Products
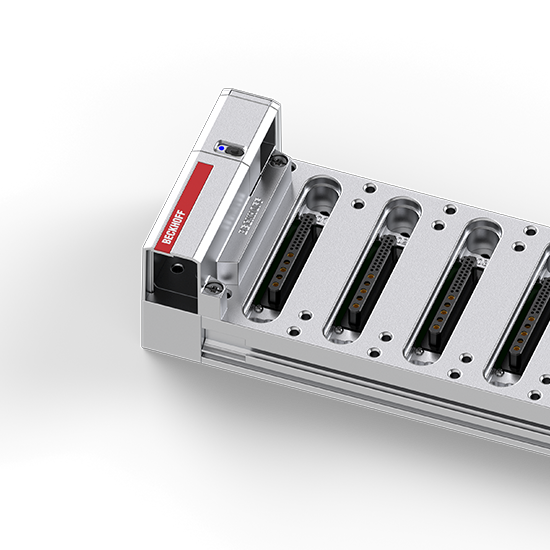
MBxxxx | Baseplates
Scalable baseplates as the basis for automation without control cabinets.
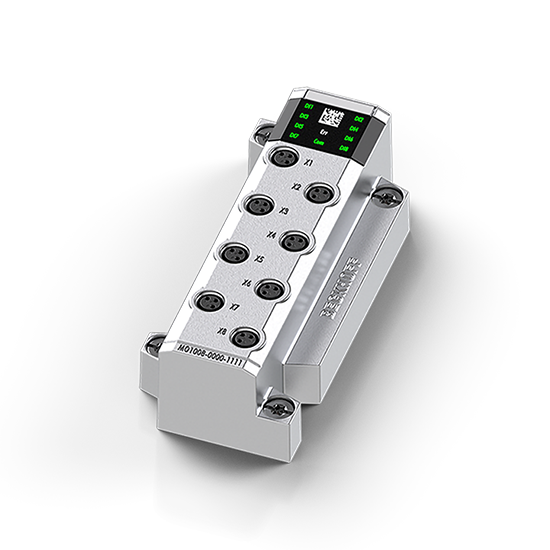
MOxxxx | I/O modules
Comprehensive selection of I/O modules for all signals of the automation world.
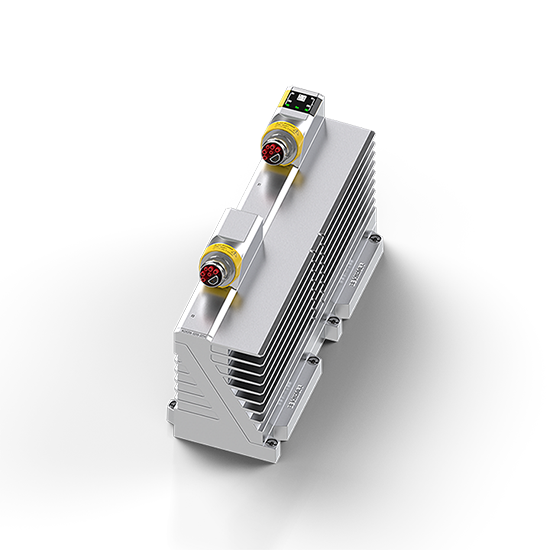
MDxxxx | Drive modules
Compact multi-axis systems for drives of all types and power levels.
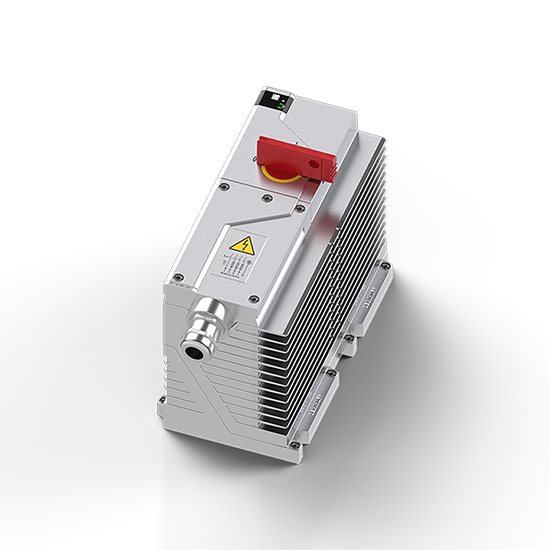
MSxxxx | System modules
Feeding and forwarding of data and voltages, power supplies and switches.
Decentralized and control-cabinet free automation
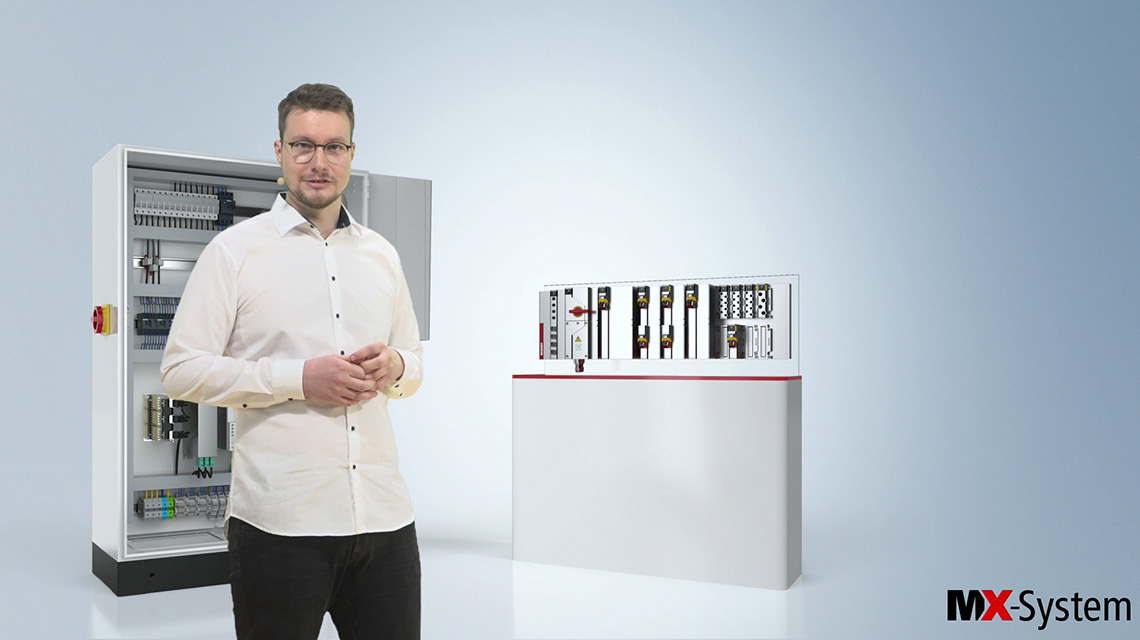
The decentralized MX-System is the first to achieve completely control cabinet-free automation of machines and systems. To this end, Beckhoff has bundled over four decades of automation expertise into a modular system that performs all of the tasks and exhibits the properties of a classic control cabinet.
Benefits
- simplified engineering phase and reduction of machine footprint and cable paths
- UL/CSA and IEC certified – the system can be used worldwide without adjustments
- plug-and-play principle so that assembly and installation can be performed by non-specialist personnel
- fast and clear system diagnostics during operation
Learn more about the MX-System
Automation beyond the control cabinet
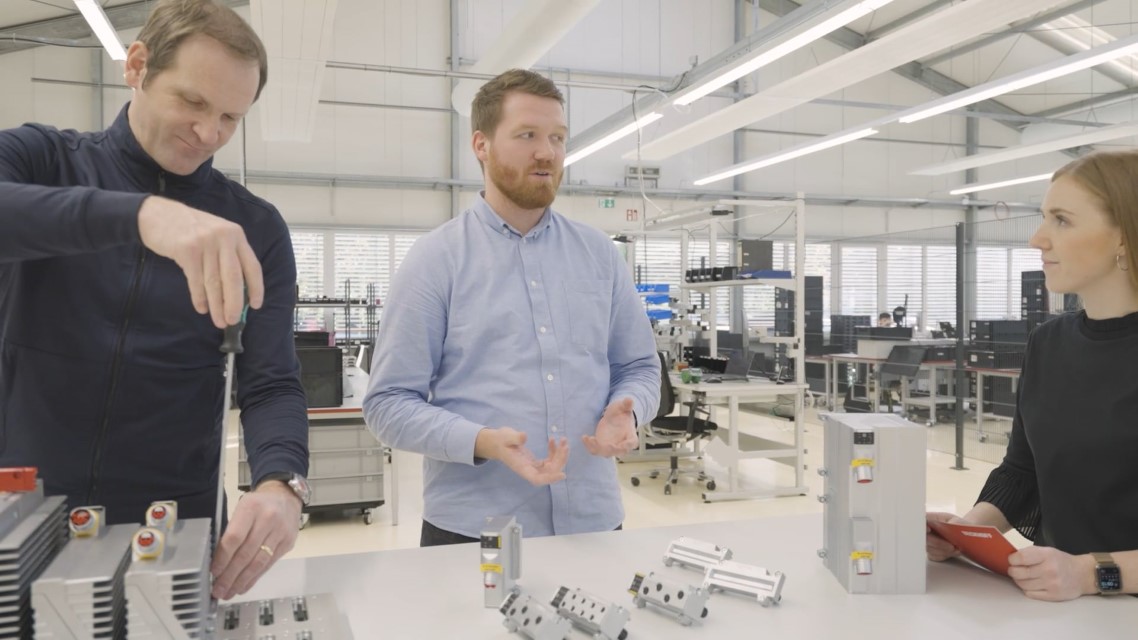
#1: What is the MX-System?
The MX-System is the first to achieve completely control cabinet-free automation of machines and systems. In this new video series, we will introduce the system, its components, and application examples. In the first episode, Paula Göbel, MX-System product manager, explores what the MX-System is and how it functions. Take a look!
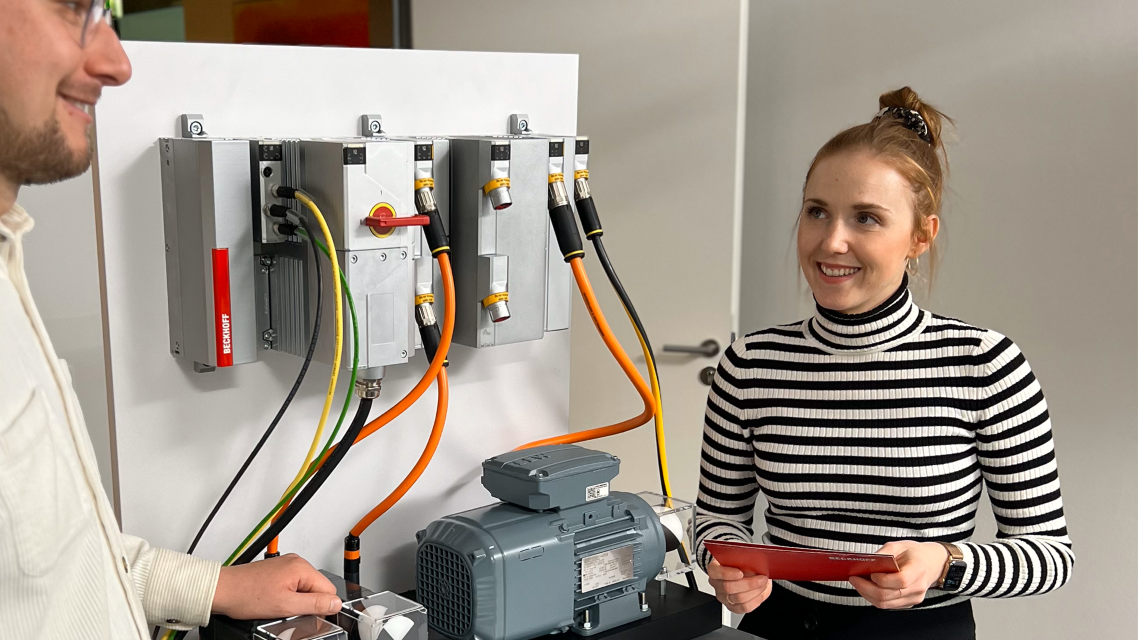
#2: Who can use the MX-System?
In this new MX-System video series, we introduce the pluggable system solution for control cabinet-free automation with all its products and features. Before we delve deeper into the individual components, let's look at who the MX-System was actually developed for.
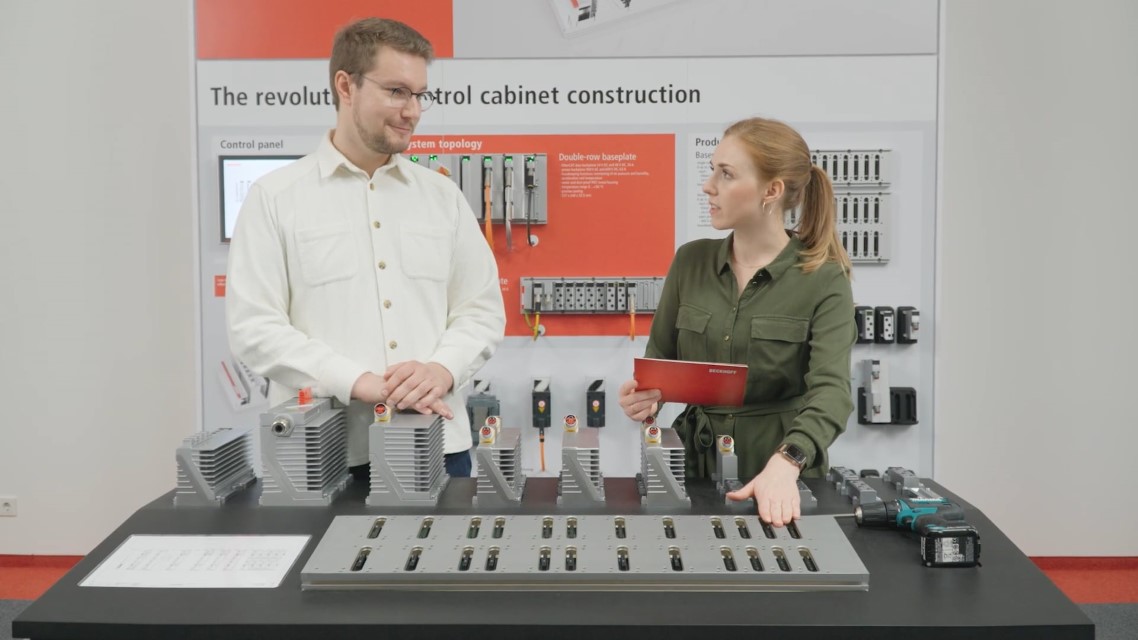
#3: The baseplates
In the third episode of this video series, Paula Göbel, MX-System product manager, introduces the baseplates. They are the back wall of the system and form the foundation of control cabinet-free automation with the MX-System. In this episode of the MX-System series, you can discover the differences between the baseplates and their common functions.
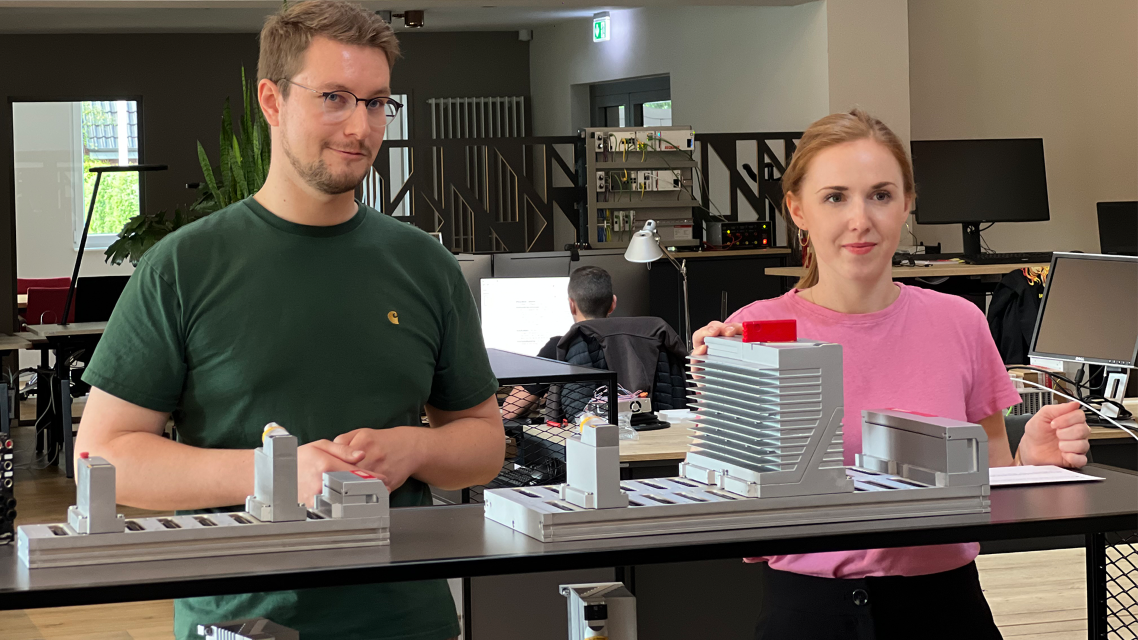
#4: The system modules
The MX-System's infrastructure is constructed with system modules. In this episode of the MX-System series, we explore the tasks that the system modules can take on in order to completely replace the control cabinet.
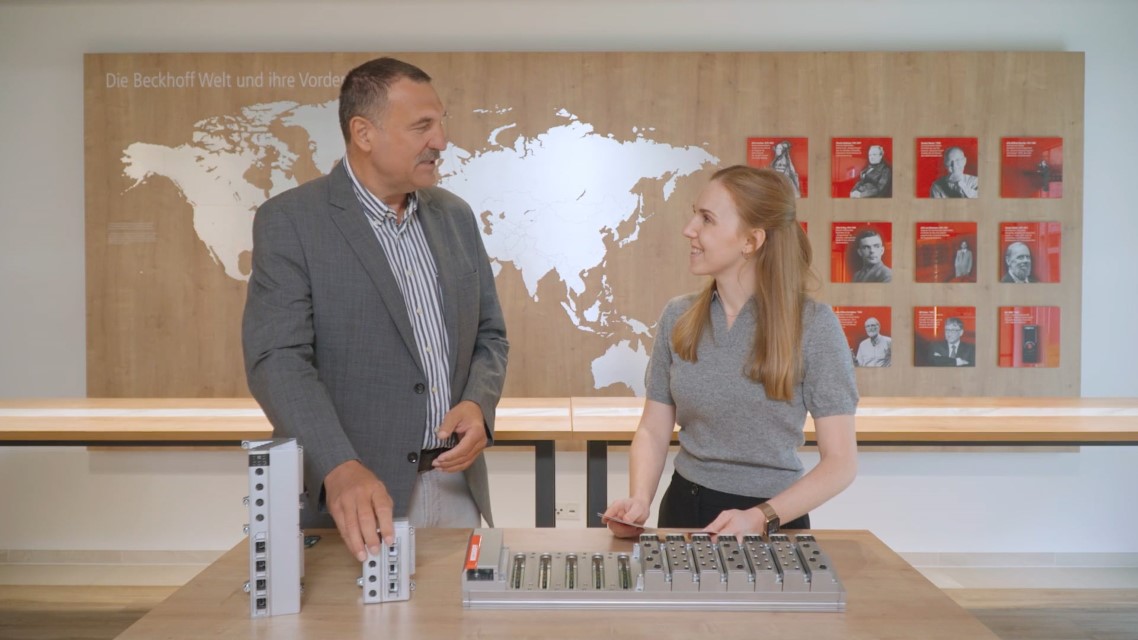
#5: The IPC modules
Industrial PCs are the core hardware for PC-based control technology. Beckhoff offers powerful and scalable industrial PCs for the MX-System in a highly compact format in its robust IPC modules. In this episode, we look at which IPC modules are available and their special properties.
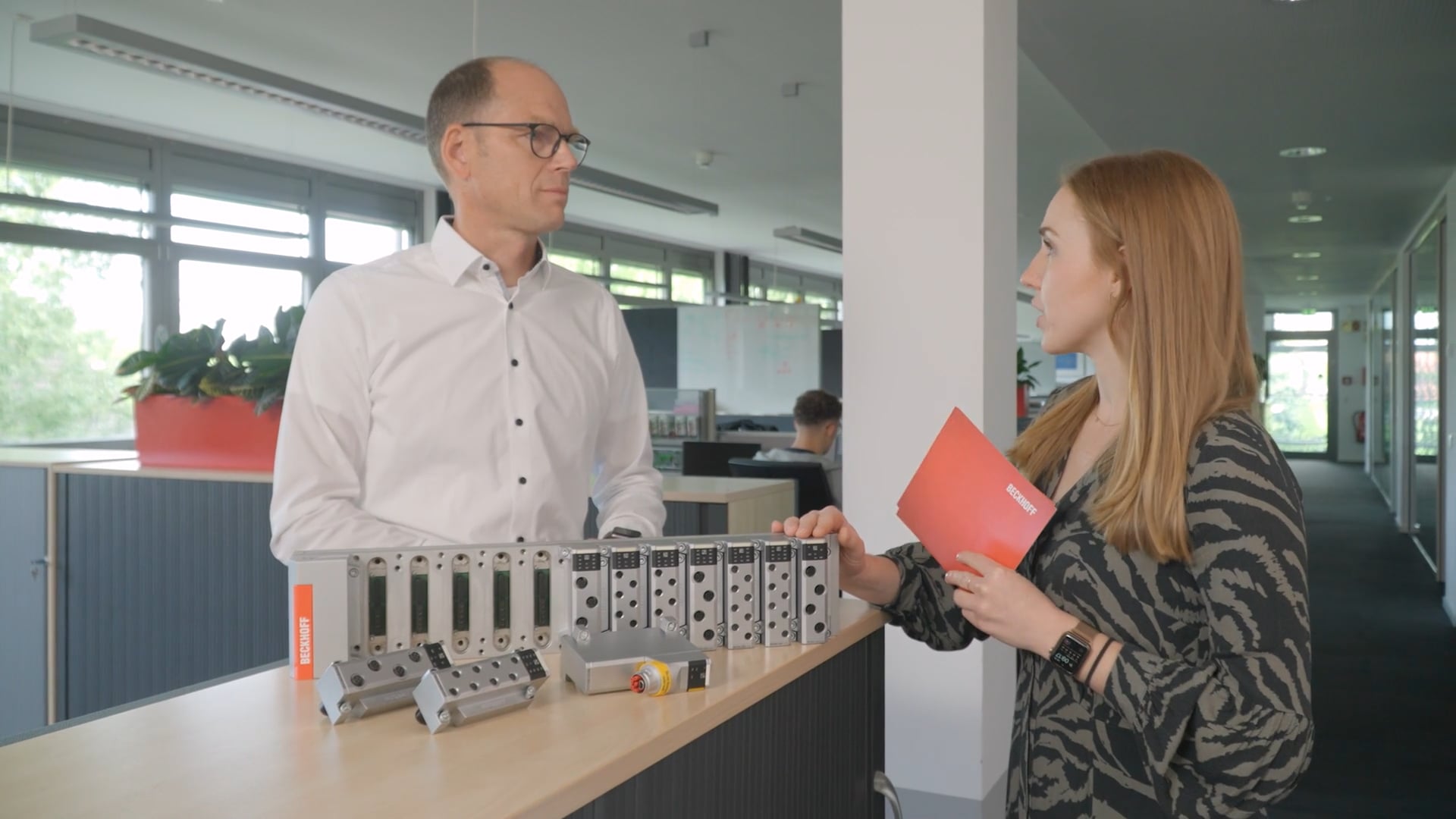
#6: The I/O modules
In line with the comprehensive Beckhoff I/O portfolio, the MX-System's I/O modules also constitute a wide product range for all automation environment signals. Paula Göbel has invited Michael Jost, senior product manager for I/Os, to discuss the I/O modules and the broad scope that they cover in this episode.
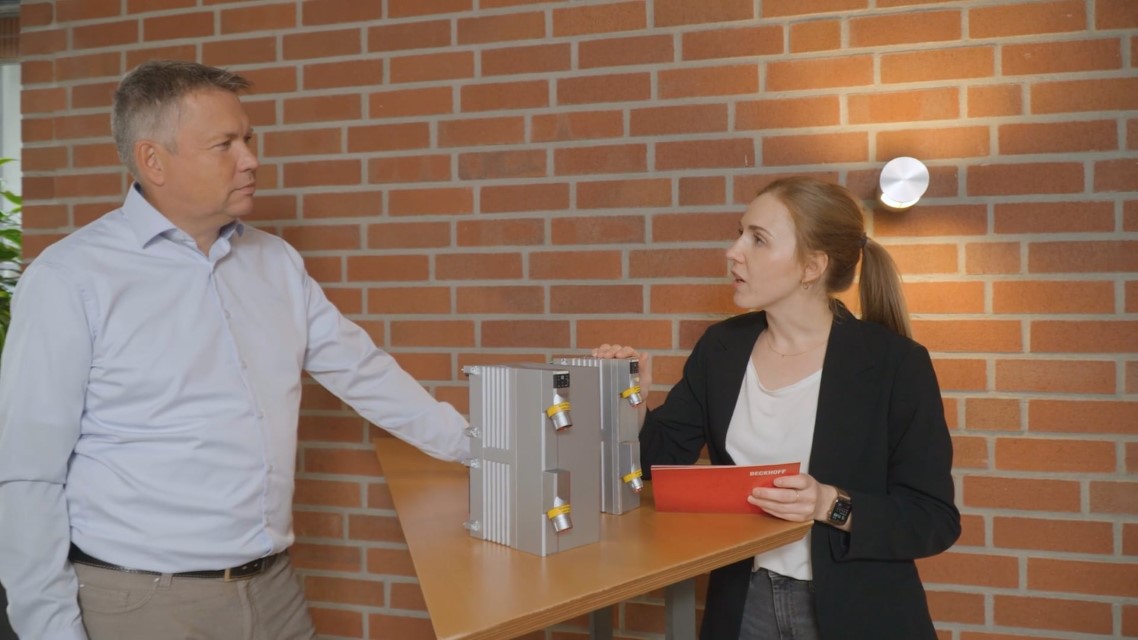
#7: The drive modules
In this new episode of the MX-System series, Paula Göbel looks at drive modules with her guest Dirk Hansen, senior product manager for motion. Can multi-axis systems be integrated into the MX-System directly? Find out the answer to this question and more in the video.
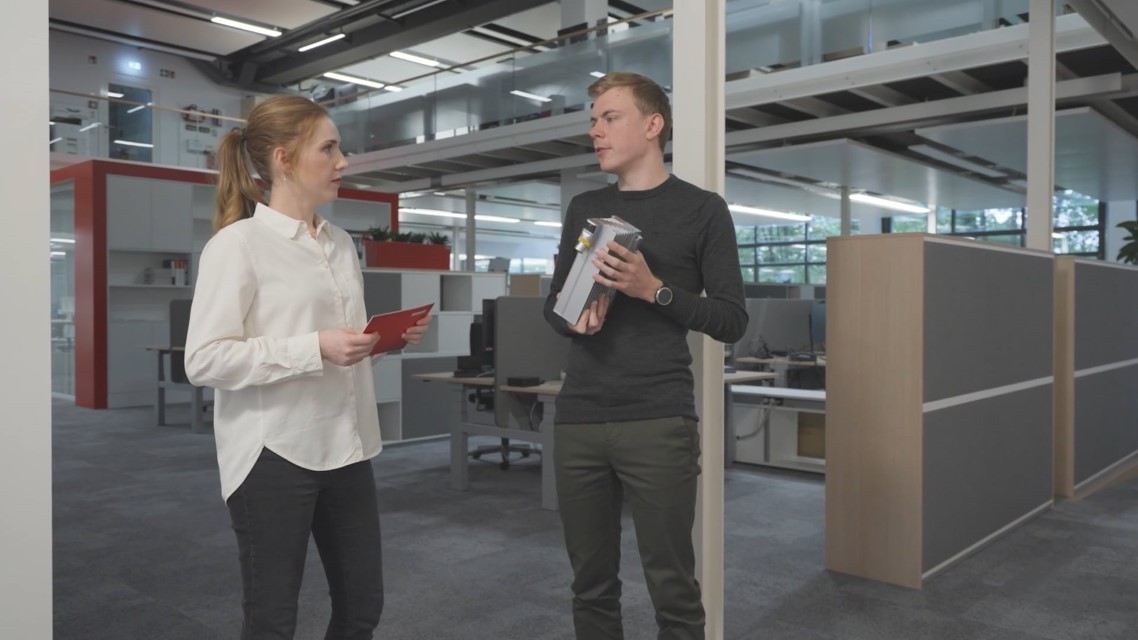
#8: The relay modules
High power needs to be connected safely in a control cabinet. In the control cabinet-free MX-System, relay modules are used for this. Watch this video to find out more about the different relay modules that Beckhoff offers for the MX-System.
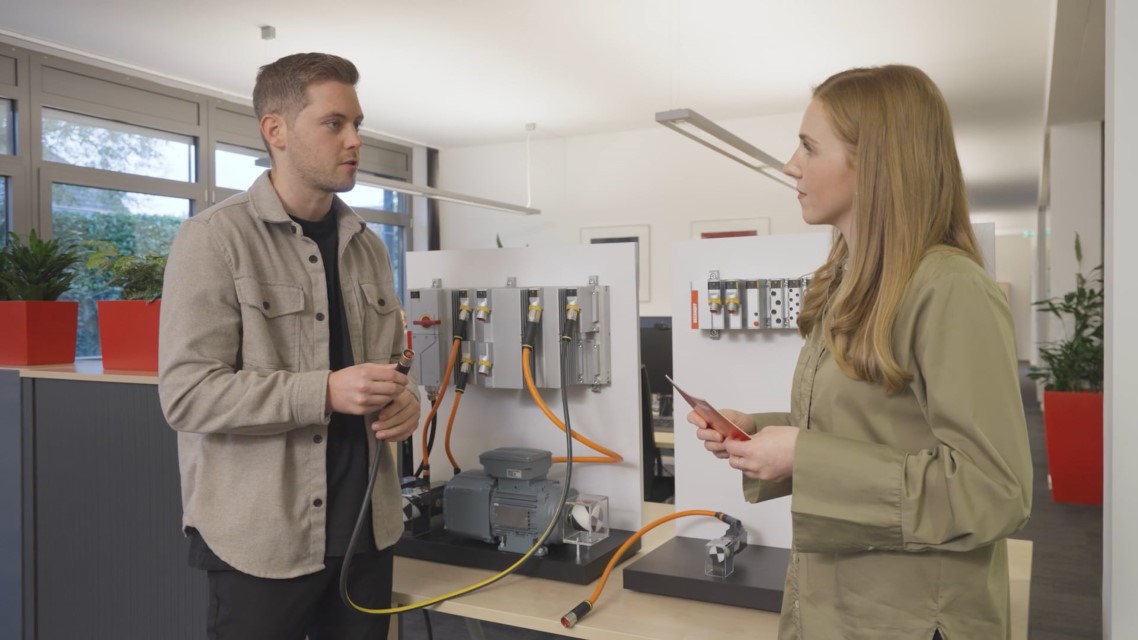
#9: Cables and plugs
Find out more about how the power signal and data communication are combined in a single cable in this new episode of the MX-System series. Having one single cable saves time and money while also protecting the environment. It also simplifies the entire process surrounding the MX-System.
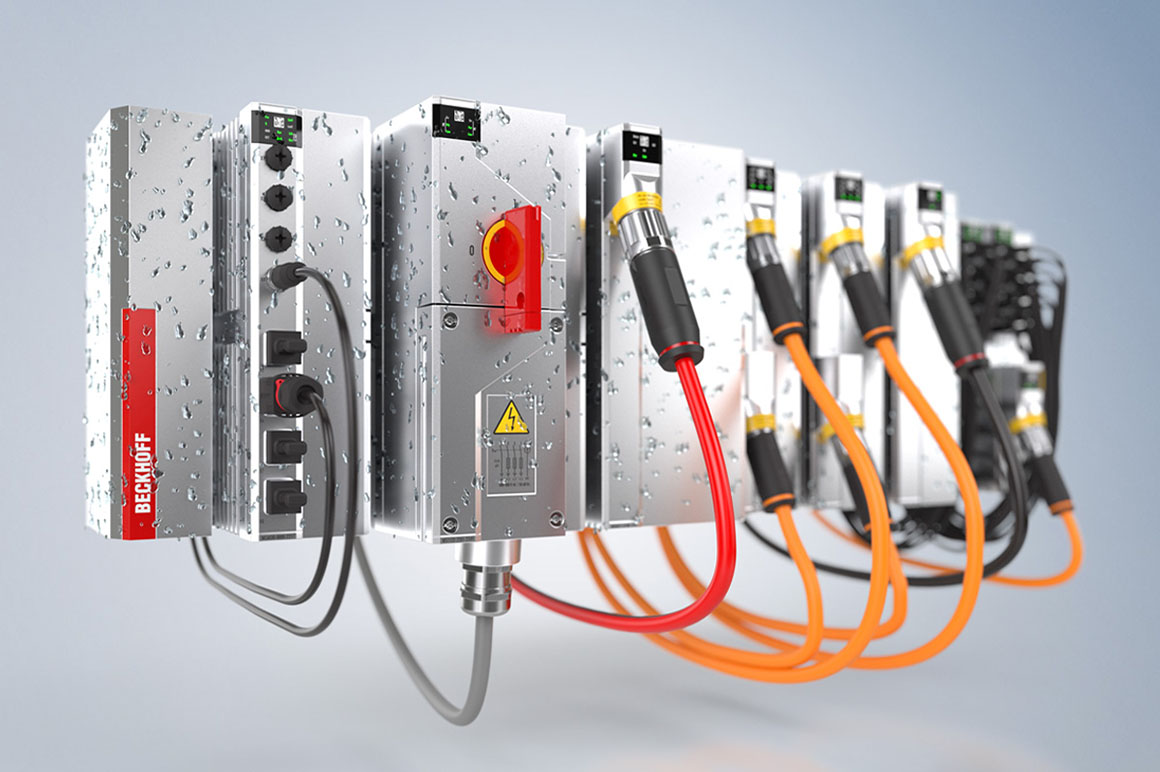
Robust and compact
A system that withstands any environment
The MX-System offers a tailor-made solution for every application. The materials and workmanship of all components are designed for maximum durability. This allows the MX-System to be used directly on the machine or system, even in demanding environments. The MX-System is characterized by the following properties:
- robust, chrome-plated, and varnished metal housing
- resistant to oil and cleaning agents
- IP67 protection thanks to the double sealing principle
- EMC interference immunity due to metal housing
- temperature-resistant between 0...50 °C
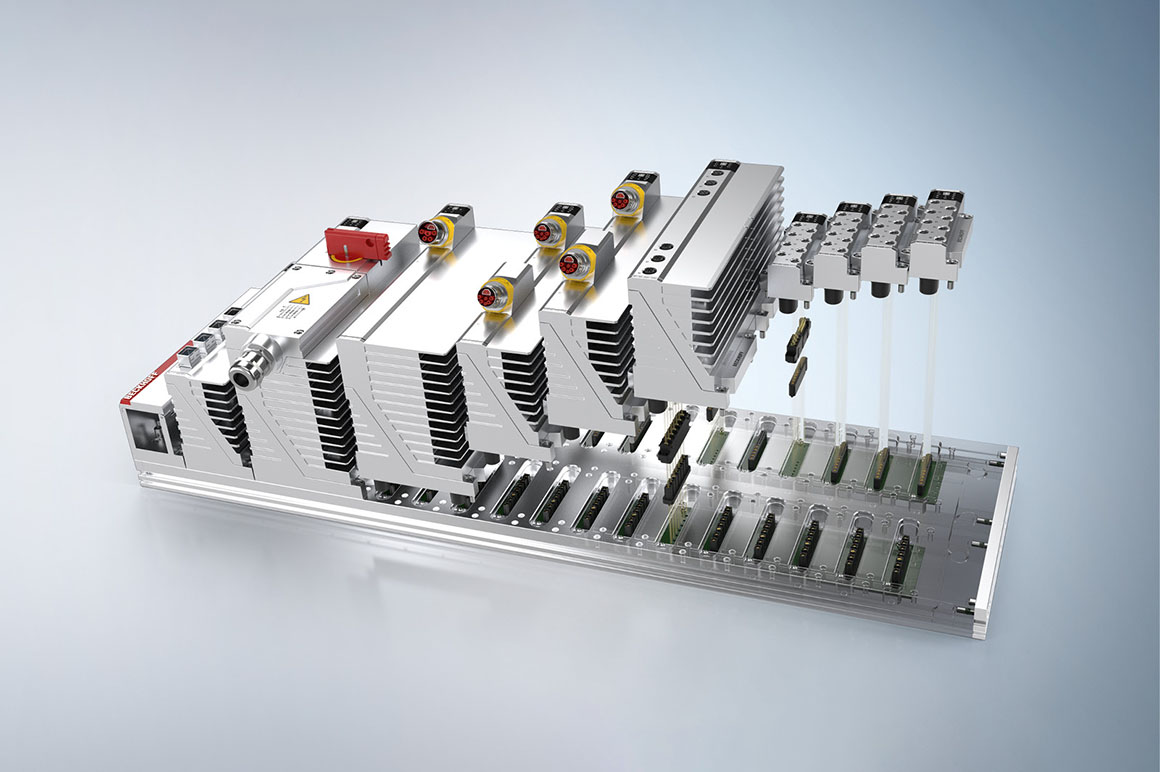
Standardized interfaces
Big savings with standard connectors and EtherCAT in every module
he standardized connectors completely replace the wiring that was required for the individual components. With the MX-System, there are no more wiring errors and no more hours of wiring work. Handling is unbelievably easy and all the connectors have been designed to provide IP20 contact protection, even when no modules and no covers have been mounted on the slots. The backplanes are literally and physically at the core of every baseplate in the MX-System.
They provide electrical power as well as communication and diagnostic functions via standardized connectors. This means that each function module is automatically connected to EtherCAT when it is connected to the baseplate. EtherCAT is implemented in every module, and this enables hot swapping and real-time capability for the MX-System, as well as parameterization and diagnostics for each individual function module.
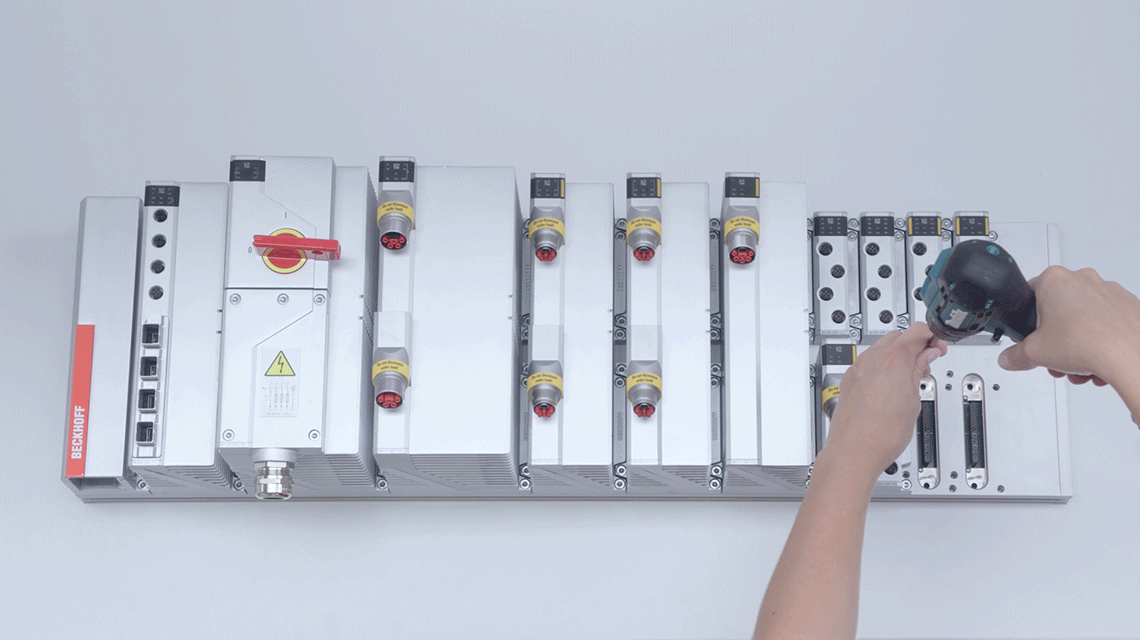
Plug-and-play
Fast assembly and even faster wiring
The compact MX-System sets new standards in handling and drastically reduces assembly times. The function modules are plugged onto the standardized connectors on the baseplate and then screwed in place using the captive screws located in the modules. Wading through a time-consuming circuit diagram is a thing of the past; the connector system wires modules together.
Wiring errors are prevented by the modular principle – this automatically leads to an increase in quality. The low number of components also reduces the number of assembly steps and the required assembly area. Storage and production areas, along with logistics processes, can be streamlined significantly. Overall, the MX-System provides a host of advantages compared to the usual machine life cycle.
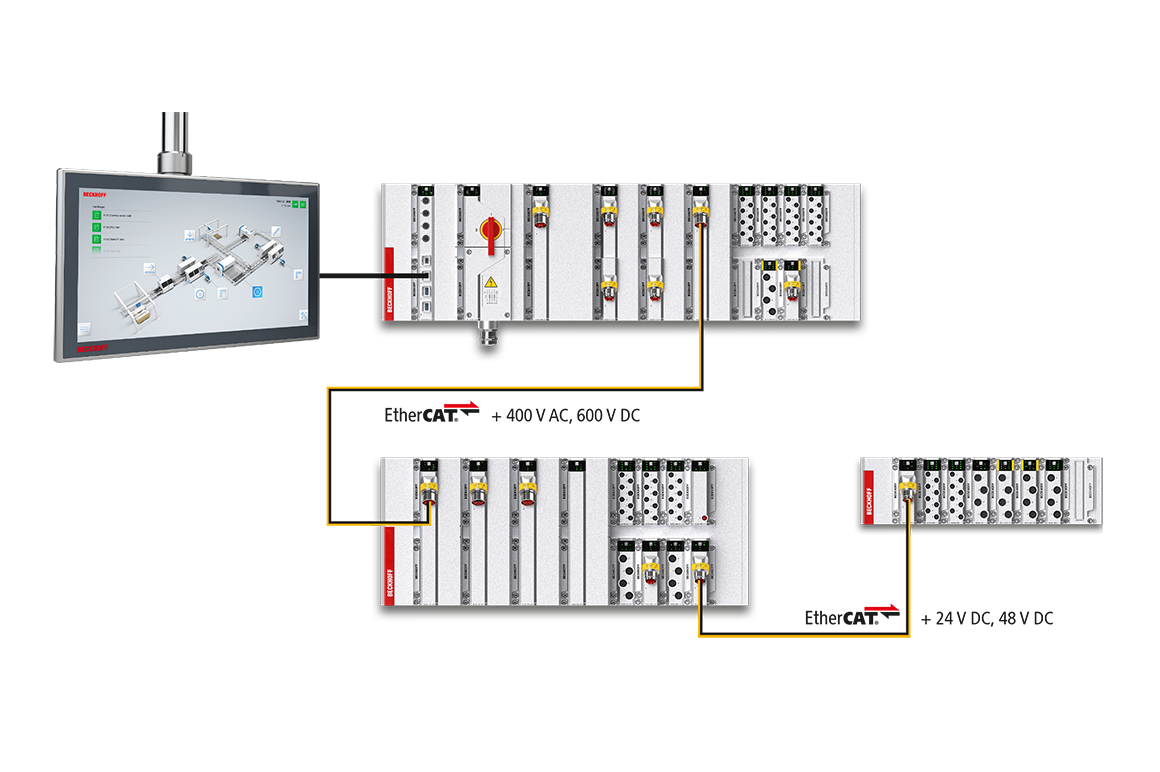
Open and flexible
As a stand-alone solution or for optimizing existing applications
The MX-System distributes EtherCAT and voltages for all systems. Various system modules are used to create flexible topologies that are precisely adapted to the application requirements. Combined, the modules provide voltages for different requirements and communication via EtherCAT. Standardized connectors and hybrid cables are used for connection.
The MX-System can be used as a stand-alone solution or seamlessly integrated into existing applications. The architecture is irrelevant: centralized with a control cabinet or in combination with decentralized devices, anything goes. If production requirements change, operators and machine builders have flexible options with the MX-System, from expanding with individual modules or entire stations to replacing the existing technology.
The MX-System in comparison
A clear winner
Control cabinet | MX-System | |
---|---|---|
800 mm × 1600 mm × 400 mm | Dimensions | 800 mm × 240 mm × 230 mm |
110 kg | Weight | 36 kg |
146 | Components | 15 |
100 pages | Circuit diagram content | 25 pages |
5 electricians | Personnel expenses | 1 non-specialist |
28 h | Assembly and test time | 1 h |
17 | Toolboxes required | 1 |
470 W | Required cooling capacity | – |
50 % | EtherCAT integration | 100 % |
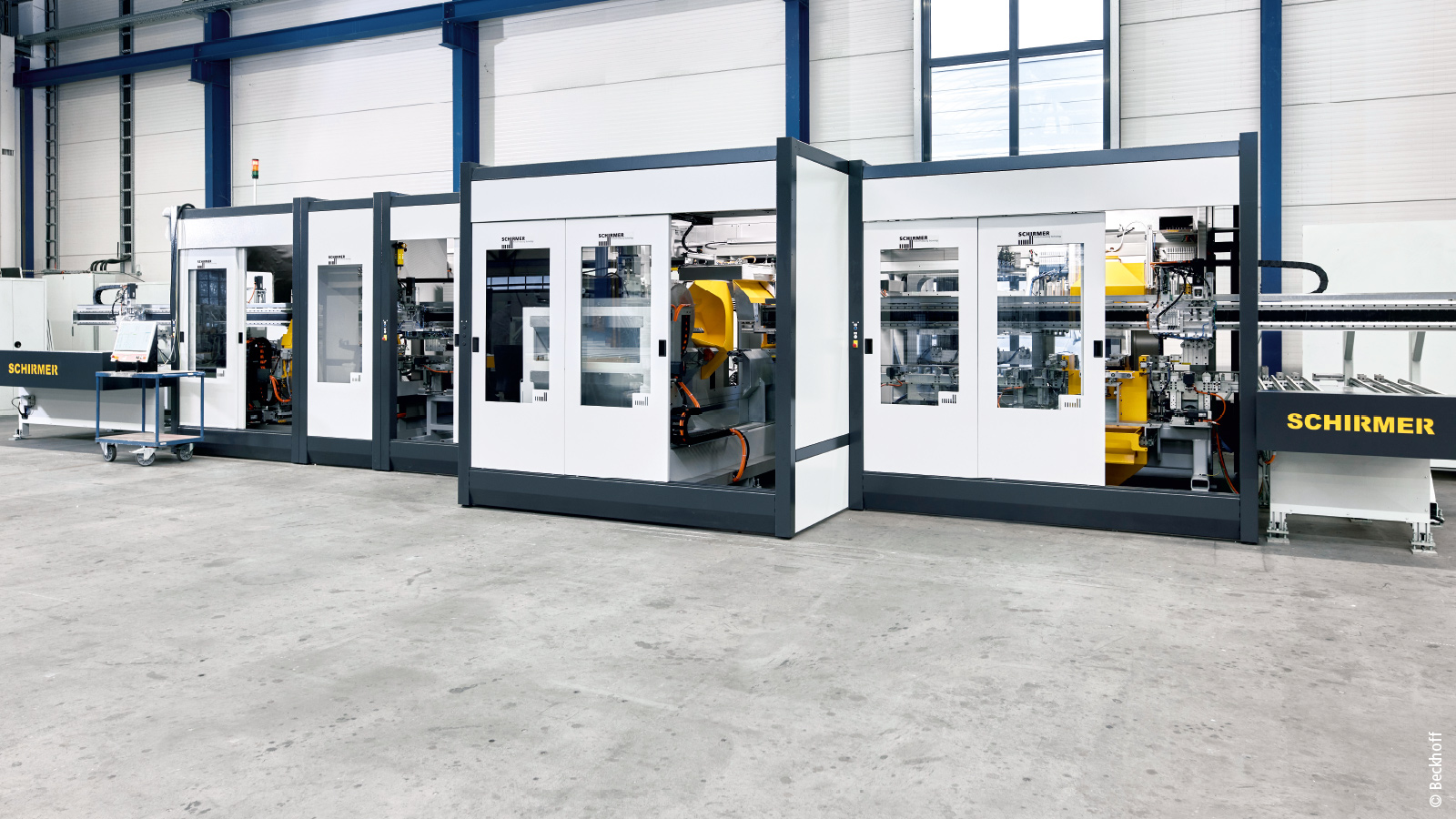
Schirmer Maschinen GmbH
Window and door construction is a high-tech business. This much is evident right from the first process step, with the fully automatic processing of raw bars on a profile processing machine from Schirmer Maschinen GmbH. Schirmer was founded in 1979 and was Beckhoff’s first customer. The company has relied on PC-based control technology from Beckhoff for over 40 years now, from the first positioning controller to the new MX-System.
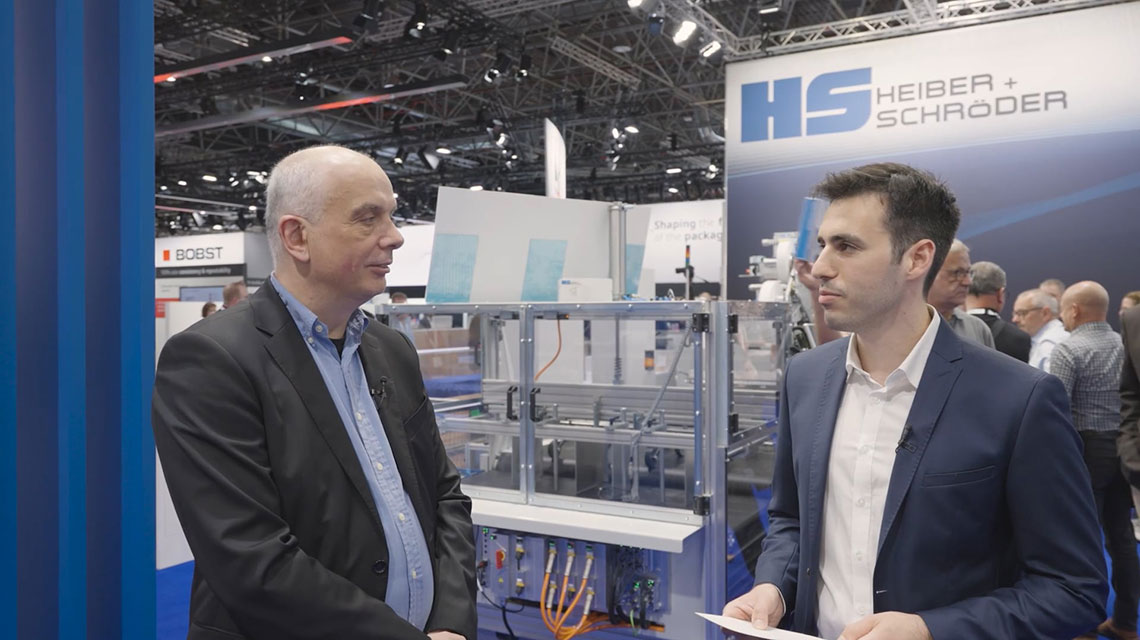
Heiber + Schröder
Heiber + Schröder Maschinenbau GmbH developed an automatic destacker which, for example, stacks packaging from a window patching machine into accurately counted stacks and transfers them to the downstream transport system - automated without a control cabinet using our MX-System.
Beckhoff Live + Interactive
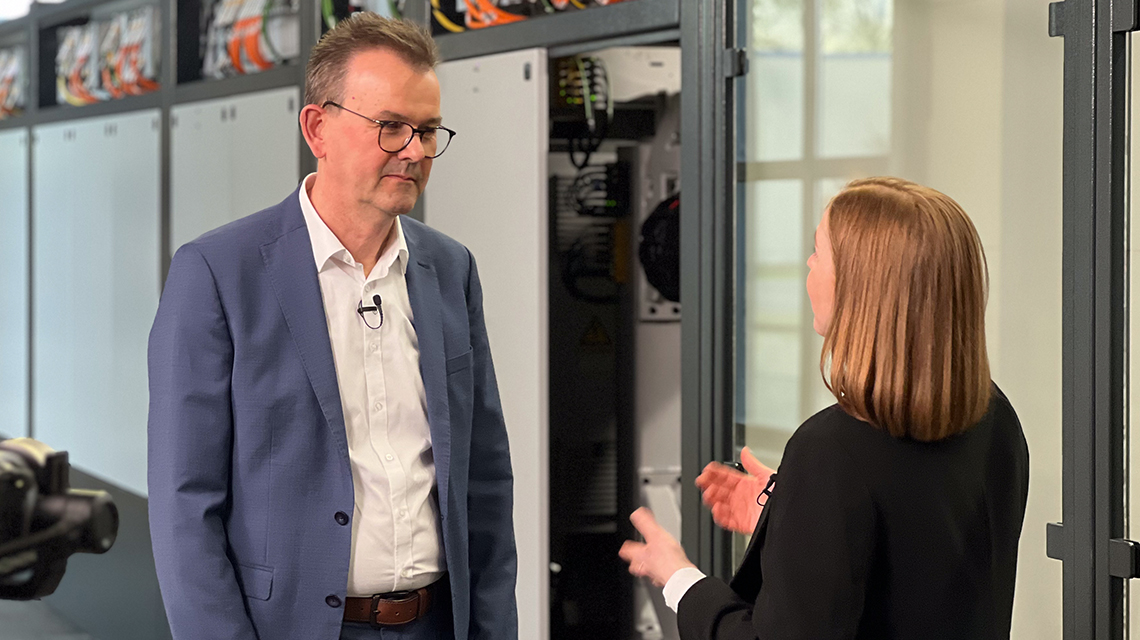
Rethinking automation
“The MX-System is changing the face of design and installation in the world of machine building,” explains Ludger Martinschledde, managing director of Schirmer Maschinen GmbH. Schirmer is breaking new ground by using the MX-System on one of its machines for the first time. This video explains the main objectives, tasks, and opportunities arising from the use of the MX-System at Schirmer.
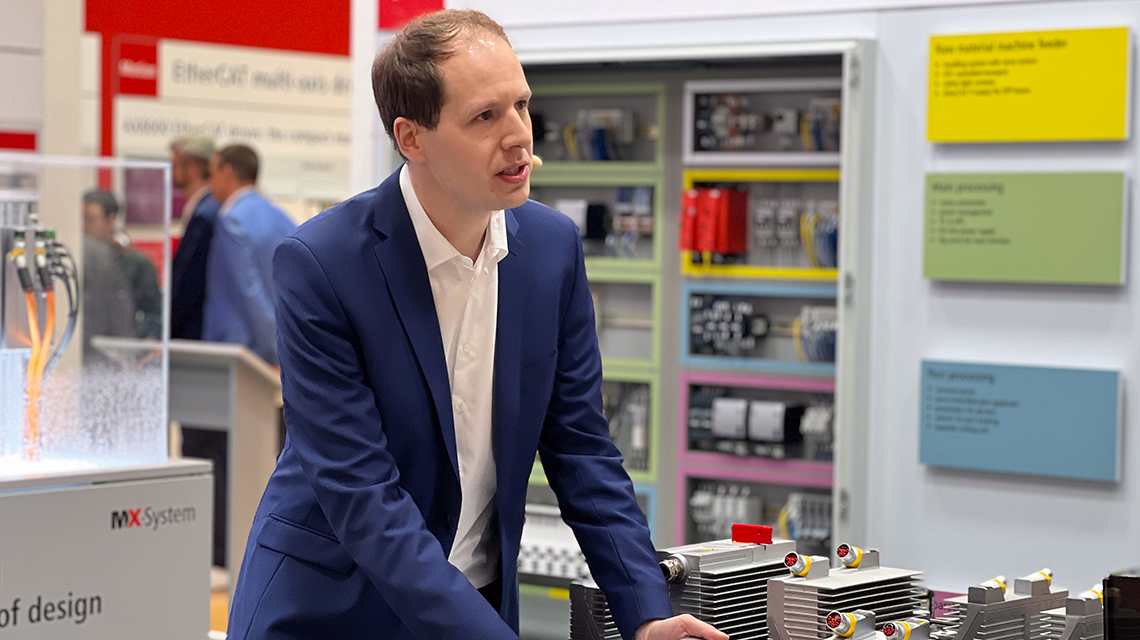
MX-System: a short explanation
Beckhoff has developed an efficient control cabinet alternative in the form of the MX-System. Marius Winkler explains the details in this video.
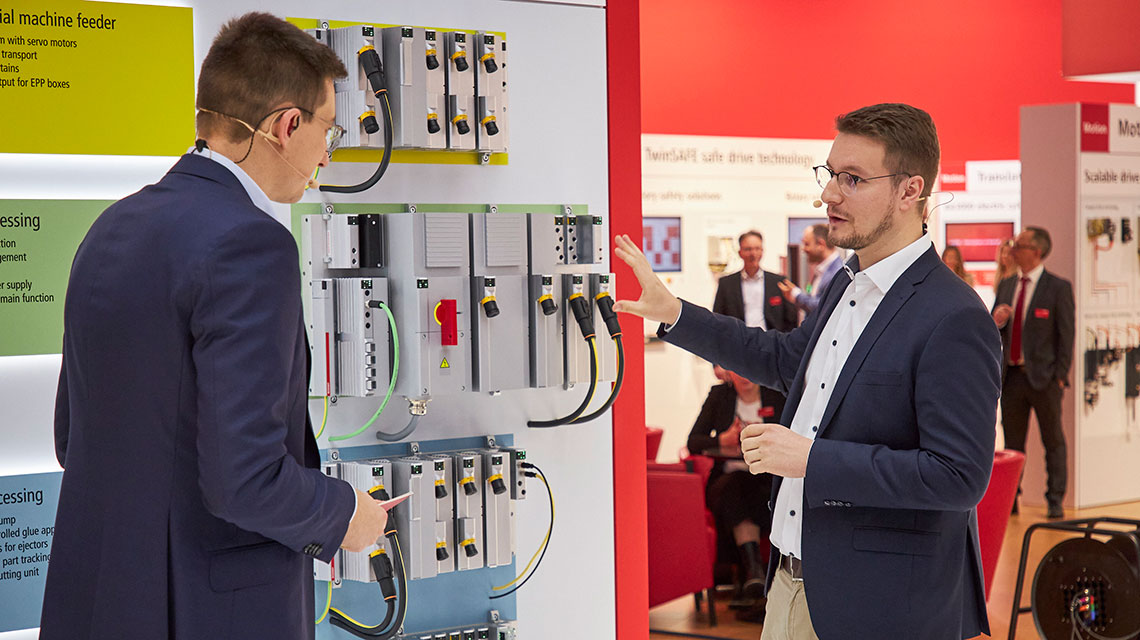
Baseplate and function modules in size 3
The MX-System has a highly modular design and can now be even better adapted to the respective application with the three-row baseplate and corresponding function modules. Watch the video to find out how a large control cabinet can be divided into several MX-Systems.
Awards
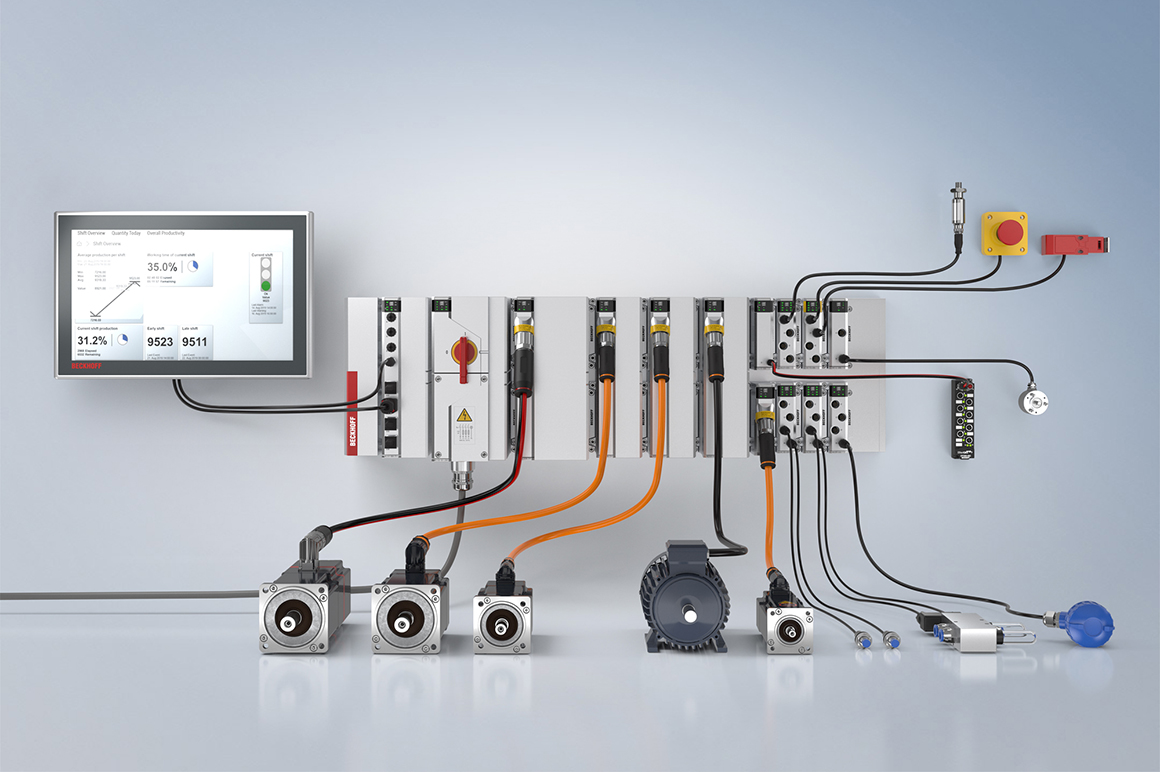
Industrie 4.0 Innovation Award
The MX-System won over the expert jury for the VDE Verlag's Industrie 4.0 Innovation Award, along with the readership of etz elektrotechnik & automation and openautomation. Every year, they award prizes to the three best products that make an enriching contribution to Industry 4.0. The MX-System won first place this year.
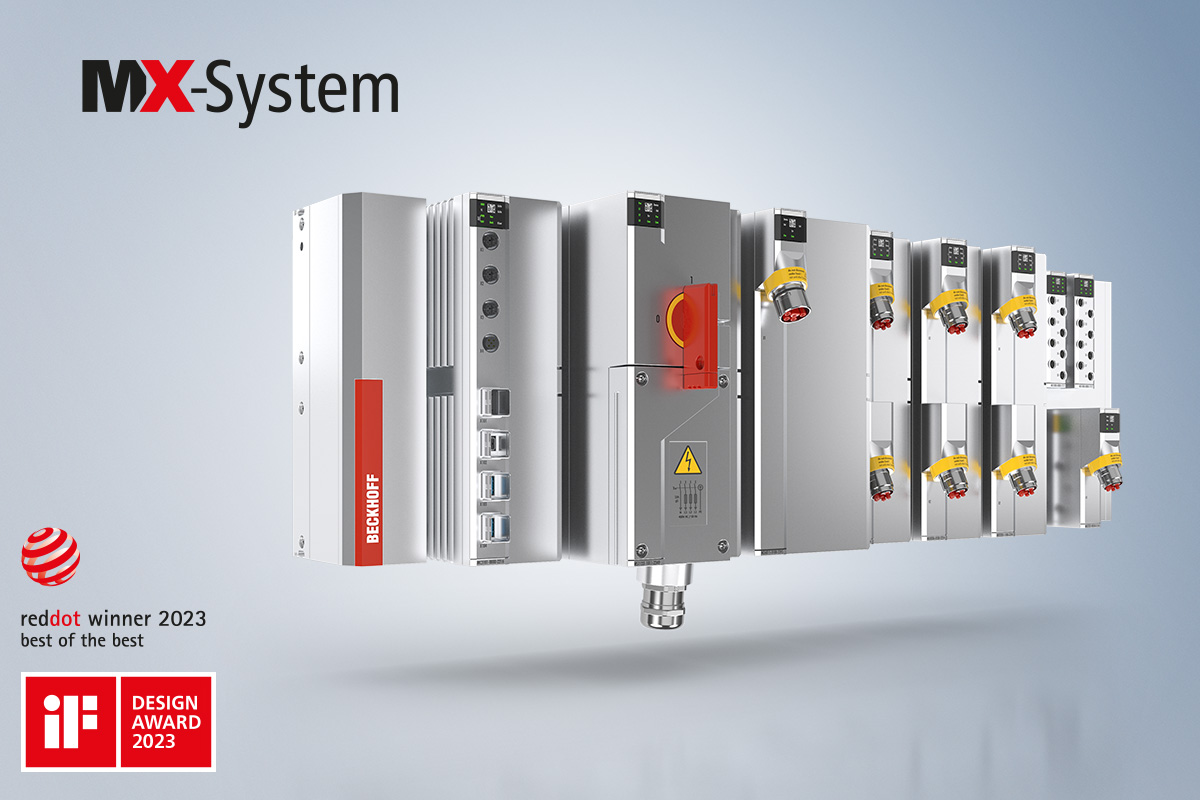
Red Dot Award and iF Design Award
The pioneering product design of the MX-System contributes massively to its potential for innovation, and this was confirmed by the jury for the renowned Red Dot Award, as they have honored this product with the highest "Best of the Best" award category. This was further confirmed with the iF Design Award.