Products
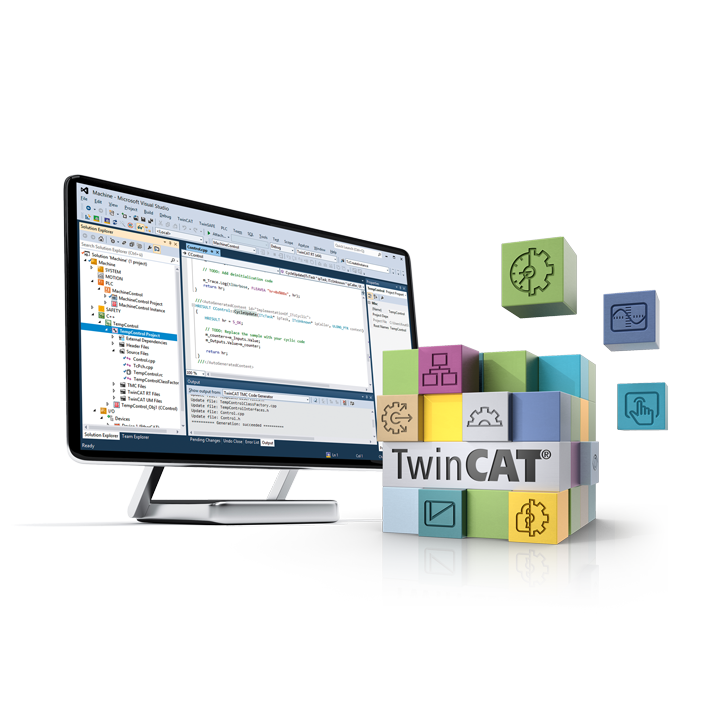
TExxxx | TwinCAT 3 Engineering
The TwinCAT 3 engineering components enable the configuration, programming and debugging of applications.
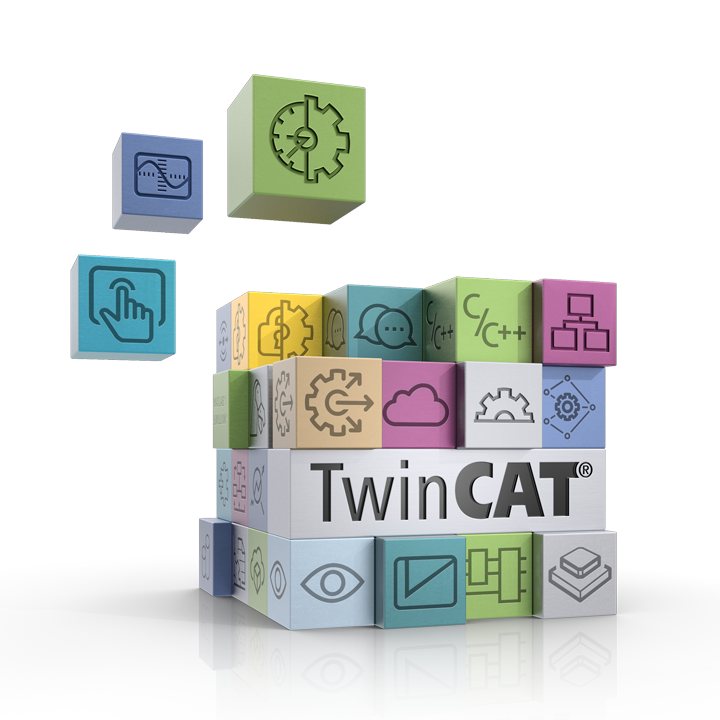
TFxxxx | TwinCAT 3 Functions
The basic components can be extended by TwinCAT 3 functions. The functions are classified into various categories. e.g. motion control, measurement technology, control technology and communication.
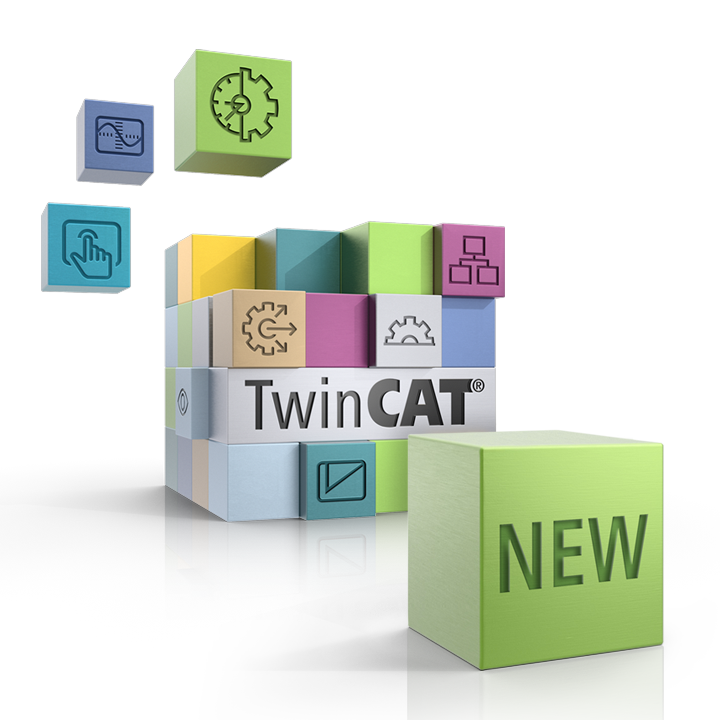
TwinCAT 3 | Build 4026
More flexibility in automation development through modularity and extensions
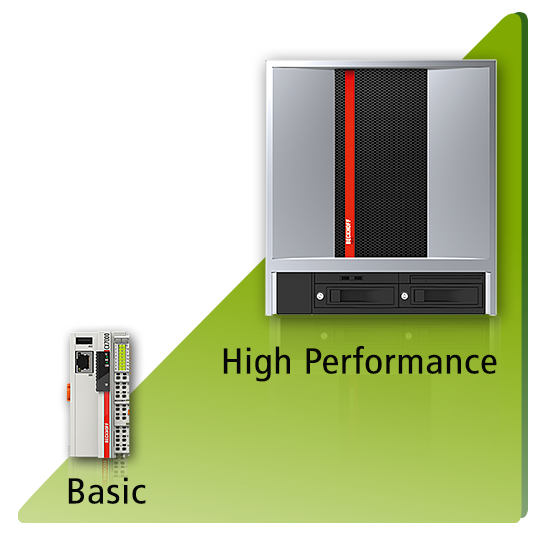
TwinCAT 3 | Platform levels
The TwinCAT 3 runtime components are available for different platform levels. The platform levels correspond to the various TwinCAT 3 platform levels of the Beckhoff PCs.
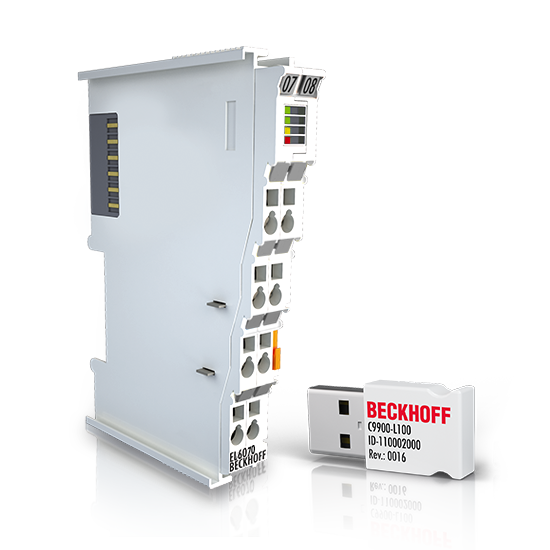
TwinCAT 3 | Licensing
TwinCAT 3.1 offers the option of using a TwinCAT 3 license key (license dongle) for licensing.
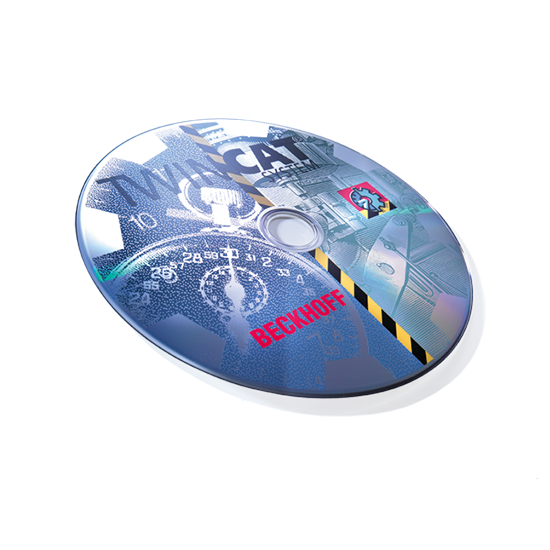
TXxxxx | TwinCAT 2 Base
TwinCAT 2 Base consists of runtime systems for the real-time execution of control programs and development environments for programming, configuration and diagnostics.
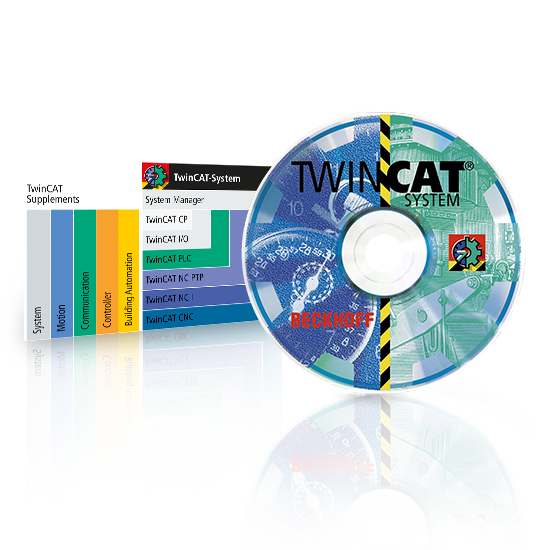
TSxxxx | TwinCAT 2 Supplements
The TwinCAT 2 Supplements can be used for the individual addition of functions to the TwinCAT 2 Base components.
The world of TwinCAT: Open, PC-based control technology
When Beckhoff launched its PC-based control technology, it created a global standard for automation. In terms of software, the core of the control system has taken the form of The Windows Control and Automation Technology – or TwinCAT – automation suite since 1996. In combination with TwinCAT, the Beckhoff portfolio results in optimally coordinated automation concepts that fulfill the basic principles of an open and highly scalable control system.
TwinCAT transforms almost any PC-based system into a real-time control complete with multiple PLC, NC, CNC, and/or robotics runtime systems. The possibility of modular extensions means functional changes and additions can be made at any time. If required, the openness of the control system allows not only the integration of third-party components, but also customized retrofit solutions for existing machines and systems. This ensures flexibility and investment protection for the customer.
TwinCAT 3: The flexible software solution for PC-based control
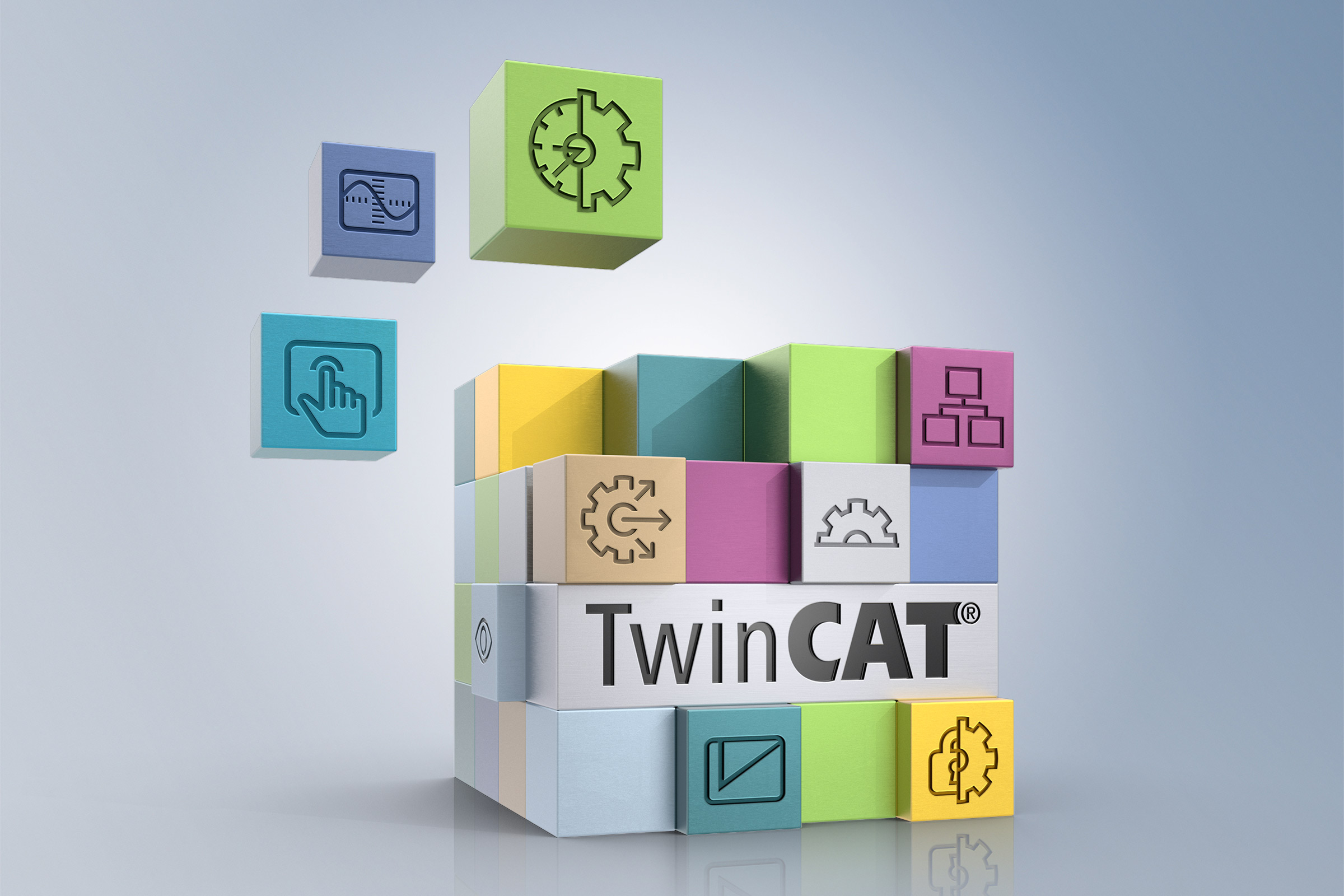
With TwinCAT 3, the latest version of the software, the Beckhoff portfolio results in optimally coordinated automation concepts that fulfill the basic principles of an open and highly scalable control system.
TwinCAT 3 follows on logically from TwinCAT 2 as the latest development in the series, which is already redefining the world of automation technology as we know it. The way the complete control intelligence is implemented on a single software platform, divided into engineering and runtime, still represents the basis of the system.
What’s more, both engineering and runtime can be flexibly extended by application-specific software modules, known as Functions, so that the TwinCAT system can be perfectly adapted to suit individual requirements.