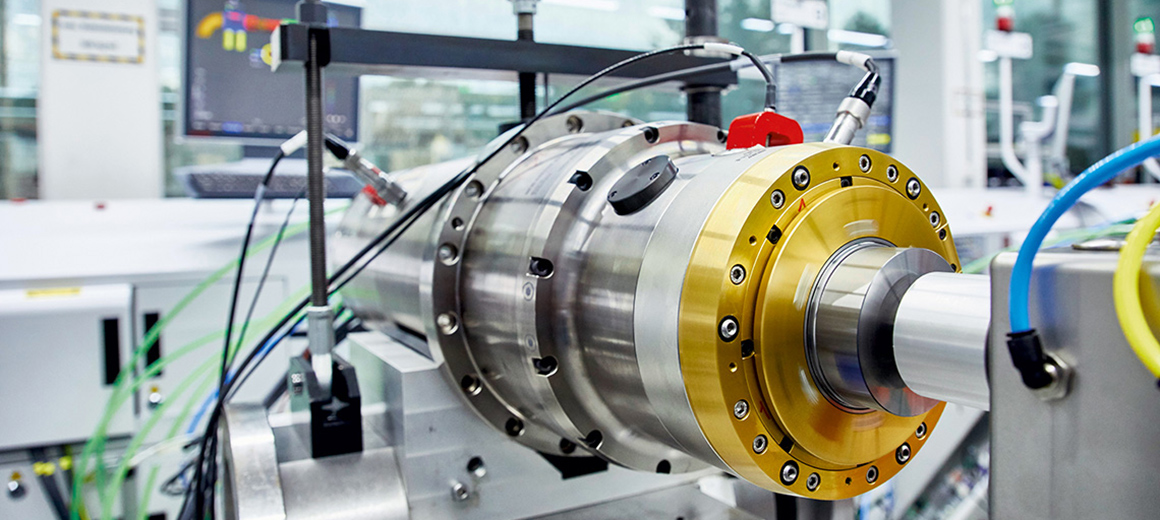
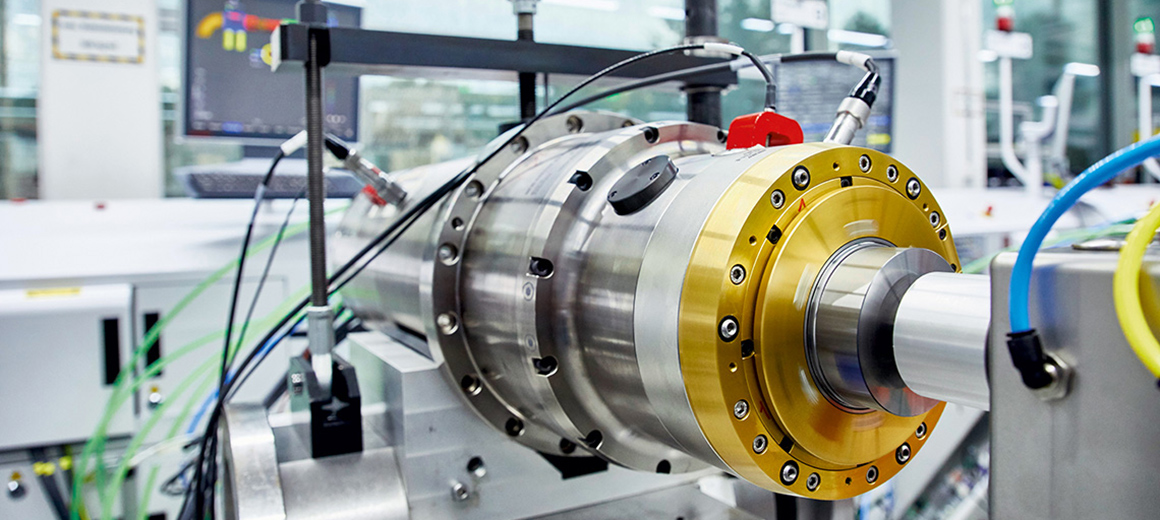
PC-based control optimizes test data
Motor spindles must meet particularly high quality requirements. Therefore, every single spindle from Fischer AG in Herzogenbuchsee, Switzerland, passes through a sophisticated test program before it is delivered. To increase testing capacity as well as the quantity and quality of the test data, a new test bench was developed with the help of PC-based control technology from Beckhoff. Fischer AG is thus taking an essential step towards digitalization.
Fischer AG is a family-run company in the third generation and celebrated the 80th anniversary of its founding in 2019. In the early years, the company developed simple, belt-driven grinding spindles, in particular for the company’s own parts manufacturing. The portfolio now encompasses all areas of machining, such as grinding, milling and high-performance cutting for structural components used in the aerospace industry. The latest additions to the portfolio are compressors with aerodynamic bearings for fuel cell air supply in the automotive segment as well as milling heads in combination with the Fischer spindle, which are produced in Taiwan. “Our spindles with patented shaft cooling are unique in this form on the market – this is a high-end product that is used for the machining of ultra-precise shapes,” explains Stefan Schneider, Head of Technology at Fischer AG. These products serve a niche market that is characterized by low-volume production.
An important reason for the development of a new test bench was the quality of data acquisition. In the future, it should be possible to collect not only more, but also more reliable test data. In particular the comparability of the data was difficult to achieve with the old test bench on account of a central cooling system that was distributed across several test stations. With the new test bench, not only has the quality control and reliability of the data improved, but the possible throughput has virtually doubled as well. “In the ‘new spindle test’ project, we decided to build the fast control technology and the complete control intelligence with automation components from Beckhoff,” explains Adrian Flükiger, Head of Test Bench Construction. He adds that speed and performance were important criteria for this decision, as was the openness of the PC-based approach that Beckhoff pursues with its control technology.
100% testing with redundant construction of test groups
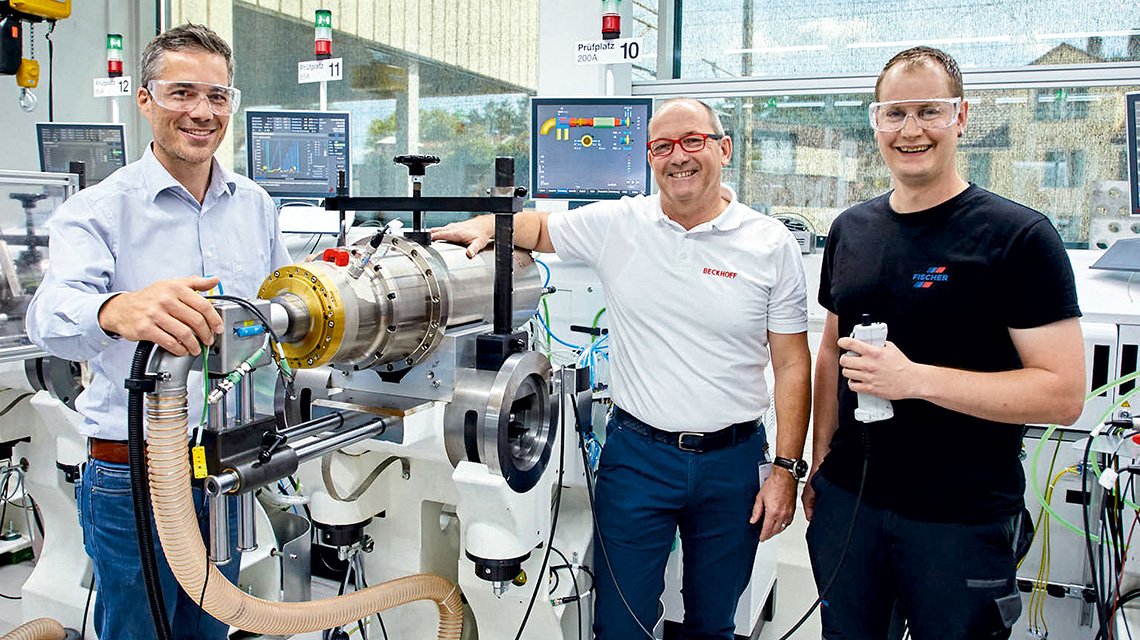
“We carry out a 100% end-of-line test for quality checking. Each spindle that we manufacture passes through a test cycle lasting several hours,” explains Stefan Schneider. The new test bench has two redundant groups, each with six independent test stations. Both groups are equipped with a Beckhoff C6250 control cabinet Industrial PC (IPC). In addition, each test station has a C6920 control cabinet IPC and a CP3919 multi-touch Control Panel on a mounting arm and connected by CP-Link 4 for the operator interface. The design with redundant test station groups was selected in order to ensure the highest possible security of the entire system against failure.
The desired test parameters are stored in a database. Once a spindle has been installed in the test bench, the matching parameter set is loaded by means of a barcode scan. Subsequently, the spindle passes through the cycles defined in the parameter set, consisting of running-up, production and acceptance cycle. 257 sensors in each test station supply high-resolution data that are exported, compressed and analyzed. These are then available worldwide in a database. “With the new test bench and the high data quality that we can achieve with it, it is now possible to overlay the results from spindles of the same type and in this way to better detect irregularities,” explains Adrian Flükiger. “That increases the quality and reduces the return of faulty spindles, because they aren’t delivered in the first place.”
The quality and reliability of the acquired data is very important, as data analysis and digitalization are of increasing significance for the company. Two employees are already overseeing these topics full-time. “Since we have been able to log with high resolution and the measured data are comparable, we can recognize patterns and define new quality criteria as a result,” says Stefan Schneider. “One example of this is the analysis of the bearing temperatures. Previously we only monitored the limit values. Fluctuations below the limit values couldn’t be detected at all. Using the new test bench, we can now detect such anomalies.”
Predictive maintenance and connectivity
The test bench has been running for one year now with all 12 test stations and without issues – and that is the way it should stay. For that reason, not only are test data for the spindles collected, but also components of the system that are subject to maintenance are monitored, such as filters. Adrian Flükiger says: “With our old test benches, we scheduled maintenance intervals at Christmas or during the summer holidays. We want to get away from that. The availability of the new system should always be guaranteed. For that reason, the components that are subject to maintenance are monitored and replaced where necessary.” In the case of the IPC, for example, the utilization is monitored and logged. If the utilization of a computer is permanently around 90%, the cause is sought and eliminated. If necessary, an IPC can be replaced by a higher-performance device from the wide Beckhoff portfolio without having to expend a great deal of time, as the installations are mirrored and can be loaded simply onto a new IPC.
The connectivity capability of the test bench is also a novelty, because with the old test bench all settings had to be made on site. The new test bench, in contrast, allows optimization via remote access, and cameras supply the images necessary to ensure reliable operation. This option is frequently used by Fischer AG, especially as the test bench is operated in several shifts as well as over the weekend.
TwinCAT 3 features facilitate test bench development
Due to performance problems, the graphic programming system originally used was abandoned in favor of the object-oriented programming language C#. The .NET interface of TwinCAT 3 is used for programming with C#. “A further feature that proved to be very helpful in the software development was the multi-instance option of TwinCAT. After all, there are 12 test stations, but with the multi-instances, the code only has to be written for one. That saves a lot of time and programming work,” explains Adrian Flükiger.
According to Adrian Flükiger, one feature that has proven very useful in the commissioning of the new test bench is the TwinCAT 3 Scope software oscilloscope, which is fully integrated into the TwinCAT control architecture and enables the simple graphic representation of signal curves via the charting tool: “With the TwinCAT 3 Scope, we can view the signal from each terminal virtually in real-time. We only realized the great benefit of this feature during the development phase. It’s a great help if you can compare the signals during commissioning or troubleshooting.”
Open control technology supports a wide range of bus systems
EtherCAT serves as the main bus system in the new test bench. However, other fieldbuses are present too due to some indispensable components. “It’s a great help to us that we can mix several fieldbus types, because we operate motors in the test bench that are connected via PROFIBUS. On account of some valves, a CAN bus is also necessary. Through the open Beckhoff control technology, however, it’s no problem to mix several bus systems,” says Adrian Flükiger. He says that the EtherCAT Box modules from Beckhoff’s EP series have also proven to be very helpful: “Much more cabling would have been necessary without these IP67 I/O modules, because the fieldbus and signal wiring is considerably simplified by the decentralized installation and pre-assembled cables of the EtherCAT Box modules. Wiring errors and commissioning times can thus be minimized. The EtherCAT Box modules support all important fieldbus systems. This substantially frees electrical design from the particular bus system in use.”
“We use the Sync Units inside TwinCAT for the terminals,” Adrian Flükiger continues. “This allows applications to be structured, which ensures a better overview and simplifies fault-finding.” Sync Units define independent units of I/O devices. If a fieldbus device fails within a Sync Unit, then devices in its own Sync Unit are marked as faulty. The devices in other Sync Units are not affected by this.
Support from Beckhoff Switzerland assists development
The fact that competent support was available in the immediate vicinity from the Beckhoff office in Lyssach proved to be very helpful during the implementation of the demanding and complex project. “Beckhoff supported us in the preliminary testing and also with workshops when several issues had accumulated,” says Stefan Schneider. “For that reason, especially at the start, employees from Fischer AG were frequently in the office in Lyssach or the other way around. Some things can best be clarified in face-to-face meetings. Even today we still need support now and again. For the project team from Fischer AG, the software development is a central pillar for sustainable business success. For that reason, the team has rigorously focused on quality and efficiency and brought a specialist for TwinCAT and .NET development on-board in the Beckhoff Solution Partner mbc engineering GmbH. Through the close cooperation, synergies can be used consistently and implemented for added value.”
Positive outlook for spindle manufacturing
“The wide range of automation technologies available from Beckhoff covers all requirements from our point of view,” says Stefan Schneider. “Our test bench construction department is therefore in the process of retrofitting all old test benches with Beckhoff components.” A further test bench is also already being planned in line with the new concept, as Adrian Flükiger explains: “The present test bench was designed for motor spindles that are used in milling applications. A further test bench will be implemented for grinding spindles using a similar design. The test bench mechanics must be completely changed for that, but the concept for the controller and software modules can be reused for the most part.”