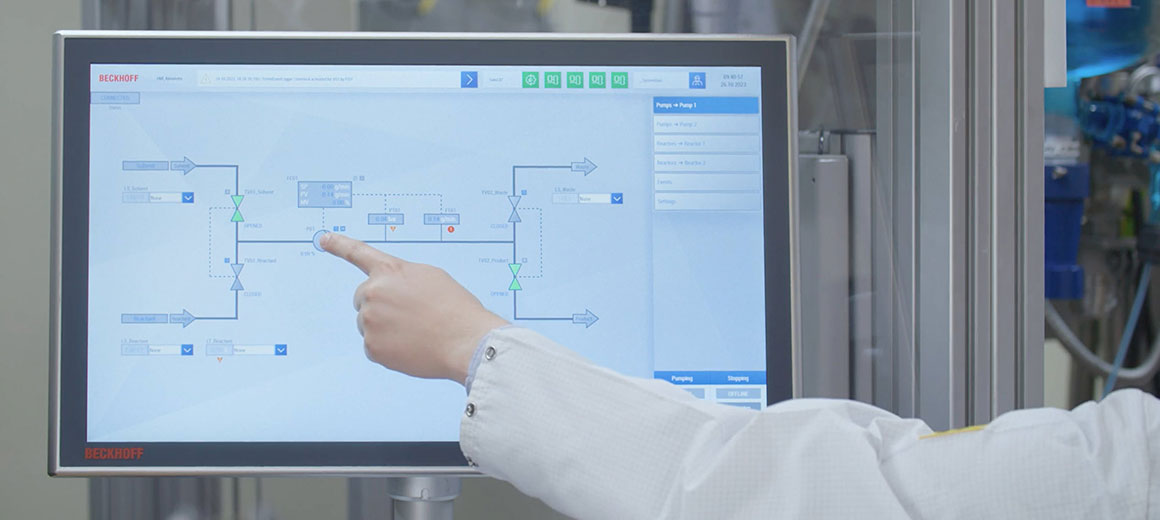
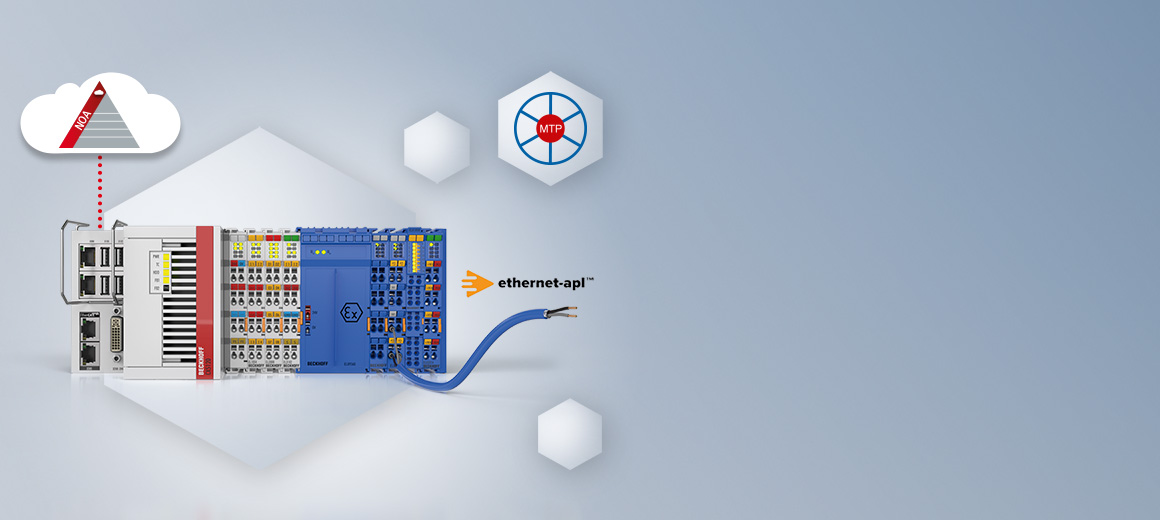
Digitalization for the process industry
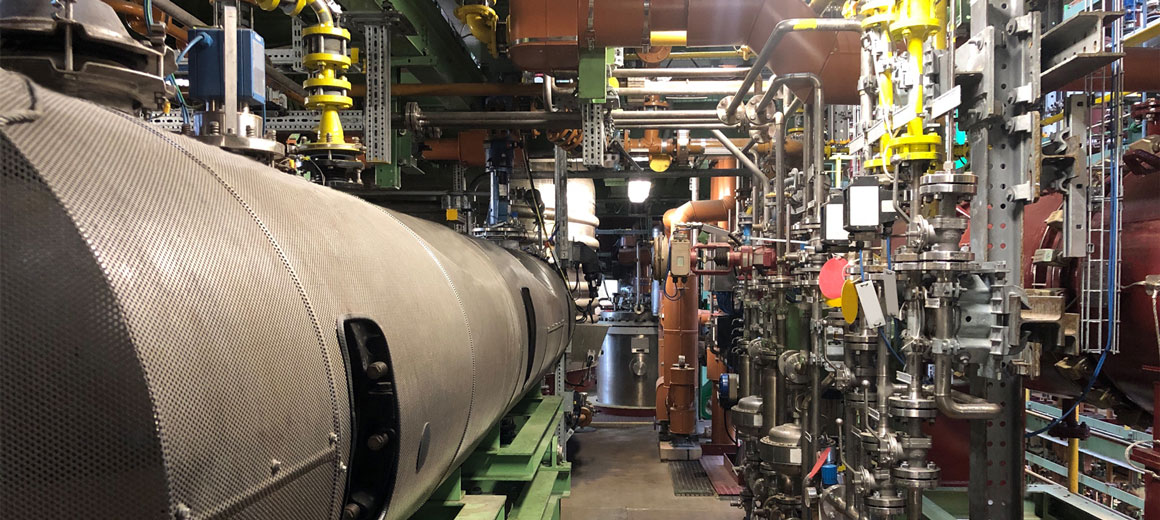
PC-based control for the implementation of
NAMUR Open Architecture (NOA)
Bayer, Deutschland
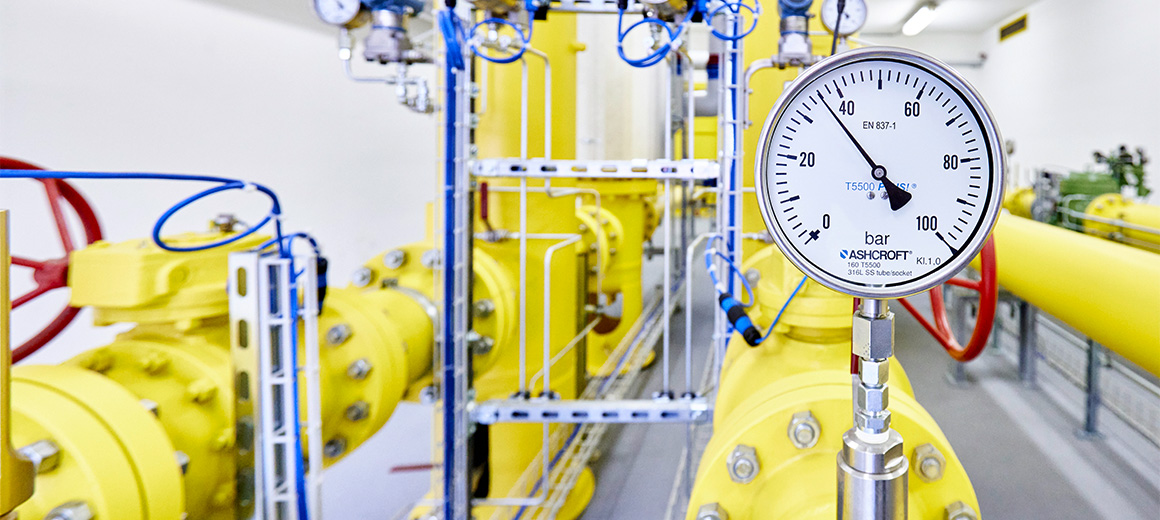
Siedziba Główna Polska
Beckhoff Automation Sp. z o.o.
Bayer, Deutschland
In the process industry, there is increasing demand for innovative automation solutions that provide an increase in efficiency while taking production quality and safety into account. The development of new technologies opens up possibilities for optimizing production processes, both for modern new plants and when retrofitting existing plants. Beckhoff offers open automation solutions that precisely meet these requirements.
Do you have any questions?
Intelligent networking improves plant availability in the oil and gas industry
Open up efficiency potentials along the entire value chain of large-scale chemical plants through Industrie 4.0
Increased productivity and enhanced personal safety through digitalization in mining
Automation and process technology in one system: from machine control to building automation in the paint shop
Innovative control systems for the efficient and flexible automation of hydrogen plants
Future-proof solutions for the energy sector: from biogas plants to smart cities
Flexible and competitive production: process monitoring and networking in the steel mill
For an explosion to occur, an ignitable mixture of oxygen and fuel must come into contact with an ignition source. Explosion protection involves measures being taken to prevent explosions by excluding one of these three factors. Since processes or plants often use flammable substances that form an explosive atmosphere in combination with air, hazardous areas must be marked as such so that attention is paid to preventing risks arising from potential ignition sources. Hazardous areas are divided into zones 0/20, 1/21, and 2/22 (gas/dust) according to European and international explosion protection regulations and into a class and division according to North American regulations.
With our comprehensive portfolio of Ex components, we enable integrated solutions for explosion protection to be implemented: EtherCAT Terminals with intrinsically safe interfaces, panel and industrial PCs or bus coupler for easy integration into all common fieldbuses. This allows you to implement any explosion protection application with Beckhoff, including the retrofitting of existing plants.
Various directives and standards apply worldwide for the use of plants and equipment in hazardous areas:
In addition, there are country-specific approvals, such as IA for South Africa. Users must ensure compliance with applicable directives and standards when repairing their plants.
The Ex component portfolio from Beckhoff complies with all listed as well as country-specific standards and is certified for use in hazardous areas in accordance with the applicable regulations. As a result, PC-based control makes uniform solution concepts possible worldwide for seamless system integration up to zone 0/20.
In a conventional implementation of standard-compliant explosion protection, separate safety barriers are required for the connection of field devices from zone 0/20. Accommodating these in the control cabinet not only requires comparatively extensive wiring work, but also a large amount of space.
The use of the ELX series of highly compact EtherCAT Terminals means separate safety barriers are no longer needed. The terminals allow the direct connection of intrinsically safe sensors and actuators installed in hazardous areas up to zone 0/20. The savings achieved by using ELX terminals in terms of the work involved and space requirements enable machines and plants to be built that are as compact as they are efficient. The result is that control cabinets can be made significantly smaller, and the costs and work involved are reduced.